Don’t you hate it when you miss a news story? The very essence of “news” is that it comes and goes pretty quickly. But we want you to be able to read news after it’s been removed from our main pages. So, check this archive if you missed something.
APRIL 2025 NEWS

May Is Maytag® Month
Includes Special Financing Offer and Distributor Events
Whirlpool Corporation Commercial Laundry announced the 2025 May is Maytag® Month special financing offer. From May 1 through June 30, 2025, eligible buyers can receive 5.99% financing for up to 60 months on new Maytag Commercial Laundry washers and dryers financed through Eastern Funding.
“With decades of engineering expertise behind every washer and dryer, Maytag® Commercial Laundry equipment is designed for long-lasting performance and maximum dependability. Whether you’re upgrading a laundromat, replacing on-premises equipment, or expanding your operation, this special financing makes it easier than ever to get the durability your business needs—on terms that work for you.
“This is the perfect time for laundromat owners, on-premises operators and distributors to take advantage of trusted Maytag performance, backed by a financing offer that makes it easier than ever to invest in the future of their business,” said Amy Gardner, Director of Sales, Service and Parts, Commercial Laundry. “We’re excited to help our customers succeed and support their growth with long-lasting, dependable equipment.”
Attend a Maytag Month Open House Near You
Visit an upcoming distributor open house. Learn more about Maytag equipment, connect with experts, and get details on this limited-time financing offer in person:
Northwest Laundry Supply
Craig Moore – craigm@northwestlaundry.com or (509) 487-4800
• May 6 – Seattle, WA
• May 8 – Spokane, WA
Mendenhall Commercial Laundry Equipment
Brad Moyes – brad@mendenhallcle.com or 801-298-1133 ext: 111
• May 15 – North Salt Lake, UT
Midland Commercial Sales and Service
Don Beesley – don@midlandcommercial.com
• June 10 – Winnipeg, MB, Canada
For more information on the May is Maytag Month offer, please contact your local distributor.
Extox Open House a “Smashing Success”
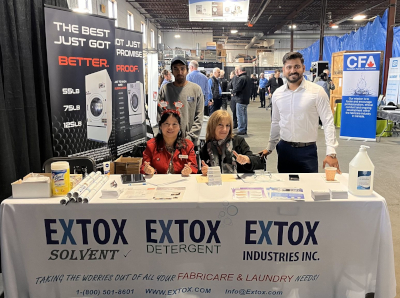
Artur Keyes-Kryaskowski and his team put together an Open House, held April 5-6, that was well-attended and a “smashing success” according to Artur.
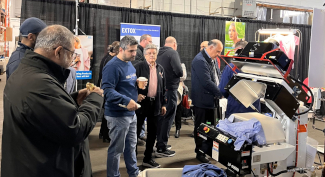
“A huge thank you to everyone who attended our Open House! We were thrilled to showcase our premium line of dry cleaning, commercial laundry, and finishing equipment, all made possible with the fantastic support and sponsorship of our trusted manufacturers: Bowe Germany, Sankosha, Yamamoto, Seitz Gmbh, Fabritec International, AL Wilson, GreenEarth, and Seeko Pump.
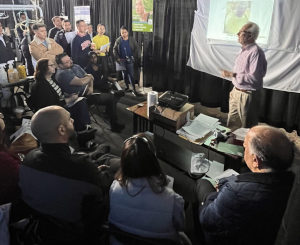
The live demonstrations and our spot removal workshop were met with great enthusiasm, and it was wonderful to engage with so many of you. Your participation and interest mean the world to us! If you couldn’t make it or want to learn more about our offerings, feel free to reach out. We can’t wait to see you at our future events!”
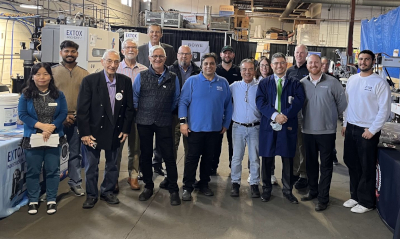
UNX-Christeyns Transitions to Christeyns
Embracing Growth and Global Identity
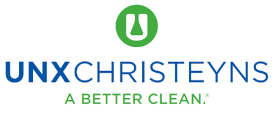
UNX-Christeyns, the trusted name in commercial cleaning solutions, is excited to announce an evolution in its brand identity. Beginning in late April 2025, the company will transition its brand identity from UNX-Christeyns to Christeyns, reinforcing its place as part of the global Christeyns family of companies while continuing to operate as an independent entity (Christeyns North America), dedicated to superior service and industry leadership within the North American markets.
This name transition does not reflect a change in ownership but rather marks a natural progression in the company’s growth strategy. Since the successful merger of UNX Industries and Christeyns USA in July 2022, the organization has strategically implemented changes in phases to ensure a seamless experience for both employees and customers.
“This rebrand has been part of our long-term vision since merging in 2022,” said Josh Lilley, CEO of UNX-Christeyns. “This transition communicates a clear and unified message about our global identity, which is increasingly focused on market-leading customer partnerships, innovation, and technology.”
The UNX-Christeyns Board of Directors also shared their enthusiasm for the next phase of the company’s growth. “Our board and shareholders are thrilled about the past, present, and future success of our company in North America. While we’ve operated as the North American division of Christeyns since our merger in 2022, this shift provides clarity correlated to our position in the global market.”
As part of this transformation, UNX-Christeyns is also proud to announce plans for a state-of-the-art manufacturing facility in Greenville, NC, set to be completed by the end of 2025. This cutting-edge facility will enhance manufacturing efficiencies, increase capacity, and consolidate the company’s manufacturing, engineering, R&D laboratory, and corporate offices into one location. “This investment demonstrates our commitment to long-term growth and excellence,” added Lilley. “By increasing production capabilities and efficiency, we will be better positioned to support our customers and drive innovation within the industries we serve.”
Further details on the new facility and other strategic initiatives will be shared in the coming months.
Braun Launches Redesigned Website to Enhance Customer Experience
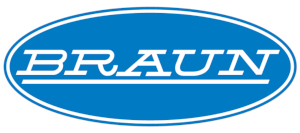
G. A. Braun, Inc., a leading U.S. manufacturer of industrial laundry equipment, is proud to unveil the newly redesigned gabraun.com — created to deliver a better, faster, and more customer-focused experience.
With improved navigation, a mobile-friendly design, and clearer access to both products and people, the new gabraun.com makes it easier than ever for customers to connect, explore, and choose Braun.
Key features of the redesigned gabraun.com include:
- A new, visually enhanced homepage and site layout
- Streamlined navigation across all devices
- Industry-specific laundry solutions
“The redesigned site highlights what sets Braun apart— durable, American-made
equipment backed by our people, expert support, and dependable solutions. It’s now
easier than ever for site visitors to find exactly what they need,” said Traci Anelli,
Director of Marketing.
“This is more than a website refresh — it’s part of our commitment to evolving with our
customers. Whether you’re starting a new laundry, expanding an existing operation,
ordering replacement parts, or connecting with our team, the new gabraun.com is built
to support you every step of the way.”
Experience the new site design today at www.gabraun.com.
ALM’s 2025 Elevate Conference Sets New Standard for Learning and Networking
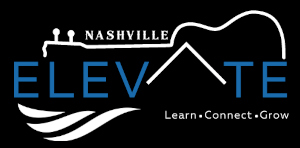
The inaugural ALM Elevate Conference, held from March 17-19, 2025, in Nashville, TN, attracted 118 professionals, including 68 laundry operators, 43% of whom were decision-makers. This two-day event offered hands-on workshops, expert insights, and valuable networking opportunities, providing attendees with practical tools to enhance their operations and industry knowledge.
“We are thrilled with the success of Elevate’s inaugural event,” said Sarah Brobeck, President and CEO of ALM. “The engagement from our attendees has been incredible, and the feedback has been overwhelmingly positive. Elevate offered a platform for professionals to expand their skills and connect with peers.”
Hands-On Learning and Real-World Application
The conference kicked off with sessions on Root Cause Analysis to identify areas for operational improvement. Linen management participants took part in a beer supply chain simulation, addressing inventory and ordering challenges. Nathan Mein, General Manager, TMC Laundry Cooperative noted, “Today’s class opened my eyes to the efforts that our partner owners put into reducing overtime and plant capacity, which ultimately helps save time and money.”
Laundry operators participated in a LEGO manufacturing line exercise, learning to streamline workflows using LEAN tools. “The LEAN presentation and exercise was not only fun but particularly telling,” said Graham Skinner, RLLD, VP of Business Development & Technical Support from UNX Christeyns. “It made you physically and mentally see how to eliminate production constraints and reduce waste.”
Sessions focused on fostering collaboration. Liz Remillong, Vice President, Core Linen emphasized, “Everything we discuss today benefits the plant and operations, helping to improve both customer service and plant performance.”
Networking and Collaboration
The second day focused on applying these concepts to real-world scenarios. Dan Sanchez, President, Sanchez Advisory Group led role-playing exercises, helping linen managers gain buy-in from hospital stakeholders. On the operations side, Bob Corfield, CLLM, CEO, Laundry Design Group, facilitated a sequencing activity, encouraging operators to apply workflow management strategies. “If they can come away with just those small, low-hanging fruit improvements, it can help improve workstation ergonomics and process throughput,” said Corfield.
Networking was a key element of the conference. The Margaritaville Mixer, sponsored by Future Polytech, encouraged attendees to connect in a relaxed, fun atmosphere. “The networking is amazing… everyone is so willing to share their knowledge and experiences,” said Christine Arnold-Tun, RLLD, CLLM, Assistant Managing Director, Belize Commercial Laundry and Linens.
The event concluded with the Tropical Paradise Reception, sponsored by Positek RFID, offering a chance for attendees to continue their conversations and deepen connections.
A Memorable Experience
The Elevate Conference successfully combined expert-led learning, hands-on activities, and networking. “I think it was a great workshop, in that, you get to network with others who do your job, and also in the way that you get to take some simple take-homes that you can implement right away in your laundry facility, and your day-to-day life,” said Chip Malboeuf, Vice President, Operations and Engineering, ImageFIRST and ALM Chairman.
For more information on upcoming ALM events, visit ALM’s Website or follow ALM on social media.
CLATA Holds Annual General Meeting
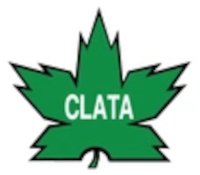
The Canadian Laundry Allied Trades Association (CLATA) held it’s Annual General Meeting, and announced the Board of Directors for 2025-2026.
CLATA’s AGM was held on April 3, 2025 in Toronto, Ontario.
2025-26 Board of Directors
- Ashlynn McConvey (Dalex Canada Inc.), President
- Earl Eichen (Lavanett Equipment), Past President
- Steve Freeman (CLATA), Secretary
- Trevor Holmes (CLATA), Treasurer
- Malcolm Caldwell (Harco Co. Ltd.), Director
- Patrick Robertson (Tingue Canada), Director
- Denis Lamarre (Lavanett Equipment), Director
- Marc-Antoine Gelac (Kannegeisser Canada), Director
- William Kahan (Unipress Corp.), Director
- Artur Keyes (Extox Industries), Director
CLATA’s annual golf tournament will be held on Thursday, September 11th at the Bay of Quinte Golf Club. Registration information will be shared at a later date. We had a record turnout at the Golf Tournament in September 2024, with 48 players and 2 people walking the course for a total of 50 people. Overall a great success.
Given the current political environment, discussions are under way with the board of directors in regards to the CLATA reception at this year’s Clean Show in Orlando.
The next AGM is tentatively scheduled for March 26th, 2026 in Toronto.
Harco receives “Top Performer” recognition for UniMac
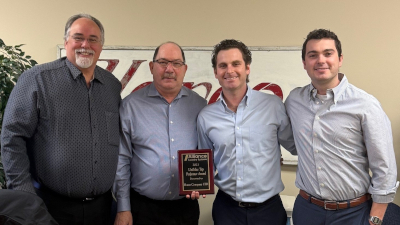
Harco was recently recognized by UniMac brand of Alliance Laundry Systems as a “Top Performer.” Phil Lapenta from Alliance presented the award to the Harco team during a recent visit to the Harco head office in Mississauga, ON.
TRSA Announces Two Industry Awards
The Textile Rental Service Association (TRSA) announced it’s two major annual awards: the Maglin-Biggie Lifetime Achievement Award and the Operator of the Year Award.
Maglin-Biggie Supplier Partner Lifetime Achievement Award: David Tingue
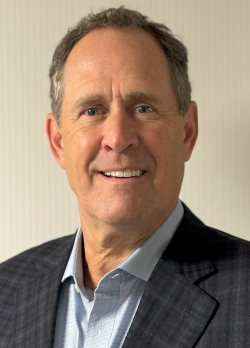
David Tingue, the CEO of Tingue, Brown & Co., Peachtree City, GA, has been honored with the 2025 Maglin-Biggie Supplier Partner Lifetime Achievement Award. This award is a testament to Tingue’s exceptional leadership, his significant contributions to the linen, uniform and facility services industry, and his steadfast dedication to excellence.
“I’m incredibly honored to receive the TRSA Supplier Partner Lifetime Achievement Award,” Tingue said. “I feel a bit overwhelmed by this honor, as it has me reflecting on the many individual mentors and influencers in my life. Above all is my father, Bill Tingue, who was a recipient of this award in 2003. Dad showed me that you can come out on top while acting like a gentleman. The names of past recipients are truly humbling – these are my idols, and they always will be. Thanks to all of them for setting such a great example.”
Tingue is a stalwart of the commercial laundry industry and has had many highlights throughout his career. He led Tingue in building a global presence, solidifying a versatile supply chain that has weathered financial crises and pandemics, so that Tingue’s laundry customers were never without their necessary consumables, spare parts and local service. Under his leadership. Tingue has opened and acquired businesses in Hong Kong, Canada, the Caribbean and Ireland. He is also a visionary in digitalizing Tingue’s operations – launching an e-commerce platform in 2023 that has been widely accepted and is already depended upon by hundreds of laundry operators in their chosen global markets, including more than 100 different TRSA members.
Tingue has dedicated much of his professional time to TRSA, serving on various committees (Healthcare, Marketing, Strategic Management, Strategic Planning and, his personal favorite, the Government Relations Committee), and serving a term on the Board of Directors (2002-’04). He is a graduate of TRSA’s SMI (Sales and Marketing Institute) and is a consistent TRSAPAC contributor. A constant cheerleader for TRSA programs – he has sent dozens of Tingue employees to EMI, MMI, PMI, committees and various TRSA-sponsored events.
Tingue became the fourth-generation family manager of the firm in 1992 after earning an MBA degree from Cornell University’s Johnson Graduate School of Management. He held various management positions in the Tingue division, becoming president in 2000. In January 2007, David succeeded his father, William J. Tingue, as CEO of the parent company. Under David’s leadership, the business has closed 18 acquisitions, three business divestitures and six real estate deals.
David resides in Tampa, FL, with his wife, Andrea, and their 14-year-old daughter Hayden. Their daughter Darby (27) is a marketing executive in Chicago. Son John is the fifth-generation Tingue in the family business. A regional sales manager based in Chicago, John oversees six sales reps for the company while actively influencing the company’s digital capabilities. He is married to Hannah, who is expecting the family’s first grandchild this summer.
“We recently launched a new mission statement at Tingue: Fostering a benevolent culture that drives us to be the familiar, friendly and trusted solution for our laundry partners,” Tingue said. “This Lifetime Achievement Award suggests that we are on the right path. While this award marks a significant milestone, I believe there is still more to contribute. I look forward to continuing to support and advance the industry, ensuring that the next generation can build on the strong foundation we’ve all worked so hard to establish. Thank you to my friends of the TRSA.”
Tingue will receive the award at TRSA’s 112th Annual Conference, scheduled for May 13-15 at The Grand Hyatt Indian Wells Resort & Villas in Indian Wells, CA. Registration and details can be found at www.trsa.org/annualconference.
Operator of the Year Award: Douglas “Woody” Ostrow
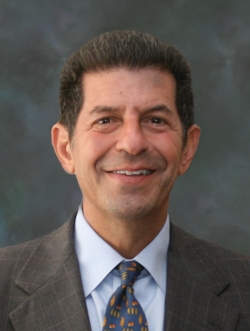
Douglas “Woody” Ostrow, President of CleanCare, Pittsburgh, will be honored with the TRSA Operator Lifetime Achievement Award at the 112th TRSA Annual Conference taking place May 13-15 at the Grand Hyatt Indian Wells Resort & Villas in Indian Wells, California. The award presentation will be held during a special dinner on May 15.
A third-generation leader in the industry, Ostrow has dedicated more than 50 years to the linen, uniform, and facility services industry. “My father won this award as well,” said Ostrow. “Without any false modesty, I don’t like recognition. I’d rather stay in the background. So, winning this award is a very flattering honor, and I’m proud to accept it.”
The award pays tribute to exceptional personal service to TRSA and the linen, uniform and facility services industry as nominated by past operator award peers and voted on by the TRSA Executive Committee. Winners have supported the association for decades, devoting their own time to association activities and facilitating their employees’ involvement in TRSA. Their teams have taken advantage of a wide range of TRSA activities, including certification, in-person and virtual events, and benchmarking surveys.
Ostrow has been recognized for a lifetime of service to TRSA and the industry. For TRSA, he served as chair (2010-’12), vice chair (2007-’09), treasurer (2005-’07) and a member of the Board of Directors (2004-’07) and the TRSA Executive Committee. He also served a pivotal role on the transition committee that oversaw the merger of TRSA with the Uniform and Textile Service Association (UTSA), which served the industry for 75 years and blended with TRSA in 2008. Additionally, Ostrow chaired the search committee that hired current TRSA President & CEO Joseph Ricci in March 2010.
Ostrow’s dedication to furthering the industry’s best interests has been reflected in other volunteer leadership positions, as he also chaired TRSA’s Operations Committee from 1981-’83 and served on the association’s Government Relations Committee. During his time on TRSA’s Board of Directors, Ostrow also was an active member of TRSA’s Healthcare Committee. In addition, he is a founding member of HOSLIN, a hospital linen cost and analysis trade group, and served on the MEDtegrity Executive Board.
Michael Potack, a former TRSA Lifetime Achievement Award winner who served on TRSA’s Board of Directors with Ostrow, said, “Woody was always very tuned in. He paid attention and was interested in how the industry worked and his company worked. He has provided a lifetime of service to TRSA and other industry groups, and his company has been a good citizen in his community in the Pittsburgh area.”
Ostrow and his family have a long tradition of involvement with TRSA dating back to 1934. Ostrow’s grandfather, Moe Struminger, was president of TRSA’s predecessor organization, the Linen Supply Association of America (LSAA), from 1949-’51, and Ostrow’s father, Gerald Ostrow, was president of TRSA from 1987-’89.
Ostrow joins 39 past recipients who have received the award since its 1982 inception, the most recent of whom were:
2024: Jim Buik, Roscoe Co., Chicago, IL
2023: Jim Vaudreuil, Huebsch Services, Eau Clare, WI
2022: Brian O’Neil, California Linen Services, Pasadena, CA
2020: Bob Brill, Republic Master Chefs/American Textile Maintenance, Los Angeles, CA
2019: Tom Watts, Prudential Overall Supply, Irvine, CA
2018: Steve Larson, Alsco Uniforms, Salt Lake City, UT
2017: Ronald Croatti, UniFirst Corp., Wilmington, MA
2016: Steve Bryant, Wildman Uniform & Linen, Warsaw, IN
2014: Michael Potack, Unitex Textile Rental Services, Mount Vernon, NY
2013: Richard Senior, Morgan Services, Chicago, IL
For more information and to register for the TRSA Annual Conference, visit www.trsa.org/annualconference.
MARCH 2025
EVI Industries to Acquire Girbau North America
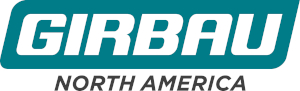
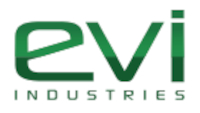
Girbau North America (GNA), Oshkosh, WI, announced on March 3 that it is being acquired by EVI Industries Inc. (EVI), Miami. Terms of the deal were not disclosed.
GNA, formerly a subsidiary of Girbau, will conduct business as usual moving forward without changes to leadership, staff, services, support or culture, according to GNA President Mike Floyd. “We remain dedicated to our customers, and now our resource pool of products, knowledge and services has grown thanks to the many partners of EVI across the United States,” Floyd said. “Simultaneously, we continue to rely on Girbau’s expertise and leadership in manufacturing to deliver best-in-class laundry solutions.”
GNA is EVI’s 30th and largest acquisition in the commercial laundry distribution and service industry. By joining EVI Industries, GNA gains access to a growing network of laundry distributors and service providers, positioning the company for accelerated growth and expanded market reach while maintaining its role as a key partner of Girbau.
“Joining EVI Industries marks an exciting new chapter for Girbau North America,” Floyd said. “EVI’s commitment to the laundry industry aligns perfectly with our mission to provide world-class equipment and services to our customers. This partnership enhances our ability to serve the laundry industry with even greater efficiency and innovation through an expanded base of laundry solution tools and programming for all GNA customers.”
EVI Industries has rapidly expanded its presence in the laundry industry through strategic acquisitions, integrating leading distributors and service providers to create a robust, customer-focused network. The addition of GNA further strengthens EVI’s ability to offer comprehensive laundry solutions across multiple market segments.
“We are thrilled to welcome Girbau North America to the EVI family,” said President and CEO Henry Nahmad. “Girbau North Amercia’s strong brand reputation, comprehensive product offerings, dedicated team and customer-centric approach make them an ideal addition to our growing platform. Together, we will continue to set new standards in commercial and industrial laundry solutions while preserving GNA’s strong relationship with Girbau as a key manufacturing partner.”
GNA maintains its long-standing role in representing Girbau-manufactured laundry solutions, just as it has for the past 30 years. “With EVI’s competitive influence, we anticipate an accelerated pace for bringing new products from Girbau and other business partners to market,” Floyd added.
From Girbau’s perspective, this transition presents an opportunity to continue innovating and growing alongside GNA. “We are excited to continue our strong collaboration with GNA under this new structure,” said Chair and CEO of Girbau, Mercè Girbau. “For years, we have worked together to deliver industry-leading solutions, and this next chapter will enable us to drive further innovation and create even greater value for our customers.”
GNA will continue to operate under the Girbau North America name, ensuring continuity for existing customers, distributors and partners. To learn more about GNA, visit www.gnalaundry.com.
Association of Wedding Gown Specialist Gathered in Ft. Worth, TX
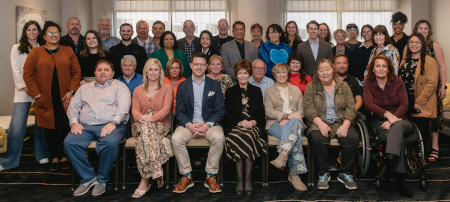
Members of the Association of Wedding Gown Specialists (AWGS) met recently in Fort Worth, Texas. In addition to the traditional tour of the host member’s plant, Kite’s Cleaners and Pinstripes, owned and managed by Nathan Kite, guest speakers included designer Callie Tein of Luna d’Miel Bridal, Emily Foster of Emily Foster Creative, Tracy Aaron of Wedding and Party Network, Kayla Fogarty of TheKnotWW.com, and Michael Tungesvick of Sankosha-USA.
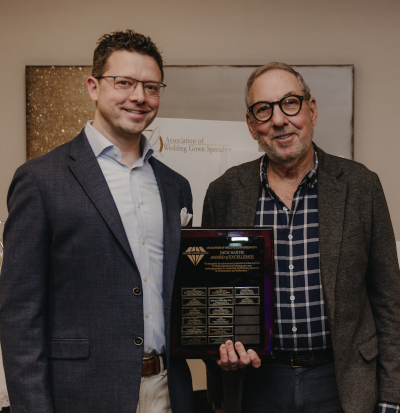
As always, a highlight of the meeting was the presentation of the fourteenth annual Jack Barth Memorial Award of Excellence. Initiated by Linda Stokes-Barth in remembrance of her late husband and his achievements in the dry cleaning industry, the award recognizes an AWGS member for advancement, promotion, and development of industry standards for wedding gown care as well as for outstanding contributions and service to the Association and its members.
This year’s recipient, Ken Kinzer of Bridgestone Cleaners in Brooklyn, New York, began his garment-care journey more than four decades ago in 1983. In that time, Kinzer has achieved respect in the industry and pioneered eco-friendly techniques as well as taken on many leadership roles. Always a strong advocate for the industry, he has served as President of the National Cleaners Association, led community initiatives such as the Brooklyn Coats for Kids Campaign, and received numerous awards from groups such as the Clothing Care Council.
AWGS president Kyle Matthews of Janet Davis Cleaners in Berkley, Michigan, presented the Barth Award to Kinzer, who first represented AWGS in Brooklyn and then expanded into Manhattan, the Bronx, and Westchester County, New York. “Kinzer’s clients describe his work as nothing short of meticulous and masterful,” said Matthews, “and one reviewer summed it up perfectly with the comment that ‘Ken treats every gown like it’s a priceless heirloom—because to the bride, it is.’ Ken, your leadership, craftsmanship, and commitment to AWGS make you more than deserving of this honor.”
Other speakers at the event included AWGS members Nadine Rana of Style and Grace Cleaners in Toronto, Ontario, and Ben Feingold of Fabricare Center Cleaners in Atlanta, Georgia on the topic of TikTok as well as Jan Barlow of Jan’s Professional Dry Cleaners in Flint, Michigan, on best hiring and incentive practices.
In addition to speakers, there was a series of round-table conversations offering everyone in the group the chance to discuss topics ranging from “must” updates for websites to keeping mechanical employees happy. AWGS table hosts included Jan Bohn of Margaret’s Cleaners in San Diego, California, on handling luxury garments, Marissa Gonzales of Five Star Wedding Gown Specialists in San Antonio, Texas, on starting a wedding alterations department, Melisa Soonius of Kite’s Cleaners and Pinstripes in Dallas/Fort Worth, Texas, on scheduling gown pick-up and delivery, and Margaret Butler of Dublin Cleaners in Dublin, Ohio, on developing a start-up video.
Matthews presided over the installation of officers who are vice president Rana, secretary-treasurer Rhonda Wernick of Oakwood the Greener Cleaners in Nashville, Tennessee, and immediate past president Kermit Engh of Methods for Management. Malcolm MacGregor of Brown’s Cleaners in Ottawa, Ontario, is chair of the Budget and Finance Committee.
Incoming members of the Board of Directors are Feingold and Kerryn Wollington of LDC Luxury Drycleaning in Cardiff, New South Wales, Australia.
Members new to the Association are Nina Lapin and Roman Cheb of Greenacres Cleaners and Alterations in Spokane Valley, Washington, Cameron Bastien of Carousel Cleaners in West Vancouver, British Columbia, Chad McMurtrie of Pristine Dry Cleaners in Tauranga, Bay of Plenty, New Zealand, Matthew Hyde of Hyde’s Quality Drycleaners in Gisborne, Victoria, Australia, and Bill Hudson of Cressbells Dry Cleaners in Ballarat, Victoria, Australia.
Sponsors of the event were Kreussler, Inc., Foster-Stephens, Inc., Sankosha-USA, Inc, Select Risk Insurance, and Kleerwite Chemicals.
AWGS is a not-for-profit trade association with members in nine countries. Members are certified to ensure that wedding gowns and heirloom textiles of all kinds are cleaned according to established museum standards and preserved in archival-quality materials. Wedding couples benefit from the personal, interactive service offered by wedding gown specialists in local communities, but the guarantee is truly an international warranty because each member honors the guarantee of every other member no matter where in the world they may be. Also, for every gown preservation, AWGS partners with the international Arbor Day Foundation to plant a tree in celebration of the bride’s wedding in a forest of great need.
AWGS members benefit from both trademarked logos and other promotions such as wedding gown care labels and recommendations from more than 70 gown designers including Romona Keveza, Modern Trousseau, Paloma Blanca, Justin Alexander, and Enzoani.
AWGS’s MuseumCareTM preservations are also Endorsed by the Association of Bridal Consultants, the professional organization dedicated to wedding planners and professionals worldwide
For more information about training and membership, call the Association office
at 800-501-5005 or go to www.WeddingGownSpecialists.com or www.WeddingGownSpecialists.net.au.
DLI Launches Industry-Wide Social Media Campaign
DLI’s Social Media Action Committee has worked quietly behind the scenes to develop a program to benefit all drycleaners. They are encouraging professional garment care providers (members and non-members of DLI) to share a new series of social media posts, currently under development.
The posts will be designed by the committee with help from a social media consulting firm. The main goals are to educate consumers on the value and convenience of professional cleaning. Think of the famous Got Milk? campaign, but powered by social media posts instead of millions of advertising dollars.
DLI Launches Industry-Wide Social Media Campaign
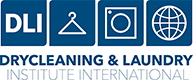
DLI’s Social Media Action Committee has worked quietly behind the scenes to develop a program to benefit all drycleaners. They are encouraging professional garment care providers (members and non-members of DLI) to share a new series of social media posts, currently under development.
The posts will be designed by the committee with help from a social media consulting firm. The main goals are to educate consumers on the value and convenience of professional cleaning. Think of the famous Got Milk? campaign, but powered by social media posts instead of millions of advertising dollars.
2025 DLI Hall of Fame Nominations soon to open
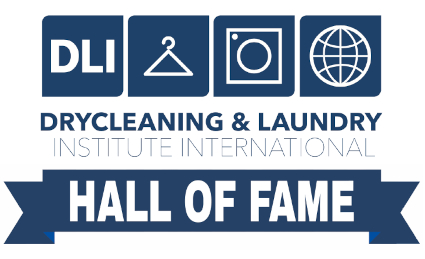
The Drycleaning & Laundry Institute is getting ready to open nominations for the Hall of Fame 2025. If you submitted a nomination last year and it was not chosen, consider submitting your 2024 candidate again this year. Last year was the inaugural year for the program and DLI had an impressive list of candidates.
“The one thing I would stress is that the decision is made purely on the strength of the nomination form. The review process attempts to turn a blind eye to the name of the individual and is judged on the merits of what is written on the form,” said Mary Scalco of DLI.
Nominations will be accepted for the 2025 Hall of Fame from April 1 to May 15. Please visit DLIonline.org/HoF to access the nomination form at that time. If you have any questions please do not hesitate to reach out, mscalco@dlionline.org.
Kudos to Free Laundry Access Program for great Toronto Star coverage!
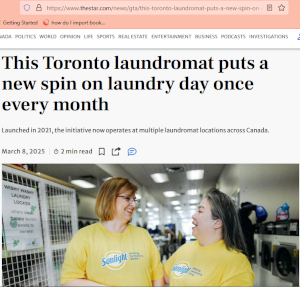
If you’ve met Nancy Seto of Yummi Cafe Laundromat, you know she’s passionate about the Free Laundry Access Program she launched in 2023, with sponsor Sunlight Detergent. And she’s a master at getting publicity for the program. If you want to see how to do public relations right, check out the full page article in the Toronto Star from earlier this week! Well done, Nancy, and congrats to Jim St. Pierre and wife Dahna Sanderson, co-owners of Wishy Washy Coin Laundry, for joining this worth-while program.

Housing is now open for the Clean Show — so jump on your reservations ASAP to ensure you get the hotel you want. The closer hotels fill up fast! For information, go to the Clean Show website
PayRange acquires laundry operating system Turns
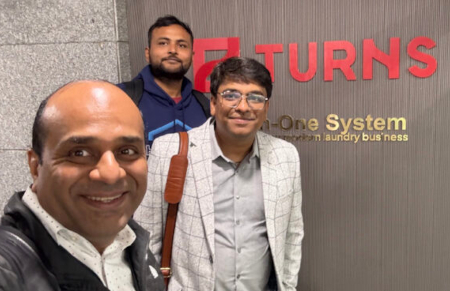
US company PayRange – a pioneer in mobile payment solutions for unattended retail businesses – has acquired Turns, an all-in-one laundromat operating system.
The acquisition is aimed at enabling the laundromat industry to transform by creating an industry-first platform, combining the machine payment platform with Turns’ new age laundry operating system. Among other things, the system includes business management, pickup and delivery management software, point-of-sale and payments. In that respect, the industry platform will provide single-store and multi-location laundry owners with a unified solution for their entire business – from machine payments to wash-dry-fold service to pickup and delivery.
Founder of Turns, Sukanth Srivastav, states that his platform was built to redefine laundromat management and that together with PayRange they can play an important role in the future of the laundromat business. Sukanth: “The vision is clear: a platform that doesn’t just process payments but transforms laundromat operations entirely. Within the next 24 months, we aim to power more than 5,000 laundromats across the U.S. – giving owners the tools to grow, scale, and create exceptional customer experiences.”
TRSA Lays the Groundwork for Action in Canada
(From TRSA)
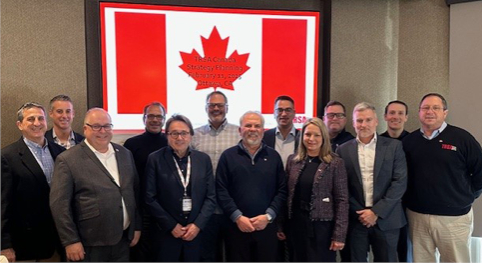
Due to the growing need for the linen, uniform and facility services industry to have representation in Canada, TRSA recently organized a planning meeting in Ottawa to develop a strategic approach to advocacy and define industry issues. TRSA’s Canadian Legislative Team, The Wellington Group, helped facilitate the meeting with a select government relations working group led by Randy Bartsch, TRSA chair; Joseph Ricci, president and CEO of TRSA; and Kevin Schwalb, TRSA’s vice president of government relations.
During the meeting, attendees heard from Canadian Senator Daryl Fridhandler and Mike de Jong, a former member of the British Columbia Legislative Assembly, to gain an understanding of the policy climate at both the federal and provincial levels of Canadian government.
The attendees discussed a wide array of topics impacting the industry such as tariffs, environmental concerns surrounding microplastics and PFAS, and currency exchange, to name a few. After deliberation, the group narrowed in on three specific issues in which TRSA will concentrate to help create Canadian jobs, improve supply-chain security and reduce costs and waste.
The three issues that the group agreed upon include:
- Increasing the use of reusable textiles
- Securing tax incentives that encourage reinvestment
- Reducing inter-provincial business impediments to help the business climate for the industry
“Our recent meetings in Ottawa were a defining moment for TRSA as we strengthen our advocacy for our members operating across Canada,” Bartsch said. “As the association’s first Canadian chair, I was truly inspired by the engagement and focus of our GR working group – a broad mix of TRSA members from the healthcare, industrial and hospitality sectors, which included family-owned firms, co-operatives and large multinationals, all united in serving the linen, uniform and facility service needs of Canadian businesses from coast to coast. Our clear advocacy priorities – promoting reusable textiles, pushing for tax policies that support capital reinvestment and reducing interprovincial trade barriers – lay out a bold roadmap to help our members drive job creation, enhance supply-chain resilience and build a more sustainable future for Canada.”
Ricci added that, “These issues provide a framework for TRSA’s advocacy efforts to promote, expand and protect the linen, uniform and facility services industry in Canada. The timing and scope of our efforts in Canada is especially critical given the recent developments in the United States and Canadian politics and relations.”
2025 Best Plants and 10 Other Top Awards Presented at Annual Industry Conference
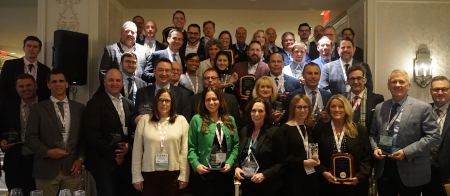
TRSA member companies and their exemplary individual performers were honored by their peers Feb. 5 for their pursuits as employers, service providers, marketers and community leaders.
The ceremony at the Annual Industry Awards Dinner at TRSA’s 15th Annual Legislative Conference culminated in the presentation of Best Plants accolades to industry leading facilities for their comprehensive efforts to improve capabilities to supply, launder and maintain linens and uniforms. They cite statistical results across a wide range of indicators from environmental stewardship to productivity improvement. Winners of the highest honor (Gold level) in this category were:
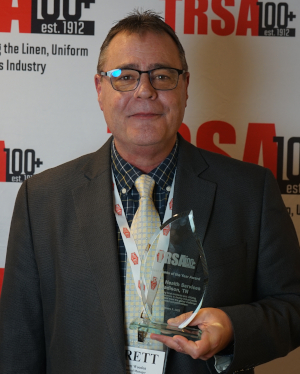
NOVO Health Services, Madison (Nashville), TN – Opened in 2016, the facility underwent major refurbishment of existing equipment in 2024, upgrading two tunnel washers, presses, dryers, ironer/folder/feeders and blanket blasters. The tool room and engineering shop were renovated. About 7,000 square feet of plant space was renovated, with the finished goods end of the plant adding 900-plus feet of trolley storage for garments shipped to depots. A boiler and make up water system/tank were added. The facility produces 55,000 lbs. (24,947 kg.) daily and has 75 employees.
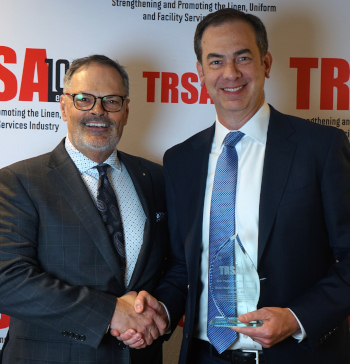
Unitex Healthcare Laundry Services, Lawrence, MA – The plant, opened in 2020, produces more than 160,000 lbs. (72,574 kg.) per day and has 221 employees. It scored high marks for technology upgrades, namely a 2024 transition to new business management software (route accounting). Extensive efforts to determine customer satisfaction were cited. Performance measures cover responsiveness, frequency of in-person visits, customer service, transportation and delivery, product quality and overall linen service. Each main linen item’s quality is individually rated.
The full list of award winners
Above & Beyond Service
Honoring exceptional attention to customer needs by individuals and organizations, setting a high standard for others to follow, as selected by industry peers.
