What Training?
|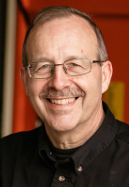
I don’t normally write more than one column in a month, but I want to give my final thoughts on the state of training in our industry before we leave this topic. Spoiler alert: this is a rant!
Are you a dry cleaner?
Some people think, “I wrote out a big cheque so that makes me a dry cleaner.” Maybe. Or you might just have jumped into something you don’t understand. Writing a big cheque doesn’t make you anything except poor.
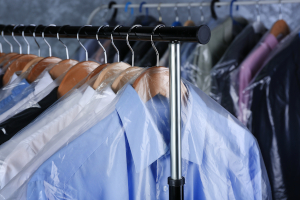
I was at a plant one day and a lady asked me about cleaning a garment. I looked at it and read the label out loud. “Professionally dry clean,” it said. I looked up as she shook her head – as if to say no, that wasn’t her. I think she was right. She may have owned a dry cleaning plant, but she wasn’t a professional dry cleaner
A customer recently bought a plant. The previous owner gave him two weeks of training. He hired a young girl to press, but she didn’t even get two weeks of training. And she is there working by herself – he is too busy to stay at the plant.
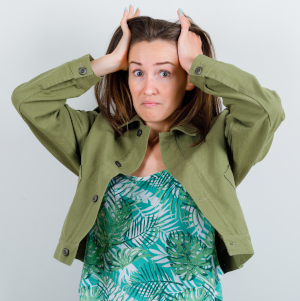
The untrained girl’s dry cleaning machine gave her an alarm the other day – ‘Full Decanter’. Paula in our office FaceTimed with her to try to help. For some reason, she was looking in the boiler room to see what was wrong. Most of us know that a ‘Full Decanter’ alarm means you need to drain the water out of the decanter so you can continue running your load. So why was she looking in the boiler room?
She probably previously had a steam pressure alarm on her dry cleaning machine and had to deal with a boiler problem to fix her dry cleaning machine alarm. Bottom line: she didn’t have a clue what she was doing. She probably should not be operating the dry cleaning machine and she definitely should not be operating the boiler. BUT THIS IS NOT HER FAULT – IT IS THE OWNER’S FAULT. She is trying her best.
I am not really annoyed with operators who don’t know what they’re doing. I am annoyed with owners who leave their people to struggle trying to do things they don’t understand, and knowing they might get fired if they damage a garment.
Lack of knowledge
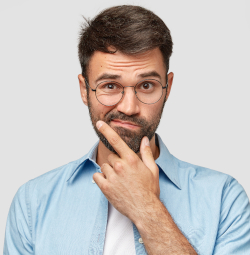
There is a lack of knowledge in this industry. I can remember the old Spenser dry cleaning machines. They did not have a computer or even a card control. They had a series of toggle switches. You manipulated the switches for each step through the cycle. “Turn on the tank valve, turn on the pump, start the wheel rotating.” Most operators are not even aware of what is happening in the machine, never mind being able to create a cycle from memory. On the Spenser machines you had to know every step and changed things manually as you went through the cycle.
If operators don’t know what’s happening, how do they tell us what is broken? We do a lot of trouble shooting. We ask questions like, “What is wrong with the machine? What did you do? How did you try to fix it?” It becomes obvious very quickly that most operators do not understand fibres and fabrics, cleaning processes (water and solvent), and they especially don’t understand their equipment. How did we ever get to this state in the industry?
Lack of proper training
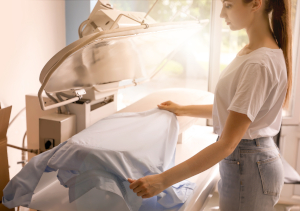
Training in most plants is delegated to the least competent employees. Everyone else is too busy doing important stuff. So the second-newest employee trains the newest employee. They pass on their limited information without much understanding of what they are doing. Every new employee learns a little less than the one before, and takes on board any bad habits or misconceptions as well.
Another way cleaners learn is through mistakes. Pay the claim and learn something. Hopefully you really do learn what went wrong and are able to ensure it doesn’t happen again.
Who will do your Training?
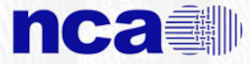
DLI (Drycleaning & Laundry Institute) and NCA (National Cleaners Association) offer training courses. I took the three-week DLI course about 35 years ago. It was quite valuable. Some of that training is now available online. That is great, but it does not duplicate the hands-on training that you receive at the school.
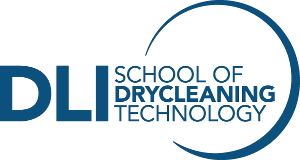
You may not know it, but IFI (the forerunner to DLI) used to have a school in Toronto where they taught dry cleaning and laundry. It was a six-month course! That was a significant investment in learning a trade.
Another good resource is the factory representative. Chemical, equipment or padding reps visit hundreds of plants each year. I know that because I have the privilege of travelling with them sometimes. They have been asked almost every question possible. They have seen many problems and solutions. Best of all, they want to help you succeed.
I can remember Bob Serniak and Brian Hatt visiting our plant and patiently answering my questions. How to remove stains, how to repair machines, the best way to process a particular garment.
Do your operators know where the manuals are for their machines and will you allow them time read them? Do you have SDS sheets for everything and have your people been trained about the dangers of those chemicals?
Talk to your equipment sales rep. They would be glad to help you with training on your machine or the proper use of chemicals. Their goal is to make sure you operate the machine properly and are successful using their product.
Training stars
One of the plants we service has a great system for training new employees. They put them to work pressing hotel uniforms. Uniforms are easier to press. You never get a complaint or claim, and it gives the new employee some confidence before they get to harder garments.
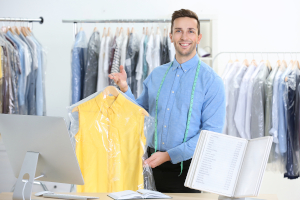
Another plant has a ‘toolbox’ meeting every morning. Different staff members take turns leading the meeting. They do physical stretching, go over some training and discuss the day’s work. The biggest benefit is that they are one team working together to accomplish the tasks for the day.
A plant I was in last week has everyone cross trained. Every person can do three jobs in the plant. They have spent a lot of time to train their people. The only exception is the cleaner spotter. They still need to do some cross training for that position, but they are miles ahead of huge swaths of the industry.
What kind of Cleaner are you going to be?
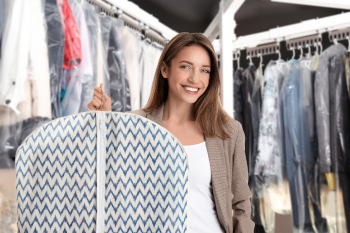
Do you care about our industry and the public’s perception of us? Why is there an expression, ‘Taken to the cleaners’? What does that say about us? Are you adding to that expression or taking away from it?
It has been said, “If I train them, they will just leave.” But what if you don’t train them and they stay? Make your plant nice enough and help them feel competent enough that they will not want to leave.
I have made some strong accusations here. Some of them may apply to you. What are you going to do about it? You are the only one who can make a change in your plant. If we work together we can improve our industry.
Now that I am done ranting, the Alberta Textile Care Association is hosting a training seminar on Saturday, May 13. (Learn more here.) You are most welcome to join us. I hope to learn some new things and I hope to see you there, too.
Kevin Marois founded Calgary-based Integrity Mechanical in 2003 to service plants in western Canada. He writes on issues related to equipment, its purchase, maintenance and use. You can reach Kevin at office@imicanada.ca or via his website www.imicanada.ca