
If you missed a news story, check our News Archive for the top stories.
Be sure to visit People and Product News while you’re catching up on all the latest. Check out our new JOBS page if you are looking for a job or a qualified employee.
JUNE 2025 NEWS
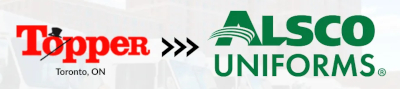
Alsco Acquires Topper Linen
Alsco Uniforms, a global leader in uniform and linen laundry services headquartered in Salt Lake City, Utah, has announced the acquisition of Topper Linen, strengthening its service capabilities and expanding its footprint in the Greater Toronto Area.
“This acquisition marks an exciting step forward in our continued growth,” said Bob Steiner, CEO of Alsco Uniforms. “We’re proud to welcome the employees and customers of Topper Linen to Alsco Uniforms. As a 135-year-old, family-owned company with deep Canadian roots, we understand the value of long-standing relationships and appreciate the trust Topper has built in the Toronto community. We look forward to building on that legacy and delivering reliable, consistent, and exceptional service.”
“We are confident our customers will be excited that Alsco Uniforms brings the same values of service and partnership that Topper always upheld,” said Tim Topornicki, President of Topper Linen and Uniform Service, who has spent 46 years committed to service excellence in the Toronto market.
As part of this transition, Topper’s Toronto facility and fleet of delivery trucks will be rebranded as Alsco Uniforms over the coming months. The addition of this location expands operations to two laundry facilities in Toronto, enhancing the ability to serve industrial, healthcare, hospitality, and food and beverage businesses throughout the region.
Alsco Uniforms will continue to operate both Toronto facilities independently. Current Topper Linen employees will remain in place, ensuring service continuity and local expertise remain at the forefront of the customer experience. “Keeping the talented Topper employees was a vital factor in this acquisition,” emphasized Mr. Steiner.
Jim Kearns, chief operating officer at Alsco Uniforms, expressed his commitment to growth, stating, “This acquisition of Topper Linen gives us a strong base to better serve customers in the Toronto area. Along with strategic acquisitions, we plan on investing more in expanding our sales and service teams across North America to support our growth initiatives.”
Alsco Uniforms now has over 80 mixed-processing facilities in North America. Each provides businesses with hygienically clean uniforms, linens, floor mats, mops, first aid, and restroom supplies. Businesses looking for an alternative laundry provider should visit www.alsco.com to learn more.
About Alsco Uniforms
Alsco Uniforms is a fifth-generation, family-owned and operated uniform and linen laundry service company founded in 1889. They are recognized by the prestigious Hohenstein Institute for having invented the uniform and linen rental industry. Celebrating over 135 years of business, Alsco Uniforms provides laundry services and other products that keep businesses clean and safe for customers across all market segments, including healthcare, automotive, industrial, and hospitality. With more than 200 locations and 16,000 employees, Alsco Uniforms provides laundry and other services and products to more than 350,000 customers in 13 countries, which makes Alsco Uniforms the largest uniform company in the world. Visit alsco.com for more information.
About Topper Linen
Topper Linen and Uniform Service is an independently owned Canadian textile rental service. Topper was founded in 1956 and remains a family-owned business that has been serving the linen and uniform rental needs of Toronto and the surrounding Ontario regions for over 60 years. Topper operates out of a 54,000-square-foot facility, employs over 90 team members, and maintains 20 route service vehicles.
America’s Best Cleaners Champions Circular Fashion Leadership at 2025 TCATA Conference
America’s Best Cleaners (ABC), the industry’s leading certification and consulting body for garment care professionals, continues to set the standard for innovation, sustainability, and leadership. At the 2025 Textile Care Allied Trades Association (TCATA) Annual Management & Educational Conference held at the Ritz-Carlton Tiburon in Naples, Florida, ABC Executive Director Christopher White delivered a keynote presentation titled “Fashion Circularity and You: Opportunities for Our Industry to Grow.”