GOLD
- Alliant Systems | Irving, TX
- Foltex USA | Columbia, SC
- Jim Baker | Loop Linen | Westwego, LA
SILVER
- T.J. Peterson | TJP Laundry Maintenance Solutions | Janesville, WI
HONORABLE MENTION
- Customer Service Team | LinenMaster | Vero Beach, FL
- Ed Shanks | Ecolab Textile Care | St. Paul, MN
- Marlene Frias | NOVO Health Services | Atlanta, GA
- Systems Performance Team | Kannegiesser ETECH | Minneapolis, MN
Advertising Effectiveness
- G.A. Braun | North Syracuse, NY
- Jensen USA | Panama, FL
Best Plant to The Year
Honoring achievements, surmounting obstacles and citation of statistical results across a wide range of indicators of improved capabilities, from environmental stewardship to productivity gains.
GOLD
- NOVO Health Services | Madison, TN
- Unitex Healthcare Laundry Services | Lawrence, MA
SILVER
- Alsco Uniforms | Vista, CA
- PureStar Group | Norwich, CT
HONORABLE MENTION
- UniFirst Corporation | Hammond, IN
- Wildman Business Group | Warsaw, IN
- | Englewood, CO
Clean Green Innovation
Honoring leadership in reducing environmental impact, aligned with best management practices of the TRSA Clean Green standard, as selected by industry peers.
GOLD
- HLS Linen Services | Ottawa, ON, Canada
- PureStar Group | Brady Linen | Las Vegas, NV
SILVER
- UniFirst Corporation | Wilmington, MA
HONORABLE MENTION
- Ecolab Textile Care | St. Paul, MN
- Penn Emblem | Philadelphia, PA
Company Community Service
Honoring significant contributions to communities by organizations, reflecting their care for and sense of responsibility to the public. Industry peers select winners.
GOLD
- Adrienne Dirosario | NOVO Health Services | Atlanta, GA
- Deanne Banton | Nixon Medical | New Castle, DE
- PureStar Group | Las Vegas, NV
SILVER
- Bates Troy, Inc. | Binghamton, NY
- Chad Renegar | NOVO Health Services | Rockmart, GA
HONORABLE MENTION
- A1 American | Pacoima, CA
- Cintas Corporation | Mason, OH
- UniFirst Corporation | Wilmington, MA
Diversity Recognition
Honoring leadership in valuing the uniqueness of individuals and encouraging and facilitating variation in human qualities in the workforce, as selected by industry peers.
GOLD
- Adrienne Dirosario | NOVO Health Services | Atlanta, GA
- Deanne Banton | Nixon Medical |New Castle, DE
- PureStar Group | Las Vegas, NV
SILVER
- CW Resources | New Britain, CT
HONORABLE MENTION
- HLS Linen Services | Ottawa, ON
Fleet Graphics
GOLD
- U.S. Linen & Uniform | Richland, WA
SILVER
- Arway Linen & Uniform Rentals | Philadelphia, PA
- NOVO Health Service | Simple | Atlanta, GA
HONORABLE MENTION
- UniFirst Corporation | Wilmington, MA
Member Engagement
Honoring exemplary participation in the wide range of TRSA activities that improve individual and corporate performance.
GOLD
- Dempsey Uniform & Linen Supply | Jessup, PA
- HHS-FMA Laundry | St. Paul, MN
- Alliant Systems | Irving, TX
- Jensen USA | Panama City, FL
- Pellerin Milnor | Kenner, LA
SILVER
- Miller’s Textile Services | Wapakoneta, OH
- Superior Linen Service | Tulsa, OK
- UniFirst Corporation | Wilmington, MA
SafeTRSA Excellence Award
Honoring leadership that embraces safety as a true corporate value, indicated by exceptional support from top management, plus employee involvement, training and communication. Industry peers select winners. as selected by industry peers.
GOLD
- UniFirst Corp. | Owensboro, KY
SILVER
- PureStar | Las Vegas, NV
TRSA Legislator of the Year Award
Honoring the U.S. legislator who is most supportive of the linen, uniform and facility services industry. The TRSA Government Relations Committee selects awardees.
- Rep. Danny Davis | House of Representatives (D-IL)
Best Video
Honoring creativity and messaging in video, whether purely informative (showcasing employees, products or services) or technical (describing capabilities, processes or training).
GOLD
- HLS Linen Services | Ottawa, ON
- Magic Laundry Services | Montebello, CA
- Unitex Healthcare Laundry Services | Elmsford, NY
SILVER
- American Textile Maintenance | Los Angeles, CA
- G.A. Braun | North Syracuse, NY
- ImageFIRST Healthcare Laundry Specialists | King of Prussia, PA
HONORABLE MENTION
- Republic Master Chefs | Los Angeles, CA
- Service Uniform | Englewood, CA
For the 2026 TRSA Industry Awards, members are encouraged to visit the awards pages on the TRSA website to learn more about the honors and how to nominate candidates for next year.

It’s Going to be a Great Show!
Clean Shows are always big. This week, Messe Frankfurt announced it is expanding the Show floor to accommodate more booths. So the BIG just got BIGGER.
If you haven’t made your plans yet, now is the time to think about it. Registration will open shortly, Housing will open in March. Booth space opened a few months ago. Get out your calendar, mark out August 23-26, and start planning your visit to Orlando. This is a no-brainer.
JANUARY 2025 NEWS
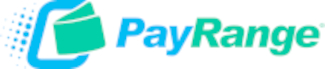
PayRange BluTap(TM) Self-Pour Technology Wins “Best Vending Solution” at the Automation & Self-Service Awards
Announced at the Self-Service Innovation Summit on December 10, 2024 in Tampa, Florida, the award honors innovators who are leading the way in the advancement of automation and self-service technologies.
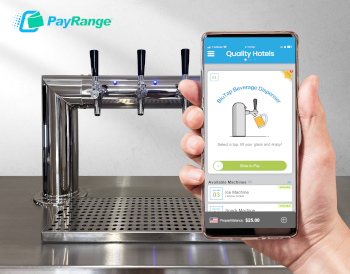
PayRange, an innovator in mobile payment solutions and hardware for automated retail, announced they were awarded the “Best Vending Solution” at the annual Self-Service Innovation Summit for their patented BluTap(TM) self-pour technology solution.
By seamlessly integrating connectivity, age verification, and cashless payments, BluTap transforms traditional beverage pour bars into a streamlined and compliant self-service bar experience, all through the convenience of the user’s smartphone.
Designed with both businesses and consumers in mind, users can seamlessly verify their age one time using the PayRange age verification services, ensuring every sale is a responsible and compliant transaction. BluTap also features built-in over-consumption controls, ensuring venues and businesses can responsibly sell unattended adult beverages.
The BluTap device simply installs on beverage equipment manufacturers’ tap equipment to enable the equipment to accept both cashless payments and age-verification. BluTap utilizes the connectivity of the user’s phone along with built-in encryption protocols to eliminate the need for network access, enhancing security and minimizing risks for businesses. This makes BluTap the most advanced and scalable solution in the industry. By seamlessly integrating into both new and existing beverage equipment, PayRange offers venues the smartest and most cost-effective way to generate new revenue streams while providing unique guest experiences. BluTap eliminated the shortcomings of other self-pour technology; no RIFD cards, manual ID checks, payment terminals, POS integration or dedicated network connections required. No other self-pour technology offers the level of advanced security features of the multi-factor verification and authentication that’s built into BluTap.
“We’re honored to have been awarded the “Best Vending Solution” at the Self-Service Innovation Summit and it further validates the market response we’ve seen. BluTap has been well received in the market this year. Our first installations have been with national franchised hotel brands, and we’ve had consistent inquiries from franchisees who have heard of the system and are interested in adding it to their properties,” stated Stephanie Cordisco, Executive Vice President for PayRange. “Self-serve beer and wine dispensing is an amenity well suited to hotel properties, many of whom are still dealing with labor shortages, allowing them to reallocate their staff to other tasks while still offering their guests the convenience of self-serve beverages in a responsible manner.”
PayRange focuses on solutions that remove friction in commerce, and BluTap does just that by either seamlessly integrating with existing beverage equipment with self-pour technology or as a complete turnkey solution for a beverage program. Connected to the 24/7 PayRange advanced backend software management system, operators can make decisions based on real-time sales data, allowing them to optimize and monitor their self-pour business proactively.
Additional information is available at: https://payrange.com.
America’s Best Cleaners Partners with Retold Recycling in Support of the #NoLandfill Movement to Reduce Textile Waste

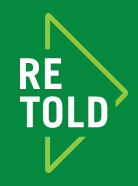
America’s Best Cleaners (ABC) announced a new and innovative partnership with Retold Recycling in support of the #NoLandFill movement to reduce textile waste and drive a more sustainable future for fashion. Launched on January 13, 2025, this collaboration will allow Retold to expand its impact by making recycling easier and more accessible through ABC’s wide network of affiliates.
The partnership between Retold and ABC is built on a shared mission: to tackle textile waste and keep it out of landfills. By combining their strengths, the two organizations are working toward a more sustainable future and are empowering consumers to make better, more eco-friendly choices.
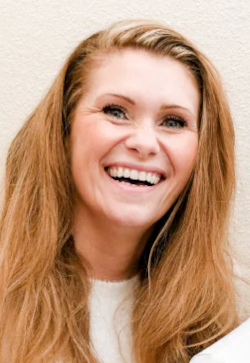
Retold co-founder and CEO Amelia Trumble shared, “At Retold Recycling, our mission and vision for the future is #nolandfill. This is why we are so thrilled to partner with America’s Best Cleaners to be our launch partner selling Retold’s “3 Bags in a Box” in participating member’s dry cleanering stores. The nucleus for this collaboration came directly from Mark Cuban from our episode of Shark Tank when he decreed that Retold bags should be sold in dry cleaners nationwide! Thank you to ABC and your members for this step-change in educating consumers on the importance of recycling textiles and partnering with us to provide a convenient solution to divert clothing and textiles from landfills.”
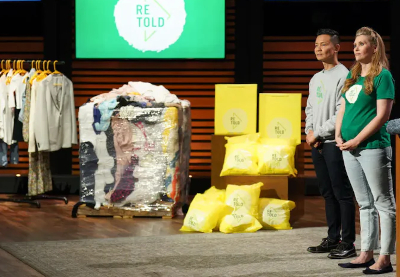
As part of the collaboration, Retold is launching a new product—“Three Bags in a Box”—which contains three compostable Retold bags, neatly packaged in a giftable box. This product offers eco-conscious consumers a convenient way to recycle their textiles while also serving as a sustainable gifting option. ABC affiliates will offer Retold Recycling’s “Three Bags in a Box” product directly to their customers, increasing the availability and convenience of textile recycling.
Retold accepts a wide range of textiles, including clothing, shoes, accessories, and household items like towels and bedding. All their recycling processes occur within the United States, ensuring transparency and control over the ethical handling of materials.
America’s Best Cleaners Executive Director Chris White says, “Our partnership with Retold Recycling is an exciting opportunity for America’s Best Cleaners affiliates to take a bold step toward a truly circular textile economy. By working together and championing the #nolandfill commitment, we’re creating innovative solutions to extend the lifecycle of garments and reduce environmental impact. This collaboration underscores our dedication to sustainability and positions our affiliates as leaders in driving meaningful change in the textile care industry.”
About America’s Best Cleaners:
America’s Best Cleaners is a certification agency and an industry-leading team of consultants who assist owners, managers, and team members to realize their full potential while striving for continued personal and professional success. For more information on America’s Best Cleaners and its Affiliates, visit the webpage.
DECEMBER 2024 NEWS
DLI School Offers 10 Complete Courses for 2025
Virtual Stain Removal Now Available in Spanish
Leadership & Customer Service Virtual Courses Added
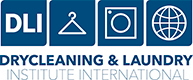
In 2025, the Drycleaning & Laundry Institute will split its virtual stain removal course into two parts, Basic Stain Removal Techniques and Advanced Stain Removal Techniques. Each course is four days long, running online Tuesdays and Thursdays over two-week periods in May, June, and July.
DLI also introduces a new Spanish language Four-Day Basic Stain Removal virtual course this November. DLI plans to expand this course into an in-person offering in the future. “Members asked for a Spanish version of our Stain Removal course,” said Brian Johnson, DLI’s Director of Education and Analysis. “We are pleased to work with Gina Hernandez, a DLI member in California to offer this course.”
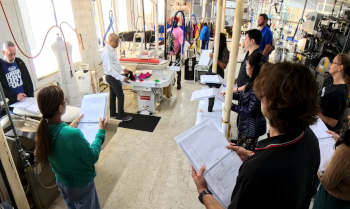
DLI members most frequently cited leadership and customer service as areas of concern on a recent survey. To meet this demand, DLI partnered with Jen Whitmarsh of Snappy Drycleaning and The Route Pros to offer two new virtual courses:
- Inspire & Influence: Leadership Virtual Course
- Service Superstars: Customer Service Representative Virtual Course
DLI continues offering its best-in-the-industry in-person courses at its training facility in Laurel, MD. DLI’s school equips managers and staff at all experience levels with the latest results-driven standards, empowering confident and efficient performance.
New Leadership & Customer Service Virtual Courses
DLI introduces two new two-day virtual courses to help managers and staff quickly develop crucial skills. Both courses will be instructed by Jennifer Whitmarsh with Snappy Dry Cleaning & The Route Pros.
Service Superstars: Customer Service Rep Course – July 29 & 31
Service Superstars is a high-energy virtual course designed to transform customer service professionals into exceptional brand ambassadors. This program focuses on building the skills and mindset needed to create unforgettable customer experiences, foster loyalty, and drive success. Participants will learn effective communication techniques, problem-solving strategies, and tools to handle challenging situations with confidence and grace. Seasoned professionals or industry newcomers will gain knowledge and techniques to exceed expectations, delight customers, and shine in every interaction.
Inspire & Influence: Leadership Course – September 9 & 11
Inspire & Influence is a virtual leadership course designed to empower individuals to become impactful leaders in today’s fast-paced world. This program focuses on mastering the art of inspiration, building trust, creating a dynamic culture, and fostering individual leadership to drive success in any team.
Through interactive sessions, real-world scenarios, and actionable strategies, participants will learn how to effectively communicate a company’s overall vision, motivate others, and create a lasting positive impact. Whitmarsh and DLI designed this course to equip emerging leaders and seasoned professionals with the tools to lead with confidence, authenticity, and purpose.
Mid-West Basic Stain Removal Techniques Hybrid Course
Building on the popularity of DLI’s 2023 and 2024 West Coast Stain Removal Courses, DLI offers a special hybrid edition of its Basic Stain Removal Techniques Course in 2025. The course covers three days of virtual learning and one day of on-site training at Sankosha’s Elk Grove facility in the Chicago area.
Hybrid Basic Stain Removal Techniques
Virtual: February 20, 25 & 27
On-Site: March 5
Virtual Stain Removal Simplification & Spanish Availability
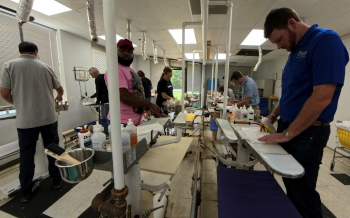
This year DLI expands its Virtual Stain Removal course into two sections: Basic Stain Removal Techniques and Advanced Stain Removal Techniques. With four-days of virtual learning each, these courses help students digest the information more efficiently and focus on fundamentals and more involved stain removal processes.
DLI will offer the Basic Stain Removal Techniques Virtual course twice in English and one session of its new Advanced Stain Removal Techniques Virtual Course in 2025. In addition, DLI presents Basic Stain Removal Techniques in Spanish in 2025. Gina Hernandez with Ortega Cleaners, a DLI Professional Member in San Juan Capistrano, CA will serve as instructor for this course.
Basic Stain Removal Techniques Virtual Course
May 6, 8, 13 & 15 (English)
July 8, 10, 15 & 17 (English)
November 11, 13, 18 & 20 (Spanish)
Advanced Stain Removal Techniques Virtual Course
June 10, 13, 17 & 19
On-Site Courses
DLI continues to offer its signature traditional in-person One-Week Introduction to Drycleaning and Two-Week Advanced Drycleaning courses twice in 2025. These courses are designed to teach students drycleaning principles and procedures that maximize quality and efficiency.
DLI’s On-Site Introduction to Drycleaning and On-Site Advanced Drycleaning courses run consecutively over a three-week period. Students who combine both courses receive a discounted rate.
On-Site One-Week Introduction to Drycleaning Course
DLI’s On-Site Introduction to Drycleaning Course is suited for experienced individuals or those who are new to the industry. It will run Monday through Friday from 9 a.m. to 4:30 p.m. at DLI’s School of Drycleaning Technology in Laurel, MD.
Some of the topics the one-week course explores include:
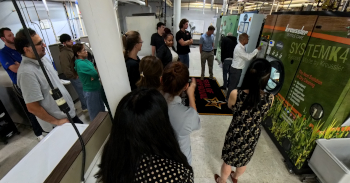
- sorting loads for drycleaning
- drycleaning science
- fibers and their characteristics
- fabric construction
- cleaning silk, satin and other fabrics
- soil and cleaning theory
- operating a drycleaning machine
- stain removal chemistry and procedures including removing ink, coffee, grease and other stains from clothing
- pressing pants, coats and skirts
- using tensioning equipment to improve finishing quality
- and more.
Tuition for DLI’s One-Week On-Site Introduction to Drycleaning Course is $2,165 for non-members. DLI members receive discounts ranging from 60% off to absolutely free depending on membership level.
On-Site Two-Week Advanced Drycleaning Course
DLI’s On-Site Advanced Drycleaning Course runs immediately after the On-Site Introduction to Drycleaning course.
The ten-day course is suited for those who have finished the introductory course or who have hands-on production experience and knowledge of basic stain removal and finishing techniques.
Course topics include:
- designing a cleaning plant with the most effective work flow
- pressing laundered shirts
- understanding the differences between solvents including perc, GreenEarth and hydrocarbon
- getting clean, white laundry
- cleaning and preserving wedding gowns
- current regulations facing the industry
- customer service techniques for cleaners
- using bleaches without damaging fabric color
- and more.
Tuition for DLI’s On-Site Advanced Drycleaning Course is $2,665 for non-members. DLI members receive discounts ranging from 67% off to absolutely free depending on membership level.
Spring 2025
387th One-Week Introduction to Drycleaning Course
March 24 – 28
387th Two-Week Advanced Drycleaning Course
March 31 – April 11
Fall 2024
388th On-Site Introduction to Drycleaning Course
October 6 – 10
388th On-Site Advanced Drycleaning Course
October 13 – 24
On-Site Complete Drycleaning Course
Students taking DLI’s On-Site Introduction to Drycleaning and On-Site Advanced Drycleaning Courses together enjoy a reduced tuition rate of $2,965 per student for non-members. DLI members receive discounts ranging from 20% off to free depending on membership level.
Complete Course information is available at DLIonline.org/Education
For more information or to register for any of DLI’s courses, contact DLI at (800) 638-2627 or visit www.DLIonline.org.
Thinking of attending? The Tom Kimmel Canadian Scholarship applies to any DLI class. Check the details on our Scholarship Page.
EPA bans Perc, TCE in final ruling
WASHINGTON – Today, Dec. 9, the U.S. Environmental Protection Agency (EPA) finalized the latest risk management rules for trichloroethylene (TCE) and perchloroethylene (PCE) under the bipartisan 2016 Toxic Substances Control Act (TSCA) amendments, marking another major milestone for chemical safety after decades of inadequate protections and serious delays. These protections align with President Biden’s Cancer Moonshot, a whole-of-government approach to end cancer as we know it.
TCE is an extremely toxic chemical known to cause liver cancer, kidney cancer, and non-Hodgkin’s lymphoma. TCE also causes damage to the central nervous system, liver, kidneys, immune system, reproductive organs, and fetal heart defects. These risks are present even at very small concentrations. Under today’s rule, all uses of TCE will be banned over time (with the vast majority of identified risks eliminated within one year), and safer alternatives are readily available for the majority of uses.
PCE is known to cause liver, kidney, brain and testicular cancer, as well as damage to the kidney, liver and immune system, neurotoxicity, and reproductive toxicity. Today’s final rule will better protect people from these risks by banning manufacture, processing and distribution in commerce of PCE for all consumer uses and many commercial uses, while allowing some workplace uses to continue only where robust workplace controls can be implemented.
“It’s simply unacceptable to continue to allow cancer-causing chemicals to be used for things like glue, dry cleaning or stain removers when safer alternatives exist,” said Assistant Administrator for the Office of Chemical Safety and Pollution Prevention Michal Freedhoff. “These rules are grounded in the best-available science that demonstrates the harmful impacts of PCE and TCE. EPA continues to deliver on actions that protect people, including workers and children, under the nation’s premier bipartisan chemical safety law.”
PCE and TCE are both nonflammable chlorinated solvents that are volatile organic compounds. PCE can biodegrade into TCE, and PCE may contain trace amounts of TCE as an impurity or a contaminant. The chemicals can often serve as alternatives for each other. For several uses of TCE that will be totally prohibited, there is an analogous use of PCE that can continue safely in perpetuity under workplace controls. Some examples of uses that will be prohibited under the TCE rule, but will continue under the PCE rule include: industrial and commercial use as an energized electrical cleaner, in laboratory use for asphalt testing and recovery, use to make refrigerants and other chemicals, and for vapor degreasing.
“Over 40 years ago, a mother named Anne Anderson from Woburn, Massachusetts, approached me and started a crusade to keep any more children like Jimmy Anderson, her son, from dying from cancer caused by toxic chemicals. Anne’s work directly led to this announcement from the Environmental Protection Agency that I am overjoyed to celebrate today alongside her and every community that stands to benefit—a finalized ban on trichloroethylene and most uses of perchloroethylene, two chemicals that cause cancer, affect reproductive systems, are neurotoxic, and compromise immune systems,” said Senator Ed Markey (D-MA). “Despite their dangers, these chemicals could still be found in industries like dry cleaning, automotive repair and manufacturing. With no doubt that these chemicals are deadly, there is no doubt that this final rule will save lives—especially our children’s lives—around the country.”
“The Camp Lejeune contaminated drinking water issue has dragged on over the better part of forty years ever since TCE, PCE and other organic solvents were first documented in the base’s drinking water supply in October 1980,” said Jerry M. Ensminger, Retired U.S. Marine Corps Master Sergeant. “My daughter, Janey, was conceived aboard Camp Lejeune during the drinking water contamination and died of leukemia in 1985, at the age of nine. I first began my fight for justice in 1997, and was later joined by Mike Partain in 2007, who was also conceived aboard the base and diagnosed with male breast cancer at the age of 39. Mike and I welcome this ban on TCE by the EPA and this is proof that our fight for justice at Camp Lejeune was not in vain.”
Trichloroethylene
TCE is used as a solvent in consumer and commercial products such as cleaning and furniture care products, degreasers, brake cleaners, sealants, lubricants, adhesives, paints and coatings, arts and crafts spray coatings, and is also used in the manufacture of some refrigerants. Safer alternatives are readily available for the majority of these uses.
EPA is finalizing its prohibition on all uses of TCE, most of which will be prohibited within one year, including TCE manufacture and processing for most commercial and all consumer products. This will protect most people who are likely to be exposed to TCE from uses covered by TSCA, including all consumers and workers in many sectors and many communities.
A limited number of uses in the workplace will be phased out over a longer period. Those uses will only continue with required stringent worker protections in place. All TCE uses with longer phaseout timeframes will have worker safety requirements, such as a Workplace Chemical Protection Plan that includes an inhalation exposure limit. The final rule sets a different inhalation exposure limit for airborne TCE than was proposed. This change was made in response to public comments to ensure the limit is feasible to implement and monitor while still reducing risk. EPA estimates that the new inhalation exposure limit would reduce long-term workplace exposure by 97%.
Many of the TCE uses that are continuing for longer than one year occur in highly industrialized settings that can adopt EPA’s new stringent worker protections, such as uses of TCE to clean parts used in aircraft and medical devices, to manufacture battery separators, to manufacture refrigerants, as well as in other transportation, security and defense systems.
For the use of TCE in manufacturing refrigerants, the longer timeframe supports fighting climate change by complementing efforts to phase down climate-damaging hydrofluorocarbons under the bipartisan American Innovation and Manufacturing Act.
All of these uses ultimately will be prohibited, but some of the exemptions associated with longer timeframes are necessary to avoid impacts to national security or critical infrastructure. In addition, some of the timeframes have been adjusted from the proposed rule based on public comment to allow reasonable time for transitioning to alternatives.
Further, to support cleanup activities at sites of past TCE contamination (e.g., Superfund sites), EPA is allowing essential laboratory use and proper disposal of TCE wastewater to continue for 50 years provided worker protections are in place, including the inhalation exposure limit set by today’s rule.
Learn more about the TCE rule.
Perchloroethylene
PCE is a solvent that is widely used for consumer uses such as brake cleaners and adhesives, in commercial applications such as dry cleaning, and in many industrial settings. Safer alternatives are readily available for the majority of these uses.
EPA is finalizing a 10-year phaseout for the use of PCE in dry cleaning to eliminate the risk to people who work or spend considerable time at dry cleaning facilities. Use of PCE in newly acquired dry-cleaning machines will be prohibited after six months. Compliance dates for machines that are already owned will vary depending on the type of the dry-cleaning machine used, with older types of machines being phased out sooner than newer ones. Many dry cleaners have already begun this transition. This timeline is unchanged from the proposed rule.
EPA’s final risk management rule requires companies to rapidly phase down manufacturing, processing and distribution of PCE for all consumer use and many uses at industrial and commercial workplaces, most of which will be fully phased out in less than three years. For most of the uses of PCE that EPA is prohibiting, EPA’s analysis found that alternative products with similar costs and efficacy to PCE are reasonably available.
The rule also finalizes stringent, achievable controls for continuing uses under a Workplace Chemical Protection Program. These rules generally occur in highly sophisticated workplaces that may be important to national security, aviation and other critical infrastructure, as well as uses that complement the agency’s efforts to combat the climate crisis. These uses include:
- Use in the production of other chemicals, including refrigerant chemicals that may complement efforts to phase down climate-damaging hydrofluorocarbons under the bipartisan American Innovation and Manufacturing Act.
- Use in petrochemical manufacturing.
- Use in agricultural chemical manufacturing (originally proposed to be prohibited).
- Use for cold cleaning of tanker vessels (originally proposed to be prohibited).
- Use as maskant for chemical milling.
- Use as a vapor degreasing solvent.
- Use in adhesives and sealants.
- Use in energized electrical cleaning (originally proposed to be prohibited).
- Processing into formulation, mixture or reaction products.
- Import, recycling, disposal, processing by repackaging and domestic manufacturing of PCE.
In response to public comments on the proposed rule, most workplaces now have 30 months instead of 12 months to fully implement the Workplace Chemical Protection Program. EPA also revised several other aspects from the proposal to strengthen and clarify aspects of the Workplace Chemical Protection Program, including monitoring requirements. EPA also ensured the employees’ designated representatives, such as labor union representatives, have access to occupational exposure monitoring and records.
Learn more about the PCE rule.
Additional Information
As a follow-up to consultations with small businesses, EPA plans to release compliance guidance for the use of PCE in dry cleaning and energized electrical cleaning in the coming months, as well as for the TCE rule. President Biden’s Fiscal Year 2025 budget requested funding to support small business efforts to transition to TSCA-compliant practices and mitigate economic impacts. If implemented, these grants could be used to support small businesses like dry cleaners in their transition away from PCE.
EPA will host a public webinar to explain what is in the PCE final rule and how it will be implemented on Wednesday, Jan. 15, 2025, at 12:30 p.m. EST. Registration is available on the Final Regulation of Perchloroethylene under TSCA webinar page.
ABS Laundry Business Solutions Announces Leadership Transition
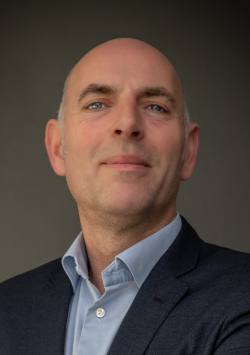
ABS Laundry Business Solutions, a part of Vitec Software Group, has announced a change in its leadership. Gerard van de Donk, the current Chief Executive Officer, will step down from his role effective January 1, 2025. Marien van Bezooijen has been appointed as the new CEO.
Gerard van de Donk, who became part of ABS in 1991, has played a pivotal role in guiding the company’s growth and accomplishing significant milestones over the years.
“It has been an honor to work with such a dedicated team and to see the company evolve. I am incredibly proud of what we’ve accomplished,” says van de Donk. “This transition is part of a thoughtful and deliberate succession plan. I am confident that Marien van Bezooijen, with his extensive experience and vision, will guide ABS to continued success.”
Van Bezooijen, who serves as the Chief Commercial Officer at ABS, brings a wealth of expertise and a strong background developed through years of dedication within the industry and organization. He has been recognized for his alignment with the company’s values and long-term goals. Van Bezooijen is committed to advancing the work of delivering high standards of service and innovation that ABS is known for.
“We have a talented Management Team and dedicated employees, and I am thrilled to lead ABS as we work closely together to achieve our objectives.” says van Bezooijen. “Together, we will continue to innovate, embrace change to remain competitive and uphold the high level of quality that our customers expect. I look forward to building on the strong foundation laid by Gerard and driving the company towards new heights.”
Gerard van de Donk will remain with the company as a Senior Advisor to ensure a smooth transition. He expresses his commitment to supporting the company’s mission and future endeavors.
“I look forward to watching ABS grow under Marien’s leadership,” he concludes.
About ABS
ABS Laundry Business Solutions, founded in 1987, specializes in providing innovative software solutions for the textile care and laundry industry. With over 750 installations worldwide and a dedicated team of 175 employees strategically located to provide local support, ABS delivers advanced technology, including its ABSSolute ERP software, to streamline laundry operations, boost efficiency, and enhance service quality. Serving a global client base, ABS offers tailored solutions for businesses of all sizes, from owner operated laundries to multinational organizations. As part of the Vitec Software Group, ABS benefits from the resources and expertise of the larger organization, ensuring continued industry leadership and innovation. For more information, visit www.abslbs.com.
JANUARY 2025 NEWS
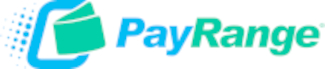
PayRange BluTap(TM) Self-Pour Technology Wins “Best Vending Solution” at the Automation & Self-Service Awards
Announced at the Self-Service Innovation Summit on December 10, 2024 in Tampa, Florida, the award honors innovators who are leading the way in the advancement of automation and self-service technologies.
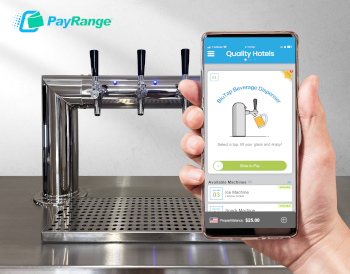
PayRange, an innovator in mobile payment solutions and hardware for automated retail, announced they were awarded the “Best Vending Solution” at the annual Self-Service Innovation Summit for their patented BluTap(TM) self-pour technology solution.
By seamlessly integrating connectivity, age verification, and cashless payments, BluTap transforms traditional beverage pour bars into a streamlined and compliant self-service bar experience, all through the convenience of the user’s smartphone.
Designed with both businesses and consumers in mind, users can seamlessly verify their age one time using the PayRange age verification services, ensuring every sale is a responsible and compliant transaction. BluTap also features built-in over-consumption controls, ensuring venues and businesses can responsibly sell unattended adult beverages.
The BluTap device simply installs on beverage equipment manufacturers’ tap equipment to enable the equipment to accept both cashless payments and age-verification. BluTap utilizes the connectivity of the user’s phone along with built-in encryption protocols to eliminate the need for network access, enhancing security and minimizing risks for businesses. This makes BluTap the most advanced and scalable solution in the industry. By seamlessly integrating into both new and existing beverage equipment, PayRange offers venues the smartest and most cost-effective way to generate new revenue streams while providing unique guest experiences. BluTap eliminated the shortcomings of other self-pour technology; no RIFD cards, manual ID checks, payment terminals, POS integration or dedicated network connections required. No other self-pour technology offers the level of advanced security features of the multi-factor verification and authentication that’s built into BluTap.
“We’re honored to have been awarded the “Best Vending Solution” at the Self-Service Innovation Summit and it further validates the market response we’ve seen. BluTap has been well received in the market this year. Our first installations have been with national franchised hotel brands, and we’ve had consistent inquiries from franchisees who have heard of the system and are interested in adding it to their properties,” stated Stephanie Cordisco, Executive Vice President for PayRange. “Self-serve beer and wine dispensing is an amenity well suited to hotel properties, many of whom are still dealing with labor shortages, allowing them to reallocate their staff to other tasks while still offering their guests the convenience of self-serve beverages in a responsible manner.”
PayRange focuses on solutions that remove friction in commerce, and BluTap does just that by either seamlessly integrating with existing beverage equipment with self-pour technology or as a complete turnkey solution for a beverage program. Connected to the 24/7 PayRange advanced backend software management system, operators can make decisions based on real-time sales data, allowing them to optimize and monitor their self-pour business proactively.
Additional information is available at: https://payrange.com.
America’s Best Cleaners Partners with Retold Recycling in Support of the #NoLandfill Movement to Reduce Textile Waste

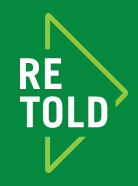
America’s Best Cleaners (ABC) announced a new and innovative partnership with Retold Recycling in support of the #NoLandFill movement to reduce textile waste and drive a more sustainable future for fashion. Launched on January 13, 2025, this collaboration will allow Retold to expand its impact by making recycling easier and more accessible through ABC’s wide network of affiliates.
The partnership between Retold and ABC is built on a shared mission: to tackle textile waste and keep it out of landfills. By combining their strengths, the two organizations are working toward a more sustainable future and are empowering consumers to make better, more eco-friendly choices.
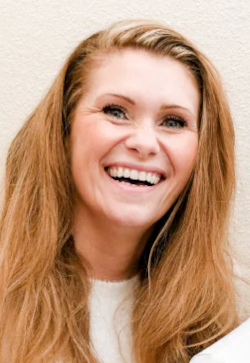
Retold co-founder and CEO Amelia Trumble shared, “At Retold Recycling, our mission and vision for the future is #nolandfill. This is why we are so thrilled to partner with America’s Best Cleaners to be our launch partner selling Retold’s “3 Bags in a Box” in participating member’s dry cleanering stores. The nucleus for this collaboration came directly from Mark Cuban from our episode of Shark Tank when he decreed that Retold bags should be sold in dry cleaners nationwide! Thank you to ABC and your members for this step-change in educating consumers on the importance of recycling textiles and partnering with us to provide a convenient solution to divert clothing and textiles from landfills.”
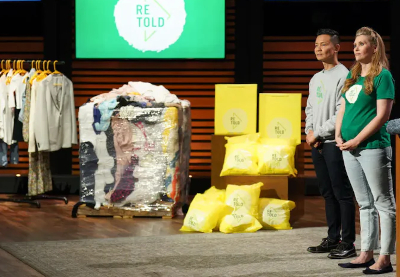
As part of the collaboration, Retold is launching a new product—“Three Bags in a Box”—which contains three compostable Retold bags, neatly packaged in a giftable box. This product offers eco-conscious consumers a convenient way to recycle their textiles while also serving as a sustainable gifting option. ABC affiliates will offer Retold Recycling’s “Three Bags in a Box” product directly to their customers, increasing the availability and convenience of textile recycling.
Retold accepts a wide range of textiles, including clothing, shoes, accessories, and household items like towels and bedding. All their recycling processes occur within the United States, ensuring transparency and control over the ethical handling of materials.
America’s Best Cleaners Executive Director Chris White says, “Our partnership with Retold Recycling is an exciting opportunity for America’s Best Cleaners affiliates to take a bold step toward a truly circular textile economy. By working together and championing the #nolandfill commitment, we’re creating innovative solutions to extend the lifecycle of garments and reduce environmental impact. This collaboration underscores our dedication to sustainability and positions our affiliates as leaders in driving meaningful change in the textile care industry.”
About America’s Best Cleaners:
America’s Best Cleaners is a certification agency and an industry-leading team of consultants who assist owners, managers, and team members to realize their full potential while striving for continued personal and professional success. For more information on America’s Best Cleaners and its Affiliates, visit the webpage.
DECEMBER 2024 NEWS
DLI School Offers 10 Complete Courses for 2025
Virtual Stain Removal Now Available in Spanish
Leadership & Customer Service Virtual Courses Added
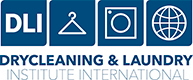
In 2025, the Drycleaning & Laundry Institute will split its virtual stain removal course into two parts, Basic Stain Removal Techniques and Advanced Stain Removal Techniques. Each course is four days long, running online Tuesdays and Thursdays over two-week periods in May, June, and July.
DLI also introduces a new Spanish language Four-Day Basic Stain Removal virtual course this November. DLI plans to expand this course into an in-person offering in the future. “Members asked for a Spanish version of our Stain Removal course,” said Brian Johnson, DLI’s Director of Education and Analysis. “We are pleased to work with Gina Hernandez, a DLI member in California to offer this course.”
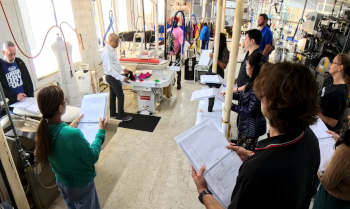
DLI members most frequently cited leadership and customer service as areas of concern on a recent survey. To meet this demand, DLI partnered with Jen Whitmarsh of Snappy Drycleaning and The Route Pros to offer two new virtual courses:
- Inspire & Influence: Leadership Virtual Course
- Service Superstars: Customer Service Representative Virtual Course
DLI continues offering its best-in-the-industry in-person courses at its training facility in Laurel, MD. DLI’s school equips managers and staff at all experience levels with the latest results-driven standards, empowering confident and efficient performance.
New Leadership & Customer Service Virtual Courses
DLI introduces two new two-day virtual courses to help managers and staff quickly develop crucial skills. Both courses will be instructed by Jennifer Whitmarsh with Snappy Dry Cleaning & The Route Pros.
Service Superstars: Customer Service Rep Course – July 29 & 31
Service Superstars is a high-energy virtual course designed to transform customer service professionals into exceptional brand ambassadors. This program focuses on building the skills and mindset needed to create unforgettable customer experiences, foster loyalty, and drive success. Participants will learn effective communication techniques, problem-solving strategies, and tools to handle challenging situations with confidence and grace. Seasoned professionals or industry newcomers will gain knowledge and techniques to exceed expectations, delight customers, and shine in every interaction.
Inspire & Influence: Leadership Course – September 9 & 11
Inspire & Influence is a virtual leadership course designed to empower individuals to become impactful leaders in today’s fast-paced world. This program focuses on mastering the art of inspiration, building trust, creating a dynamic culture, and fostering individual leadership to drive success in any team.
Through interactive sessions, real-world scenarios, and actionable strategies, participants will learn how to effectively communicate a company’s overall vision, motivate others, and create a lasting positive impact. Whitmarsh and DLI designed this course to equip emerging leaders and seasoned professionals with the tools to lead with confidence, authenticity, and purpose.
Mid-West Basic Stain Removal Techniques Hybrid Course
Building on the popularity of DLI’s 2023 and 2024 West Coast Stain Removal Courses, DLI offers a special hybrid edition of its Basic Stain Removal Techniques Course in 2025. The course covers three days of virtual learning and one day of on-site training at Sankosha’s Elk Grove facility in the Chicago area.
Hybrid Basic Stain Removal Techniques
Virtual: February 20, 25 & 27
On-Site: March 5
Virtual Stain Removal Simplification & Spanish Availability
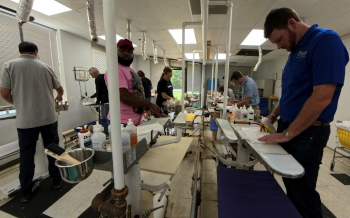
This year DLI expands its Virtual Stain Removal course into two sections: Basic Stain Removal Techniques and Advanced Stain Removal Techniques. With four-days of virtual learning each, these courses help students digest the information more efficiently and focus on fundamentals and more involved stain removal processes.
DLI will offer the Basic Stain Removal Techniques Virtual course twice in English and one session of its new Advanced Stain Removal Techniques Virtual Course in 2025. In addition, DLI presents Basic Stain Removal Techniques in Spanish in 2025. Gina Hernandez with Ortega Cleaners, a DLI Professional Member in San Juan Capistrano, CA will serve as instructor for this course.
Basic Stain Removal Techniques Virtual Course
May 6, 8, 13 & 15 (English)
July 8, 10, 15 & 17 (English)
November 11, 13, 18 & 20 (Spanish)
Advanced Stain Removal Techniques Virtual Course
June 10, 13, 17 & 19
On-Site Courses
DLI continues to offer its signature traditional in-person One-Week Introduction to Drycleaning and Two-Week Advanced Drycleaning courses twice in 2025. These courses are designed to teach students drycleaning principles and procedures that maximize quality and efficiency.
DLI’s On-Site Introduction to Drycleaning and On-Site Advanced Drycleaning courses run consecutively over a three-week period. Students who combine both courses receive a discounted rate.
On-Site One-Week Introduction to Drycleaning Course
DLI’s On-Site Introduction to Drycleaning Course is suited for experienced individuals or those who are new to the industry. It will run Monday through Friday from 9 a.m. to 4:30 p.m. at DLI’s School of Drycleaning Technology in Laurel, MD.
Some of the topics the one-week course explores include:
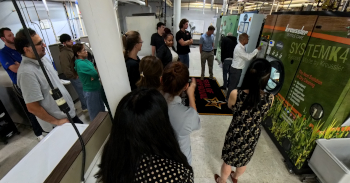
- sorting loads for drycleaning
- drycleaning science
- fibers and their characteristics
- fabric construction
- cleaning silk, satin and other fabrics
- soil and cleaning theory
- operating a drycleaning machine
- stain removal chemistry and procedures including removing ink, coffee, grease and other stains from clothing
- pressing pants, coats and skirts
- using tensioning equipment to improve finishing quality
- and more.
Tuition for DLI’s One-Week On-Site Introduction to Drycleaning Course is $2,165 for non-members. DLI members receive discounts ranging from 60% off to absolutely free depending on membership level.
On-Site Two-Week Advanced Drycleaning Course
DLI’s On-Site Advanced Drycleaning Course runs immediately after the On-Site Introduction to Drycleaning course.
The ten-day course is suited for those who have finished the introductory course or who have hands-on production experience and knowledge of basic stain removal and finishing techniques.
Course topics include:
- designing a cleaning plant with the most effective work flow
- pressing laundered shirts
- understanding the differences between solvents including perc, GreenEarth and hydrocarbon
- getting clean, white laundry
- cleaning and preserving wedding gowns
- current regulations facing the industry
- customer service techniques for cleaners
- using bleaches without damaging fabric color
- and more.
Tuition for DLI’s On-Site Advanced Drycleaning Course is $2,665 for non-members. DLI members receive discounts ranging from 67% off to absolutely free depending on membership level.
Spring 2025
387th One-Week Introduction to Drycleaning Course
March 24 – 28
387th Two-Week Advanced Drycleaning Course
March 31 – April 11
Fall 2024
388th On-Site Introduction to Drycleaning Course
October 6 – 10
388th On-Site Advanced Drycleaning Course
October 13 – 24
On-Site Complete Drycleaning Course
Students taking DLI’s On-Site Introduction to Drycleaning and On-Site Advanced Drycleaning Courses together enjoy a reduced tuition rate of $2,965 per student for non-members. DLI members receive discounts ranging from 20% off to free depending on membership level.
Complete Course information is available at DLIonline.org/Education
For more information or to register for any of DLI’s courses, contact DLI at (800) 638-2627 or visit www.DLIonline.org.
Thinking of attending? The Tom Kimmel Canadian Scholarship applies to any DLI class. Check the details on our Scholarship Page.
EPA bans Perc, TCE in final ruling
WASHINGTON – Today, Dec. 9, the U.S. Environmental Protection Agency (EPA) finalized the latest risk management rules for trichloroethylene (TCE) and perchloroethylene (PCE) under the bipartisan 2016 Toxic Substances Control Act (TSCA) amendments, marking another major milestone for chemical safety after decades of inadequate protections and serious delays. These protections align with President Biden’s Cancer Moonshot, a whole-of-government approach to end cancer as we know it.
TCE is an extremely toxic chemical known to cause liver cancer, kidney cancer, and non-Hodgkin’s lymphoma. TCE also causes damage to the central nervous system, liver, kidneys, immune system, reproductive organs, and fetal heart defects. These risks are present even at very small concentrations. Under today’s rule, all uses of TCE will be banned over time (with the vast majority of identified risks eliminated within one year), and safer alternatives are readily available for the majority of uses.
PCE is known to cause liver, kidney, brain and testicular cancer, as well as damage to the kidney, liver and immune system, neurotoxicity, and reproductive toxicity. Today’s final rule will better protect people from these risks by banning manufacture, processing and distribution in commerce of PCE for all consumer uses and many commercial uses, while allowing some workplace uses to continue only where robust workplace controls can be implemented.
“It’s simply unacceptable to continue to allow cancer-causing chemicals to be used for things like glue, dry cleaning or stain removers when safer alternatives exist,” said Assistant Administrator for the Office of Chemical Safety and Pollution Prevention Michal Freedhoff. “These rules are grounded in the best-available science that demonstrates the harmful impacts of PCE and TCE. EPA continues to deliver on actions that protect people, including workers and children, under the nation’s premier bipartisan chemical safety law.”
PCE and TCE are both nonflammable chlorinated solvents that are volatile organic compounds. PCE can biodegrade into TCE, and PCE may contain trace amounts of TCE as an impurity or a contaminant. The chemicals can often serve as alternatives for each other. For several uses of TCE that will be totally prohibited, there is an analogous use of PCE that can continue safely in perpetuity under workplace controls. Some examples of uses that will be prohibited under the TCE rule, but will continue under the PCE rule include: industrial and commercial use as an energized electrical cleaner, in laboratory use for asphalt testing and recovery, use to make refrigerants and other chemicals, and for vapor degreasing.
“Over 40 years ago, a mother named Anne Anderson from Woburn, Massachusetts, approached me and started a crusade to keep any more children like Jimmy Anderson, her son, from dying from cancer caused by toxic chemicals. Anne’s work directly led to this announcement from the Environmental Protection Agency that I am overjoyed to celebrate today alongside her and every community that stands to benefit—a finalized ban on trichloroethylene and most uses of perchloroethylene, two chemicals that cause cancer, affect reproductive systems, are neurotoxic, and compromise immune systems,” said Senator Ed Markey (D-MA). “Despite their dangers, these chemicals could still be found in industries like dry cleaning, automotive repair and manufacturing. With no doubt that these chemicals are deadly, there is no doubt that this final rule will save lives—especially our children’s lives—around the country.”
“The Camp Lejeune contaminated drinking water issue has dragged on over the better part of forty years ever since TCE, PCE and other organic solvents were first documented in the base’s drinking water supply in October 1980,” said Jerry M. Ensminger, Retired U.S. Marine Corps Master Sergeant. “My daughter, Janey, was conceived aboard Camp Lejeune during the drinking water contamination and died of leukemia in 1985, at the age of nine. I first began my fight for justice in 1997, and was later joined by Mike Partain in 2007, who was also conceived aboard the base and diagnosed with male breast cancer at the age of 39. Mike and I welcome this ban on TCE by the EPA and this is proof that our fight for justice at Camp Lejeune was not in vain.”
Trichloroethylene
TCE is used as a solvent in consumer and commercial products such as cleaning and furniture care products, degreasers, brake cleaners, sealants, lubricants, adhesives, paints and coatings, arts and crafts spray coatings, and is also used in the manufacture of some refrigerants. Safer alternatives are readily available for the majority of these uses.
EPA is finalizing its prohibition on all uses of TCE, most of which will be prohibited within one year, including TCE manufacture and processing for most commercial and all consumer products. This will protect most people who are likely to be exposed to TCE from uses covered by TSCA, including all consumers and workers in many sectors and many communities.
A limited number of uses in the workplace will be phased out over a longer period. Those uses will only continue with required stringent worker protections in place. All TCE uses with longer phaseout timeframes will have worker safety requirements, such as a Workplace Chemical Protection Plan that includes an inhalation exposure limit. The final rule sets a different inhalation exposure limit for airborne TCE than was proposed. This change was made in response to public comments to ensure the limit is feasible to implement and monitor while still reducing risk. EPA estimates that the new inhalation exposure limit would reduce long-term workplace exposure by 97%.
Many of the TCE uses that are continuing for longer than one year occur in highly industrialized settings that can adopt EPA’s new stringent worker protections, such as uses of TCE to clean parts used in aircraft and medical devices, to manufacture battery separators, to manufacture refrigerants, as well as in other transportation, security and defense systems.
For the use of TCE in manufacturing refrigerants, the longer timeframe supports fighting climate change by complementing efforts to phase down climate-damaging hydrofluorocarbons under the bipartisan American Innovation and Manufacturing Act.
All of these uses ultimately will be prohibited, but some of the exemptions associated with longer timeframes are necessary to avoid impacts to national security or critical infrastructure. In addition, some of the timeframes have been adjusted from the proposed rule based on public comment to allow reasonable time for transitioning to alternatives.
Further, to support cleanup activities at sites of past TCE contamination (e.g., Superfund sites), EPA is allowing essential laboratory use and proper disposal of TCE wastewater to continue for 50 years provided worker protections are in place, including the inhalation exposure limit set by today’s rule.
Learn more about the TCE rule.
Perchloroethylene
PCE is a solvent that is widely used for consumer uses such as brake cleaners and adhesives, in commercial applications such as dry cleaning, and in many industrial settings. Safer alternatives are readily available for the majority of these uses.
EPA is finalizing a 10-year phaseout for the use of PCE in dry cleaning to eliminate the risk to people who work or spend considerable time at dry cleaning facilities. Use of PCE in newly acquired dry-cleaning machines will be prohibited after six months. Compliance dates for machines that are already owned will vary depending on the type of the dry-cleaning machine used, with older types of machines being phased out sooner than newer ones. Many dry cleaners have already begun this transition. This timeline is unchanged from the proposed rule.
EPA’s final risk management rule requires companies to rapidly phase down manufacturing, processing and distribution of PCE for all consumer use and many uses at industrial and commercial workplaces, most of which will be fully phased out in less than three years. For most of the uses of PCE that EPA is prohibiting, EPA’s analysis found that alternative products with similar costs and efficacy to PCE are reasonably available.
The rule also finalizes stringent, achievable controls for continuing uses under a Workplace Chemical Protection Program. These rules generally occur in highly sophisticated workplaces that may be important to national security, aviation and other critical infrastructure, as well as uses that complement the agency’s efforts to combat the climate crisis. These uses include:
- Use in the production of other chemicals, including refrigerant chemicals that may complement efforts to phase down climate-damaging hydrofluorocarbons under the bipartisan American Innovation and Manufacturing Act.
- Use in petrochemical manufacturing.
- Use in agricultural chemical manufacturing (originally proposed to be prohibited).
- Use for cold cleaning of tanker vessels (originally proposed to be prohibited).
- Use as maskant for chemical milling.
- Use as a vapor degreasing solvent.
- Use in adhesives and sealants.
- Use in energized electrical cleaning (originally proposed to be prohibited).
- Processing into formulation, mixture or reaction products.
- Import, recycling, disposal, processing by repackaging and domestic manufacturing of PCE.
In response to public comments on the proposed rule, most workplaces now have 30 months instead of 12 months to fully implement the Workplace Chemical Protection Program. EPA also revised several other aspects from the proposal to strengthen and clarify aspects of the Workplace Chemical Protection Program, including monitoring requirements. EPA also ensured the employees’ designated representatives, such as labor union representatives, have access to occupational exposure monitoring and records.
Learn more about the PCE rule.
Additional Information
As a follow-up to consultations with small businesses, EPA plans to release compliance guidance for the use of PCE in dry cleaning and energized electrical cleaning in the coming months, as well as for the TCE rule. President Biden’s Fiscal Year 2025 budget requested funding to support small business efforts to transition to TSCA-compliant practices and mitigate economic impacts. If implemented, these grants could be used to support small businesses like dry cleaners in their transition away from PCE.
EPA will host a public webinar to explain what is in the PCE final rule and how it will be implemented on Wednesday, Jan. 15, 2025, at 12:30 p.m. EST. Registration is available on the Final Regulation of Perchloroethylene under TSCA webinar page.
ABS Laundry Business Solutions Announces Leadership Transition
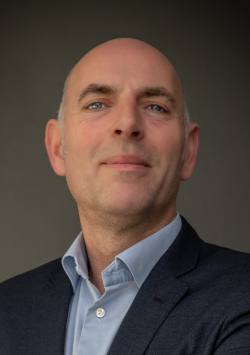
ABS Laundry Business Solutions, a part of Vitec Software Group, has announced a change in its leadership. Gerard van de Donk, the current Chief Executive Officer, will step down from his role effective January 1, 2025. Marien van Bezooijen has been appointed as the new CEO.
Gerard van de Donk, who became part of ABS in 1991, has played a pivotal role in guiding the company’s growth and accomplishing significant milestones over the years.
“It has been an honor to work with such a dedicated team and to see the company evolve. I am incredibly proud of what we’ve accomplished,” says van de Donk. “This transition is part of a thoughtful and deliberate succession plan. I am confident that Marien van Bezooijen, with his extensive experience and vision, will guide ABS to continued success.”
Van Bezooijen, who serves as the Chief Commercial Officer at ABS, brings a wealth of expertise and a strong background developed through years of dedication within the industry and organization. He has been recognized for his alignment with the company’s values and long-term goals. Van Bezooijen is committed to advancing the work of delivering high standards of service and innovation that ABS is known for.
“We have a talented Management Team and dedicated employees, and I am thrilled to lead ABS as we work closely together to achieve our objectives.” says van Bezooijen. “Together, we will continue to innovate, embrace change to remain competitive and uphold the high level of quality that our customers expect. I look forward to building on the strong foundation laid by Gerard and driving the company towards new heights.”
Gerard van de Donk will remain with the company as a Senior Advisor to ensure a smooth transition. He expresses his commitment to supporting the company’s mission and future endeavors.
“I look forward to watching ABS grow under Marien’s leadership,” he concludes.
About ABS
ABS Laundry Business Solutions, founded in 1987, specializes in providing innovative software solutions for the textile care and laundry industry. With over 750 installations worldwide and a dedicated team of 175 employees strategically located to provide local support, ABS delivers advanced technology, including its ABSSolute ERP software, to streamline laundry operations, boost efficiency, and enhance service quality. Serving a global client base, ABS offers tailored solutions for businesses of all sizes, from owner operated laundries to multinational organizations. As part of the Vitec Software Group, ABS benefits from the resources and expertise of the larger organization, ensuring continued industry leadership and innovation. For more information, visit www.abslbs.com.
NOVEMBER 2024 NEWS
Kreussler Teams Up with Integrity Mechanical to Elevate Support for Canadian Customers
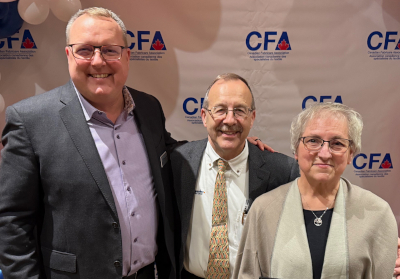
Kreussler is partnering with Integrity Mechanical to oversee and manage its operations throughout Canada. The move will bring a more local, Canadian-focused activity, presence and service. Integrity will take over as the nationwide Canadian primary distributor for Kreussler products, working with existing distribution partners in all the provinces for technical support, sales and promotion. This change will not affect how current clients source and purchase Kreussler products at the local level, but will allow for hiring sales and support staff, thereby improving customer service.
The partnership will immediately add a local technical sales representative to the Ontario market by hiring J.P. Renauld, a highly respected figure in the industry with decades of experience from owning and running his family’s dry cleaning business in Kitchener.
Kreussler Inc. is the North American daughter company of Chemische Fabrik Chreussler & Co. GmbH, a 4th generation family-owned manufacturer of high-end detergents, stain remover cleaning boosters and ancillary agents used in the professional textile care, commercial and industrial washing industries.
Integrity Mechanical is a family-owned full-service equipment and supply company offering premium brands like Union, Sankosha, Leonard, Rema, Unipress and White Conveyor, to name a few. Founded in 2003 by Kevin and Paula Marois on the principle of integrity, the company has built a reputation of trust, competency and reliability throughout western Canada.
DLI School Graduates Complete 386th Hands-On Dry Cleaning Courses
Fifteen students graduated the Drycleaning & Laundry Institute’s School of Drycleaning Technology’s Introduction to Drycleaning Course, October 7–11 and 17 graduated its Advanced Drycleaning Course, October 14–25. DLI’s Introduction course lasts five days and the Advanced Course runs for 10 days. Founded in 1927, DLI’s School of Drycleaning Technology has helped shape the careers of thousands of drycleaners worldwide.
In these courses, students learned about:
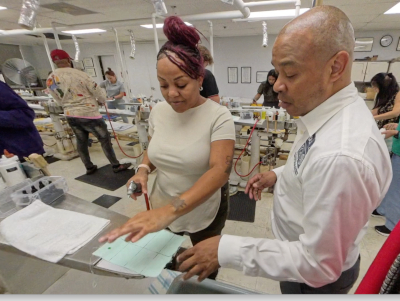
Latisha Robinson.PNG: Latisha Robinson with Dependable Cleaners in Denver, CO, works on her stain removal skills with help from Brian Johnson, DLI Education Director. One-on-one hands-on instruction helps students retain important new lessons at DLI’s School of Drycleaning Technology.
- Sorting loads for drycleaning
- The science of drycleaning
- Fibers and their characteristics
- Fabric construction
- Cleaning silk, stain, and other fabrics
- Soil and cleaning theory
- Operating a drycleaning machine
- Stain removal chemistry and procedures
- Removing coffee, ink, grease, and other stains from clothing
- Pressing pants, coats, blouses, ties, pleated garments, and skirts
- Using tensioning equipment to improve finishing quality
- Using bleaches without damaging fabric color
- Distillation procedures
- Understanding the differences between solvent types
- Wetcleaning wool, silk, and more
- Designing a drycleaning plant with the most effective workflow
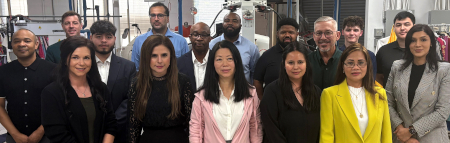
INTRODUCTORY COURSE
Front Row (left to right): Jhana Richardson, Crown Cleaners, West Des Moines, IA; Sofia Garcia, Keller Cleaners, Monterrey, Mexico; Hui “Becky” Cao, Wesselmann Cleaners, Buffalo, NY; Yesenia Ruiz, Floras & Johnson Cleaners, Douglas, AZ; Doris Mangrobang, Halekulani Hotel, Honolulu, HI. Middle Row (l-r): Brian Johnson, DLI Director of Education & Analysis; Jacobo Brenes Cerrato, Nettoyeur Victoria Village, Westmount, Quebec, Canada; Carlos Rosemond, Huntington Cleaners, Huntington Woods, MI; Michael Lausen, Lapels of Houma, Houma, LA; Adriana Lopez, 3rd Generation Cleaners, Chico, CA. Back Row (l-r): Matt Nemec, St. Croix Cleaners, Stillwater, MN; Hiten Nihalani, Rockville, MD; Geovanni Dountsop Tchinda, Reliable Transporters, LLC, Silver Spring, MD; Washington Youson, 7 to 7 Cleaners, Harper Woods, MI; Victor Targett, Targetts, Inc., Keene, NH; Dylan Chin, Helena’s Cleaners, Normandy Park, WA. Jacobo Brenes Cerrato, Hui “Becky” Cao, Michael Lausen, Adriana Lopez, Juana Richardson, and Victor Targett attended the course free of charge as DLI Premier Members. Dylan Chin attended the course on a scholarship from Kreussler.
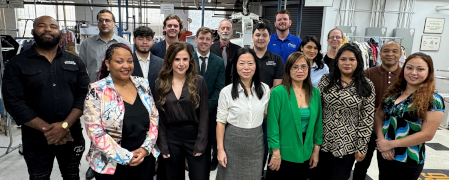
ADVANCED CLASS
Front Row (left to right): Latisha Robinson, Dependable Cleaners, Denver, CO; Sofia Garcia, Keller Cleaners, Col del Valle, Monterrey, Mexico; Hui “Becky” Cao, Wesselmann Cleaners, Buffalo, NY; Doris Mangrobang, Halekulani Hotel, Honolulu, HI; Angeles Amayrany Castillo, Telluride Eco Cleaners, Telluride, CO; Chelsie Zamora, Lavaseco Universal, Ltd., San Antonio, TX. Middle Row (l-r): Geovanni Dountsop Tchinda, Reliable Transporters, LLC, Silver Spring, MD; Jacobo Brenes Cerrato, Nettoyeur Victoria Village, Westmount, Quebec, Canada; Matt Nemec, St. Croix Cleaners, Stillwater, MN; Dylan Chin, Helena’s Cleaners, Normandy Park, WA; Adriana Lopez, 3rd Generation Cleaners, Chico, CA; Brian Johnson, DLI Director of Education & Analysis. Back Row (l-r): Hiten Nihalani, Rockville, MD; Isaac Hamilton, Broadway Dry Cleaners, Perth, Western Australia; Beau Williams, Puritan Cleaners, Richmond, VA; Mark Harris, Oceanside Cleaners, Ponte Vedra Beach, FL; Donna Wagner, Glyndon Lord Baltimore Cleaners, Glyndon, MD. Not Pictured: Victor Targett, Targetts, Inc., Keene, NH. Victor Targett, Jacobo Brenes Cerrato, Hui “Becky” Cao, Adriana Lopez, and Beau Williams attended the course free of charge as DLI Premier Members. Donna Wagner and Dylan Chin attended the course with a scholarship from Kreisler.
Latisha Robinson, Plant Manager with Dependable Cleaners in Denver CO, attended the Advanced Drycleaning Course. She said, “My boss attended [DLI’s School] earlier this year. When she came back she told me this information would help me help my girls and help us serve our customers.” She said DLI’s courses helped her learn best practices and more efficient ways to help customers. “I was kind of thrown in, like one of the managers said this is how you do this, this how you do that and the rest, you just wing it or figure it out from experience.” DLI’s structured courses mix classroom learning with hands-on learning experience to help cement best practice procedures.
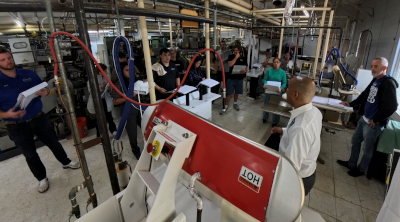
Finishing Demo.JPG & Finishing DemoB.JPG: Brian Johnson, DLI Director of Education (left), demonstrated advanced finishing techniques during DLI’s 386th Advanced Drycleaning Course in October.
Matt Nemec with St. Croix Cleaners in Stillwater, MN, took both courses to better understand the drycleaning business and position himself to someday take charge of his family cleaning business. “Stain removal is very exciting. We’re learning so much here, it’s unreal,” Nemec said. “I got some great ideas to take back. Brian Johnson’s got a bunch of great ideas and insights on business. He’s helping out so many people, it’s awesome. I would say my favorite part of the courses is honestly, just stain removal, seeing the stains disappear. It’s a really good process and he does a great job with that.”
Adriana Lopez with 3rd Generation Cleaners in Chico, CA, attended both the October Introduction to Drycleaning and Advanced Drycleaning Courses. “The courses are great because they are interactive, you know, hands on and everything.” Lopez said she was excited to apply the new skills she learned. “I heard the courses were great and having the ability to enhance my knowledge is so wonderful,” she said.
See the list of upcoming DLI educational opportunities on our Conferences & Events page.
Learn about the Tom Kimmel Scholarship program for Canadians wanting to attend the DLI training courses on our Scholarships page!
Texcare International 2024: when visions of the future become reality
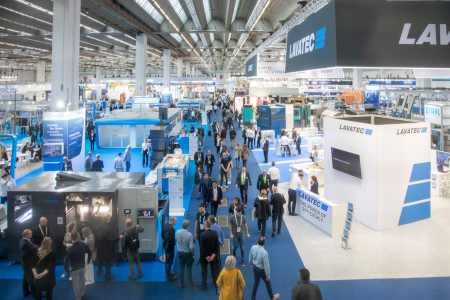
Texcare International celebrated its comeback November 6-9 with an exceptionally high level of international participation and top marks from the participants. 305 companies from 32 countries presented their innovations in automation and energy efficiency. About 15,500 visitors from 122 countries came to Frankfurt.
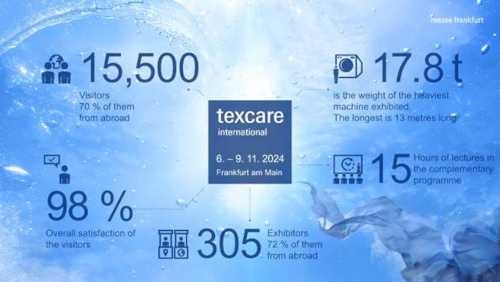
Over the past four days, the leading international trade fair for textile care presented innovations for laundries, dry cleaners and textile service companies with great success: 98 per cent of trade visitors were satisfied to extremely satisfied with how they achieved their goals for the trade fair; 52 per cent expect an improved industry economy.
After eight years without Texcare due to the pandemic, the desire among exhibitors to exchange ideas and present innovations was palpable. The international character of the event was reflected in the wide range of countries represented – around 15,500 visitors from 122 countries, including Germany, took advantage of Texcare, which ran from Wednesday to Saturday, to exchange ideas and information on topics relevant to the industry.
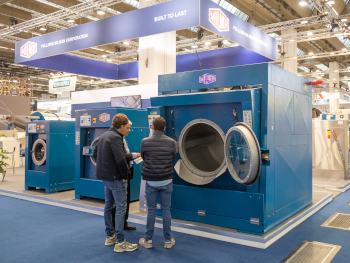
Wolfgang Marzin, President and Chief Executive Officer (CEO) of Messe Frankfurt: “After the long break, we are delighted with this successful comeback of Texcare. The leading international trade fair demonstrated the great strides in innovation that the industry has made in recent years. I was really thrilled to see so many exhibitors, especially new exhibitors and start-ups, as well as visitors from all over the world at Texcare. Above all, it was great to see so many young professionals at the stands and in the aisles.”
Industry celebrates its future potential
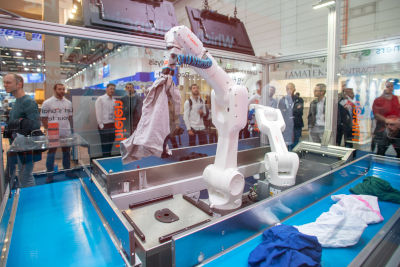
The industry is meeting the challenges of labour shortage and rising energy prices with a significant surge in innovation. The solutions are available, as demonstrated by the exhibitors with their machines, technologies and expertise. The leap towards robotization was clearly visible at the stands. The circular economy was also in focus: many innovations showed how machine builders and textile manufacturers are working together to advance sustainability. Texcare provided the right impulse for companies in the textile care industry at the right time, enabling them to secure their successful market position by investing.
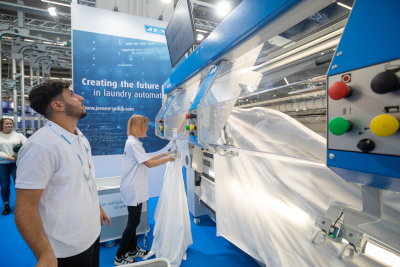
The partner industry associations of Texcare also draw a positive conclusion. Elgar Straub, CEO of VDMA Textile Care, Fabric and Leather Technologies, emphasizes: “Expectations for Texcare International were very high after eight years without a trade fair, but they were even exceeded. I have rarely experienced such a good atmosphere at trade fairs in recent years. Furthermore, Texcare International was extremely well prepared by Messe Frankfurt, but the exhibitors also presented themselves to their global customers with exceptionally beautiful and informative stands. As expected, the topics that are driving the industry were hygiene, automation, digitalization, logistics and AI. But my highlight of this fair was the truly excellent mood among visitors and exhibitors and the positive outlook for the future of textile care. Texcare International this year was simply a pleasure.”
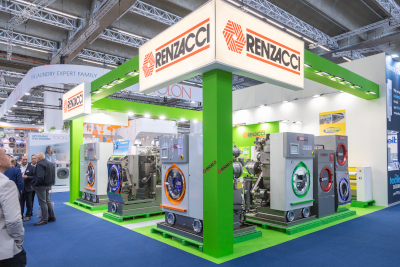
Andreas Schumacher, General Manager of the German Textile Care Association, summarizes: “There was a sense of a fresh start. You could feel that after eight long years, the exhibitors were eager to show their products and developments, and the visitors were excited about innovations.
“In particular, the topics of automation and digital solutions, as well as robotics, were the subject of much discussion, as many companies are facing a shortage of skilled workers. After the pandemic and the energy crisis, the discussions were once again characterized by a willingness to invest and a sense of optimism. Energy costs and corresponding opportunities for saving energy and other resources were also a key topic. Last but not least, companies in the industry are working to further improve their circular business models and to adapt to the upcoming regulations for the recycling of textiles.”
Comprehensive lecture program and guided tours
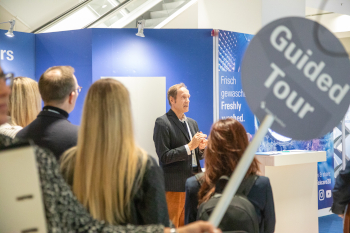
The supporting program at Texcare addressed key topics at the Texcare Forum and the guided tours. The panels, for example, focused on sustainability through innovation, business models in the circular economy and automation in small businesses. Experts from the USA, Scandinavia, France and China provided insights into the textile care markets in their respective countries. The daily guided tours, curated and conducted by industry experts, were very well received. For the first time, Texcare International offered young professionals from six vocational schools in Berlin, Hanover, Frankfurt, Cologne and Zurich the opportunity to visit stands and network with companies as part of the Young Competence Program.
Texcare 2024 in figures
98 per cent of visitors were satisfied to extremely satisfied with what Texcare had to offer, and 97 per cent said they had achieved their goals for the trade fair. Visitors from a total of 122 countries came to the leading trade fair. The top ten visitor countries were: Germany, Italy, the Netherlands, France, Spain, Great Britain, Poland, Belgium, Greece and Switzerland. The most important visitor countries from outside Europe were the USA, China and Australia. The degree of internationality was around 70 per cent for visitors and 72 per cent for exhibitors.
The main areas of interest for visitors were machinery, equipment and components for washing, cleaning, drying and finishing textiles, as well as for energy generation, energy saving, recycling, environmental and water technology. Texcare took place this year over four days, with a new sequence of days from Wednesday to Saturday.
Exhibiting companies at Texcare 2024 and their products can be viewed 365 days a year in the Texcare Contactor: www.texcare.com/contactor.
The next Texcare International in Frankfurt am Main will take place in 2028.
Canada Stand Out at CINET Best Practices Awards
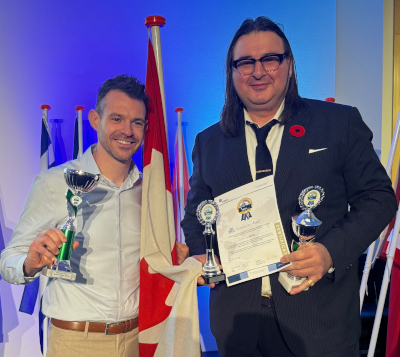
The CINET conference, featuring the 2024 Best Practices competition, immediately followed the TexCare show in Frankfurt, Germany Nov. 9-11. The competition gives cleaners from around the world the opportunity to strut their stuff and show how they are building Best Practices into their daily procedures and mindset.
We will feature a full report on the awards as soon as details are received from CINET. In the mean time, we didn’t want to wait to report exciting results for Canadian companies.
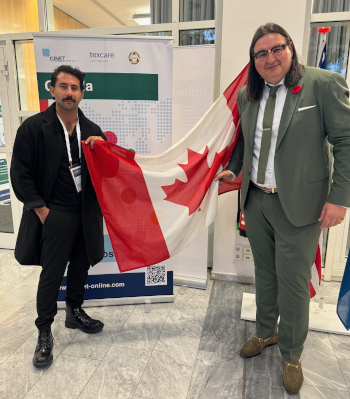
“The Canadian Fabricare Association was well represented, with many Canadian participants,” said CFA President Dino Kantzavelos. “At the CINET Global Best Practice Awards, along with me, there was Dave Crouse of Crouse’s Cleaners, and Michael Gosio of Parklane Cleaners.
“Dave Crouse and Crouse’s Cleaners received the award in the Global Corporate Social Responsibility category.
“TSC Wetclean was the winner for best cleaner in the Country Category, as well as the Global Award for Sustainability. Truly a proud moment for the Canadian industry,” he reported.
Well done, all!
TRSA 31st Annual Maintenance Management Institute
The Textile Rental Services Association (TRSA) hosted its 31st Annual Maintenance Management Institute (MMI) from Oct. 15-17 in Newark, NJ. The event brought together industry professionals for three days of insightful sessions and valuable networking opportunities.
The event commenced with a keynote address by Tommy Cocanougher, a seasoned engineering veteran from Cintas Corp., Mason, OH. His presentation, titled “Developing You and Your Team for Growth,” emphasized the importance of personal and professional development within maintenance and reliability teams. Cocanougher highlighted the need for self-growth, skill-building and the adoption of new technologies to foster a culture of reliability and career advancement.
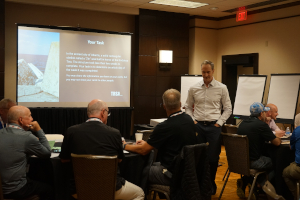
Following the keynote, attendees engaged in “The Maintenance Mindset: Conquering the Complex,” led by Christopher Stammer from Voluminant. This immersive session challenged participants with a complex problem-solving exercise designed to enhance critical thinking, communication and teamwork skills. The engaging simulation encouraged technical professionals to think strategically and adaptively-essential traits for thriving in production-driven environments.
Brian Varner, owner of Safety Solutions for Healthcare, conducted a session titled “Essentials: Safety Communications for Maintenance Engineers.” This session provided crucial insights into recognizing and communicating chemical hazards. Through real-world scenarios and case studies, attendees learned to interpret safety data sheets, understand labeling requirements, and implement effective communication strategies to ensure OSHA compliance and promote a safety-first culture.
Todd Leeth, strategic growth leader at Spindle, and industry consultant Keith Ware explored critical strategies for driving operational success in commercial laundry operations. Their session focused on overcoming complacency, fostering a proactive-maintenance culture, and leading teams in preventive maintenance, troubleshooting, and machine repair to optimize performance and reduce downtime.
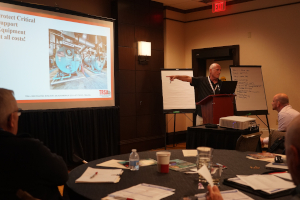
Ian Bigelow, co-founder of Simple Laundry Solutions, led a session titled “What is Old is New Again: Keeping Machinery Up after 30 Years of Hard Use.” Bigelow shared valuable lessons on maintaining aging machinery and identifying signs of wear and inefficiency. He also discussed strategies for justifying new equipment purchases to company leadership, balancing cost considerations with the benefits of improved productivity and safety.
Varner returned to discuss key safety practices for plant engineers. Through hands-on activities and discussions, participants learned to identify hazards, practice proper entry procedures, and use safety equipment effectively to ensure OSHA compliance and workplace safety.
The second day featured plant tours to American Wear Inc. and Unitex Healthcare Laundry. Following lunch, attendees met in work groups to develop presentations that each group shared on the final day of the institute.