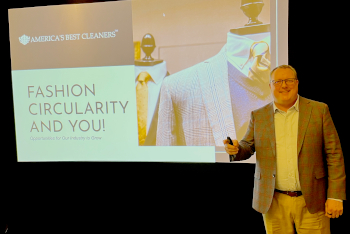
As a featured speaker among a dynamic lineup of industry leaders, White delivered a timely message on how the dry cleaning and textile care industry can thrive by embracing the principles of a circular economy. His session addressed the urgent need to reduce textile waste, the growth of the luxury resale market, and how ABC affiliates are uniquely positioned to capitalize on this shift by offering garment care, restoration, and re-commerce services.
“Dry cleaners are no longer just service providers,” said White. “They are neighborhood sustainability hubs. By caring for garments at the highest level, offering expert repairs and restorations, and facilitating resale and reuse, we extend garment life—and our relevance in a rapidly changing marketplace.”
Attendees of the conference were shown data visualizations of global textile waste, including the mounting impact of ultra-fast fashion and the systemic overproduction that plagues the industry. White underscored how brands like SHEIN release thousands of new styles weekly, accelerating consumption and disposal cycles. He also addressed the often-misunderstood role of luxury brands in this landscape—noting that while some headlines have criticized overproduction, ABC remains committed to working with the world’s most respected fashion houses.
“We firmly believe that better-made apparel and high-quality textiles are essential to reducing global textile waste,” said White. “Our alignment with luxury fashion design partners reflects a shared commitment to craftsmanship, longevity, and sustainability. When garments are made to last—and cared for properly—they don’t contribute to the waste crisis. Instead, they help shift consumer behavior away from disposable fashion and toward mindful ownership.”
In addition to strengthening ties with the fashion world, ABC emphasized its deep appreciation for allied trade partners who play a critical role in supporting innovation across textile care.
“As this emerging circular fashion economy accelerates, from care and repair to full textile-to-textile recycling, we want to ensure that our allied trade partners are equipped to grow with it,” White said. “We value their contributions and see their capabilities as foundational to positioning this industry for long-term viability and environmental relevance.”
As ABC celebrates its 25th anniversary in 2025, the organization remains firmly committed to accelerating innovation in garment care and promoting sustainable business practices. Through its ongoing work with the American Circular Textiles (ACT) group, ABC is also a vocal supporter of the America’s Act—a bipartisan bill that includes over $14 billion in tax, grant, and loan incentives to support circular textile initiatives.
ALM’s “Your Future Unfolds” Campaign Video Wins Telly Award
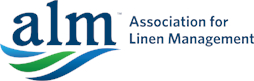
The Association of Linen Management’s (ALM) video campaign entitled “Your Future Unfolds” has received a prestigious Silver Telly Award.
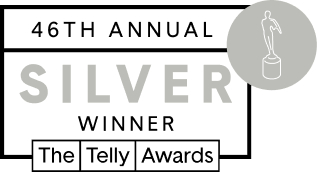
The Telly Awards is the premier award honoring video and television across all screens. Established in 1979, The Telly Awards receives over 12,000 entries from all 50 states and 5 continents. Entrants are judged by The Telly Awards Judging Council—an industry body of over 200 leading experts including advertising agencies, production companies, and major television networks.
The “Your Future Unfolds” campaign is all about highlighting the real opportunities waiting in the textile care industry. Through stories, spotlights, and straight talk from people working in all kinds of roles—from the plant floor to leadership—it shows how a career in laundry and linen management can grow into something meaningful with the support of ALM and its resources along the way. The campaign focuses on the people behind the process, showcasing how skills, training, and teamwork come together to create stable jobs and clear career paths. Whether someone’s just starting out or looking to take the next step, Your Future Unfolds sends a simple, strong message: there’s a place for you here, and there’s room to grow.
ALM partnered with the David James Group (DJG) to bring the “Your Future Unfolds” campaign to life. DJG, known for its work with nonprofit organizations, developed the campaign’s message and visual identity to resonate with individuals in the industry to connect them with the vast suite of educational programs, certifications, and resources provided by ALM.
“Our industry is experimenting with new technologies like never before, shaping truly compelling stories to draw attention to some of the world’s most pressing issues,” shares Telly Awards Managing Director Amanda Needham. “The Telly Awards is uniquely positioned to meet the industry where it’s actually making work, be that on television or TikTok.”