Christopher Stammer summarized the value of MMI, stating, “MMI isn’t structured as a bunch of speakers disseminating information. Participants receive a framework for boosting plant uptime, throughput and safety on the first day of the event. The remaining day and a half are spent on making and processing observations focused on helping operations improve. We had participants from 17 different companies and two dozen sets of eyes who made some amazing observations for plant improvement that would typically get lost in the rush of the day. They hit it out of the ballpark. There was a huge amount of value gained from the collaboration of the entire group and the insight from both the speakers and the industry veterans who attended.”
The 32nd Annual MMI is slated for Oct. 22-24, 2025, in Philadelphia. For more details, visit TRSA’s website.
TRSA’s third regional summit of 2024
The Textile Rental Services Association (TRSA) successfully concluded its final Regional Production Summit program of 2024 with the Northeast Production Summit and Plant Tours held in Newark, NJ, on Oct. 15-16. The summits featured a uniform design aimed at making a quality program more accessible to all members by bringing it to a central location in their region.
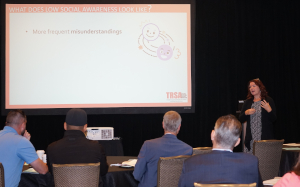
The Northeast Summit kicked off with a keynote session from Nancy Roberts, CEO and founder of The DISC Wizard. Roberts provided an insightful overview of emotional intelligence (EQ), detailing the five traits of emotionally intelligent individuals and how attendees could leverage this knowledge to become more effective leaders. Attendees had the option to complete an EQ evaluation beforehand, allowing Roberts to tailor her presentation to the audience’s specific scores.
Other speakers in order of appearance included:
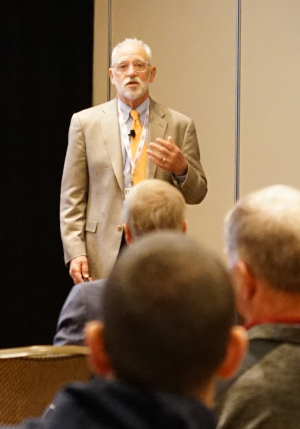
- Roberts, Todd Leeth, strategic growth leader at Spindle, delivered a presentation focused on the role of production managers in preventive maintenance. Leeth shared strategies for saving labor and energy costs by scheduling preventive maintenance during normal working hours and provided real-world examples of the consequences of neglecting preventive maintenance. He emphasized the importance of regular meetings between production and maintenance staff to ensure smooth and safe operations.
- Industry consultant Don Bock then presented “Fire Safety – Strategies for Prevention,” offering a comprehensive report on common fire sources in laundries and the best prevention strategies. Bock also detailed various fire-suppression systems used in the industry.
- Christopher Stammer, CEO of Voluminant, followed with a session on leadership skills, challenging attendees to consider whether they act as captains or crew in their roles. Drawing on his experience as a United States Coast Guard licensed Master Captain, Stammer used real-world examples to highlight the importance of informed decision-making. He led an exercise where participants ranked survival items in order of importance, illustrating the value of collaboration and avoiding group-think in leadership. Stammer concluded with tips on aligning team members’ individual desires with organizational incentives to maximize performance.
- Keith Ware, an industry consultant, presented on process improvement and root-cause analysis. Ware explained the basics of root-cause analysis and stressed the importance of creative problem-solving and team collaboration. He engaged the audience in a hands-on activity to build the highest structure using marshmallows, dry spaghetti, and pipe cleaners. This exercise underscored the principles of teamwork and innovation. Attendees then participated in facilitated roundtables to discuss common issues and strategies for improvement. They addressed topics such as EQ, leadership development, and safety.
The first day concluded with a standards and regulations update from TRSA’s vice president of government relations, Kevin Schwalb. Schwalb provided a concise overview of current laws and regulations affecting the industry and discussed new developments and predictions as the country approaches a new presidential term.
On the second day, American Wear Inc. and Unitex Healthcare Laundry Services opened their doors for plant tours, providing attendees with opportunities to see industry best practices in action.
For more information about TRSA and upcoming events, visit TRSA’s website.
OCTOBER 2024 NEWS
Association of Wedding Gown Specialists hosts 2-Day training session
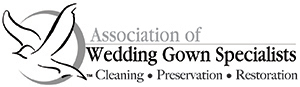
The Association of Wedding Gown Specialists (AWGS) recently hosted a two-day intensive training session at Janet Davis Cleaners in Berkley, MI. The event brought together a diverse group of experienced and new members from across the United States, Brazil, Canada, and the Philippines. Led by AWGS National Training Director, Dave Matthews, and ably assisted by Janet Matthews and AWGS President Kyle Matthews, the training session provided attendees a comprehensive, hands-on experience, delving into every aspect of wedding gown care, from meticulous cleaning techniques to the fine art of preservation.
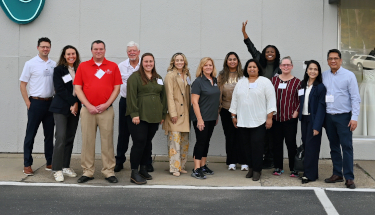
Left to right: Kyle Matthews, AWGS president, Jeanne Meden, Charleston Prestige Cleaners, Charleston, SC, Joe Harmon, Shores Fine Dry Cleaners, High Point, NC, Dave Matthews, AWGS National Training Director, Miranda Hildebrandt, Jan’s Professional Dry Cleaners, Flint, MI, Cinara Monteiro, Lavanderia CLASSEA, Belo Horizonte, Brazil, Janet Matthews, Janet Davis Cleaners, Berkley, MI, Madina Hashimi, Style and Grace Cleaners, Toronto, Canada, Nadine Rana, Style and Grace Cleaners, Toronto, Canada, Crystel Hilton, Style and Grace Cleaners, Toronto, Canada, Ashley Pursails, Jan’s Professional Dry Cleaners, Flint, MI, Zaida and Dominador Asis, Absolute Laundry and Dry Cleaners, Manila, The Philippines.
The regularly scheduled training sessions serve as a testament to the Association’s unwavering commitment to quality and its dedication to ensuring that members are equipped with the knowledge, tools, and techniques needed to meet the highest standards in the wedding gown care industry. The session not only focused on practical applications but also emphasized the collaborative spirit of the organization, which has grown into a supportive global community, united by a shared passion for wedding gown care.
The first day of the training session began with a warm welcome from Dave Matthews, who set the tone for the session by highlighting the importance of maintaining museum-quality standards in wedding gown care. His opening remarks resonated with both veteran members and newcomers, underlining the importance of attention to detail and professionalism in preserving cherished memories for brides worldwide.
Attendees through a series of practical workshops covered every aspect of wedding gown cleaning, addressing the various types of fabrics and embellishments commonly fcound on gowns. From gowns with delicate lace and intricate beading to sleek satin dresses, members were given the opportunity to work directly with a wide range of gown styles. This practical experience is vital to developing the skills necessary to care for each unique gown with the precision and sensitivity it demands.
Key topics covered included:
- Pre-Cleaning Inspection: Attendees learned how to conduct a thorough examination of gowns before cleaning, identifying potential problem areas such as stains, fragile fabrics, and loose beading.
- Cleaning Techniques: The session delved into different cleaning methods tailored to specific fabrics, including how to effectively remove stains without compromising the integrity of the gown.
- Use of Specialized Equipment: Demonstrations of cutting-edge cleaning equipment used to ensure that gowns are returned to brides in pristine condition were provided. This included discussions about eco-friendly options that are becoming increasingly popular in the industry.
The day concluded with a discussion on the importance of consistency and attention to detail, as even the smallest oversight could result in damage to a gown. By adhering to AWGS’s strict guidelines, members ensure that they meet the same high standards that brides expect when entrusting their most precious garment to a specialist.
The second day of the training shifted focus from cleaning to wedding gown preservation and restoration, another critical aspect of the services provided by AWGS members. Dave Matthews opened the day’s session by emphasizing the significance of properly preserving a gown, not only to protect it from aging and yellowing but also to allow brides to cherish and pass down their gowns to future generations.
Attendees were walked through the meticulous steps involved in preservation, from layering the gown with acid-free tissue paper to folding it carefully into an archival-quality wedding gown chest. One of the most important elements emphasized was the inspection process, which allows brides to personally approve the condition of their gown before it is preserved. This personal touch is a hallmark of AWGS members, reinforcing trust and transparency.
Key preservation techniques include:
- Acid-Free Materials: Members learned the importance of using acid-free tissue and archival-quality chests to ensure the long-term preservation of gowns.
- Preventing Yellowing: Special techniques to prevent yellowing, one of the most common concerns brides have about storing their gowns, were thoroughly explained. These methods have been tested and endorsed by the Association of Bridal Consultants, adding a layer of credibility to the services offered by AWGS members.
- Wedding Gown Restoration: For older gowns or gowns that have been damaged, the session included training on restoration techniques, allowing members to bring vintage gowns back to life by returning them to their true color. This is an increasingly popular service as many brides choose to wear or repurpose family heirloom gowns.
In addition to the technical aspects of the training, the session highlighted the sense of community that defines the AWGS organization. Attendees from different countries shared their experiences and insights, creating an environment of mutual support and continuous learning. This network is one of the greatest strengths of AWGS, as it allows members to collaborate and share best practices, even outside of formal training sessions.
AWGS also reiterated its commitment to providing ongoing support to members. This includes 24/7 access to training and technical support from industry leaders. Whether members are facing a particularly challenging stain or need advice on preservation techniques, they have a wealth of knowledge at their fingertips through the AWGS network.
Furthermore, the session underscored AWGS’s dedication to sustainability through its partnership with the Arbor Day Foundation. For every wedding gown preserved by a member, a tree is planted in a forest of great need. This initiative not only reflects the organization’s commitment to environmental responsibility but also adds another dimension of value to the services provided by AWGS members.
One of the key takeaways from the session was the significant industry recognition AWGS members receive. With more than seventy designers recommending AWGS services, members stand out from other cleaners. The organization’s logos, trademarks, and written international guarantee that preserved gowns will not yellow further set members apart and provide peace of mind to brides worldwide.
AWGS’s global reach was evident in the diversity of attendees, with participants from Brazil, Canada, the Philippines, and the U.S. all coming together to share in the experience. The training session proved that no matter where they are located, AWGS members are united by a shared commitment to excellence in wedding gown care.
The two-day training session at Janet Davis Cleaners in Berkley, MI, was a resounding success. It provided members with the hands-on experience and technical knowledge needed to uphold AWGS’s high standards of wedding gown care. More importantly, it reinforced the sense of community and support that makes AWGS a thriving organization. The session was not just about learning—it was about strengthening bonds, sharing knowledge, and continuing the legacy of trust that brides place in AWGS members around the world.
Methods for Management hosts 4th Quarter All Bureau meeting
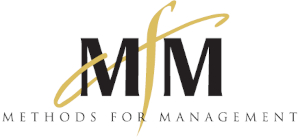
Methods for Management (MfM), a peer membership bureau group serving the dry cleaning industry, hosted a powerful Fourth Quarter ALL Bureau meeting in Las Vegas, coinciding with the DL Expo West. This dynamic event brought together members from across the Canadian Bureau, Mid-America Bureau, East Coast, and West Coast Bureau for an invigorating two-day session focused on operational excellence and strategic planning for the year ahead.
“We are thrilled to have gathered such a diverse group of industry leaders in one room,” said Kermit Engh, Managing Partner of MfM. “Having the larger group expanded the discussion of all topics and provided additional insight when addressing member issues.”
The meeting was an exciting opportunity for collaboration, opening new avenues for dialogue among members and generating valuable ideas for future success.
Meeting Highlights:
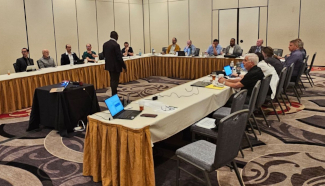
- Collaborative Energy: The All Bureau format energized participants, sparking in-depth conversations and cross-regional learning.
- EFOBAGS & Benchmarks: Members delved into Equipment, Financial, Operating, Bad News, Advertising, Good News and Sales (EFOBAGS) analysis, leveraging MfM’s online database and financial benchmarks to identify areas for improvement.
- Strategic Planning: Each member outlined their #1 initiative for 2025, promoting accountability and focused growth strategies.
- Expert Presentations:
- Francis Flair of Flair Consulting provided valuable insights on employee recruiting, retention, and the critical importance of a formalized onboarding process.
- Mark Albrecht of Route Pros introduced a cutting-edge route management system adopted by 12 major operators, highlighting its potential to boost sales, reduce costs, and enhance customer engagement.
Engh added, “Combining the meeting with the DL Expo West turned out extremely well and added to each member’s overall experience.”
The energy in the room was palpable, as members exchanged ideas, discussed financial trends, and gained actionable takeaways to implement in their businesses. The enthusiasm for this ALL Member format was evident, with members unanimously deciding to adopt this format every other quarter going forward.
“This was one of our most engaging sessions yet,” said Engh. “Bringing members together from different regions stimulated fresh perspectives and allowed for deeper conversations about the opportunities and challenges we all face.”
MfM has announced that the 2025 first-quarter meeting will also follow the ALL Bureau format. It will be hosted by Prestige Cleaners in Knoxville, TX, from January 14-16, 2025.
Methods for Management continues to demonstrate its commitment to fostering innovation, collaboration, and profitability in the dry cleaning industry through its Management Bureau model. By bringing together industry leaders and facilitating the exchange of ideas and best practices, MfM is helping shape the future of the dry cleaning business.
About Methods for Management
Methods for Management, an international consulting group facilitated by Kermit Engh, provides membership to elite dry cleaners who wish to further their expertise and improve their business through shared industry knowledge, local community action, higher productivity and efficiency, and training for excellent quality in garment care and customer service.
Fresh Ideas for the Industry’s Future:
Texcare 2024 educational program
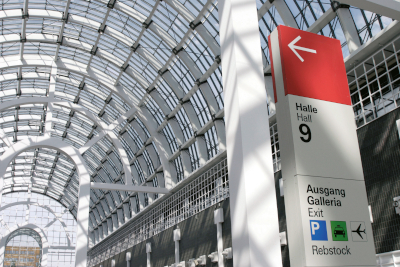
The focus of Texcare International 2024 (6-9 November) will be on the major challenges facing the textile care industry, including automation, energy saving, circular models and textile hygiene. Together with its partners, the leading trade fair has designed a supporting program that can offer progressive ideas for the future of the sector.
“Texcare International is a must-attend exhibition for our industry. It serves as a vital platform for JENSEN and our partners. We are thrilled to return after eight years, eager to showcase our latest innovations and renew connections with clients and industry partners from Germany, Europe, and the world. This show holds a special place in our hearts!” — Jesper Munch Jensen, Jensen-Group
Texcare Forum: free knowledge transfer
The program will launch on Wednesday, 6 November at 12.00 noon with the opening of the fair by the organizers on the Texcare Forum stage. Visitors and exhibitors are warmly invited. This also marks the start of Texcare’s free lecture program, covering the top themes of automation, energy and resources, the circular economy and textile hygiene. It runs over all four days of the fair and was developed in close cooperation with the German Textile Cleaning Association (DTV), VDMA Textile Care, Fabric and Leather Technologies, the European Research Association for Innovative Textile Care (EFIT), the European Textile Service Association (ETSA) and Hohenstein Laboratories.
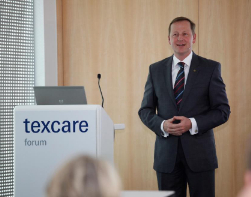
The Forum focuses on promoting the transfer of knowledge between experts, manufacturers and users. In this context, development trends, challenges, status determination and future-oriented solutions for the industry will be examined in detail.
The VDMA and EFIT will address the broad topic of automation in their panels, each with a view to developments in laundries and textile cleaning. The focus will be on the robotization of laundries, digital product passports, data security, and automation approaches for smaller companies.
Current trends in the field of textile hygiene in laundries will be discussed by Hohenstein Laboratories – including the comparison of reusable and disposable products in the healthcare sector, support for end customers in sorting textiles and laundry hygiene certification systems.
“BÖWE exports more than 90 % of its products all over the world. The Texcare International trade fair is therefore very important for us to network and to show the world our latest developments as well as our wide range of products and concepts, which go far beyond just dry cleaning machines.” — Frank Ziermann, BÖWE
The ‘Energy and Resources’ panel, also hosted by the VDMA, will discuss innovative solutions in the service of sustainability. CSR reporting, energy management and CO2 neutrality are at the centre here.
The ETSA is dedicating itself to textile recycling as part of the ‘Circularity’ theme. Among other things, it will be looking at innovations in the field of textile sorting, how to overcome logistical challenges, how to use recycled fibres and how digital platforms can provide support.
In its panel, the DTV will provide information about new business models in the circular economy, from ecodesign to rental and repair services, and the European strategy for sustainable and recyclable textiles.
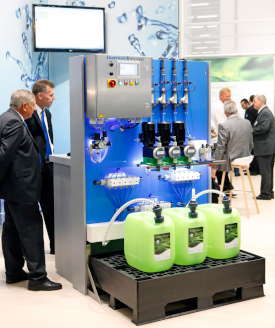
Messe Frankfurt Exhibition GmbH/
Jens Liebchen
The exhibitor presentations: a focus on product innovations
In addition to invited panels, the Texcare Forum will also include a lecture format for exhibitors this year. These companies will present particularly innovative solutions or products from their portfolios to the audience in 20-minute slots. The participating companies include, among others, Ecolab, Kannegiesser, Christeyns, Electrolux, Veit and Seitz.
International market trends and developments
In their ‘International Market Updates’, also at the Texcare Forum, experts from TRSA (Textile Rental Services Association), Sveriges Tvätteriförbund (Swedish Textile Service Association) and Texcare France will be providing well-founded insights into the textile service markets and industry initiatives in their respective countries (Galleria Level 0, A09).
“Automation and robots, ergonomic workspaces and intelligent logistics are revolutionizing our industry. It is crucial to put laundries on the right track now to be prepared for the future – to overcome labor shortages, rising costs, and sustainability demands. The Texcare is a great opportunity to discover how to take the next big step toward a smarter, more sustainable future.” — Michael Harre, Kannegiesser
In the presentation ‘The new Scandinavian Quality Control model’ (Wednesday, 6 November, 1:30 – 2:00 p.m.), the Swedish and Danish Laundry Associations will jointly address developments within the Scandinavian market and provide information about their new quality control model.
Under the title ‘American Linen, Uniform and Facility Services Market: Advocacy, Performance and Sustainability’, the TRSA lecture (Thursday, 7 November, 1:00 – 2:00 p.m.) will shed light on emerging market trends within the nearly $50 billion US North American industry, among other things. The changing economic, social and ecological conditions will also be discussed. The focus will be on reusable materials as a responsible alternative to disposable products, textile services as an integral part of customer sustainability, improved hygiene and the industry’s environmentally friendly reputation.
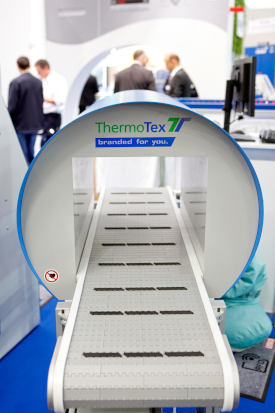
Messe Frankfurt Exhibition GmbH/Jens Liebchen
The Texcare France lecture (Thursday, 7 November, 4:00 – 5:00 p.m.) will address the status quo, current trends and developments in the French market, which is estimated to be worth €3 billion.
As a German company with customers all over the world, we look forward to proving our innovation power once again to Texcare’s international audience. New solutions for sustainable, future-proof textile care and upgraded benchmark solutions like the original wet cleaning meet the highest demands on cleaning performance as well as fibre protection – see you at booth D42! — Christoph Richter, Kreussler
Guided Tours: discover innovations
For the first time, there will be Guided Tours at Texcare. On these tours, curated and led by experts, participants will be introduced to a selection of particularly exciting innovations. The focus is not only on innovations from major key players, but also on advanced solutions from smaller companies. The tours will be conducted in English on all four days of the fair. They are free of charge for holders of a valid Texcare ticket. The tours, which last around an hour, will begin at 1 p.m. on 6 November and at 11 a.m. respectively from 7 to 9 November. The starting point is the Guided Tours stand B 03 in Galleria Level 0. Interested visitors can register to take part at the stand.
Young Competence: together against the shortage of skilled workers
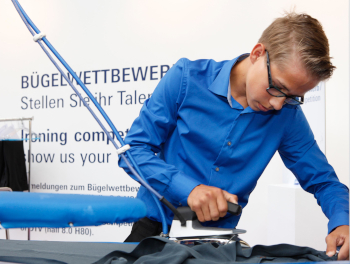
Messe Frankfurt Exhibition GmbH/
Jens Liebchen
Another new feature is the ‘Young Competence’ program, which has been developed in cooperation with the German Textile Cleaning Association (DTV) and vocational schools from Germany and abroad. German-based vocational schools have the opportunity to register for guided tours of Texcare on the Thursday of the fair (7 November) free of charge. Together with their young talent, the schools will visit selected exhibitors at their stands. There, the budding young professionals will have the opportunity to make contacts in the industry and gain exciting insights into the latest technologies and the diverse career options in the textile service industry.
Interested vocational schools can register to participate via the Texcare website.
Industry association events
In addition, leading industry associations use the international platform of Texcare to present themselves with their own special events. Among others, CINET (Comité International De L`Entretien du Textile) invites visitors to its PTC World Congress on 8 and 9 November and presents the internationally renowned Global Best Practices Awards on the afternoon of the last day of the fair (9 November).
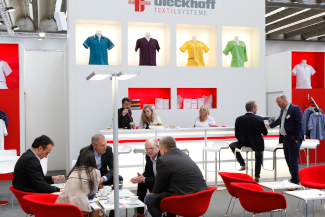
Messe Frankfurt Exhibition GmbH/
Jens Liebchen
Texcare Happy Hour: networking in a relaxed atmosphere
Besides product innovations and knowledge transfer, Texcare International also focuses on the exchange of ideas within the industry. The organizers therefore invite all participants to a daily happy hour (except on the Saturday of the fair). This will take place in Galleria 0, next to Hall 8, from 5.30 p.m. onwards. In a relaxed atmosphere, new contacts can be established, existing ones can be cultivated or a toast to a successful day at the fair can be made.
Further details about the Texcare 2024 supporting program can be found on the website here.
America’s Best Cleaners Holds Fall Accelerator Live Meeting in Denver, CO
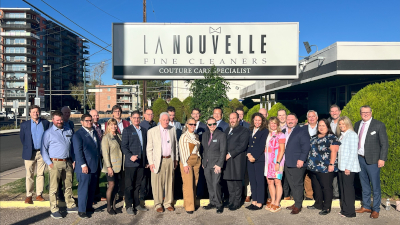
America’s Best Cleaners (ABC) hosted its fall Accelerator Live meeting on September 18-20, 2024, in Denver, CO. The theme of the meeting was “Relationships,” and Affiliates explored the many benefits of building and maintaining long-lasting relationships with employees, retailers, clients and the community.
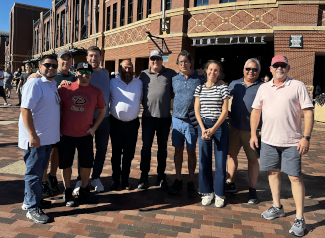
The three-day event was hosted by ABC Affiliate La Nouvelle Fine Cleaners and kicked off with an outing at Coors Field to see the Colorado Rockies host the Arizona Diamondbacks.
In addition to visiting La Nouvelle’s retail production facility, the group also had the opportunity to visit Andrisen Morton, Denver’s premier retailer and long-term partner and supporter of La Nouvelle. Affiliates experienced firsthand the attention to detail and high-touch way that Andrisen Morton cultivates generations of loyal customers.
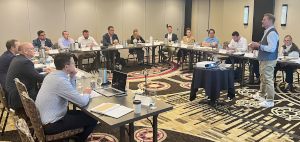
Brent O’Bannon hosted a keynote presentation on Thursday for all affiliates, guests, and partnering sponsors, who each received their Top 5 Clifton Strengths Assessments. On Friday, he led an intensive workshop aimed at helping affiliates implement their newfound skills and identify their teams’ superpowers.
Additionally, representatives from Kreussler Textile Care, Xplor Spot, Be Creative 360, and Sankosha USA delivered snapshot presentations on how they developed and maintained sustainable relationships, sharing products and services that help affiliates strengthen their client connections. This was followed by a panel discussion, where participants explored how to leverage these insights to cultivate meaningful, mutually beneficial relationships that best serve both affiliates and their clients. The event concluded on Friday afternoon with an Affiliate mastermind session led by Chris White.
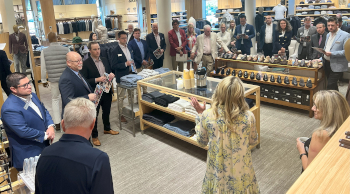
Brent O’Bannon, keynote speaker and Clifton Strengths Specialist, shared, “The ABC Accelerator Event far exceeded my expectations, from top-notch event planning to dynamic networking opportunities. The hands-on 360 audit with La Nouvelle Fine Cleaners, the visit to the iconic Andrisen Morton specialty store, and the deep dive into business core values and customer service were truly remarkable. As a speaker, I found myself inspired by the entire experience.”
Jeanne Meden, owner of ABC Affiliate Charleston Prestige Cleaners, shared, “The accelerator event was outstanding, offering a range of learning experiences, best practice sharing, and enjoyable relationship-building opportunities. I was thrilled to participate and learn from it all.”
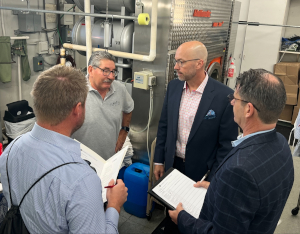
Chris White, ABC Executive Director, shared, “Denver was a truly transformative experience for everyone involved. The energy and enthusiasm from our affiliates, as they embraced the power of genuine relationships, were nothing short of inspiring. Our leaders left the event energized with a new approach to leveraging their existing relationships and building needs-oriented partnerships with our allies in the luxury retail and fashion industries. Moreover, they gained the skills and ability to begin identifying and empowering their teams based on their unique superpowers, fostering a culture of growth and excellence.”
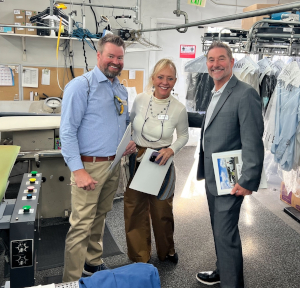
Andre Lobato, Vice President of host La Nouvelle Fine Cleaners, shared, “Hosting the live accelerator event in Denver was both an incredible experience and an honor. As a third-generation professional in the industry, I had a unique opportunity to connect with America’s best owners and operators, showcase our commitment to excellence, and emphasize the importance of building and maintaining lasting relationships with clients and B2B partners. These meetings are critical for expanding our professional network and collaborating to help members succeed in their respective markets.”
ABC would like to thank the event host partners, La Nouvelle Fine Cleaners, as well as the event sponsors, Xplor Spot, Select Risk Insurance Services, Inc., SMRT Systems, Kreussler Chemical, Sankosha, and BeCreative360 for their participation and support.
The next Accelerator Live will be hosted by Fox Cleaners in Tulsa, OK on April 23-25, 2025.
About America’s Best Cleaners:
America’s Best Cleaners is a certification agency and an industry-leading team of consultants who assist owners, managers, and team members to realize their full potential while striving for continued personal and professional success. For more information on America’s Best Cleaners and its Affiliates, visit this page.
ALM Celebrates Milestone:
5,000 Industry Technicians Complete Training Programs
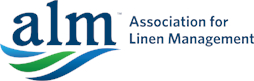
The Association for Linen Management (ALM) announced a remarkable achievement in the textile care industry, with the 5,000th individual completing ALM’s Certificate Programs for technician staff. This significant milestone marks a key moment in the industry’s continuous effort to raise the bar in quality, efficiency, and professional expertise.
ALM’s technician level programs – the Certified Washroom Technician (CWT) and Certified Linen Technician (CLT) are designed to equip front line employees with essential skills and knowledge in laundry operations, linen management, and safety protocols. Graduates of these programs contribute to the success of healthcare, hospitality, and other service industries by ensuring clean, safe, and efficient textile care.
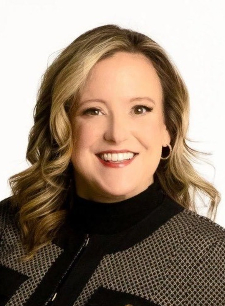
“We are thrilled to celebrate this landmark achievement,” said Sarah Brobeck, RLLD, President & CEO of ALM. “It reflects our commitment to advancing the profession and preparing a workforce that meets the evolving needs of the textile care industry. Each graduate strengthens the quality and efficiency of textile services in organizations, ensuring a positive impact on both employee satisfaction and customer experience. At ALM, we passionately believe that training at all levels, from entry-level technicians to seasoned managers, is essential for the success and sustainability of the textile care industry.”
As the 5,000th individual crosses the finish line, ALM continues to expand its training and certification offerings, adapting to modern technologies and industry trends. The association’s commitment to excellence in education empowers technicians to stay ahead in a competitive and dynamic field.
Included in this expansion are newly created opportunities to make these valuable programs more accessible to the industry with both programs being launched online, and a new group-led format “EmpowerED Facilitator Program” in which classroom style instructional materials are available for use in the field.
These programs are part of ALM’s broader mission to promote best practices in laundry operations and textile management. Considering this milestone, ALM will continue to offer expanded resources and opportunities for professionals to enhance their skills and contribute to the industry’s future success.
For more information, visit ALM’s website.
TRSA Celebrates Industry Milestones at 111th Annual Conference and Exchange
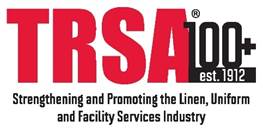
The Textile Rental Services Association (TRSA) recently held its 111th Annual Conference and Exchange at The Broadmoor in Colorado Springs, CO, from September 24-26. The event brought together TRSA members, guests and TRSA staff to celebrate and advance the industry.
The conference kicked off with a Welcome Reception in The Broadmoor’s courtyard, where attendees enjoyed local Colorado beers, wines, and spirits, along with a variety of hors d’oeuvres. This reception provided an excellent opportunity for TRSA members to network and reconnect with industry peers.
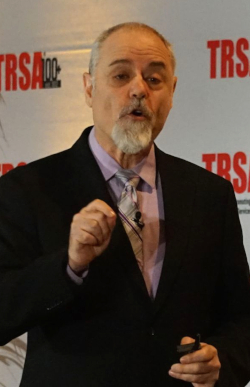
The educational program began the following morning with a keynote session by Jay Samit, who shared his insights on breaking free from the status quo and embracing change. Samit’s presentation highlighted 12 truths for navigating uncertainty and maximizing opportunities, drawing from his extensive experience in transforming the digital landscape.
Attendees then participated in breakout sessions, choosing from topics such as safety excellence, presented by Brian Varner of Safety Solutions for Healthcare, and market growth strategies by Mark Kowalski of Envise Partners LLC. Additional sessions included an industry performance report by Andrew Whittman of Robert W. Baird & Co. and a discussion on organized labor trends in 2024. The day concluded with a creative “Cupcake Clash,” where participants showcased their decorating skills.
The final day featured TRSA’s Annual Business Meeting, focusing on the association’s current projects and the swearing-in of new board members. A panel discussion on succession planning followed. This session featured insights from Bill Evans, retired CEO & chairman of AmeriPride; Patrick Garcia, president, Division Laundry & Cleaners Inc.; Theresa Garcia, COO, Division; and Jim Doro, retired president/owner, Doritex Corp. The panelists discussed the actions they took, or are now planning to take, to maintain their organization’s legacy amid leadership changes.
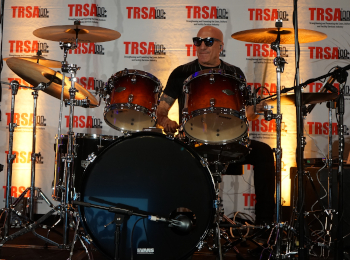
The final keynote speaker of the conference was renowned drummer and rock n’ roll legend, Kenny Aronoff. He seamlessly blended inherited wisdom with hard-earned expertise, offering valuable lessons for succession planning, both within and beyond family businesses. Aronoff identified the tempo shifts required for effective leadership transitions, whether passing the torch within an organization or entering new arenas. His resilience in the face of challenges inspired others to stay in tune with their goals, even when the rhythm gets complicated. He provided insights into overcoming obstacles, maintaining focus, and creating a unique rhythm of success.
In between sessions, attendees had the opportunity to tour The Broadmoor’s on-premise laundry (OPL), organized by Jim Slatcher of Lavatec Laundry Technology Inc. The OPL handles all manners of hospitality facility services, as well as dry-cleaning and repairs to customers’ garments. The tour included a look at the OPL’s new tunnel washer, which has 10, 132 lb. (60 kg) compartments, a 40 bar press, and four double-batch dryers.
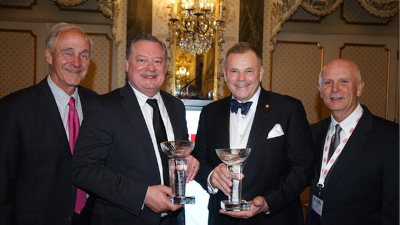
The conference concluded with The Lifetime Achievement Award Dinner, where Jim Kearns, COO of Alsco Uniforms, Salt Lake City, was honored for his term as TRSA Chairman of the Board. Jim Buik, president of Roscoe Co., Chicago, received the Operator Lifetime Achievement Award. Phil Hart, president/CEO of Kannegiesser ETECH, Minneapolis, was honored with the Maglin-Biggie Award, TRSA’s highest award for a supplier partner.
For more information about TRSA and its initiatives, visit TRSA’s website.
Whirlpool Corp. to Showcase Industry-Leading Laundry Solutions at Texcare International 2024
Whirlpool Corp., a global leader in commercial laundry solutions, is excited to announce its participation in Texcare International 2024, taking place in Frankfurt, Germany November 6-9, 2024. As the premier event for the global laundry, cleaning and textile services industry, Texcare serves as the focal point for industry innovation and networking.
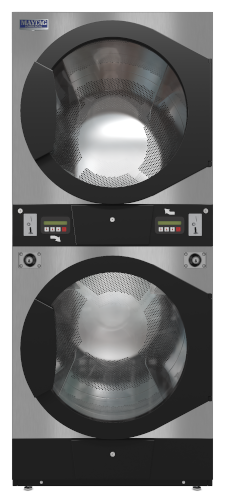
In-Booth Product Showcase: Visitors to Whirlpool’s booth, Hall 8.0, A12, will have the opportunity to explore and interact with a wide range of commercial laundry products, including:
● ADC Dryers: Designed for optimal efficiency and performance.
● Maytag Multiload Washers and Dryers: Ideal for high-capacity and heavy-duty laundry needs.
● Maytag Single Load Washers: Perfect for efficient, daily use.
Daily Product Overviews: Whirlpool’s team of experts will conduct in-depth product overview sessions daily at 11:00 a.m. and 1:00 p.m., offering valuable insights into the latest features and benefits of their machines.
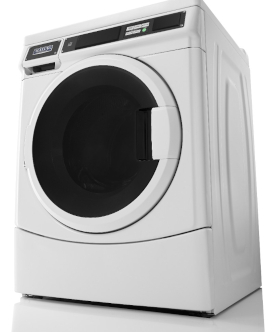
Exciting Giveaways: Attendees who participate in one of the daily product overview sessions will have a chance to win a KitchenAid stand mixer. Daily drawings will be held at 5:00 p.m.
1:1 Meetings: For a more personalized experience, Whirlpool will offer one-on-one meetings with product experts, allowing attendees to delve deeper into Whirlpool’s machine offerings, discuss their specific needs and learn more about the benefits of a Maytag equipped laundry.
“We are thrilled to be part of Texcare International 2024, where we can connect with industry professionals from around the world,” said Luis Lopez, General Manager of Commercial Laundry at Whirlpool Corp. “Our team is eager to demonstrate how our comprehensive laundry solutions can drive business success, combining innovation with the reliability that ADC and Maytag are known for.”
Canadian Randy Bartsch Elected as Chair of TRSA Board of Directors
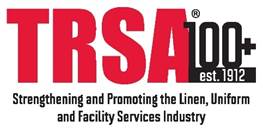
The Textile Rental Service Association’s (TRSA) 111th Annual Conference was held in Colorado Springs, CO recently, and new board members were elected at its Annual Business Meeting.

Randy Bartsch, Chairman of Ecotex Healthcare Linen Service, based in Vancouver, Canada was elected as the 68th Chair of TRSA’s Board of Directors. Bartsch made history as the first elected leader from outside the U.S. Bartsch’s major objective as the new chair of TRSA is to focus on promoting environmental sustainability and the efficacy of reusable linen and textiles.
Bartsch believes that the industry and North American economy are at an inflection point with mixed growth and consolidation, and he envisions a future with opportunities for both national and independent laundry operators. “My preference is to see a robust and diverse industry where independent operators can learn and grow,” said Bartsch.
Outgoing chair, Jim Kearns reflected on his tenure as TRSA chair, highlighting significant progress in advocacy, developing Environmental Social Governance (ESG) resources, and promulgating industry best practices Through support of TRSA’s Executive Management Institute (EMI) programs leadership development and Hygienically Clean Certification. He emphasized the rewarding journey of generating positive change in the textile services industry. “I am confident in Randy’s leadership to continue these efforts and encourage TRSA members to stay involved and support the industry’s ongoing progress,” Kearns said.
TRSA President & CEO Joseph Ricci expressed his gratitude to Kearns for his dedicated service and warmly welcomed Bartsch as the new chair. “Jim has been an exceptional leader, driving significant progress in advocacy and reinforcing industry best practices. We are deeply thankful for his contributions and the positive impact he has made for the industry and TRSA,” Ricci said. “As we welcome Randy, we are excited about the future. His commitment to sustainability, certification and education will undoubtedly steer TRSA toward continued growth and innovation. I encourage all members to support Randy as we embark on this new chapter together.”
TRSA also elected additional Officers and Directors:
- P.J. Dempsey, president, Dempsey Uniform & Linen Supply (vice chair)
- Roger Harris, president & CEO, Metro Linen (treasurer)
- Scott Burke, President, Loop Linen (2nd Term )
- Rich Kramer, President, City Uniforms and Linen
- Ed Orzetti, CEO, ImageFirst
In addition, the TRSA Supplier Partner Council has elected Anwer Shakoor, vice president, Unitex International Inc., as the Director Candidate representing Soft Goods.
Bartsch added a message to members, “The TRSA Board of Directors represents the interests of the industry’s diverse membership, including our independent operators, national and international companies as well as our supplier partners. Each of us are an important part of an essential service that supplies, launders and maintains linens, uniforms and other reusable textiles and facility services for customers in every sector of the economy. We must work together to strengthen our industry, and create a more sustainable future for our customers and the communities we serve.”
SEPTEMBER 2024 NEWS
Alsco Uniforms opens state-of-the-art processing facility in BC
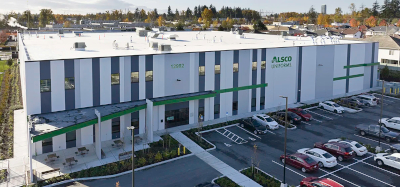
Alsco Uniforms announced the opening of its new state-of-the-art laundry processing facility in Surrey, British Columbia. The plant relocated earlier this year from the company’s downtown Vancouver facility. This new plant is designed to produce hygienically clean uniforms, linens, floor mats, mops, and first aid and restroom supplies to better serve a growing customer base throughout British Columbia.
With a fleet of 20 delivery vehicles, Alsco Uniforms currently services more than 1,500 customers from the Whistler area to the Fraser Valley, covering more than 500 kilometers. This new facility, spanning 62,000 square feet on 4.5 acres in Surrey, BC, is among the most advanced of its kind in North America. It features cutting-edge technology that significantly enhances operational efficiency, allowing them to process more than 300,000 pounds of laundry per week.
Bob Steiner, Chief Executive Officer, shared his thoughts on this new facility, “Our new plant is designed with the future in mind, equipped to handle up to three times as many customers. This capability ensures that we are well prepared to meet growing customer demands and continue delivering exceptional service.”
Alsco Uniforms maintained a commitment to the community as a central focus when building this facility. This plant employs more than 90 full-time staff and has contributed to local enhancement projects, including the planting of 2,000 new trees, the expansion of streets, and the installation of public benches. “We are so proud of our new facility and the positive impact we will make in the Surrey community for many years to come,” said General Manager Dan Barnetson.
Linda Annis, Councillor for the city of Surrey, said, “What a terrific new addition to Surrey and our Newton neighbourhood. With 135 years of experience, the Alsco Uniforms list of clients is impressive and a reflection of the professionalism and service that has become a hallmark of the company. Like Alsco Uniforms, Surrey is growing, and in five short years we will be British Columbia’s largest city. Having well-established companies like Alsco Uniforms in our community makes me even more optimistic about our city’s future as a great place to work and live.”
Alsco Uniforms believes in sustainable growth. Their facility is equipped with advanced laundry processing technology designed to reduce water and energy usage, minimizing their environmental footprint. They are committed to sustainable practices that benefit both the community and the environment. They believe reusable uniforms and linen support sustainability and should be something every business should consider rather than relying on the convenience of using disposable products to keep their facilities clean and safe.
UniFirst opens new uniform service and processing facility in London, Ontario
New facility designed to enhance uniform services across Southwestern Ontario
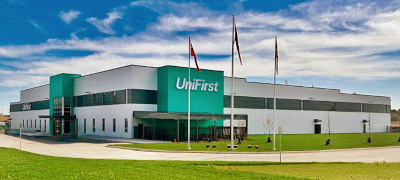
UniFirst Corporation (NYSE:UNF), a North American leader in providing customized business uniform programs, facility service products and first aid and safety services, announced the grand opening of its latest state-of-the-art uniform service and processing facility in London, Ontario. The facility, located at 2365 Innovation Drive, London, Ontario, marks a significant investment in the region and underscores UniFirst’s commitment to supporting businesses across London, Guelph, Cambridge, Kitchener, Chatham, Windsor, and surrounding areas with enhanced service capabilities.
The 56,000 square-foot-facility is equipped with advanced processing technology designed to optimize the quality and efficiency of uniform cleaning, maintenance, and delivery. With a focus on sustainability, the plant incorporates several environmentally friendly features, including energy-efficient systems and water conservation measures, aligning with UniFirst’s ongoing commitment to reducing its environmental footprint.
The new facility will serve nearly 2000 customers across Southwestern Ontario, providing a range of services, including uniform and workwear rental, laundering, and maintenance, as well as facility products and services for industries spanning healthcare, hospitality, food processing, manufacturing, and more. The plant employs approximately 80 residents, contributing to the economic growth of the London community.
“We are thrilled to open our new facility in London, Ontario, which will allow us to better serve our customers in this region with the highest levels of service and efficiency,” said Steven Sintros, UniFirst President and CEO. “Our state-of-the-art facility represents our commitment to continuous improvement and our promise to always deliver to the communities where we operate.”
Michelle Clarke, General Manager, added, “This new plant is a testament to our team’s hard work and dedication to our customers. We’re excited to bring the latest in uniform service technology to Southwestern Ontario and to provide our customers with the reliable, high-quality service they’ve come to expect from UniFirst.”
The grand opening event took place on September 10 with a ribbon-cutting ceremony. Special guests included London Mayor Josh Morgan, representatives from the London Economic Development Corporation, UniFirst executives, and employees.
TRSA Programs Graduate 2024 Classes
The Textile Rental Services Association (TRSA) hosted the 59th annual commencement of its Executive Management Institute (EMI) on August 15th. The event, held at a conference center near the University of Maryland, celebrated the achievements of 26 graduates from this prestigious four-year educational program. Nearly 170 students from all four classes, along with faculty, staff, and guests, attended the ceremony.
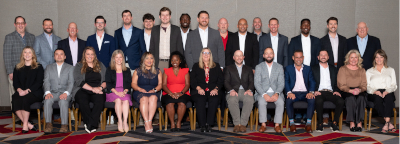
The Year IV graduates represented a diverse group of executives from national, regional, and independent commercial laundries across North America, as well as several supplier-partner company representatives. TRSA President & CEO Joseph Ricci presented the graduation certificates, followed by reflections from Brian Kimmel of Kimmel Corp., Upper Sandusky, OH. Kimmel praised his fellow graduates as “great ambassadors from this industry” and expressed his gratitude for being part of the program.
Kimmel also acknowledged the contributions of Year IV faculty members Dan Gonder and Eric Kurjan. He highlighted Kurjan’s emphasis on the importance of developing skills for individual and company success, quoting Kurjan’s advice on finding the right team players who are “hungry, humble, and smart.”
The camaraderie and openness among the students were evident throughout the program. Kimmel noted, “The trust that we have with each other, it’s real. We have some lifelong friends, and it took four years to build.”
The commencement program featured fewer speeches and skits compared to previous years, with the Year IV group standing out with a parody of “Family Feud.” Kimmel and fellow graduate Emily Hauber of CITY Clean and Simple, Oelwein, IA, entertained the audience with their humorous take on the EMI experience.
Jim Underwood, Year III instructor, paid tribute to the late Les Frankfurt, a Holocaust survivor and psychology professor who co-founded EMI Year III. Underwood emphasized Frankfurt’s lasting impact on the program and the importance of caring in leadership, a sentiment echoed by Kimmel in his closing remarks.
TRSA President & CEO Joseph Ricci concluded the ceremony by recognizing the dedication of the EMI faculty, who volunteer their time and expertise to support the program. Ricci emphasized the long-term growth and development that EMI fosters, stating, “You are the future of this industry. Your employers invest in you because they believe in your potential.”
First-year attendee, Meredyth Ellington, TRSA database manager, added, “Attending the first year of EMI as an attendee and not as a staffer provided me with a fresh perspective on our industry. The expertly taught classes and the invaluable knowledge gained from my peers is significantly enhancing my leadership skills.”
The event concluded with a networking reception at the College Park Marriott Hotel & Conference Center, where attendees celebrated their achievements and strengthened their professional connections.
TRSA extends its gratitude to the supplier-partner sponsors of the 2024 EMI program, including Kannegiesser ETECH, JENSEN USA, Ellis Corp., Pellerin Milnor Corp, Unitex International Inc., G.A. Braun Inc., Brim Laundry Machinery Co. Inc., Lavatec Laundry Technology Inc., Monarch Brands, Morgan Olson, and Workwear Outfitters.
Production Management Institute
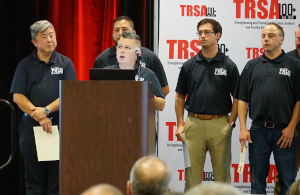
At the same time, TRSA concluded its 34th Annual Production Management Institute (PMI) with a graduation ceremony on August 15. The event, held at the College Park Marriott Hotel & Conference Center near the University of Maryland campus, celebrated the achievements of the program’s participants, including a standout group of graduates who dubbed themselves “The Magnificent Seven.”
Wendy Adriano of Crown Linen and Uniform Service, Brockton, MA, speaking on behalf of the graduates, praised the program: “This year’s experience was great; we were very happy to be here. It’s been outstanding.” The two-year program saw a total of 30 participants, with the Year II group of seven receiving their graduation certificates.
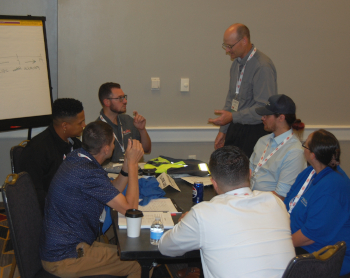
Adriano encouraged her fellow PMI attendees to maintain the connections they had formed: “Keep your emails going. You have great contacts. Just stay in contact with each other.” She highlighted the camaraderie developed during the week-long program from August 11-15, noting, “We built great relationships. Not just with the people we work with, but with different backgrounds and from different areas of the country. I think it’s been really helpful for us. We’re excited that we’ll be able to take everything we’ve learned and really make an effort to help our companies become even more successful.”
Named in honor of its founder, the late Roger F. Cocivera, PMI is designed to help new and experienced managers in the linen, uniform, and facility services industry learn and incorporate production-management principles and practices. The program focuses on developing the core skills and knowledge necessary to operate plants more efficiently and effectively. It includes four days of interactive classroom training, followed by a year of self-paced online modules and an additional four days of training in Year II.
PMI sponsors included Kannegiesser ETECH, Alliant Systems, JENSEN USA, Ellis Corp., Pellerin Milnor Corp., Unitex International Inc., G.A. Braun Inc., Brim Laundry Machinery Co. Inc., Lavatec Laundry Technology Inc., Monarch Brands, Morgan Olson, and Workwear Outfitters.
For more information on TRSA and its programs, click here.
ProtoTitan Acquires Leonard Automatics
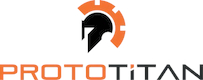
ProtoTitan, a North Carolina-based provider of engineering and manufacturing solutions, has recently announced its acquisition of Leonard Automatics, a global leader in textile finishing equipment. With this strategic move, ProtoTitan aims to further enhance its position as a trusted partner for businesses seeking advanced manufacturing solutions to optimize their operations.
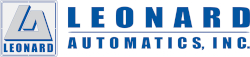
The acquisition brings together two major industry players with complementary strengths and expertise. By merging ProtoTitan’s cutting-edge engineering and manufacturing solutions with Leonard Automatics’ in-house metal fabrication and electrical engineering capabilities, ProtoTitan is creating a formidable synergy that will enhance operations and deliver unparalleled benefits to both companies and their customers. This strategic move not only amplifies ProtoTitan’s collective capabilities but also reinforces our commitment to delivering innovative, high-quality solutions that meet and exceed market demands.
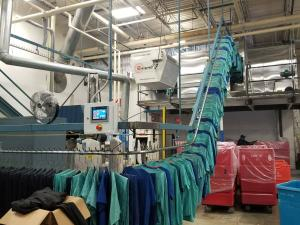
As part of the acquisition, Jeff Frushtick will be stepping down from his role as Leonard Automatics CEO and refocusing on sales and customer support. ProtoTitan brings a wealth of operations management and strategy as co-founders Chris Clark and Dave Rochau will be taking over daily operations of Leonard Automatics and its subsidiaries Leonard Fabrication & Design, LFD Off Road and LFD Gates.
“It is time to turn the helm over to the next generation, with more understanding of the technology that can carry us forward,” commented Leonard Automatics CEO, Jeff Frushtick. “ProtoTitan brings a variety of skill sets and markets that complement and expand the opportunities for Leonard manufacturing. I am excited to be part of the continuing evolution of Leonard Automatics.”
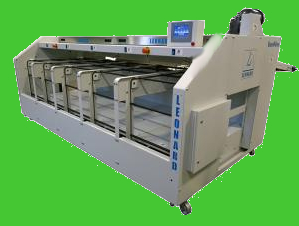
“Leonard Automatics is a true innovator and has been instrumental in the textile and laundry industry’s progress over the past several decades,” said Chris Clark, Co-Founder and CEO of ProtoTitan. “Jeff’s decades of experience in this world are an invaluable asset, and we’re very excited to give him the space to revitalize this market.”
This landmark partnership underscores ProtoTitan’s unwavering commitment to innovation and growth, heralding a new era of operational excellence for the company. By welcoming Leonard Automatics into the ProtoTitan family—which already boasts industry leaders such as Armageddon Turbo, Sawicki Speed, KB Titan Racing, and Veer Performance—ProtoTitan has significantly elevated its engineering and manufacturing prowess. This strategic alliance not only enhances our capabilities but also solidifies our position at the forefront of industry advancements, ensuring we continue to deliver unparalleled value and cutting-edge solutions to its clients.
AUGUST 2024 NEWS
CINET Growth Hacker Award 2024 will net winner €20,000
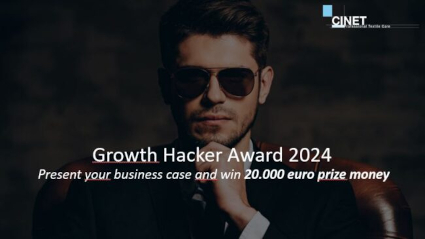
The CINET Growth Hacker Award 2024 is your chance to lead the change in transforming the Professional Textile Care (PTC) industry. This prestigious award, which includes a €20,000 prize, will be presented at the Texcare Show in Frankfurt on November 8-9, 2024. The DEADLINE for submissions is SEPTEMBER 10.
Goal: New Business & industry growth
The central theme of this award is ‘new business‘. The goal of the award is to stimulate PTC companies to service customer groups which weren’t serviced before, resulting in industry growth. A good example is the development of ‘wash & fold laundry services’, where consumers and commercial clients start outsourcing laundry that was previously done in a domestic washer at home. The CINET Growth Hacker Award is intended for promising startups, as well as innovative existing PTC companies worldwide.
Criteria
The award will be judged based on qualitative and quantitative data. The qualitative data is derived from filling out the business model canvas. This is a simple frame used to visually explain a business case. The quantitative data is based on sales/revenue, #orders, #customers, retention rates, CAC (cost per acquired customer), ATV (average transaction value), CLV (customer lifetime value) and customer satisfaction scores such as Google ratings.
Program milestones
The program is designed for exchanging information, know-how and practical experiences between the participants and recognised experts. This will include a wide variety of topics. Participation involves joining 3 – 4 sessions online. There will also be one or two personal encounters organized in Sweden and the UK in the months before Texcare in Frankfurt. These will be hosted by international esteemed brands in the industry. Participants are invited to discuss their ideas on new business in professional textile care and present their Business Case for an independent International Jury of experts, presided by Mr. Geert Boettger of EXPO + Consulting. The CINET Growth Hacker Award will be chaired by Mr. Leon Wennekes of TextileCare Research.
How to participate
Cost for participation is Euro 150,- (excl. VAT), including all materials, drinks and catering (excluding flights and hotel).
FOR MORE INFORMATION visit the CINET website on this program.
CINET members can have 1 person participate free of charge. This initiative is supported by Electrolux Professional.
DLI Announces 2024 Hall of Fame Inductees
The Drycleaning & Laundry Institute (DLI) announced the induction of three outstanding industry professionals into its Hall of Fame. This prestigious honor recognizes individuals who have made significant contributions to the dry cleaning and laundry industry.
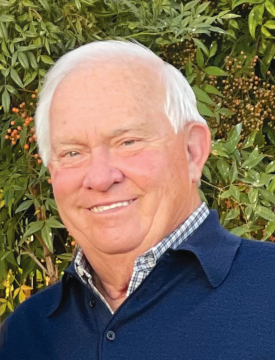
Jim Douglas, representing GreenEarth Cleaning, played a pivotal role in advancing environmentally-friendly cleaning technologies. As a co-founder of Prestige Cleaners in Sacramento, CA, and GreenEarth Cleaning, Douglas developed and promotes safe, sustainable cleaning methods. His leadership roles, including serving as President of the California Cleaners Association and other industry groups, reflect his commitment to the industry.
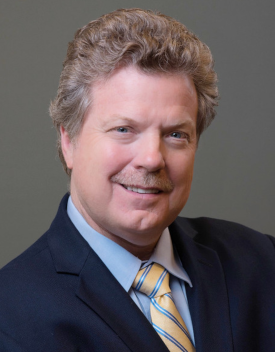
Mike Nesbit, of Texas-based Edit TX, LLC., one of the largest dry cleaning businesses in the U.S., has made substantial contributions through his leadership and innovation. As a Past President of DLI and a key figure in the establishment of the Texas Dry Cleaner Remediation Program, Nesbit is a strong advocate for environmental responsibility. His innovative spirit is also evident in his role as a pioneer of offsite locker pickup and delivery systems, which have since become standard in the industry.
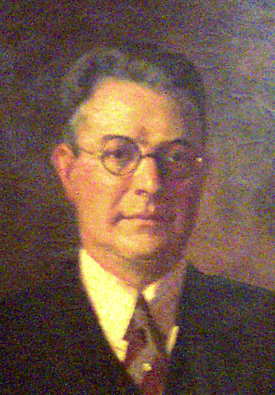
Joseph William “Dixie” Stoddard, Past President of DLI and inventor of Stoddard Solvent, revolutionized the dry cleaning industry in the 1920s with the development of the less-flammable Stoddard Solvent, significantly enhancing safety standards throughout the industry. Stoddard’s dedication to improving industry practices and promoting education continues to influence DLI’s priorities and modern dry cleaning practices.
Honoring Excellence
These inductees exemplify the highest standards of leadership, integrity, and dedication to the industry. The DLI Hall of Fame Award recognizes industry professionals who have demonstrated exemplary leadership, innovation, and commitment to excellence. This year’s group of inductees join the following professionals in receiving this award: Barney Deden, Stan Golomb, Chris Edwards, Jeffrey Miller, Sid Tuchman, Donald Fawcett, Walter “Buster” Bell, and Milton Chortkoff.
“We are grateful to everyone who nominated an industry legend for this award, be they members of DLI or otherwise,” Mary Scalco, DLI’s CEO said. “We know excellence on this level can be found in all corners of our industry. Our goals is to spotlight those professionals whose contributions stand to inspire others and help make our industry stronger.”
DLI’s Board of Directors will present the awards to this year’s group of Hall of Fame inductees at events of their choosing. Details for the 2025 Hall of Fame nomination period will be released early next year.
For more information on DLI’s Hall of Fame, please visit DLIonline.org/HoF.
HLS Celebrates 50 Years, CEO Award
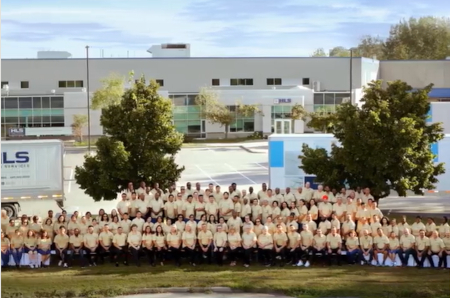
HLS Linen Services (HLS) is celebrating 50 years of excellence in 2024. Established in 1974, the company provides a centralized, cost-effective linen service for its many customers, including acute care hospitals, long term care facilities, hotels, hospitality providers, rehabilitation centres and mental health facilities. The staff and management are internationally recognized as leaders in North America for quality finishing and cost-effective processing.
HLS Linen Services is an Ontario-based company with two locations in Ottawa and Woodbridge, and services many regions of Ontario and Western Quebec.
The company has two locations which are state-of-the-art. Both location plants represent a combined total of 250,000 square feet, processing approximately 70 million pounds of linen per year with the capacity to process up to 120 million pounds of linen yearly.
Leading by Example
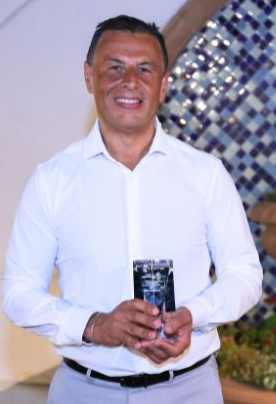
Rocco Romeo, CEO of HLS, was honoured with the prestigious 2024 Don Pedder Lifetime Achievement Award from the International Association for Healthcare Textile Management (IAHTM). This accolade stands as a testament to Rocco’s unwavering commitment, his unparalleled leadership, and his remarkable contributions to the industry.
In the heartfelt words of Matthew Victor, during his award speech: “If there’s one value I hold dear, it’s the enduring importance of integrity. They say, ‘Success will come and go, but integrity is forever.'” These words encapsulate the essence of Rocco’s character—the embodiment of integrity, the steadfast dedication to doing what’s right, even when no one is watching.
Rocco’s career trajectory, marked by over 75 million pounds in annual shipments across our two plants, and his vast operational reach across Ontario and Western Quebec, has been built on a foundation of honesty, integrity, and forward-thinking leadership. His remarkable contributions extend beyond his role as CEO of HLS Linen Services, encompassing a lifelong commitment to advancing the industry. This recognition is truly deserved, and the entire HLS team takes pride in it!
A note from Rocco, “I am truly honoured and grateful. There is no greater honour in one’s career than to be recognized by your peers in an industry I have been proud to be part of. Thank you to everyone who has been with me on the journey.”
JULY 2024 NEWS
Jensen-Group acquires a majority stake in Maxi-Press Holding GmbH, Germany and its subsidiaries.
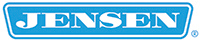
Jensen-Group is pleased to announce the acquisition of 85% of the share capital of Maxi-Press Holding GmbH, Germany and its subsidiaries (“Maxi-Press”). This strategic move will help to develop Jensen-Group’s offerings in consumables, spares and services, further solidifying its position in the global heavy duty laundry market.
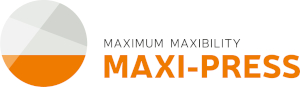
Maxi-Press, renowned for its leading market share in press cushions as well as its unique range of consumables, will play a pivotal role in enhancing Jensen-Group’s service business. The acquisition is fully aligned with Jensen-Group’s long-term value creation strategy, aiming to provide a comprehensive range of service propositions to laundries across the globe. For the fiscal year ending on December 31, 2023, Maxi-Press reported consolidated revenues of 21.5 million euro and an EBITDA of 5.6 million euro.
“I am truly impressed by the company’s market position and growth trajectory, resulting from the Maxi-Press team efforts under the leadership of Mr. Zaiser in just fifteen years and I am looking forward to working together with Mr. Zaiser to further grow the business and take Maxi-Press to the next level,” stated Jesper M. Jensen, CEO of Jensen-Group.
“I knew that one day they would reach out to me, and I am very proud that Maxi-Press becomes a member of the Jensen-Group” said Mr. Zaiser, Managing Director of Maxi-Press, sharing his enthusiasm about joining Jensen-Group, a vision he has harbored for years.
Dr. Himmelmann from the private equity firm Auctus Capital Partners AG, Germany, former majority owner of Maxi-Press stated: “We have seen how Maxi-Press has shown tremendous growth even during the COVID years and are happy to hand over a well-run company to a strategic buyer like Jensen-Group”.
Under the agreement, Maxi-Press will continue to operate under the well-established Maxi-Press brand, while Mr. Zaiser will report directly to the Jensen-Group Executive Management Team.
The acquisition of Maxi-Press marks a significant milestone in Jensen-Group’s journey to enhance its service offerings and its global leading position as a provider of full-fledged laundry solutions. With Maxi-Press joining its ranks, Jensen-Group is well-placed to offer a broad range of high-quality consumables, spares and services to its customers worldwide.
Street’s Announces “On The Spot™” Stain Removal Guide with Videos in English, Korean and Spanish
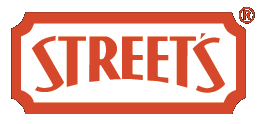
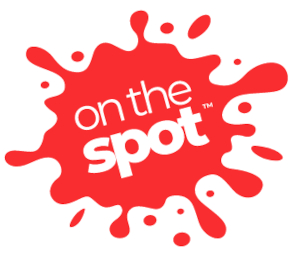
R. R. Street & Co. Inc. has announced the launch of their new “On the Spot” Stain Removal Guide, an online resource for step-by-step videos, expert tips and fast results.
The world today seeks quick answers and solutions from their cell phones, and it is Street’s goal to provide easy access to on-the-go video instruction for removal of commonly encountered stains in any process.
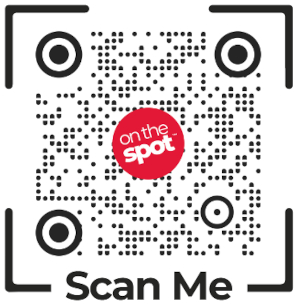
Employees working at the spotting board can easily access “On the Spot” with their phone at 4streets.com/onthespot/ or can simply scan the QR Code below to be conveniently connected to this helpful tool. Stickers featuring the convenient QR Code are available for placement on or near the spotting board.
“On the Spot” is easy to use—the user will be able to find the stain they are looking for in the “search by stain” box, or by clicking on the solvent in use and then the correct category of stain. Also included are introductory videos about the “Proper Use of the Spotting Board” as well as “Stain Identification & Classification”. All videos are available in English, Spanish and Korean.
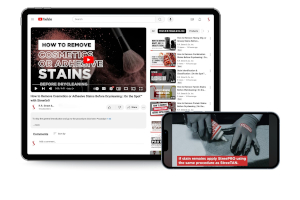
“On The Spot” features some of the most popular Street’s stain removal products, but also identifies comparable Adco® and Laidlaw® products that can be used as an alternative. For each stain removal procedure and video, additional links are provided for more specific product information.
Kristen Vos, Executive Vice President at Street’s, commented:
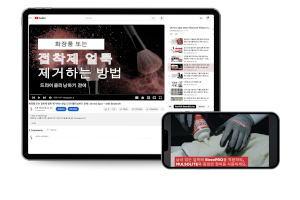
“For nearly 150 years, Street’s has been a leader in creating products that achieve the highest level of fabric care. Our stain removal products are recognized throughout the world for their effectiveness. But, unless used
properly, they won’t achieve the excellent results they were designed for. We hope that “On the Spot” not only helps make our customers’ jobs easier, but also helps them achieve the best possible results with our products.”
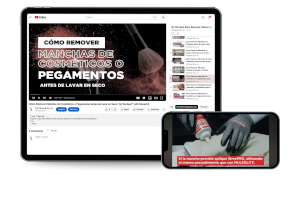
Street’s new “On The Spot” Stain Removal Guide is the latest addition to Street’s Academy at 4streets.com. It is Street’s intention to continue to build a reliable online resource for information and instruction related to quality fabric care.
Check out “On The Spot” at 4streets.com/onthespot/ or email Street’s at info@4streets.com for free stickers and additional product information.
Coin Laundry Association Embraces Industry Changes with New Name and Branding
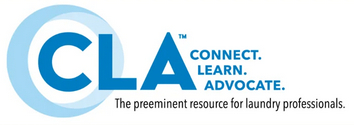
The largest trade organization dedicated to the vended laundry industry is excited to announce an update to its branding, including its name. The Coin Laundry Association will now be known as simply “CLA,” with each of the three letters signifying an action that the highly respected organization makes possible for its 1500+ members (connect, learn, advocate). Additionally, its refreshed tagline, “the preeminent resource for laundry professionals”, speaks to its unwavering commitment to provide valuable and tangible resources to those members.
CLA has begun rolling out the refreshed name and brand look across its social channels and email communications to members. Members of the community will continue to see the new branding replace the previous brand look throughout the year.
Founded in 1960, the association has empowered thousands of store owners, investors, manufacturers and distributors to successfully navigate industry shifts — from the dramatic rise in cashless payments to the demand for value-add services like wash and fold. Now CLA is adopting a refreshed name and look to reflect its dedication to staying current and helping the vended laundry community do the same.
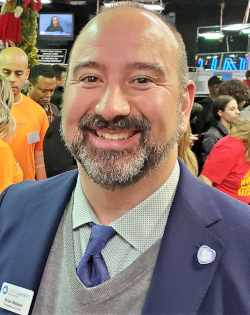
“Updating our name and branding felt like the perfect step forward as we continue to evolve alongside the vended laundry industry,” said CLA President and CEO Brian Wallace. “Our commitment to supporting our members remains unwavering, and this rebranding underscores our dedication to innovation and growth while continuing to provide the same high level of support and resources that our members rely on.”
No changes will be made to the market insights and opportunities CLA provides to its members, such as white papers and training kits focused on best practices, exclusive discounts on solutions vetted by the association, advocacy efforts at the state and federal levels and in-person events like the Wash-Dry-Fold Workshop, September 18-20, in Nashville, Tenn. As always, CLA’s offerings will feature updated content designed to keep members ahead of trends and other factors that impact their businesses.
For more information about CLA, membership benefits and upcoming events, visit coinlaundry.org.
DLI Announces 2024-2025 Board of Directors
Each year DLI’s Board of Directors brings on new members as other members retire or move into Executive Committee positions. This June DLI’s Board bid farewell to Chairman Jeff Schwegmann II of U.S. Leather Cleaning and Sunshine Cleaners in Cold Spring, KY, and John Mertes of Ziker Cleaners in Mishawaka, IN, at its Summer Board Meeting.
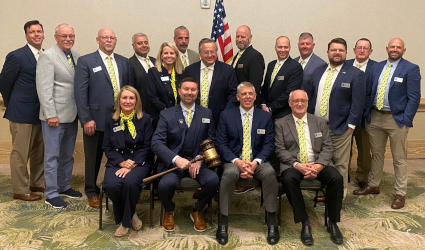
Back Row (l-r): Don Holochek, District Three Director; Larry Fish, District One Director; Norman Way, District Two Director; Ray Rangwala, District Eight Director; Rhonda Eysel, District Three Committee Member; Dan Sims, District Five Director; Tom Ustanik, District Five Committee Member; Allan Cripe, District Six Committee Member; David Grippi, District One DCM; Mark Albrecht, Allied Trades Director; Jeff Jordan, Allied Trades Committee Member; Danny Bahlman, CGCP®, District Six Director; Ryan Fish, District Seven Director.
Not Pictured: Chris Edwards, District 7 Committee Member.
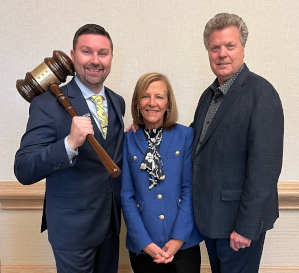
Nesbit Dynasty — DLI’s 2024-2025 President Kyle Nesbit (left) poses with CEO Mary Scalco and his father Mike Nesbit, DLI Past President 2017-2018.
Kathy Benzinger moved to the Chair position while Kyle Nesbit became President for the 2024-2025 term. Toran Brown became President-Elect and Ray Kroner was elected Treasurer. All Executive Committee positions are for the 2024–2025 term.
All Executive, Director, and District Committee Member leadership positions are volunteer. DLI greatly appreciates the time and resources all members of the Board of Directors share in guiding the Institute.
DLI exists to help member drycleaners succeed.
Learn more at DLIonline.org
K-Bro Acquires Buanderie CM, Inc. for $12 million
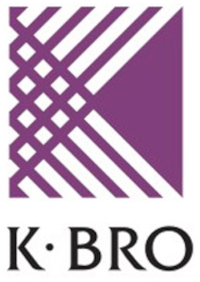
K-Bro Linen Inc. (“K-Bro” or the “Corporation“) (TSX: KBL) announced that it has successfully completed its acquisition of Buanderie C.M. Inc. (“C.M.”) for an enterprise value of $12 million, on a cash-free, debt-free basis. The transaction includes the real estate for C.M.’s processing and storage facilities located in North Montréal. The acquisition is being funded entirely from K-Bro’s syndicated revolving credit facility and, after synergies, is expected to be accretive to the Corporation.

C.M. is a private laundry and linen operator located in Montréal and serving the healthcare market with annual revenues of approximately $7.3 million. The acquisition will enable K-Bro to operate with two facilities in Montreal to service its growing healthcare and hospitality business.
“K-Bro is proud to serve Quebec and we are excited to further diversify our customer base in the province. C.M. has been serving top-tier healthcare customers in the attractive Montréal market for decades. Our acquisition of C.M. expands K-Bro’s healthcare customer base, increases healthcare volumes, adds additional healthcare capacity, and supports significant future growth opportunities,” said Linda McCurdy, President and Chief Executive Officer at K-Bro.
“The C.M. acquisition aligns with our strategy of acquiring high-quality operators. We’re excited about our outlook and have an active M&A pipeline. K-Bro remains well positioned from a balance sheet and liquidity perspective and will continue to be disciplined as we evaluate acquisitions.”
CORPORATE PROFILE
K-Bro is the largest owner and operator of laundry and linen processing facilities in Canada. K-Bro provides a comprehensive range of general linen and operating room linen processing, management and distribution services to healthcare institutions, hotels and other commercial accounts. K-Bro currently operates ten processing facilities and two distribution centres under two distinctive brands, including K-Bro Linen Systems Inc. and Buanderie HMR, in ten Canadian cities: Québec City, Montréal, Toronto, Regina, Saskatoon, Prince Albert, Edmonton, Calgary, Vancouver and Victoria.
JUNE 2024 NEWS
TRSA Honors Hart
To Receive the Prestigious 2024 Maglin-Biggie Supplier Partner Lifetime Achievement Award
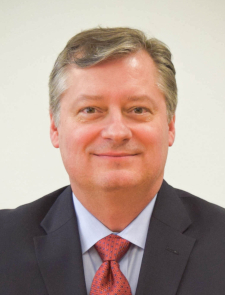
The Textile Rental Services Association (TRSA) announced that Phil Hart, president and CEO of Kannegiesser ETECH, Minneapolis, has been honored with the 2024 Maglin-Biggie Supplier Partner Lifetime Achievement Award. This award is a testament to Hart’s exceptional leadership, his significant contributions to the linen, uniform and facility services industry, and his steadfast dedication to excellence.
“It is a truly unexpected surprise to be nominated for this award,” Hart said. “Many of the names of the prior recipients are people that I have a great deal of respect for and have learned much from. To be associated with those leaders in our industry is truly an honor.”
Revered by his colleagues for creating an outstanding workplace environment and fostering a culture of success and contentment among customers and staff, Hart’s philosophy is that the team should get the credit. This exemplifies his modest approach and belief in shared success. His core principle, “We Do What’s Right,” has garnered him respect from customers and has cultivated a high level of accountability and trust within the Kannegiesser ETECH team. Renowned for his patience and eagerness to educate, Hart engages meaningfully with individuals, remembering personal details and showing sincere interest in their lives. His actions, such as personally ensuring the safe return of ill team members from job sites, demonstrate his faith in his team’s potential and his role as a true leader.
Since joining Kannegiesser USA in 2004, Hart’s visionary leadership has played a crucial role in evolving the company from a European supplier to a formidable U.S. corporation. His pivotal role in the acquisition of ETECH stands as a tribute to his strategic foresight and the acknowledgment of American technological excellence by Kannegiesser. As CEO for the past seven years, Kannegiesser ETECH has become a byword for responsiveness and innovation, always seeking ways to make challenging ideas feasible while maintaining sharp business acumen.
Hart’s TRSA leadership positions and accomplishments include:
- Founding chair and ongoing member of the Supplier Partner Council Board of Directors
- Member of the TRSA Board of Directors
- Contributor to the Strategic Planning Committee
- Instructor at the Production Management Institute (PMI) and Maintenance Management Institute (MMI)
- Steadfast supporter of TRSA programs through advertising and sponsorship
- Host of international plant tours, promoting global industry insights
- Proponent for team engagement in TRSA events, both in-person and virtual
- Participant in DEI Committee meetings at the TRSA Legislative Conference
Kannegiesser ETECH considers it a great privilege that Hart receives this award. Michael Harre, chief sales and service officer, said that, “His loyalty, continuous striving for improvement, and dedication to the industry, have set a high standard within our organization. Moreover, Phil’s valuable contributions have helped advance our industry, making him a deserving recipient of this award. Kannegiesser, as a supplier, is deeply committed to the same principles and values. Over the past two decades, Phil has exemplified dedication and excellence, and this award reflects our shared commitment to advancing the industry and setting new standards. We extend our sincere congratulations to Phil Hart and celebrate this well-deserved honor.”
Hart will receive the award at TRSA’s 111th Annual Conference & Exchange, this Sept. 24-25 at The Broadmoor in Colorado Springs, CO. Registration and details can be found at www.trsa.org/annual conference.
ALM Revises Bylaws, Makes Leadership Changes
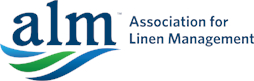
Brobeck to Become President/CEO
The Association for Linen Management’s (ALMs’s) membership voted to revise the association’s bylaws to modernize the organization’s governance structure and enhance the leadership framework. As a result of the affirmative vote, the Board of Directors’ role has been clarified to become more strategic in nature, allowing them to concentrate on oversight, policy-making, and long-term strategy. As a result of this change, the chief elected officer will assume the title of chairman, while the chief staff officer, will assume the title of President and CEO.
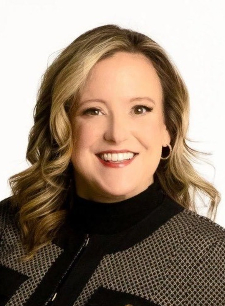
Sarah Brobeck, RLLD who joined the staff in 2022 as Executive Director will become ALM’s President and CEO effective July 1. In this elevated role, Brobeck will not only drive the association’s strategic initiatives, but will represent the association with a keen focus on its growth and development.