“We’re incredibly honored to receive a Silver Telly Award for our “Your Future Unfolds” campaign,” said Sarah Brobeck, President and CEO of the Association for Linen Management. “This recognition is a testament to the powerful partnership we had with the David James Group. Their creative vision helped us tell a compelling story about the value and opportunity within our industry. Our hope is that this video continues to spark interest, drive engagement, and connect more people with the resources they need to grow—both professionally and operationally.”
The full list of the 46th Annual Telly Awards winners can be found at www.tellyawards.com/winners/
Visit ALM’s website to learn more about the organization.
TCATA Awards Scholarships
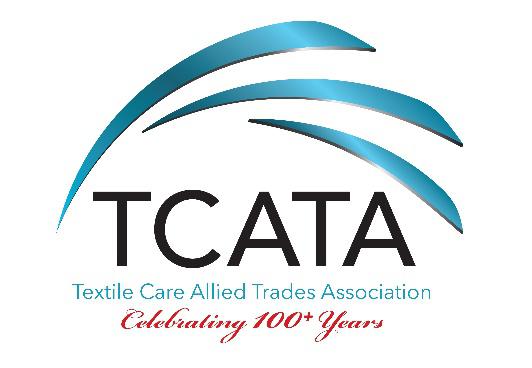
The Textile Care Allied Trades Association (TCATA) is proud to announce the recipients of its 2025 Educational Fund Scholarships, awarded annually to support the educational goals of employees and family members of TCATA member companies.
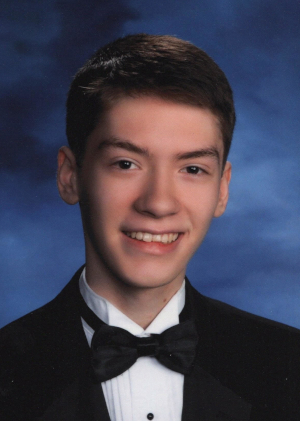
This year’s Scholastic Scholarship has been awarded to Eli Regan, son of Mary Castro-Regan, an employee at BPS Communications. Eli’s strong academic record, leadership qualities, and commitment to higher education earned him this $2,000 annual scholarship, which is renewable for up to four years. Outside of academics, Eli is a member and leader of his high school’s FIRST Robotics Competition team and volunteers at a local co-op grocery store and as a volunteer docent at Wings of Freedom aircraft museum. Eli plans to study mechanical engineering at Purdue University upon graduation.
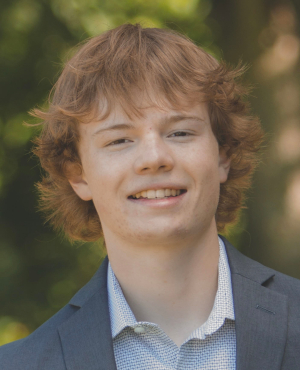
TCATA is also pleased to announce the first-ever recipient of its new Vocational Program Scholarship, created to support students pursuing certifications or technical education. Keegan McKillip, an employee of Felins, has been selected for this $2,000 per year award, which supports up to two years of trade or vocational school. Keegan began working at Felins in the summer of his junior year of high school manufacturing parts for their Pak-Tyers and Flex-Strap machines. The following year, he was accepted into the Industrial Equipment Apprentice Program. Keegan plans to continue working with the Service Department at Felins while pursuing an associate’s degree in Robotics and Automation Engineering Technology at Waukesha County Technical College.
This new scholarship reflects TCATA’s commitment to supporting a skilled and diverse workforce in the textile care industry. “These scholarships are a way for us to invest in the future of our members and their families,” said Luci Ward, Executive Director of TCATA. “We congratulate Eli and Keegan on their accomplishments and are honored to support their continued education.”
For more information on TCATA’s scholarship programs, visit www.tcata.org.
For news earlier than the articles above, please visit the New Archives.
Can our Canadian Scholarship cover the cost of the webinars for non-members?
EDITOR’S NOTE: We checked with Mary Scalco at DLI, and she said that scholarships can be used for online classes, just like in-person courses.