Brobeck came to the association with over 15 years of experience working in textile care services, which fortified her business acumen with extensive insight on the industry along with a vast network of connections. In her first 18 months as Executive Director, Brobeck led the association through two record-breaking IMPACT conferences, along with the development of new programs and services designed to provide more value to all members.
Brobeck has a rich history in developing teams and fostering individual growth, marked by her strategic vision and empathetic leadership. She has successfully built and managed diverse teams, driving them towards achieving high performance and collaboration. She intends to use this experience to build and launch ALM’s future leaders program, which will provide education and mentoring for individuals embarking on their own leadership journey.
“Sarah’s passion and dedication to the industry and association, along with her adept leadership style made her the ideal candidate for the Executive Director position,” said ALM Chairman Jim Mangini, RLLD. “But, her strategic mindset and results-driven approach earned her this promotion to president and CEO. Behind Sarah’s drive, the association is now positioned for unparalleled growth and enhanced member value.”
“I have set ambitious goals for enhancing the value to all members and ensuring the next generation of leaders are well-equipped for success” said Brobeck. “I’m honored to have the Board’s support behind me as we continue to grow ALM.”
Brady and Remillong Join Board, Malboeuf Takes Helm
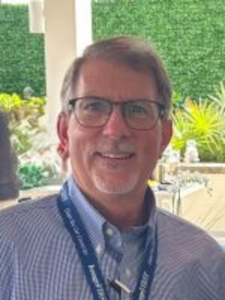
The Association for Linen Management (ALM) announced new Board leadership as Chip Malboeuf, Vice President Operations and Engineering at ImageFIRST assumes role as Chairman of the Board, Liz Remillong, Vice President of Business Development at Core Linen Service was elected as Vice Chair, and Tiffany Brady, Director of Customer Relations and Logistics at West Michigan Shared Hospital Laundry was elected as a Director. Chris Christie, CLLM, MHLM, System Linen Manager at Ascension Health was also re-elected as a director.
With ALM’s aggressive strategic plan and rapid growth, these leaders assume their role in a defining moment for the association.
“Under Chip’s leadership and with the addition of Liz and Tiffany, I couldn’t be more excited about ALM’s direction. Visionary leaders like them are what propels ALM to become even more vital in the textile care services landscape as the premier resource for education and networking,” said ALM Executive Director, Sarah Brobeck.
“I am deeply honored to ascend to the role of Chairman of the ALM Board of Directors,” said Malboeuf. “Building upon the remarkable momentum of the Board of Directors and the ALM staff, I am committed to advancing our mission and continuing to grow the educational opportunities we offer. Together, we will strive to help provide leadership development and industry expertise, ensuring ALM continues to be a beacon of learning and development for all.”
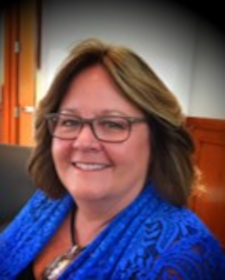
“I am so honored to be able to serve the members of ALM. I am excited to work with Chip and the board on all the fantastic initiatives Sarah and her team have been working on,” shared Remillong. “It’s a great time to be part of a wonderful organization and am looking forward to all the future offerings ALM will bring to the industry!”
The ALM Board of Directors provides the association with oversight, policy making and long-term strategy. The new board positions were elected by the membership and announced at the June 11 virtual membership meeting.
For more information about ALM, visit the website.
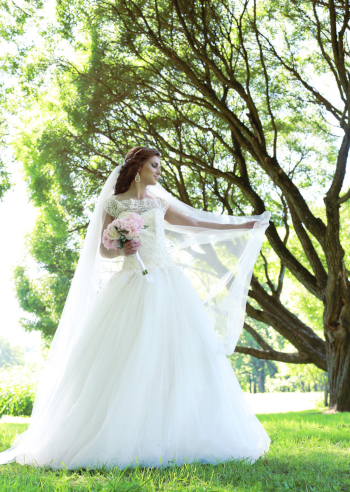
Preserve a Gown, Plant a Tree
Association of Wedding Gown Specialists joins forces with Arbor Day Foundation.
The Association of Wedding Gown Specialists (AWGS) announced that wedding couples can now ensure the beauty of their gowns and help safeguard the planet’s beauty, too.
AWGS has established a ReforestationFund (TM) and will help provide support to the Arbor Day Foundation, to help make a positive impact and celebrate a couple’s wedding by planting a tree for every gown its members preserve. Trees will be planted in a forest of great need. Founded in 1972, the Arbor Day Foundation is the world’s largest member nonprofit dedicated to planting trees. Together with their members, partners, and programs, they have helped plant more than 500 million trees in neighborhoods, communities, cities, and forests throughout the world.
AWGS is proud of its long-time eco-friendly commitment. President Kyle Matthews of Janet Davis Cleaners in Berkley, Michigan, noted, “Our Association was the first to try to calculate the carbon footprint of cleaning and preserving the wedding gown, from travel to and from one of our members, to the cleaning of the gown, and the manufacture of the wedding chest to preserve the gown. In 2009 we began funding reforestation projects worldwide, and our MuseumCareTM preservations are unique with regard to our commitment to the environment.”
Established in 1987, AWGS, a not-for-profit trade association with members in nine countries, is a network of cleaners who specialize in the meticulous care of wedding gowns, specialty garments, and other fine fabrics. Members share a common vision: to elevate their brands and become the trusted dry cleaners in their respective communities. Members also understand the unique challenges and opportunities that come with handling delicate and cherished items such as wedding gowns and other luxury garments and cherished heirlooms. The Association’s mission is to empower members with the knowledge, resources, and support needed to excel in this specialized field. However, the preservation guarantee is truly an international warranty because each member honors the guarantee of every other member no matter where in the world they may be.
The organization’s trademarked MuseumCareTM preservations are endorsed by the Association of Bridal Consultants (the professional organization dedicated to wedding planners and professionals worldwide) and are also recommended by many designers and manufacturers.
For more information about training and membership, go to www.WeddingGownSpecialists.com or to www.WeddingGownSpecialists.net.au or call the office at 800-5001-5005 or 203-415-4079.
Preparing for PFAs in Commercial Real Estate
EnviroForensics Explains PFAs — and why they matter
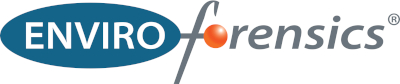
You may (or may not) have heard of PFAs (per- and polyfluoroalkyl substances) and the recent U.S. EPA announcement designating two PFAs compounds as hazardous substances. There’s been a lot of doom and gloom posted about PFAs recently and while their hazardous substance designation will have effects that trickle down to commercial real estate, all is not lost. Below is a quick summary of what PFAS are and some immediate effects you may see in commercial real estate beginning July 8, 2024, when two common PFAs compounds officially become hazardous substances.
WHAT ARE PFAs ?
PFAs are a group of 9,000+ chemicals developed in the 1930s used in water-resistant textiles, paper products, non-stick coatings, and cleaning products. They are found in items like shampoo, cosmetics, non-stick cookware, stain-resistant or waterproofing products, fast food packaging, paints, and pesticides. Biosolids from sewer treatment plants, used as fertilizer, and aqueous film-forming foam (AFFF) used for fire suppression, can also contain PFAs . Electronic manufacturing and electroplating operations use PFAs too.
PFAs breaks down slowly in the environment, easily travel through groundwater, and can bioaccumulate in humans and animals. Research links PFAs exposure to health concerns in humans and animals.
REAL ESTATE IMPLICATIONS
Until recently, PFAs were regarded as emerging contaminants and were not officially listed as CERCLA hazardous substances. Two (2) common PFAs compounds (known as PFOA and PFOS) will become CERCLA hazardous substances on July 8, 2024. Below are four ways the hazardous substance designation of these PFAs compounds may affect commercial real estate transactions going forward.
- Environmental screening levels for PFAs are very low and PFAs may be found at lots of properties. Studies have shown that PFAs can cause issues at very low levels in the environment; for example, common petroleum compounds are assessed at a part-per-billion (ppb) level; PFAs compounds are assessed at a part-per-trillion (ppt) level, a thousand times lower. PFAs do not easily breakdown and can readily travel when they encounter groundwater. PFAs may be present at many properties, even if the historical or current operations may not have directly used PFAs . Types of businesses that may have PFAs impacts includes, but is not limited to laundromats, car washes, dry cleaners, airports, firefighting training facilities, electronic manufacturers, oil refineries, plastic and paper mills, landfills, metal platers, and any business where non-stick or waterproofing applications are applied.
- PFAs will now be a consideration in Phase I ESAs. Historically, PFAs were considered out-of-scope items for Phase I ESAs, as the ASTM standard only calls for assessing CERCLA hazardous substances and petroleum products. Beginning July 8, 2024, the PFAs compounds PFOA and PFOS will need to be assessed during Phase I ESAs.
- A current Phase I ESA may identify PFAs as an environmental concern at properties where historical Phase Is may have not identified environmental concerns. PFAs were used in many processes and operations that were previously not considered issues. For example, laundromats (with no dry cleaning operations) and farm fields may have environmental concerns due to PFAs , whereas they may not have had issues previously. Other facilities, such as dry cleaners or electroplating operations, may have identified environmental concerns in their past Phase I and Phase II ESAs, but those historical reports likely did not address PFAs .
- Cost for environmental sampling (i.e., Phase II ESAs) may increase. PFAs sampling techniques can require increased time and stringent procedures to ensure cross-contamination will not occur. Laboratories will also need to analyze PFAs samples at extremely low levels, which will likely increase analytical costs. For example, analysis of groundwater for dry cleaning compounds is roughly $80 – $100 per sample. Current groundwater analytical costs for a PFAs sample can start in the high $300s and go up from there.
The bottom line is that the impending designation of PFAs as a hazardous substance may have far-reaching effects in the environmental world; however, this does not mean the sky is falling. Property owners and prospective purchasers should be aware of these upcoming regulations and a trusted environmental consultant can help guide you through the next steps.
EnviroForensics helps business owners through environmental investigations and cleanup, often while business goes on as usual. EnviroForensics may be able to help find historical insurance to fund the investigation or connect you with third parties who can manage environmental liabilities for property owners or even purchase contaminated properties. For more information, visit the website.
TRSA Announces Buik to Receive Operator Lifetime Achievement Award
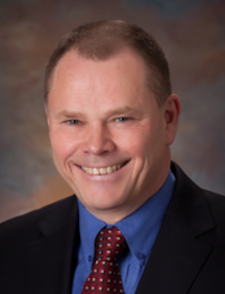
James Buik, president and owner of the Roscoe Co., Chicago, will be honored at the 111th TRSA Annual Conference & Exchange in September with the TRSA Operator Lifetime Achievement Award.
The award pays tribute to exceptional personal service to TRSA and the industry as nominated by past linen, uniform and facility services operator award peers and voted on by the TRSA Executive Committee. Winners have supported the association for decades, devoting their own time to association activities and facilitating their employees’ involvement in TRSA. Their teams have taken advantage of a wide range of TRSA activities, including certification, in-person and virtual events, and benchmarking surveys.
Buik has been recognized for engagement in and personal leadership of TRSA and the Uniform and Textile Service Association (UTSA), which served the industry for 75 years and blended with TRSA in 2009. For TRSA, he was chair (2018–’20) and a member of the Executive Committee (2014–’22) and Board of Directors (2012–’14). For UTSA, he was chair (2005–’06) and executive (2003–’08) and a board member (1993–’95).
“I am humbled to be included on a prestigious list of previous award winners, to include my father Donald, and many industry friends and colleagues,” Buik said. “I have so many to thank, but especially my wife Teresa, who has supported and encouraged me throughout the journey.”
His dedication to furthering the industry’s best interests has been reflected in other volunteer leadership positions, as he currently chairs TRSA’s Environmental Committee and serves on the Government Relations Committee. He previously chaired the Strategic Planning Committee and was a member of the TRSA Education and UTSA Marketing Committees.
“Jim’s leadership reflects a belief we share that when any operator makes a good impression on their customers, it serves us all well,” said Jim Kearns, current TRSA board chair and COO, Alsco Uniforms, Salt Lake City. “The more you get to know him, the more you realize he really does have the industry’s best interests at heart.”
In recent years, Buik has empowered Roscoe staff to serve on four other TRSA committees, facilitated extensive Roscoe staff participation in TRSA professional-development events and led the company in earning Clean Green and Hygienically Clean Food Safety certifications.
TRSA President and CEO Joseph Ricci commended Buik’s hospitality to TRSA groups seeking to visit Roscoe during professional-development events such as the Production Summit and Plant Tours, Maintenance Management Institute and Next-Generation Executives Roundtable. “Jim has upheld TRSA members’ longstanding tradition to welcome industry colleagues to view their teams and machinery at work,” Ricci said. “Roscoe’s company motto is ‘Take Pride.’ Jim and the Roscoe staff enjoy these opportunities to demonstrate their performance excellence. They realize the benefits of hosting a plant tour, including building teamwork and boosting morale by putting a local team on a national stage.”
The award presentation will take place during a Sept. 26 dinner at the TRSA Annual Conference & Exchange, Sept. 24-26, at The Broadmoor in Colorado Springs, CO. At the event, Buik will join 38 past recipients who have received the award since its 1982 inception.
MAY 2024 NEWS
TRSA Annual HR, Health, and Safety Summit Empowers Professionals
Textile Rental Services Association (TRSA) recently concluded its annual HR, Health, and Safety Summit in Milwaukee. Professionals from both human resources and health and safety fields gathered for a day of intensive professional development, aimed at enhancing their skills and knowledge. The event featured educational sessions tailored to each field.
Mental Health and Workplace Well-Being
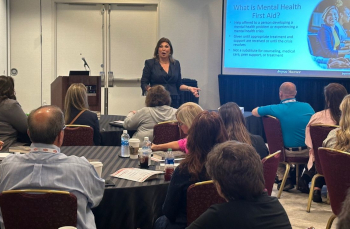
The summit kicked off with a welcome session led by Joyce Marter, mental health thought leader and author of The Financial Mindset Fix. Marter conducted a “mental triage” for the workplace, emphasizing the benefits of positive mental health practices. Attendees learned how fostering a supportive environment positively impacts retention, productivity and overall morale. Practical tools and resources were provided to address mental health challenges, ultimately reducing accidents, injuries and healthcare costs. Attendees also received complimentary copies of Marter’s book.
Will Maness of Alsco Uniforms commented that all the material presented in the keynote was extremely applicable to their day-to-day operations. He added, “It was a great mixture of material presented, as well as the opportunity for group discussion.”
HR Track: Legal Updates and Employee Retention
In the HR track, Jason Keck, partner at Fisher Phillips, discussed critical updates to HR laws for 2024. Attendees gained insights into legal best practices to mitigate workplace risks. Katie Cosgrove, partner at Cosgrove Partners, focused on retaining and developing employees, addressing generational gaps and cultural challenges. Kortney Overzet, VP of people development and culture at Spindle, shared strategies for employee retention, including recognition programs and the innovative “Work Human” platform. Lori Stanger, VP of people and culture at Wildman Benefit Group, emphasized aligning rewards with company values and cost-efficient program design.
Safety and Health Sessions: Mitigating Risks
Safety and health professionals attended breakout sessions, starting with Charlie Edelman, corporate safety director at Unitex Healthcare Laundry Services Inc. Edelman emphasized safety culture, risk assessments, and open communication to mitigate workplace risks. Colin Giles, regional safety manager at Unitex, joined Edelman on stage. A panel discussion on chemical safety essentials followed. Cintas executives Stephen Jenkins (Director of Health and Safety) and Sydney Kelley (Ergonomics Engineer) engaged the audience in an interactive session on safe ergonomic practices and laundry cart selection. Brian Varner, owner of Safety Solutions for Healthcare, delivered insights on creating and using safety KPI dashboards.
Maness stated, “The summit was a great opportunity to learn about different metrics and dashboards to adequately report and improve safety.”
AI Solutions for Production Ergonomics
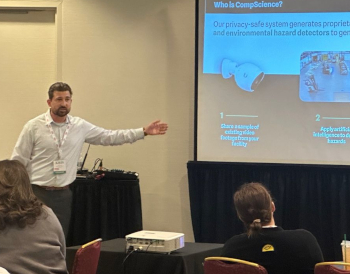
The summit concluded with two general sessions. Kriz Mizen, head of loss control at CompScience, explored AI solutions for production ergonomics. Mizen highlighted how AI supports employees by providing real-time feedback, guidance, and skill enhancement. Attendees learned best practices for leveraging AI in production ergonomics as well as the benefits and challenges of AI implementation.
In the final session, Samlane Ketevong, the senior director of certification and accreditation at TRSA; and Varner debuted their plan for a new and improved certification for Safety and Health.
TCATA Holds Successful Annual Management and Educational Conference
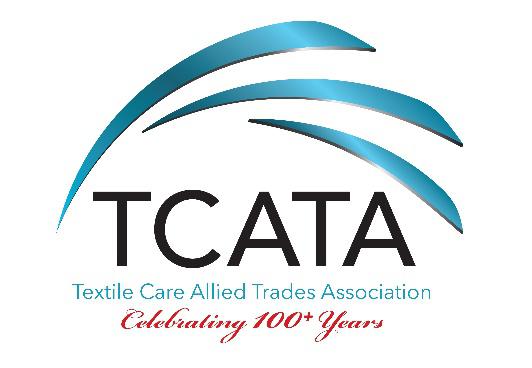
The Textile Care Allied Trades Association (TCATA) announced the success of its 2024 Annual Management and Educational Conference. Held April 28 – May 1 at The Omni Barton Creek in Austin, TX, this year’s conference brought together industry leaders for a dynamic exchange of ideas and insights.
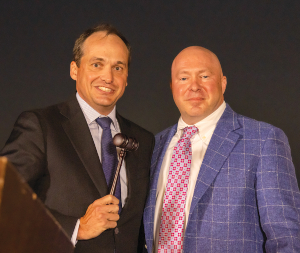
During the conference, TCATA President John Silverman installed Mack Magnus of M & B Hangers as its new President, marking a new chapter of leadership under his guidance. Mack, President of M & B Hangers, has served as TCATA Conference Chair as well as Vice President on the Board of Directors representing supply manufacturers.
TCATA also introduced its newest board members. Terry Hammond of UNX Christeyns, Jack Heaviside of Sunburst Chemicals, Justin Shamion of Colmac Industries, Wes Nelson of Sankosha, and Robb Vacek of Horwath Laundry Equipment, are poised to contribute to the association’s mission of advancing the textile care industry.
TCATA celebrated the anniversaries of longstanding members recognizing A-1 Products of Birmingham, AL, and Tschopp Supply of Buffalo, NY, for their 50 years of membership, as well as honoring M & B Hangers of Birmingham, AL for an incredible 75 years of membership.
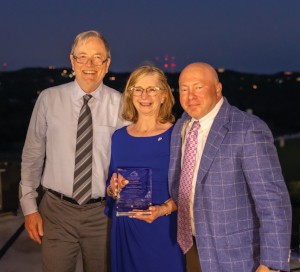
Highlighting the spirit of leadership and collaboration within the TCATA community, the inaugural Leslie Schaeffer Member-Driven Award was presented to Leslie Schaeffer, TCATA CEO, acknowledging her outstanding contributions and commitment to the association’s member driven mission.
TCATA is excited to announce that the 2025 Annual Management and Educational Conference will take place at the Ritz Carlton Tiburon in Naples, FL, April 27 – 30.
For more information about TCATA and upcoming events, please visit www.tcata.org.
DLI Spring Graduates, Upcoming Classes
The Drycleaning & Laundry Institute’s (DLI) School of Drycleaning Technology trained 22 students in its 385th General Drycleaning Course, composed of the five-day Introduction to Drycleaning Course, March 4 – 8 and ten-day Advanced Drycleaning Course, March 11 – 22.
Founded in 1927, DLI’s School of Drycleaning Technology has helped shape the careers of thousands of drycleaners worldwide. In these courses, students learned about:
- Sorting loads for drycleaning
- The science of drycleaning
- Fibers and their characteristics
- Fabric construction
- Cleaning silk, stain, and other fabrics
- Soil and cleaning theory
- Operating a drycleaning machine
- Stain removal chemistry and procedures
- Removing coffee, ink, grease, and other stains from clothing
- Pressing pants, coats, blouses, ties, pleated garments, and skirts
- Using tensioning equipment to improve finishing quality
- Using bleaches without damaging fabric color
- Distillation procedures
- Understanding the differences between solvent types
Upcoming 2024 DLI Courses
- Virtual Stain Removal Course: July 9 – 30
- Virtual & In-Person West Coast Stain Removal Couse: July 24 – August 7
- Virtual Stain Removal Course: September 10 – October 1
- On-Site Introduction to Drycleaning: October 7 – 11
- On-Site Advanced Drycleaning: October 14 – 25
- Combined Introduction & Advanced Courses: October 7 – 25
Prospective students are invited to learn more and register at www.DLIonline.org/Education or contact Melissa Wagner at 800-638-2627.
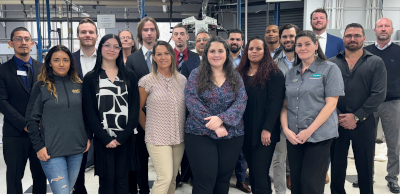
DLI’s 385th Introduction to Drycleaning
Front row (left to right): Alisson Guamba, Zips Dry Cleaners, Columbia, MD; Jolene Law, Sierra Cleaners, Belen, NM; Haven Law, Sierra Cleaners, Belen, NM; Alana Siuda, Gibson’s Cleaners, Toronto, ON; Serena Lane, Gold Star Cleaners, Brewer, ME; Kayla Hughes, Puritan Cleaners, Richmond, VA.
Middle row (l-r): John Garza, Lavaseco Universal, San Antonio, TX; Lundy Burns, Crazy Cleanerz, Memphis, TN; David Starr, Kraft Cleaners, San Antonio, TX; Sukhjiwan “Jay” Singh, Lapels Cleaners, Cary, NC; Pete Everest, Rick’s Cleaners, Austin, TX; Aaron Vassallo, My Butler Service, Thornleigh, New South Wales, Australia.
Back row (l-r): Donna Wagner, Glyndon Lord Baltimore Cleaners; John Saviano, Gold Star Cleaners, Brewer, ME; Boston Chauthani, Polo Cleaners, San Juan Capostrano, CA; Gerrayl Bryson, Tiffany Couture Cleaners, Las Vegas, NV; Mark Harris, Oceanside Cleaners, Jacksonville, FL; Phillip Wedel, Neighborhood Cleaners, Eatonton, GA. (Not Pictured: Sheikh Hossain, TinyBubbles III, Inc., Grand Prairie, TX.)
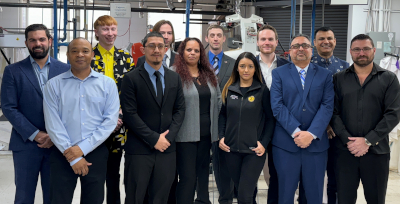
DLI’s 385th Advanced Drycleaning Course
Front row (left to right): Brian Johnson, DLI Director of Education & Analysis; John Garza, Lavaseco Universal, San Antonio, TX; Alisson Guamba, Zips Dry Cleaners, Columbia, MD; Sukhjiwan “Jay” Singh, Lapels Cleaners, Cary, NC; Aaron Vassallo, My Butler Service, Thornleigh, New South Wales; Australia.
Back row (l-r): Boston Chauthani, Polo Cleaners, San Juan Capostrano, CA; Kyle Nye, Brio Cleaners, Bellingham, WA; David Starr, Kraft Cleaners, San Antonio, TX; John Saviano, Gold Star Cleaners, Brewer, ME; Lundy Burns, Crazy Cleanerz, Memphis, TN; Sheikh Hossain, TinyBubbles III, Inc., Grand Prairie, TX.
Scholarship Students: Alana Siuda, Gibson’s Cleaners, Toronto, ON; John Garza, Lavaseco Universal LTDA, San Antonio, TX; Boston Chauthani, Polo Cleaners, San Juan Capostrano, CA; John Saviano, Gold Star Cleaners, Brewer, ME; Lundy Burns, Crazy Cleanerz, Memphis, TN.
TRSA Hosts Successful Midwest Summit and Plant Tour
The Textile Rental Services Association held its second Regional Production Summit and Plant Tour event on May 1-2 in Milwaukee. Held in collaboration with the Wisconsin Association of Textile Services (WATS), the summit aimed to enhance quality programs and accessibility for all members by bringing them together at a central location within their region.
Keynote Sessions and Presentations
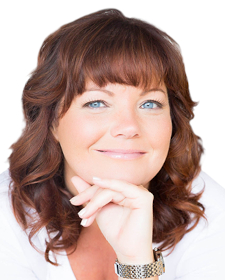
The Midwest Summit commenced with an engaging keynote session by Nancy Roberts, CEO and founder of The DISC Wizard. Roberts delved into the concept of emotional intelligence (EQ), highlighting the five traits of emotionally intelligent individuals. Attendees gained valuable insights on how to apply EQ knowledge to become more effective leaders. Roberts also incorporated audience EQ evaluations into her presentation, ensuring a tailored experience.
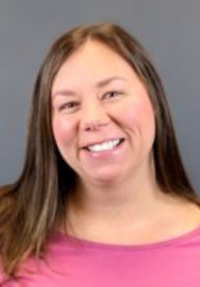
Jessica Leigh, customer success manager at Spindle, followed with a focus on production managers’ roles in preventative maintenance. Attendees learned strategies to optimize labor and energy costs by scheduling preventive maintenance during regular working hours. Real-world examples underscored the importance of proactive maintenance practices. Leigh emphasized the significance of scheduled meetings between production and maintenance staff for organizational efficiency and safety.
Don Bock, an industry consultant, delivered a comprehensive presentation on “Fire Safety – Strategies for Prevention.” Bock covered common sources of fire in laundries and provided best practices to prevent such incidents. He also discussed various fire suppression systems applicable to laundry facilities.
Leadership Skills and Process Improvement
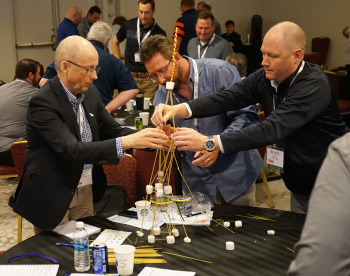
Christopher Stammer, CEO of Volu Interactive, challenged attendees to reflect on their leadership styles. Drawing from his experience as a United States Coast Guard licensed Master Captain, Stammer shared real-world scenarios where captains’ decisions impacted outcomes. An interactive exercise highlighted collaboration and decision-making as essential leadership skills.
Keith Ware, another industry consultant, explored process improvement and root-cause analysis. Ware emphasized thinking outside the box and fostering collaborative teams. Attendees participated in a creative challenge, building structures from marshmallows, dry spaghetti, and pipe cleaners. Facilitated roundtables further encouraged discussions on EQ, leadership development, and safety.
Panel Discussion and Plant Tours
The summit’s first day concluded with a dynamic panel discussion featuring Doug Roskopf (ITU AbsorbTech Inc.), Chris Gibson (UniFirst Corp.), and Andrew Leonard (Gunderson Group). Ken Koepper, TRSA’s director of membership and industry relations, moderated the panel.
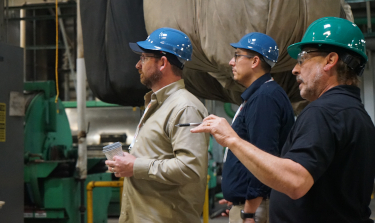
On May 2, Alsco Uniforms and Superior Health Linens graciously opened their local facilities for guided tours, providing attendees with a tour of their facilities.
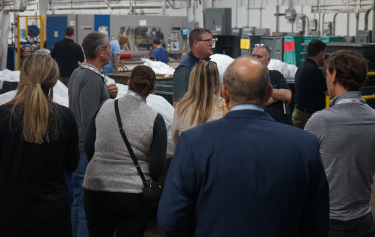
First-time attendee Chris Milum, plant manager at Spotless Uniform in British Columbia, found the information and technology shared very useful. He added, “I look forward to taking much back to implement in my plant.”
The third program in this series will be held on Oct. 15-16, in Newark, NJ, for members in the Northeast region. Click here to learn more about the Northeast Summit.
Methods for Management meets in Winnipeg
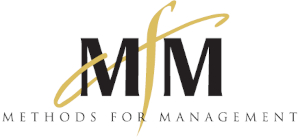
Methods for Management (MfM), a leader in providing strategic guidance to the dry cleaning industry, held a successful meeting of its Canadian Bureau. Hosted by Lisa Loscerbo and Kevin Hiebert of Best Care Dry Cleaners, the event took place at the Inn at The Forks in Winnipeg, Manitoba, on April 17-18, 2024. This assembly was two days of industry collaboration and innovation among top-tier Canadian dry cleaning professionals.
A Day of Insight and Industry Advancement
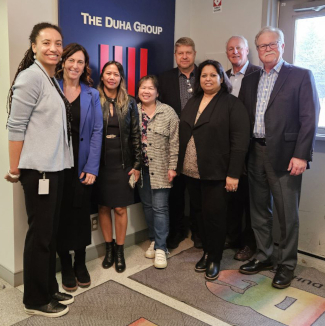
The meeting commenced with a working breakfast on Wednesday, setting the tone for a day filled with insightful activities and industry engagement. The highlight was a planned field trip to The Duha Group, a global pioneer in color marketing solutions. Kermit Engh, Managing Partner of Methods for Management, reflected on the visit: “This was a fascinating field trip to the Duha Group, a worldwide company that produces designer paint samples used by paint stores and interior designers. An integral part of this company is its long-standing continuous improvement culture.”
Participants explored Duha’s innovative approaches to color strategy, mass reproduction, and system management. The tour showcased the company’s commitment to cultural excellence and continuous improvement, providing participants with a firsthand look at effective communication and standardization through visual systems.
Best Care Dry Cleaners Plant Tour and Peer Review
Later in the day, attendees visited the Best Care Dry Cleaners plant, engaging in a constructive critique session. This visit allowed members to exchange ideas and insights, fostering a collaborative environment to discuss advancements and innovations. The session concluded with a delightful dinner hosted by Lisa Loscerbo, providing a perfect setting for relaxed yet productive networking.
Lisa Loscerbo shared her thoughts: “Our recent MfM collaborative gathering served as a platform for sharing knowledge, discussing emerging trends, and brainstorming innovative solutions to common challenges faced by our industry.”
Strategic Discussions and Knowledge Exchange
Thursday was dedicated entirely to strategic discussions and knowledge exchange. The day started with a working breakfast and was intensive, focusing on individual plant issues, sales trends, and financial health. Members shared their ‘Best Ideas’ from the last quarter, reviewing successes and learning points, which spurred discussions on marketing strategies and technological advancements in equipment.
Lisa Loscerbo, reflecting on the outcomes, stated: “As CEO of Best Care Dry Cleaners, I am proud to have participated in this exchange of ideas. Some of the key takeaways from the meeting were the significance of leveraging technology to streamline processes and enhance the customer experience. By staying informed of the latest advancements in garment care technology, we can ensure that our services are efficient, convenient, and tailored to meet the evolving needs of our clients. At Best Care Dry Cleaners, we are committed to continuous improvement and exceeding our customers’ expectations. The insights gained from this meeting will inform our strategic initiatives as we strive to uphold our reputation as the preferred choice for discerning individuals who demand the best for their garments.”
Nadine Rana of Style & Grace Cleaners added, “As MfM members, we build on each other’s success among our peer groups and within the dry cleaning industry. After attending the recent bureau meeting hosted by ‘Best Care Cleaners’ in Winnipeg, we left completely inspired and motivated to embrace continuous improvements in our business. Not only did we have huge takeaways from our peer group but beyond in recent insights gained in a completely different industry sector with ‘The Duha Group’ and how their leadership team has embraced ‘The Kaizen philosophy’.”
Continuing the Legacy of Excellence
The second quarter meeting of the Methods for Management’s Canadian Bureau not only reinforced the importance of collaborative learning and innovation in the dry cleaning industry but also highlighted the crucial role of strategic leadership in adapting to changing market dynamics. As the industry evolves, MfM remains at the forefront, facilitating peer groups that propel the dry cleaners toward greater efficiency and success.
For more information on Methods for Management and upcoming meetings, please contact Vikki Reed at vreed@mfmi.com.
Acquisition of Shortridge expands K-Bro’s geographic footprint in the UK
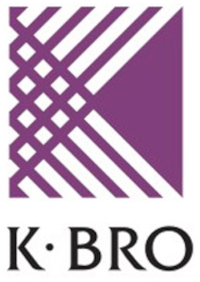
K-Bro Linen Inc. (“K-Bro” or the “Corporation”) (TSX: KBL) announces the acquisition of Shortridge Ltd. (“Shortridge”), a high-quality hospitality laundry provider based in the North West of England, expanding K-Bro’s geographic footprint in the £1.4 billion UK commercial laundry and textile rental market. K-Bro also owns Fishers Laundry Group (“Fishers”), the commercial laundry and textile rental provider covering Scotland and the North East of England, which it acquired in 2017.
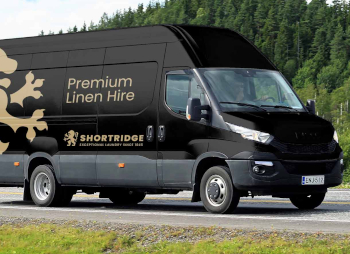
Shortridge is being acquired for consideration of £24.1 million (approximately C$41.2 million), on a cash-free, debt free basis (subject to customary conditions, including certain escrows) and with a further potential earn-out of £2.0 million (approximately C$3.4 million) for achieving certain targets for the 12 months through September 2024. Shortridge’s last twelve months’ revenue for the period ended March 31, 2024 was approximately £12.5 million (approximately C$21.4 million). The transaction includes the freehold and leasehold real estate for Shortridge’s laundry processing facilities. The acquisition is being funded entirely from K-Bro’s recently increased syndicated debt facility and is expected to be accretive to the Corporation.
Shortridge is headquartered in North West England, with laundry processing sites in Lillyhall and Dumfries and a distribution centre in Darlington. Shortridge is a long-established and respected laundry company and K-Bro plans to retain its branding. Its experienced management team will remain with the business and K-Bro intends to retain Shortridge’s employees across its three sites.
Linda McCurdy, President and Chief Executive Officer of K-Bro, said, “While our original plans to grow our presence in the UK were interrupted by the Covid pandemic, we have stayed on the alert for further growth opportunities in the UK, and I am excited by the potential that this acquisition presents for us and for Shortridge’s customers. We share the same values as Shortridge, so the cultural fit is strong and the business has found a good home as part of the K-Bro family.
“This is a great opportunity for us to diversify our customer base in the UK and to position our combined UK business for more growth as we look to extend K-Bro’s geographic reach further south into the UK.”
Peter Semple, Shortridge Business Director, said, “This is a good news story for Shortridge and our customers as we join the K-Bro family with the resources and the vision to help us grow the business further while continuing to look after the interests of our valued customer base. K-Bro’s experience, coupled with Fishers’ strong reputation and track record here in the UK, make for a formidable team and we can look forward to an exciting future together.”
Transaction Highlights
- High-Quality Operator: Shortridge is a prestigious commercial laundry operator with a reputation for serving the needs of its customers well and represents the addition of a second, highly recognizable local brand in the UK for K-Bro.
- Adjacent Geographic Footprint: Two strategically located processing facilities and one distribution depot expand K-Bro’s geographic footprint into the North West of England.
- Highly Diversified Customer Base: Shortridge services over 1,200 hospitality customers, including many local, independent businesses, with no customer representing more than 3% of revenue.
- Experienced Management and Shared Values: The experienced management team at Shortridge has significant industry experience and both K-Bro and Shortridge have shared values in ‘putting people first’, prioritizing customers, employees and all stakeholders.
- Well Positioned for Growth: Shortridge has attractive organic growth opportunities and K-Bro’s vision includes supporting both existing and new customers. The acquisition creates a foundation to extend both Shortridge’s and Fishers’ services further south into the UK while remaining vigilant for further acquisitive growth opportunities elsewhere in the UK.
Transaction Financing
The acquisition is being funded entirely from K-Bro’s credit facility. K-Bro is committed to maintaining a flexible capital structure to support future acquisition and organic growth.
Legal Counsel
Burness Paull LLP and Stikeman Elliott LLP are acting as legal advisors to K-Bro.
About K-Bro
K-Bro is the largest owner and operator of laundry and linen processing facilities in Canada. K-Bro provides a comprehensive range of general linen and operating room linen processing, management and distribution services to healthcare institutions, hotels and other commercial accounts.
K-Bro currently operates ten processing facilities and two distribution centres under two distinctive brands, including K-Bro Linen Systems Inc. and Buanderie HMR, in ten Canadian cities: Québec City, Montréal, Toronto, Regina, Saskatoon, Prince Albert, Edmonton, Calgary, Vancouver and Victoria.
About Shortridge
Since the early 1990’s, Shortridge has operated as a family run laundry business, based in Cumbria, with plants in Lillyhall, Dumfries and a distribution depot in Darlington.
It specialises in providing high quality laundry services to local independent hospitality businesses, including hotels, B&Bs, self-catering units and restaurants.
About Fishers
Fishers was established in 1900 and remained family owned up to 2003. Acquired by K-Bro in 2017 the company has invested significantly in its large, highly automated, laundries to become the leading laundry provider to large hotel chains operating in Scotland and North East of England.
The company has also pioneered the use of RFID technology with its own luxury linen brand to create a bespoke offering to some of Scotland’s most prestigious hotels and venues.
The company operates five sites in Scotland and the North East of England:
- Cupar – Prestonhall
- Perth
- Newcastle upon Tyne
- Livingston
Coatbridge
APRIL 2024 NEWS
Jensen USA launches fleet of regional service vans
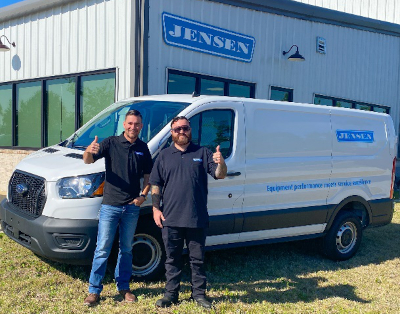
As the first service van departed from the Jensen USA factory last week, it was not only on its way to fulfill a service call—it also fulfills Jensen’s latest commitment to elevate its service by introducing a stronger regional presence within key parts of North America.
“The goal is to bring us even closer to our customers,” explains Tony Biela, the President of Jensen USA. “We have launched a new spare parts website and phone app, making spare parts easier to purchase. We stock over 4,700 spare parts locally, for the shortest possible delivery times. And now, we have several new regional service engineers along with a new fleet of service vehicles. At Jensen USA, service excellence is as much a part of our commitment to customers as our equipment performance.”
Emblazoned on each van is the phrase “Equipment performance meets service excellence”. Jensen says its solutions have a reputation for the highest performance in the market, and with the latest improvements to service excellence, Jensen they hope to help their customers maximize the performance and uptime of their Jensen solutions.
Greater accessibility is becoming more and more important to customers, which Tommy Kallgren, the VP of Spares and Service, explained. “Having a regional service technician allows us to respond more quickly to customer needs—plus it gives our customers more flexibility when scheduling regular maintenance packages. In some regions, it is possible to schedule shorter yet more frequent preventative maintenance visits.”
The van’s inaugural trip was to Central Florida, after which it will continue to drive around the southeast region making service calls. By the end of the year, Jensen plans to operate at least five such regional service vans, with more plans for expansion in 2025. Each van will specialize in the customers of a specific region.
TRSA Annual Awards
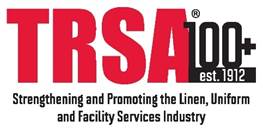
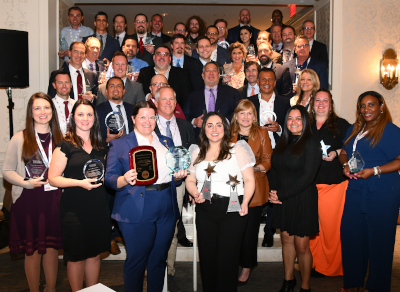
On April 10, individuals and companies were honored by their peers for outstanding achievements in specialized categories related to their digital, safety, educational, inclusionary and operational pursuits. In total 11 award categories were presented to 60 member companies and individuals, each of whom had received nominations from their peers or customers. The awards were distributed during TRSA’s Industry Awards Dinner at the association’s 14th Annual Legislative Conference in Washington, DC.
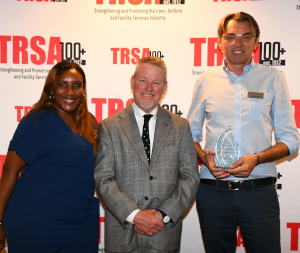
NOVO Health Services’ Miami facility took top honors with the TRSA Plant of the Year award. This honor recognizes industry-leading facilities for their comprehensive efforts to improve their expertise in supplying, laundering and maintaining linens and uniforms. Winners of this award describe how they achieve goals and surmount obstacles. They cited statistical results across a wide range of indicators from environmental stewardship to productivity improvement in order to document their expertise in a range of areas.
Novo Health Services was honored for its achievements in improved efficiency, as well as its excellent record in infection control, safety and ergonomics best practices. These combined efforts help to create a work environment that promotes employee retention. Opened in 2022 following a $25-million investment, the 80,000-square-foot NOVO Miami plant has 186 employees and runs two shifts, six days a week.
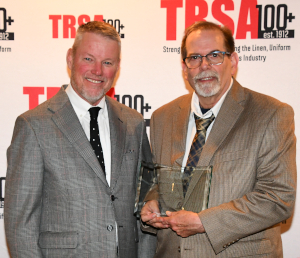
Charles Edelman, Unitex Healthcare Laundry Services, Elmsford, NY, received the Volunteer Leadership Award. Edelman, Unitex’s corporate safety director, chairs TRSA’s Safety Committee. He’s been a steadfast contributor to TRSA education programs as a speaker and organizer, including the Maintenance Management Institute and the HR, Health & Safety Summit.
The TRSA Industry Awards Dinner is an annual event. It’s never too early to begin working toward earning one or more honors at the next program. Members are encouraged to visit the awards page on TRSA’s website to learn more about the individual awards and how they can nominate candidates for next year. Click here for details.
THE AWARD WINNERS
Above & Beyond Service
Honoring exceptional attention to customer needs by individuals and organizations, setting a high standard for others to follow, as selected by industry peers.
GOLD
- Alliant Systems | Irving, TX
- Foltex USA | Columbia, SC
- Joe Chernot | Foltex USA
- Chris Williams | Foltex USA
- Preston McElheney | Halifax Linen Service
- Rhonda Benna | Virginia Linen Service
SILVER
- Scott Rotkowski | ABS Laundry Business Solutions
- Linen Master | Vero Beach, FL
HONORABLE MENTION
- Brian Anderson | ABS Laundry Business Solutions
- Patrick Brown | ABS Laundry Business Solutions
- Fred Kolenda | Ecolab Textile Care
- Scott Delin | Fashion Seal Healthcare
- Chris Northcutt | Foltex USA
- Karineh Minissian | Norchem Corp.
- Customer Service Representatives | Standard Textile
Best Plant to The Year
Honoring achievements, surmounting obstacles and citation of statistical results across a wide range of indicators of improved capabilities, from environmental stewardship to productivity gains.
- NOVO Health Services | Miami, FL
Best Video – Operators
Honoring creativity and messaging in video, whether purely informative (showcasing employees, products or services) or technical (describing capabilities, processes or training).
GOLD
- Ecotex Healthcare Linen Services | Abbottsford, BC
- HLS Linen Services | Ottawa, ON
- Plymate, Inc | Shelbyville, IN
- UniFirst Corp. | Wilmington, MA
- Unitex Healthcare Laundry Services | Elmsford, NY
HONORABLE MENTION
- APPI Energy | Salisbury, MD
- Kurt and Wendy Vander Meer | Continental Linen Services (CLS)
- ImageFIRST Healthcare Laundry Specialists | King of Prussia, PA
Best Video – Supplier Partner
GOLD
- Norchem Corp. | Los Angeles, CA
SILVER
- Norchem Corp. | Los Angeles, CA
- REED Manufacturing | Tupelo, MS
HONORABLE MENTION
- Tingue | Peachtree City, GA
Clean Green Innovation
Honoring leadership in reducing environmental impact, aligned with best management practices
of the TRSA Clean Green standard, as selected by industry peers.
GOLD
- Diamond Chemical Co. | East Rutherford, NJ.
SILVER
- Ecolab Textile Care Division | St. Paul, MN
- ImageFIRST Healthcare Laundry Specialists | King of Prussia, PA
Company Community Service
Honoring significant contributions to communities by organizations, reflecting their care for and
sense of responsibility to the public. Industry peers select winners.
GOLD
- City Uniforms and Linen | Findlay, OH
- Unitex Healthcare Laundry Services | Elmsford, NY
- Robert Potack | Unitex Healthcare Laundry Services
SILVER
- Balfurd Linen & Uniform Service | Tipton, PA
HONORABLE MENTION
- APPI Energy | Salisbury, MD
- Kurt and Wendy Vander Meer | Continental Linen Services (CLS)
- ImageFIRST Healthcare Laundry Specialists | King of Prussia, PA
Diversity Recognition
Honoring leadership in valuing the uniqueness of individuals and encouraging and facilitating
variation in human qualities in the workforce, as selected by industry peers.
DIVERSITY RECOGNITION
- Sohn Linen Service | Lansing, MI
SILVER
- NOVO Health Services | Atlanta, GA
- Wanda Javier, NOVO Health Services | Miami, FL
Fleet Graphics
- GOLD
- Alsco Uniforms | Salt Lake City, UT
- Medico Healthcare Linen Service | Los Angeles, CA
- Mickey’s Linen | Chicago, IL
- Wagg’s Linen & Uniform | Orilla, ON
SILVER
- HLS Linen Services | Ottawa, ON
- Prudential Overall Supply | Irvine, CA
- Sohn Linen Service | Lansing, MI
- U.S. Linen & Uniform | Richland, WA
HONORABLE MENTION
- CITY Healthcare | Pine City, MN
- Gallagher Uniform | Battle Creek, MI
- Huebsch Services | Eau Claire, WI
- ImageFIRST Healthcare Laundry Specialists | King of Prussia, PA
- Medicleanse | Renton, WA
- Republic Master Chefs | Los Angeles, CA
- Wildman Business Group | Warsaw, IN
Member Engagement
Honoring exemplary participation in the wide range of TRSA activities that improve individual and
corporate performance.
GOLD
- Alsco Uniforms | Salt Lake City, UT
- ARCO/Murray | Downers Grove, IL
- Dempsey Uniform and Linen Supply | Jessup, PA
- Ellis Corp. | Itasca, IL
- Kannegiesser ETech | Minneapolis, MN
- Roscoe Co. | Chicago, IL
SILVER
- Miller’s Textile Services | Wapakoneta, OH
- Superior Linen Service | Tulsa, OK
- UniFirst Corp. | Wilmington, MA
SafeTRSA Excellence Award
Honoring leadership that embraces safety as a true corporate value, indicated by exceptional
support from top management, plus employee involvement, training and communication.
Industry peers select winners. as selected by industry peers.
GOLD
- UniFirst Corp. | Owensboro, KY
SILVER
- ImageFIRST Healthcare Laundry Specialists | King of Prussia, PA
- NOVO Health Services | Atlanta, GA
- Superior Linen Service, Inc. | Eastern Division
Honorable Mention
- HandCraft Linen Services | Richmond, VA
- Linen King | Ooltewah, TN
- Virginia Textile Services | Petersburg, VA
TRSA Legislator of the Year Award
Honoring theU.S. legislator who is most supportive of the linen, uniform and facility services
industry. The TRSA Government Relations Committee selects awardees.
- Rep. Greg Landsman | House of Representatives (D-OH)
- Rep. Mike Carey | House of Representatives (R-OH
Volunteer Leadership
Honoring leadership in guiding TRSA’s success in advocacy, certification, education, research,
benchmarking and networking to strengthen the association.
- Charles Edelman | Unitex Healthcare Laundry Services
For more information on TRSA visit the website.
CFA at Parliament
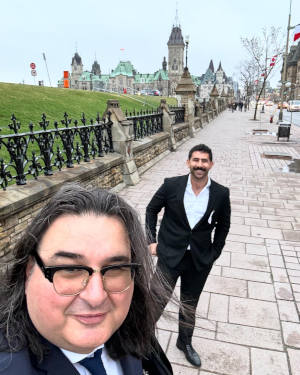
On April 11, Canadian Fabricare Association President Konstadin (Dino) Kantzavelos spoke in front of House of Commons Committee on Finance on Parliament Hill in Ottawa, to solicit the Members’ support for assistance to the industry.
“The main focus of the meetings was a bill that addresses options for the redistribution of the extra money available to various industries from the collection of the new carbon tax,” Dino said. “20% of the money collected is not spent, but held in trust or escrow. The government will allocate these funds to areas that are open for discussion. CFA presented in front of some of the biggest Canadian lobby groups, which are all vying for a piece of these billions of dollars.”
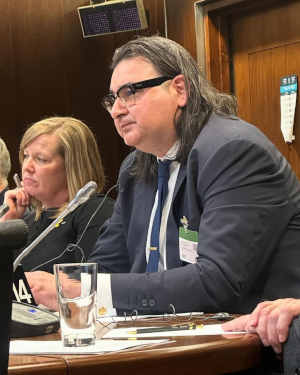
Dino focused his testimony on the state of the fabricare industry before, during and since the COVID-19 pandemic. The impact of the lockdowns and being designated an Essential Service were devastating to the industry, and caused an estimated one-third of the companies in Canada to close their doors permanently. He said the Members seemed engaged and interested to learn of these facts, most of which they had not considered before.
He also made the point that, though the lock-downs and pandemic seem to be past, the impact on the industry lingers strongly.
Dino requested implementation of a 25% tax credit for using commercial cleaning and laundry services, as is done in Sweden.
Many other lobby groups were present, and the committee will be considering all the proposals.
If you would like to view the hearing, click here.
Dino’s speech starts at 16:44:30
1st Q and A starts at 17:29:20
2nd Q and A starts at 17:42:01
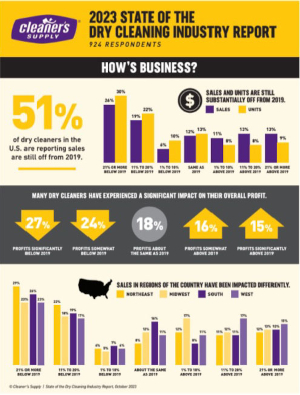
Cleaner’s Supply issues both Industry and Consumer pulse reports
Two reports by Cleaner’s Supply — both the result of surveys of hundreds of operators and consumers — are the buzz of the industry right now. Both reports are packed with interesting and provocative information, presented in an easy-to-understand format using charts, graphics and large print. You won’t fall asleep reading these, and you just might find ways to improve your business by taking them to heart.
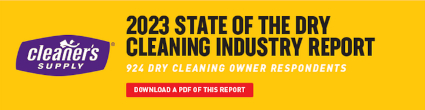
The State of the Dry Cleaning Industry report was drawn from 924 respondents’ surveys. It includes:
- How’s business?
- Garment prices and trends
- Garment prices by region and location
- Store operations and challenges
- Who is the typical dry cleaner owner?
- Grow, grow, grow your business
- Dry cleaners with profits up
- Future of dry cleaning
You can read the report on their website here, or you can download your own copy to print out and study (in PDF format).
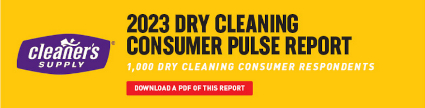
The Dry Cleaning Consumer Pulse Report was drawn from the results of 1000 consumers responding to the survey. It includes:
- How satisfied are customers with their dry cleaner?
- Delivery vs. in-store
- Types of dry cleaning the consumers use
- The value they place on quality
- Speed of service
- How they want to be notified by their cleaner
You can read the report on their website here, or you can download your own copy to print out and study (in PDF format).
Alberta Conference 2024 Report
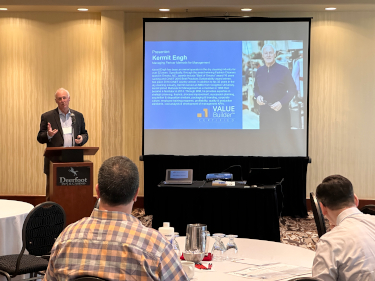
The Alberta Textile Care Association held it’s annual conference over the weekend of April 13, 2024 in Calgary, AB. People attended from Edmonton, Calgary and many places in Alberta and Saskatchewan. They networked, shared information, and listened to interesting speakers on a variety of topics.
- Kermit Engh (Methods for Management) spoke on drivers of value, preparing for an exit from your business, and open book management.
- Tok Bakinson (local CPA) spoke on how to prepare for growth in your company, where to find growth, and make sure you have the cash to meet the challenges of growth.
- Neil Gerritson (local business broker) spoke about the process of selling a business, and how the industry can attract strong valuations.
- Mike Tungesvick (Sankosha) spoke on how to use top of the line equipment to bring effiency and increase profitability.
- Chris Tebbs gave an industry update and spoke on care labeling.
The association is grateful to longtime vendor supporters Integrity Mechanical and Elevation Supplies.
CLATA holds Annual General Meeting
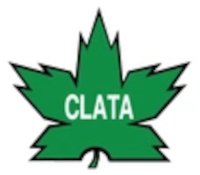
The Cleaners and Launderers Allied Trades Association held it’s Annual General Meeting on April 4 in Montreal, QC. Various items were discussed, including:
2024-25 Officers
- Ashlynn McConvey (Dalex Canada Inc.), President
- Earl Eichen (Lavanett Equipment), Past President
- Steve Freeman, Secretary
- Trevor Holmes (Seitz Inc.), Treasurer
2024-25 Board of Directors
- Malcolm Caldwell (Harco Co. Ltd.)
- Patrick Robertson (Tingue Canada)
- Denis Lamarre (Lavanett Equipment)
- Marc-Antoine Gelac (Kannegeisser Canada)
- Nicolas Legault (Gurtler Chemicals)
- William Kahan (Unipress Corp.)
- Artur Keyes (Extox Industries)
The annual golf tournament will be held on Thursday September 12th at the Bay of Quinte Golf Club. Trevor Holmes will share further details at a later date. [They will be posted on our Events Page as soon as we have them.]
Planning is also under way for the always-well-attended CLATA reception at the next US Clean Show in August 2025 in Orlando.
The next AGM is tentatively scheduled for April 3, 2025 in Toronto.
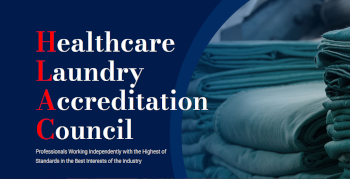
HLAC RECEIVES AHE SEAL
HLAC’s dedication to excellence in Healthcare Laundry Accreditation has brought it the prestigious AHE (Association for the Health Care Environment) Seal of Review and Recognition. “This honor is a testament to our unwavering commitment to providing top-tier quality and safety in all facets of laundry operations” HLAC said.
The AHE Seal of Review and Recognition Program is designed to be a comprehensive review and formalized recognition process aimed at assisting professionals in selecting training and in-service programs for the health care environment.
For providers of health care training and in-service programs, the AHE Seal of Review and Recognition is a respected symbol, providing acknowledgment that a training or education program is a recognized resource for environmental services and multi-disciplinary professionals.
The AHE Seal of Review and Recognition is a trademark of AHE, all rights reserved.
Reminder to Canadian users of tetrachloroethylene (PERC or PCE)

Every dry-cleaning facility that uses tetrachloroethylene (PERC or PCE) is subject to the Tetrachloroethylene (Use in Dry Cleaning and Reporting Requirements) Regulations? As a PERC user under the Regulations, you are responsible for: 1) Proper handling, recovery and disposal of PERC, 2) Preventing spills, and 3) Reporting and keeping your records.
Please refer to the following factsheets and video for an overview of your obligations under the Regulations:
- PERC pointer 1 – Cover Waste Containers
- PERC pointer 2 – PERC Waste Disposal
- PERC pointer 3 – PERC Resistant Drain Plugs
- PERC pointer 4 – Secondary Containment
- PERC pointer 5 – Secondary Containment Size
- Factsheet on Handling PERC and PERC Waste in Dry Cleaning
- Checklist for Dry Cleaners Using PERC
- Video on Handling PERC and PERC Waste
If you are subject to the Regulations, to avoid common errors when completing the reporting forms, please remember to include the:
- reporting year, complete address (postal code and province included) and contact information.
- date(s) and quantity(ies), in kilograms, of each PERC purchase made.
- date(s) and quantity(ies), in kilograms or litres, of waste water and residue (including any filters), which must be transported at least once every 12 months regardless of volume.
- the name and contact information of your waste transporter and waste management facility.
The Tetrachloroethylene (Use in Dry Cleaning and Reporting Requirements) Regulations also have requirements that apply to sellers of PERC to owners or operators of dry-cleaning machines, to importers of PERC for any purpose, and to recyclers of PERC. For more information on how these Regulations apply to you or to find copies and examples of reporting forms, please visit: www.canada.ca/perc-dry-cleaning.
Persons subject to the Regulations are required to report to Environment and Climate Change Canada by April 30, 2024, to produits-products@ec.gc.ca or to:
Tetrachloroethylene Regulations Coordinator
Chemical Production and Products Division
Environment and Climate Change Canada
351 Boulevard Saint‐Joseph, 9th floor
Gatineau, QC K1A 0H3
Failure to comply with the Regulations is an offence under the Canadian Environmental Protection Act, 1999 and is punishable under the Act.
If you have further questions, you may contact your regional compliance promotion officer: Regional contacts: Tetrachloroethylene (PERC) Regulations.
Avis à l’intention des nettoyeurs à sec qui utilisent du tétrachloroéthylène (PERC ou PCE)
Saviez-vous que toutes les installations de nettoyage à sec qui utilisent du PERC sont assujetties au Règlement sur le tétrachloroéthylène (utilisation dans le nettoyage à sec et rapports)? En tant qu’utilisateur de PERC en vertu de ce règlement, vous êtes responsable 1) de la manipulation, de la récupération et de l’élimination appropriées du PERC, 2) de la prévention des déversements et 3) de la production de rapports et de la tenue des registres.
Reportez-vous aux fiches d’information et vidéo suivantes pour un aperçu de vos obligations en vertu du Règlement :
- Conseil no 1 sur le PERC – Couvrir les conteneurs à déchets
- Conseil no 2 sur le PERC – Pratiques d’élimination des déchets de PERC
- Conseil no 3 sur le PERC – Bouchons résistant au PERC
- Conseil no 4 sur le PERC – Systèmes de confinement secondaire
- Conseil no 5 sur le PERC – Format des systèmes de confinement secondaire
- Fiche d’information sur la manipulation du PERC et les déchets de PERC pour le nettoyage à sec
- Liste de vérification pour les installations de nettoyage à sec utilisant le PERC
- Un vidéo sur la manipulation du PERC et les déchets de PERC
Si le règlement s’applique à vous, évitez les erreurs communes suivantes lorsque vous remplissez votre rapport annuel en incluant ce qui suit :
- l’année du rapport, votre adresse complète (avec code postal et province) et vos coordonnées;
- la quantité, en kilogrammes, des achats de PERC, et date à laquelle les achats ont été effectués;
- la quantité, en kilogrammes ou litres, des eaux usées et des résidus (y compris tous les filtres) qui doivent être transportés au moins une fois tous les 12 mois, quel que soit le volume, et la date à laquelle les transports ont été effectués;
- le nom et coordonnées de votre transporteur de déchets et de votre installation de gestion des déchets.
Le Règlement comporte également des exigences qui s’appliquent aux entités qui vendent du PERC aux propriétaires ou aux exploitants d’appareils de nettoyage à sec, aux importateurs de PERC à toutes fins et aux recycleurs de PERC. Pour de plus amples renseignements sur le Règlement ou pour trouver des copies et des exemples de formulaires de rapport, veuillez consulter le site : www.canada.ca/PERC-nettoyage-sec.
Quiconque est assujetti au Règlement doit soumettre son rapport à Environnement et Changement climatique Canada d’ici le 30 avril 2024 à produits-products@ec.gc.ca ou à :
Coordinateur du Règlement sur le tétrachloroéthylène
Division des produits et de la production chimique
Environnement et Changement climatique Canada
351, boulevard Saint-Joseph, 9e étage
Gatineau (Québec) K1A 0H3
Le non-respect de ce règlement constitue une infraction à la Loi canadienne sur la protection de l’environnement (1999) et est punissable en vertu de cette loi.
Si vous avez d’autres questions, vous pouvez communiquer avec votre agent régional chargé de la promotion de la conformité à l’adresse suivante : Contacts régionaux : Règlement sur le tétrachloroéthylène (PERC)
MARCH 2024 NEWS
CFA Partners with Allied Trades for Clean Canada EXPO 2024
The Canadian Fabricare Association is partnering with the Allied Trades to put on Clean Canada Expo 2024. The event will take place at the Delta Toronto Airport Hotel in Toronto, Canada on Saturday, November 23rd, and Sunday November 24th, 2024.
The event will feature products, services, and operational equipment from over 35 manufacturers and distributors and will also include several business sessions simultaneously during the event. Attendees will have their choice of which sessions they want to attend and participate in one-on-one discussions with the presenters. This format will guarantee attendees the opportunity to learn about new ideas and technology to help them grow their business. The list of speakers and their topics will be announced shortly.
Registration for the show is FREE. For those who are interested in continuing to network and enjoy the events, there will be a cocktail party and dinner when the show closes on Saturday. Lunch on Saturday and food and drink during the event are available, thanks to the sponsors.
Rooms at the hotel are available at a reduced rate of Can $199.00 plus tax. There is a limited block of rooms available, so book yours as soon as possible. Last year the group ran out of its allotment, and many were disappointed. The hotel is located just minutes from the airport, and the hotel provides free shuttle services.
For information see the website: www.fabricare.org or contact Sid Chelsky, the Executive Director, at canadianfabricare@fabricare.org or 416-573-1929.
ARTA Announces New Board President
The American Reusable Textile Association (ARTA) announced Jerry Martin, Vice President of Sales and Marketing at Prudential Overall Supply has been appointed as the new ARTA President of the Board of Directors.
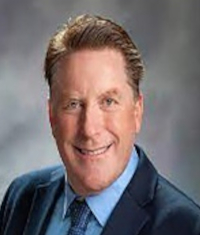
With over 30 years of wide-ranging sales, marketing, public relations and management experience at Prudential Overall Supply, Jerry Martin uses his extensive knowledge of the company and the industry to lead Prudential’s sales and marketing efforts. He is committed to building and enhancing the company’s customer-focused, growth-oriented sales culture as demonstrated by being recognized on Selling Power’s “50 Best Companies to Sell For” list for the fifth consecutive year.
Jerry participates in related green industry efforts through his involvement in the American Reusable Textile Association (ARTA). In addition to the presidency, he also chairs the cleanroom committee and is a member of the marketing and education conference committees. He is the past co-chairman of the association’s Marketing & PR committee.
Through his work at TRSA, Jerry helped establish the organization’s international standard for the Clean Green certification program. He currently serves on TRSA’s Clean Green advisory committee to help maintain the integrity of the certification program, along with growing the program’s marketplace brand.
Jerry earned his M.B.A. and B.A. degrees from San Diego State University. He has been married to his wife Nicole for the past 30 years and they have two daughters (23 and 20) who all reside in the San Diego, CA area.
Onward and Upward for Jensen
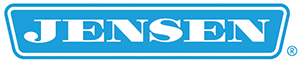
In 2023, the Jensen-Group achieved an unprecedented revenue milestone of 400.1 MEUR [million Euros] [US$437.6 million], compared to 341.6 MEUR in 2022, representing exponential growth of 17.1%. This increase was attributed to an exceptionally high order backlog at the end of 2022, a strong order intake in the first semester, and a notable rebound of orders received in the second semester of 2023. The notable increase in operating profit, standing now at 40.7 MEUR, is a direct result of the growth.
Recognition from laundries around the world
Healthcare, hospitality and also industrial laundry services in all countries that Jensen serves have seen a strong rebound, matching the levels seen before the COVID-19 pandemic. The company says this renewed growth is prompting laundry facilities to explore innovative solutions that improve hygiene standards and enhance operational efficiency and align with their sustainability goals.
The Jensen-Group recognized a rising demand for automated solutions employing robotics and AI. Throughout its fifth year of collaboration with Inwatec Aps, numerous new laundries were established across all continents, where robotics were integrated alongside tunnel washers and finishing lines.
Recognition from the financial markets
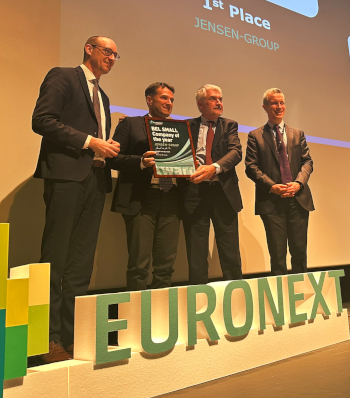
On January 15, 2024, the Jensen-Group was honored with the BEL Small Company of the Year 2023 Award at the Euronext & GUBERNA New Year 2024 Event in Brussels. The award recognized the company’s share performance compared to peers, reflecting how the market evaluates the performance of a publicly traded company and the trust analysts and investors place in it. This achievement is particularly noteworthy, as an industrial company surpassing consumer or other brands is very unusual.
Investments for a successful future
To prepare for the next phase of growth, the Group executed several key investments in 2023. This included acquiring 49% of the shares of Inax Corporation, a leading Japanese manufacturer and distributor of commercial laundry equipment. Additionally, the Group acquired Ole Almeborg, a manufacturing facility on the island of Bornholm intended to supplement production space. Alongside this acquisition, the Group committed to additional capital expenditures of €6 million [US$6.52 million] for 2024. Investments were also made in larger production premises for Inwatec, the Group’s AI and robotics subsidiary in Denmark.
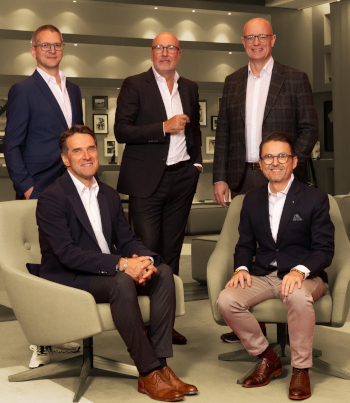
Expansion of the Executive Management Team
As of January 1, 2024, Mads Andresen will become a member of Jensen’s Executive Management Team in his new role as Chief Innovation Officer. He will enhance the framework for innovative advancements in all the company’s technologies and play a crucial role in further defining the integration strategy for robotics, AI, and machine learning within the Jensen-Group’s operations.
Outlook
The Group’s aim for 2024 is to “maintain momentum and solidify its market position and profitability level by relentlessly focusing on commercial excellence and manufacturing productivity.” The Group will continue to drive customer-centricity and sustainable innovation through the development of new products and services and by means of its participating interest in Inwatec ApS, while further enhancing the optimization and digitalization of business processes and applications.
The company’s CEO, Jesper Munch Jensen is delighted with the results: “Over the past few years, we have become the number one market leader in heavy-duty laundry equipment, surpassing our competitors in innovation leadership and revenue.”
AWGS Conference Report
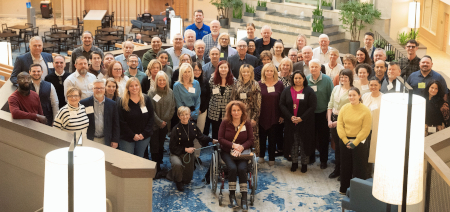
Members of the Association of Wedding Gown Specialists (AWGS) met recently in Dublin, Ohio. In addition to the traditional tour of a member’s plant, Dublin Cleaners, owned and managed by Brian Butler as well as Greg and Margaret Butler, guest speakers included digital marketing strategist Kristina Stubblefirld, who is also an expert in AI, and Emily Rochotte, a social media manager whose specialty is TikTok content.
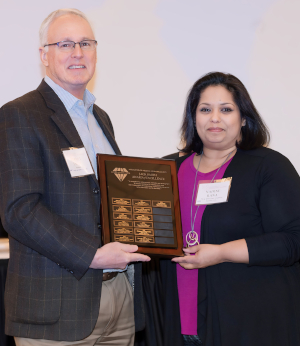
A highlight of the meeting was the presentation of the thirteenth annual Jack Barth Memorial Award of Excellence. Initiated by Linda Stokes-Barth in remembrance of her late husband and his achievements in the dry cleaning industry, the award recognizes an AWGS for advancement, promotion, and development of industry standards for wedding gown care and for outstanding contributions and service to the Association and its members.
This year’s honoree, Nadine Rana of Style & Grace Cleaners in Toronto, Ontario, is a highly-regarded choice. Rana’s parents, Neville and Grace Mungal, joined the Association in 1991, and Rana and her brother Don Mungal (of Drape Master) are currently second-generation owners. Rana has presided over rebranding her company from multiple names to the new designation Style & Grace Cleaners. As she notes, “Our goal at Style & Grace is to take the term ‘Take you to the cleaners’ and turn it on its head, leaving you with a positive experience, polished product, and convenient service. Our expert dry or wet cleaning, garment finishing and convenient repairs and alterations will make sure you maintain your style, with Grace.”
At the meeting of the Association last year in Napa, California, Rana co-chaired a team who managed the group’s self-directed SWOT analysis and has continued to direct the team’s follow-up activities including Zoom calls devoted developing a process for obtaining reviews and partnering with bridal boutiques. In previous years she has presented on topics such as “Training and Recruiting a Reliable Team.” She was also an important component in the creation of the Association’s all-new websites www.weddinggownspecialists.com and www.weddinggownspecialists.net which include a special digital resource section accessible to Association members only..
Other speakers at the event included Jim Gilligan of Snedicor’s in Howell, Michigan, on the topic of transitioning to a delivery-only model of garment care as well as Gary Fine of Parkers Custom Clothing Care in Toronto, Ontario, and Mickey Goldberg of One Local on generating reviews at the counter.
In addition to speakers, there were a series of round-table conversations offering everyone in the group the chance to discuss topics ranging from the best techniques for marketing with AI to appealing to brides on TikTok. Table hosts were Clare Bobbitt of Oceanside Cleaners in Jacksonville, FL on creating a positive work culture, Brian Butler on training with video, and Dave Matthews, National Training Director on managing tough cleaning challenges.
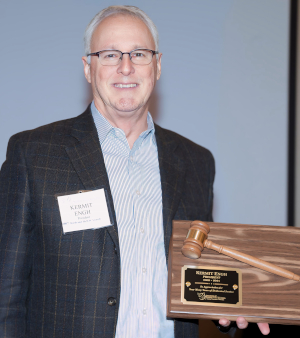
Retiring president Kermit Engh of Fashion Cleaners and Omaha Lace in Omaha, Nebraska as well as of Methods for Management presided over the installation of officers: incoming president Kyle Matthews of Janet Davis Cleaners in Berkeley, Michigan, vice president Gary Fine of Parkers Custom Clothing Care in Toronto, Ontario, and secretary-treasurer Rhonda Wernick of Oakwood the Greener Cleaners in Nashville, Tennessee. Engh takes the place of immediate past president Malcolm MacGregor of Brown’s Cleaners in Ottawa, Ontario, who remains in place as chair of the Budget and Finance Committee.
Incoming members of the Board are Bobbitt and Kurt Lucero of The Cleanery in Albuquerque and Santa Fe, New Mexico.
Retiring members of the Board are Brandon Maloney of Nu-Yale Cleaners in Jeffersonville, Indiana, and Louisville, Kentucky, and Tom Ustanik of Lansing Cleaners in Lansing, Illinois.
Members new to the Association are Randy and Ramona Jaeger of Canyon Cleaners in Rifle, Colorado, Art Buckland of Nor’East Cleaners in Gloucester, Massachusetts, Will Drook of Fox Cleaners and Armstrong Cleaners in Dayton, Ohio, Maggie Fox of Fox Cleaners in Tulsa, Oklahoma, Greg Gunderson of Gunderson Cleaners in Appleton, Wisconsin, Marcus Walker of Upton Cleaners in Southport, Queensland, Australia, Brittany Chamberland of ARC Sewing Services in St. Paul, Alberta, Canada, and Dominador Asis III of Absolute Laundry and Drycleaners in Antipolo City, The Philippines.
Sponsors of the event were Kreussler, Inc., Foster-Stephens, Inc., Sankosha-USA, Inc, Select Risk Insurance, and Kleerwite Chemicals.
AWGS is a not-for-profit trade association with members in eight countries. Members are certified to ensure that wedding gowns and heirloom textiles of all kinds are cleaned according to established museum standards and preserved in archival-quality materials. Wedding couples benefit from the personal, interactive service offered by wedding gown specialists in local communities, but the guarantee is truly an international warranty because each member honors the guarantee of every other member no matter where in the world they may be.
For more information about training and membership, call the Association office
at 800-501-5005 or go to www.WeddingGownSpecialists.com or www.WeddingGownSpecialists.net.au.
Alberta Textile Care Association Convention coming in April
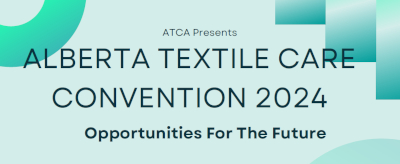
The ATCA convention, themed “Opportunities for the Future”, will be held Saturday, April 13, at the Deerfoot Inn & Casino, Calgary, AB.
In announcing the event, the convention committee said, “Get ready to join the coolest crowd in town — industry leaders, inspiring speakers, and awesome business owners just like you! We’re coming together to geek out on the latest trends and juicy opportunities to help you skyrocket your business to success. Don’t miss out on this epic event — let’s learn, network, and have a blast together!”
Speakers will be announced soon. Topics will include:
- Grow & Expand — Financial literacy as a superpower
- Innovative equipment to boost profits
- Marketing — digital and traditional techniques
- Regulation changes affecting our industry
- More…
The convention will also include supplier trade show tables, lunch, and an open forum, plus networking opportunities. Registrations before March 12 are entered into an Early Bird Drawing for a free night at Deerfoot Inn & Casino.
Registration and tickets are available at ABTCA.eventbrite.ca.
TCATA 2024 Annual Management and Educational Conference
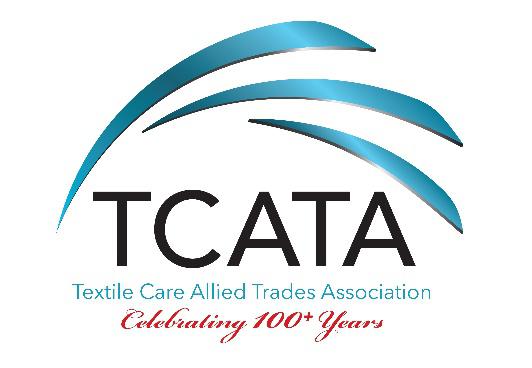
The Textile Care Allied Trades Association will hold its 2024 Management and Educational Conference April 28 – May 1 at the Barton Creek Omni Resort in Austin, TX.
The conference will include two keynote speakers. Pamela Barnum, The Trust Agent, will discuss intentional communication through verbal and non-verbal cues to help you build trust, and influence and negotiate in your business. Tom Edwards, Futurist, will speak on how Artificial Intelligence (AI) can streamline tasks for businesses of any size. He will also give an interactive workshop on AI during the Executive Idea Exchange at the conference.
First-time attendees, and those who have not attended in at least 5 years, receive a special registration rate of $625. The conference rate for additional attendees from the same company has been dropped to $595.
For more information, visit the TCATA conference page on the website.
DLI Announces Hall of Fame
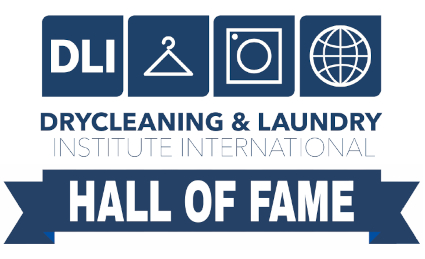
Nominations open April 1 for the Drycleaning & Laundry Institute’s (DLI) all-new Hall of Fame Award, the Institute’s highest honor. All industry professionals are invited to nominate a candidate for the award. Membership in DLI or any other organization is not required to nominate a candidate or receive an award. DLI’s Board of Directors established the Hall of Fame Award to recognize and acknowledge individuals who have contributed to the betterment of the drycleaning and laundry industry.
“Pioneers, heroes, innovators – the Hall of Fame forever memorializes those who shaped our industry’s past and ignites its future,” said Jeff Schwegmann II, DLI’s current Chairman of the Board and Owner of Sunshine Cleaners in Cold Spring, Kentucky, and U.S. Leather Cleaning.
Nominations for DLI’s Hall of Fame Award are open April 1 – May 15 and will be accepted from and for any industry participant, regardless of organizational membership, through a form available at DLIonline.org/HoF. DLI’s Board of Directors will review applications and recipients will be announced to the industry by mid-September.
Candidates for the award include industry pioneers, exceptional business leaders, and community advocates. DLI intends to shine a spotlight on individuals who have made a lasting positive impact on the industry.
Mary Scalco, DLI’s CEO, said, “Professional drycleaning and laundry operators from all over the world contribute to the betterment of our industry every day. Our goal with the Hall of Fame is to recognize contributions made by any professional in our industry who has made a positive impact and honor them as examples for other members of the industry. All cleaning professionals, regardless of membership, are welcome to nominate industry professionals they see as inspirational for this award.”
Norman Way of Puritan Cleaners in Richmond, Virginia and District 2 Director on DLI Board, said, “At a recent DLI Board meeting, we all thought of people in our industry who helped us grow personally and professionally and how we might honor them. We know others feel the same and the DLI Hall of Fame Award seems like the perfect way to commend and recognize these impactful leaders who left a lasting effect on us all.”
“The introduction of DLI’s Hall of Fame award is just one of many aspects that makes our industry great,” said Mark Albrecht of The Route Pros in Woodbury, New Jersey. “We all have so many true mentors and drycleaning superheroes. This award will ensure that those peoples’ legacies are at the forefront of so many of our minds as we move into the future.”
Online Nominations Due May 15
To be eligible for nomination, candidates must have a minimum of 10 years of experience working in the drycleaning and laundry industry. The selection process will involve a two-stage voting process by DLI’s Hall of Fame committee, and the awardees will be publicly announced and celebrated.
Inaugural Inductees
DLI’s inaugural group of Hall of Fame inductees includes previous recipients of DLI’s Diamond Achievement Meritorious Service Award. DLI recognized eight industry legends with its Diamond Achievement Award over a 25-year period. Their names are etched in bronze on a plaque that hangs at DLI’s offices by the entrance to DLI’s School of Drycleaning Technology in Laurel, Maryland. Industry professionals who received DLI’s highest honor are:
- Barney Deden, retired drycleaner in Omaha, Nebraska (1999)
“For his deep commitment and untiring efforts on legislative efforts for the industry” - Stan Golomb, Founder of The Golomb Group, Chicago, Illinois (2001)
“For helping generations of drycleaning & laundry professionals achieve success” - Chris Edwards, A Cleaner World, High Point, North Carolina (2005)
“For his work to enhance the industry’s image through tireless charitable and environmental community service” - Jeff Miller, Miller’s Fine Drycleaning, Hendersonville, North Carolina (2007)
“For helping hundreds of WWII Veterans visit their memorial on the National Mall in Washington, D.C.” - Sid Tuchman, Tuchman Training Systems, San Francisco, California (2011)
“For his unwavering dedication to helping hundreds of drycleaning & laundry professionals achieve success” - Don Fawcett, Dependable Cleaners, Quincy, Massachusetts (2015)
“For his unwavering commitment to excellence and lifetime of selfless service to the industry” - Milt Chortkoff, Milt & Edie’s Drycleaning & Tailoring Center, Burbank, California (2018)
“For a lifetime of demonstrating excellence in customer service and charitable service” - Walter “Buster “Bell, Bell Laundry and Cleaners, Spartanburg, South Carolina (2018)
“For his deep commitment and lifelong dedication to helping people succeed in the drycleaning business”
These individuals consistently demonstrated exceptional dedication and achievement in their respective fields. DLI’s Hall of Fame was created to honor outstanding industry individuals and businesses. The new Hall of Fame award succeeds the institute’s highest honor, celebrating excellence in leadership, business operations, community involvement, environmental stewardship, and a deep-seated passion for the industry.
All 2024 recipients of the Hall of Fame Award will be recognized at state or national events, further highlighting their significant contributions to the drycleaning and laundry industry.
For more information about the DLI Hall of Fame Award and to make a nomination, please visit DLI’s official Hall of Fame page at DLIonline.org/HoF
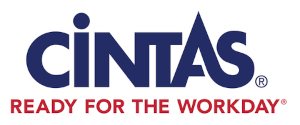
Cintas acquires SITEX
(As reported by Business Newswire)
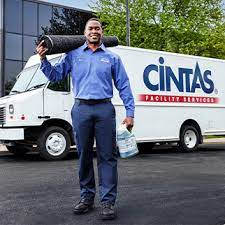
Cintas Corporation (Nasdaq: CTAS) has acquired SITEX, a Kentucky-based, family-owned supplier of uniform and facility service programs.
SITEX was founded by the Sights family in Henderson, Kentucky in 1961. Currently, Wes Sights serves as CEO of SITEX, which has five different locations servicing customers in a four-state region, including Illinois, Indiana, Kentucky and Tennessee.
“The Sights family has grown SITEX into a strong regional provider of quality apparel and facility service solutions to their customers in the central Midwest,” said Scott Garula, President and COO of Cintas’ Rental Division. “They’ve built a successful company with a well-earned reputation for delivering outstanding customer and employee experiences. We look forward to welcoming SITEX’s customers and employees to Cintas in the coming months.”
“Our customers and employees have always been and remain our primary focus for any decision we make,” said Wes Sights, CEO of SITEX. “The opportunity for SITEX to become part of the industry-leading Cintas team allows us to offer more services and products for our customers and capitalize on Cintas’ supply chain support while still delivering the highest level of service.”
About Cintas Corporation
Cintas Corporation helps more than one million businesses of all types and sizes get Ready™ to open their doors with confidence every day by providing products and services that help keep their customers’ facilities and employees clean, safe, and looking their best. With offerings including uniforms, mats, mops, towels, restroom supplies, workplace water services, first aid and safety products, eye-wash stations, safety training, fire extinguishers, sprinkler systems and alarm service, Cintas helps customers get Ready for the Workday®. Headquartered in Cincinnati, Cintas is a publicly held Fortune 500 company traded over the Nasdaq Global Select Market under the symbol CTAS and is a component of both the Standard & Poor’s 500 Index and Nasdaq-100 Index.
For more information: Michelle Goret, Cintas Vice President of Corporate Affairs | goretm@cintas.com, 513-972-4155.
FEBRUARY 2024 NEWS
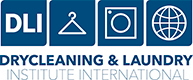
DLI Hosts 13 Events In March
The Drycleaning & Laundry Institute will host 13 in-person and virtual events this month. One, the virtual Customer Service Excellence, sold out in just two weeks, and a second has been added. Other learning opportunities are below.
- March 5, 7, and 12 – 1–3 p.m. Eastern: DLI’s Customer Service Excellence Virtual Course featuring Jennifer Whitmarsh of Snappy Drycleaning & The Route Pros
Students will learn how to create raving fans by confidently managing customer issues and gain insights into industry best practices.
On-Site Drycleaning Courses Educate and Elevate
DLI’s School of Drycleaning Technology is the ultimate destination for professionals who seek to advance their expertise and stay ahead in the industry. DLI presents two in-person, on-site courses this month. DLIs’ school is now in its 97th year of educating drycleaning personnel, managers, and business owners.
- March 4–8: DLI’s Five-Day Introduction to Drycleaning Course
Suited for experienced individuals or those who are new to the industry. - March 11–22: Ten-Day Advanced Drycleaning Course
For individuals who have completed the Introduction to Drycleaning Course or have hands-on production experience and knowledge of basic stain removal ad finishing techniques.
These courses are designed to run together as DLI’s 15-Day General Drycleaning Course. Scholarships are available for these courses. (NOTE: The Canadian scholarship has already been awarded. We will have a report from the winner when she returns.)
Featured Online Presentations Enlighten & Entertain
This month’s web presentations focus on looking at the economy ahead and offering multiple service levels to customers.
DLI’s *Not Boring* “2024 Economic Forecast” web presentation by economist Chris Kuehl was moved to March 6 at 1 p.m. Eastern. Kuehl is known for his entertaining and informative look at economic concerns. While every crystal ball is foggy, Kuehl is well-informed and able to share economic data in enlightening and light-hearted ways.
In recent years, many clothing care professionals expanded their levels of service for customers. To help drycleaners consider the possibility of introducing multiple service levels, DLI presents “Exploring Multiple Service Levels in Drycleaning” a live online presentation March 27 at 1 p.m. Eastern on Zoom. Attendees will learn from several drycleaners who integrated multiple levels of service into their business strategy.
- March 6 – 1 p.m. Eastern: *Not Boring* 2024 Economic Forecast with Economist Chris Kuehl
- March 27 – 1 p.m. Eastern: Multiple Service Levels – Your New Business Model?
Since offering live monthly webinar programs in March 2020, DLI has recorded and stored more than 150 presentations in its Online Webinar Library covering marketing, management, diversifications, and more aspects of running a successful drycleaning business. Full access to all the recordings and live presentations is available for all DLI members.
Additional Virtual Programs Keep Members Engaged
In addition to the live presentation on service levels, DLI will host its monthly Membership Orientation program March 6. Not just for new members, the interactive presentation provides a comprehensive overview of the benefits afforded to all members of the association.
DLI’s Marketing Lab will bring cleaners together March 20 to discuss current marketing trends and effective solutions. Recent meetings covered the value of trigger-based marketing, what some members are doing to keep customers happy and using additional services.
- March 6 – 3 p.m. Eastern: DLI Member Virtual Reception and Orientation
All members are invited to take a tour of DLI’s extended array of money-saving benefits and services.
- March 20 – 3 p.m. Eastern: DLI’s Marketing Lab
All Members are invited to brainstorm marketing ideas in this monthly Virtual roundtable discussion.
Weekly Member Peer Meetings Keep Members Connected
Bringing the drycleaning and laundry community together, DLI hosts weekly coffee-and-shop-talk meetings every Tuesday morning on Zoom so members can discuss what’s happening and share new ideas, thoughts and tips.
- March 6, 13, 20 & 27 – 11:30 a.m. to 12:30 p.m. Eastern: DLI Peer-To-Peer Membership Zoom Meetings
Members receive invitations to these meetings via email from DLI.
Regional Association Programs Bring Cleaners Together
DLI’s expansive network of regional associations present the following events:
- March 8 & 9 – Joint Board Meeting hosted by the Southwest Drycleaners Association (SDA) & South Eastern Fabricare Association (SEFA)
SOLD OUT
Hotel Indigo French Quarter, New Orleans, Louisiana
Free for drycleaners and will feature “Creating a Contagious Business Culture,” a seminar by Jason Loeb of Sudsies. Mike Nesbit of Nesbit Consulting will present “Diversify or Die: Unveiling the Vision of Increased Piece Counts.”
- March 23 – Midwest Drycleaning & Laundry Institute (MWDLI) Indy Hanger & MWDLI Open House
Indy Hanger, Indianapolis, IN Includes two professional stain removal seminars, live Indy Hanger Manufacturing Tour, tabletop exhibits by industry vendors and complementary lunch.
For more information on any of these opportunities, visit the website, DLIonline.org.
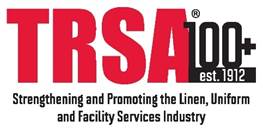
TRSA to Host HR, Health and Safety Summit in Milwaukee
The Textile Rental Services Association (TRSA), the leading trade association for linens, uniforms and facility services, is hosting its HR, Health and Safety Summit on April 30 at the Hyatt Regency Milwaukee. The one-day event will feature expert speakers, panel discussions and roundtable sessions on topics such as mental health, employee retention, compensation, safety culture, chemical safety and more.
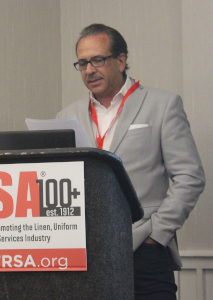
The summit is designed to help laundry managers and executives improve their human resources and safety practices, comply with the latest regulations, and enhance their employee engagement and performance. Attendees also will have the opportunity to network with peers, share best practices and learn from industry leaders.
The keynote speaker for the summit is Joyce Marter, a mental health thought leader and the founder of Joyce Marter Enterprises. Marter will share insights and strategies on how to promote mental wellness in the workplace, reduce stress and burnout, and foster a positive and productive work environment.
The HR track will include Jason Keck, a partner at Fisher Phillips, who will discuss the new HR laws and how they affect the laundry industry; Katie Cosgrove, a partner at Cosgrove Partners, who will talk about people strategy, succession, retention, and development; Lori Stanger, the vice president of people and culture at Wildman Business Group,who will cover compensation trends and best practices; and Kortney Overzet, the vice president of people development & culture at Spindle, an expert in fostering a culture of sustainability and employee engagement within organizations, will lead a conversation on new trends in retention of employees.
The Health and Safety sessions will start with learning valuable insights from SafeTRSA Award winners on fostering a strong safety culture within your organization. Stephen Jenkins, the director of safety and health at Cintas Corp., will lead a session focused on ergonomics and how to optimize workstations, equipment and processes to prevent injuries and promote employee health. Representatives from several supplier partner chemical companies will discuss the safe handling of chemicals. Additionally, Brian Varner, the owner and founder of Safety Solutions for Healthcare, will discuss the importance of safety metrics and how to effectively measure safety performance using dashboards and data-driven insights.
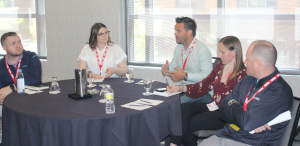
After the two breakout groups finish, attendees will gather for a presentation by Jacob Geyer, the chief insurance officer at CompScience, who will demonstrate how artificial intelligence solutions can help improve production ergonomics and reduce workers’ compensation claims. In addition, Samlane Ketevong, the director of certification and accreditation at TRSA, and Varner, will introduce the TRSA Health & Safety Self-Audit and Certification Program, a new initiative to help laundries achieve excellence in safety performance and management.
The summit will conclude with a networking reception, combined with the TRSA & WATS Midwest Production Summit, which kicks off the next day (May 1) at the same location allowing attendees to mingle with speakers, sponsors and fellow laundry professionals. Register for both summits at the same time and save 10% off the total cost. Simply enter the promo code “PRODHRSAFECOMBO” when checking out online. Early registration rates are available until March 22. To register, visit the event website at trsa.org/hr-hs, or contact TRSA at 877.770.9274 or info@trsa.org.
JANUARY 2024 NEWS
Rudi Moors launches Beyond Washing
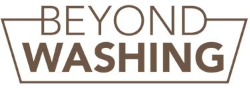
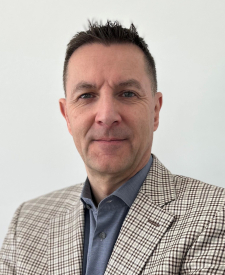
After 32 years of demonstrated success in the laundry business, Rudi Moors believes it is time for him to give back to the industry he has made his career. An executive with a unique skill base and an excellent understanding of a laundry operation, he has created Beyond Washing, LLC. The strategic services consultancy is designed so he can inspire, challenge and assist vendors who can offer meaningful solutions, as well as help operators further improve their bottom line with specific recommendations.
Moors most recently was North America’s ambassador for European hygiene solutions provider Christeyns, and he has served in many top management capacities over the years. Shortly after beginning his career in 1992, he joined Henkel-Ecolab in Europe as a territory manager at the start of a 16-year stint with the company. Following subsequent promotions with international sales and division manager positions, he left the company in 2008 to become the marketing director of laundry technology at Belgium-based Christeyns.
Three years later, Moors was named president of Christeyns USA. Tasked with establishing headquarters south of Boston, he built the company’s business by introducing innovative chemical wash solutions and concepts, precise dosing equipment, water re-use concepts and wash aisle information systems. He also was active with several acquisitions and instrumental in the negotiations that led to a merger with UNX Industries in 2022.
Through a partnership with TRSA and its certification initiatives, Beyond Washing will manage the certification auditors and process. The auditors verify that plants meet established Hygienically Clean and Clean Green standards. “TRSA is looking forward to applying Rudi’s experience and expertise toward continuously improving and expanding its certification programs,” said Joseph Ricci, TRSA President and CEO.
“Beyond Washing,” explained Moors, “is designed to help operators improve their operations, apply best practices and the best available technology, and focus on specific KPIs. I want to give back to the industry that gave me so much, with strategies that can help shape someone’s future while saving them money and improving their ROI.”
Moors will also provide expert advice to commercial and industrial laundries to help optimize plant operations, with his main focus on the wash aisle and utilities.
“For example, with wash aisle chemistry, most laundries only see it as 2-3% of their total costs,” he noted. “Who cares if you work to save 10% of that cost? But if you can improve specific KPIs by optimizing your chemical program, you can impact over 20% of your total costs through water and energy savings, extended linen life and increased productivity. That’s real money that drops to the bottom line.”
Contact him at 781-364-0247, or via email: rudi.moors@beyond-washing.com.

Ecotex to Purchase Mohawk Medbuy Linen Services and Make Major Investment in Hamilton Facility
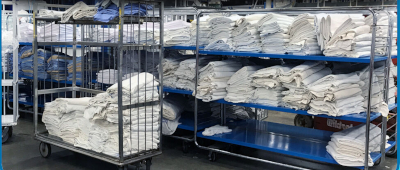
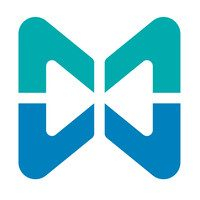
Mohawk Medbuy Corporation (MMC) announced the sale of its Linen Services division to Ecotex Healthcare Linen Service, a family-owned leader in the health care linens service business in Canada and the United States. The sale follows a competitive process facilitated by a third-party and conducted in collaboration with MMC Members. The outcome meets the criteria Mohawk Medbuy established at the outset to ensure continued employment for its Hamilton-based employees and long-term service commitments to the hospitals and other customers it supports. Divesting its linens business will allow MMC to focus on its growing, national health care supply chain services.
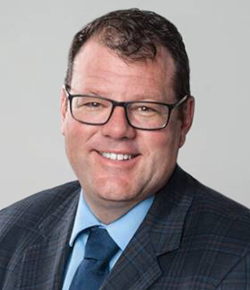
“Mohawk Medbuy has a 50-year legacy of providing quality Linens Services and we’re very proud of our team,” said Peter Longo, MMC’s Chief Operating Officer. “Ecotex is extremely well equipped to build on the dedicated service we’ve provided – and is bringing new investments in equipment to the Hamilton plant. It’s a very positive next step for our Linens staff, our Member hospitals and customers – and the City of Hamilton.” Ecotex provides health care laundry services using its large regional linen reprocessing facilities. Their use of environmentally friendly practices has earned the company a Clean Green certification. “We’re thrilled that MMC and their hospitals selected Ecotex based on the value, quality and savings we offer,” said Ecotex President and CEO, Bryan Bartsch. “We look forward to having the 200+ person team in Hamilton become part of the Ecotex family and to delivering our high standard of service to our new customers. To ensure that, we’re making infrastructure investments to the Hamilton facility this year, including a new Tunnel Washer, Press, Shuttle & Dryer System.”
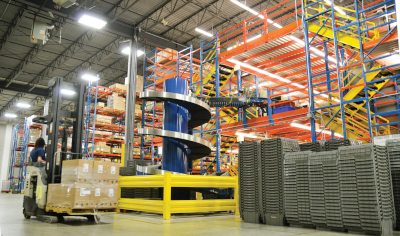
For hospitals currently served by MMC, Ecotex brings a new level of scale and resources. Based on the company’s expertise and strong track record within health care, the selection of Ecotex was firmly endorsed by all the hospitals currently served by MMC’s linen operations. “This is a very good outcome for our patients, our hospital, and our community,” said John Aldis, Senior Vice President, Finance and Corporate Services at St. Joseph’s Healthcare Hamilton. “It reflects the effort MMC undertook to engage Member hospitals through the process, align on key objectives, and find the best match in a partner that really understands and can meet our evolving linen service needs into the future.”
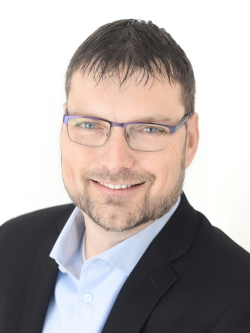
The selection of Ecotex was the right decision, according to Paul Truscott Jr., Senior Vice President and Chief Operating Officer of Health Sciences North (HSN). “Linens are essential to patient care. The scale, resources and operational redundancy that Ecotex brings to the table gives us great confidence that they will deliver for our hospital. Equally important, they’re able to provide cost savings in the process. That’s a win-win for HSN.”
Mohawk Medbuy and Ecotex are currently implementing the transition phase to ensure a seamless service handoff on February 29, 2024.
About Mohawk Medbuy
Mohawk Medbuy Corporation (MMC) is a national, not-for-profit, shared services organization that supports hundreds of health care providers across Canada, as well as child welfare agencies and otherpublic sector organizations. MMC provides value-driven contracting and procurement solutions formedical/surgical supplies, pharmaceutical products, local sourcing, capital (equipment, FF&E and redevelopment) and nutrition solutions. Other services include data analytics, in-hospital support, warehousing/logistics, technology, procure-to-pay, accounts payable and linens.
MMC is actively supporting the creation of a resilient value chain that incorporates environmental social, and economic wellbeing and fosters the participation of Indigenous businesses. Based in Burlington, ON, MMC operates regional hubs in Toronto, Thunder Bay, Kingston, Brantford and London, a distribution centre in Oakville and a linens facility in Hamilton.
About Ecotex
Ecotex Healthcare Linen Service (Ecotex) is family owned and operated company founded in 1959. Over the past 65 years the company has evolved and grown. Ecotex provides Smarter Linen Solutions™ andpartners with large regional healthcare customers. Ecotex has an exclusive focus on the healthcare market, our focused approach has propelled our expansion and healthcare subject matter expertise.Ecotex supports both urban and rural healthcare facilities, ranging from hospitals to long-term care centers. The Ecotex team is comprised of 1,700 employees producing millions of hygienically clean hospital linens each year.
Bob Cusack to Share Political Insights at TRSA’s 14th Annual Legislative Conference
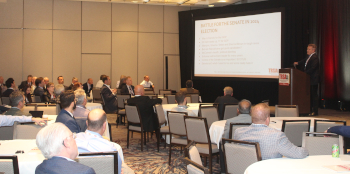
The TRSA 14th Annual Legislative Conference and Annual Awards dinner in Washington, D.C., Apr. 10-11, 2024, is described as providing members a chance to meet U.S. legislators in person to establish relationships and help educate the legislators on the issues that are important to the linen, uniform and facilities industry.
The day before the Legislative Conference, a workshop for supplier partner members will be lead by Ben Kniffen, CEO of LinkedSelling . Kniffen will offer skills and tools that will enable sales teams to place the right message in front of the right person through the right channels and develop a sales process that ties everything together. Supplier Partners will collaborate with other suppliers and gain knowledge in a non-competitive setting.
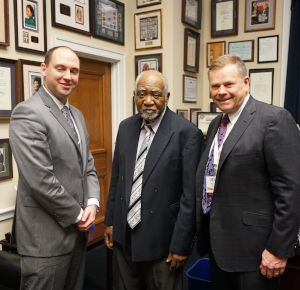
The conference agenda kicks off with an afternoon of TRSA committee meetings, followed by an opening keynote, a Hill Day issue briefing, and the Annual Industry Awards reception and dinner that evening. The following day attendees will meet at the Capitol Hill Club for breakfast and a briefing before heading out to congressional meetings.
Keynoter Bob Cusack, the national policy and politics analyst and editor-in-chief of The Hill newspaper, will share his political perspective on Capitol Hill, including his take on this year’s federal elections in the U.S. House, Senate, and the presidency. Drawing on his extensive institutional knowledge from his time on Capitol Hill, Cusack will provide insights into the current political climate and expected changes following the 2024 election cycle. Following the keynote, TRSA Vice President of Government Relations Kevin Schwalb will prep attendees for Hill meetings providing the latest Hill intel and talking points that members can use during the legislative meetings.
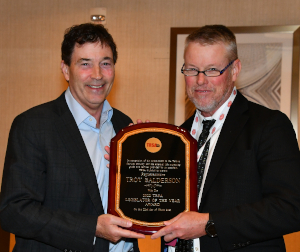
TRSA’s Industry Awards Dinner will include a celebration of industry creativity and excellence. Recognition of exemplary efforts of employees and leaders of member companies, both operator and supplier member, will highlight the evening. Awards include:
- Above and Beyond Service Award
- Best Plants of The Year Award
- Clean Green Innovation Award
- Company Community Service Award
- Diversity Recognition Award
- Fleet Graphics Award
- Legislator of the Year Award.
- SafeTRSA Safety Excellence Award.
- TRSA Volunteer Leadership Award
While attendees will be meeting with congressional teams on April 11, spouses and partners traveling to Washington, DC for the conference are invited to visit Marjorie Merriweather Post ‘s Hillwood Estate, Museum and Gardens for a private tour and afternoon tea. The Hillwood Museum features the fullest and most exquisite collection of Russian imperial pieces outside of Russia, including a stunning collection of Faberge eggs.
Registration is currently open and attendees can save $100 if they register before March 1. Visit www.trsa.org/legcon for more information.
DLI Online and In-Person training for Spring 2024
The Drycleaning & Laundry Institute continues its relentless drive to educate dry cleaners in the best practices for their businesses, from marketing to building a team, to training floor employees in better performance of their jobs. Here are some recent successes, and an opportunity for online education.
January 17, 2024 — How to Create a Team that Operates and Grows Your Company Without You
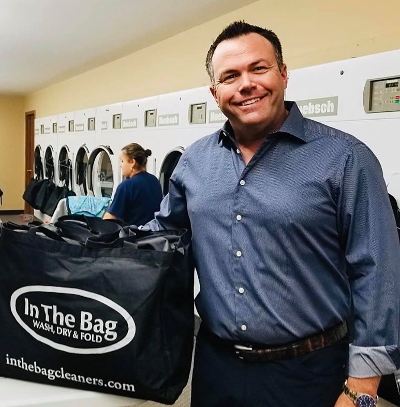
Dave Coyle of Maverick Drycleaners will present online on the topic of giving yourself freedom from day-to-day operational management by building a team that does the job as well as — if not better — than you can.
Learn more at DLIonline.org.
All Hands to the Press
DLI regularly graduates newly-trained students from its hands-on dry cleaning courses. The following individuals have successfully completed the beginning and/or advanced courses.
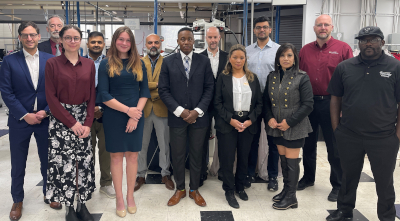
Front row (left to right): Colby Schapiro, Wedding Gown Preservation Co., Endicott, NY; Mary Kenney, Crown Cleaners, West Des Moines, IA; Isabella Giles, Glyndon Lord Baltimore Cleaners, Glyndon, MD; Keith Lowry, Warner’s One Stop, Basseterre, St. Kitts; Carlita Torres-Collins, La Nuova, Inglewood, Taranaki, New Zealand; Maria Hernandez, Avon Cleaners, Dallas, TX; Shermondez Wise Sr., Varsity Cleaners, Inc., Waterloo, IA.
Back row (l-r): Beau Williams, Puritan Cleaners, Richmond, VA; Yash Amin, Frankford Cleaners and Shirts, Penndel, PA; Mike Malek, Zesty Cleaners, LLC, Kennesaw, GA; Lance Frizzell-Reynolds, Wedding Gown Preservation Co., Endicott, NY; Nabeel Saleheen, NSquared, Duluth, GA; Jeff Chapman, Classic Cleaners, Indianapolis, IN.
Not pictured: Emmanuel Lassiter, Nu Royal Cleaners, Newport News, VA.
Yash Amin, Jeff Chapman, Lance Frizzell-Reynolds, Mary Kenney, Mike Malek, Nabeel Saleheen, Colby Schapiro, and Beau Williams attended the course at no cost as part of their DLI Premier Membership.
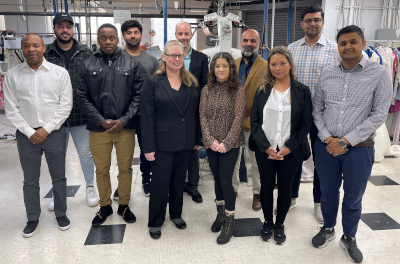
Front row (left to right): Brian Johnson, DLI Director of Education & Analysis; Keith Lowry, Warner’s One Stop, Basseterre, St. Kitt’s; Ashley Persails, Jan’s Professional Cleaners, Clio, MI; Amber Edwards, Crown Cleaners, Ankeny, IA; Carlita Torres-Collins, La Nuova, Taranaki, New Zealand; Yash Amin, Frankford Cleaners and Shirts, Penndel, PA.
Back row (l-r): Anas Zahir, Connels Valet, Vienna, VA; Haroon Malik, Connels Valet, Vienna, VA; Lance Frizzell-Reynolds, Wedding Gown Preservation Co., Endicott, NY; Mike Malek, Zesty Cleaners, LLC, Kennesaw, GA; Nabeel Saleheen, NSquared, Duluth, GA.
Not pictured: Emmanuel Lassiter, Nu Royal Cleaners, Newport News, VA, and Ashley Persails,Jan’s Professional Cleaners, Clio, MI.
Yash Amin, Amber Edwards, Lance Frizzell-Reynolds, Mike Malek, and Nabeel Saleheen attended the course at no cost as part of their DLI Premier Membership.
Upcoming training
Tuition for DLI’s On-Site Advanced Drycleaning Course is $2,195 for non-members. DLI members receive discounts ranging from 20% off to absolutely free depending on membership level.
Fabricare Canada, awards scholarships to Canadian industry members each year. To apply, send an email to Becca Anderson (becca@fabricarecanada.com) explaining your connection to the industry, stating that you are over 18, speak English, and can travel to the training. You must live in Canada, work in a dry cleaning or wet cleaning plant, speak English and be able to cover your housing and meal costs (except daily lunches, which are provided.)
Spring 2024
385th One-Week Introduction to Drycleaning Course, March 4 – 8
385th Two-Week Advanced Drycleaning Course, March 11 – 22
Fall 2024
386th On-Site Introduction to Drycleaning Course, October 7 – 11
386th On-Site Advanced Drycleaning Course, October 14 – 25
On-Site General Drycleaning Course
Students taking DLI’s On-Site Introduction to Drycleaning and On-Site Advanced Drycleaning Courses together enjoy a reduced tuition rate of $2,895 per student for non-members. DLI members receive discounts ranging from 20% off to absolutely free depending on membership level.
Virtual Stain Removal Course
DLI is offering three sessions of its Virtual Stain Removal Class covering everything from fiber identification and characteristics to stain removal chemistry and procedures to using bleaches and specialty products such as digesters, amyl acetate and acetone to assist in the spotting process.
Classes meet virtually over seven days. Attendance at all seven sessions is required to achieve a passing grade in the course. Classes meet on Tuesdays and Thursdays and are represented by week below.
Spring 2024 Virtual Stain Removal Course
April 30, May 2
May 7, 9
May 14, 16
May 21
Summer 2024 Virtual Stain Removal Course
July 9, 11
July 16, 18
Visit dlionline.org for more information on courses or to apply.
DECEMBER 2023 NEWS
K-BRO ANNOUNCES CLOSING OF VILLERAY ACQUISITION
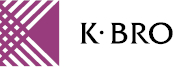
K-Bro Linen Inc. of Edmonton, AB announced that it has successfully completed its acquisition of Buanderie Villeray and its affiliate Buanderie La Relance (together “Villeray”) for an enterprise value of $11.5 million and a potential earnout of $1 million. Villeray is a private laundry and linen operator centrally located in Montréal and serving the healthcare and hospitality markets with annual revenues of approximately $10 million.
K-Bro will invest a further $5 million in capital expenditures to expand capacity and enhance operational efficiencies, enabling our Montreal business to significantly and profitably grow. As part of the transaction, K-Bro will close its Granby facility and consolidate its volumes into Villeray. K-Bro anticipates that the integration of its existing Granby operations into Villeray will be completed by the end of Q2 2024. The purchase price and capital expenditures will be satisfied by drawing down on K-Bro’s revolving credit facility.
“Our acquisition of Villeray enhances K-Bro’s position within the attractive Montréal market. Villeray’s modern plant is strategically located in close proximity to customers, and we are investing to expand capacity, consolidate volumes, enhance operating efficiency, reduce fixed costs and support significant growth opportunities,” said Linda McCurdy, President and Chief Executive Officer at K-Bro.
“The Villeray acquisition is another example of our strategy of acquiring high-quality operators with leading market positions enabling K-Bro to grow market share in key regions. As we emerge from the pandemic, we are excited about our outlook. We continue to have an active M&A pipeline and remain well-positioned from a balance sheet and liquidity perspective to fund acquisitions, organic growth and our normal course issuer bid,” McCurdy said.
For further information, visit www.k-brolinen.com.
Healthcare Laundry Leaders Share Insights on Innovation and Trends at TRSA Conference
TRSA (Textile Rental Services Association), the association for linen, uniform and facility services, recently held its 12th Annual Healthcare Conference and Exchange on Nov. 15–16 in Memphis, TN. The event brought together industry leaders and experts to share insights and best practices on serving the healthcare market sector.
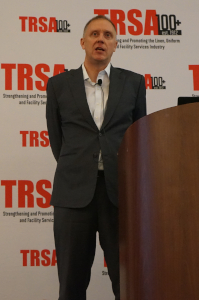
The conference featured a keynote session by Nathan Bays, a healthcare M&A specialist at Citi, who discussed the latest trends and opportunities in the healthcare economy. Bays also shared insights on how healthcare operators can optimize their performance and deliver more value to their customers.
Following the keynote, a panel of technology experts from LinenMaster, Ecotex Healthcare Linen Services and NOVO Health Services shared their experiences and tips on using technology to enhance customer satisfaction and retention. The panel was moderated by Daniel Sanchez, the vice president of sales and marketing at Emerald Textiles.
The conference also included a presentation by Dr. Katie Laird, the head of infectious disease research at De Montfort University. She explained the current and emerging methods of microbiological testing in the commercial laundry industry. Kevin Schwalb, the vice president of government relations at TRSA, provided an update on the organization’s advocacy efforts and the key regulatory issues affecting the industry.
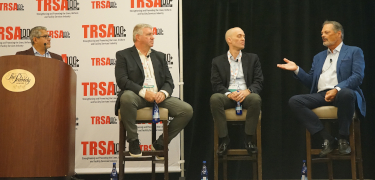
Chuck Rossmiller, the senior director of national field sales at Medline, presented the findings of the TRSA Healthcare Committee’s healthcare trends survey, which revealed the latest data and trends in the healthcare linen market. Rossmiller also engaged the audience with interactive live polling to get their feedback on the survey results.
The attendees had the opportunity to choose from two breakout sessions, one focusing on linen-loss prevention in the acute-healthcare sector, and the other on employee- engagement strategies in the nonacute healthcare sector.
The first day of the conference concluded with two more panel discussions. The first featured executives from Crothall, Ecotex Healthcare Linen Services, HHA-FMA Laundry and HandCraft Services. These company leaders shared their perspectives on the challenges and opportunities of serving the healthcare market, both acute and nonacute. The panel was moderated by Liz Remillong, vice president of strategic alliances at Crothall. Alsco Uniforms’ Healthcare Marketing Manager, Sara Oser, found the panel to be the most-engaging session. “It was like a crystal ball into the future of laundering. Navigating through this insightful session not only gave us a sneak peek into where the industry is headed but also served as a compass on how to best target our market.” Oser added, “Exciting times are ahead for those who dare to follow the trends.”
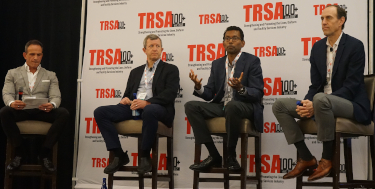
The second panel featured investment bankers from CIBC U.S. Middle Market Investment Banking, Stephens Inc. and Piper Sandler, who spoke on the role and impact of private equity in the healthcare linen industry. The panel was moderated by Andy Kratky, CEO of Emerald Textiles.
Healthcare conference attendees got a benefit by participating in the Exchange, TRSA’s online planner tool which allows attendees to efficiently schedule 15-minute, customized in-person meetings between TRSA Operator Members and Supplier Partners. The Exchange earned positive reviews from attendees such as Dan Flaherty, senior energy consultant, APPI Energy. He described the Exchange as, “a highly valuable and unique tool for members to connect with service providers.”
The conference concluded with a tour of Medline Industries’ facility in Southhaven, MS. There the attendees saw a 1.2-million-square-foot, medical-grade distribution center that serves over 1,000 healthcare facilities in the region.
Next year’s TRSA Healthcare Conference will be held at the Westin Buckhead in Atlanta on Nov. 13-14, 2024. Learn more at trsa.org/healthcaresummit.
NOVEMBER 2023 NEWS
TRSA Marketing, Sales & Service Summit Continues to Expand
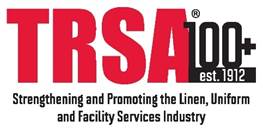
Memphis, Tenn., was the location for the 6th Annual Marketing, Sales & Service Summit, the most well-attended Marketing Summit to date. Adding service to the mix for the first time reinforced the importance of a team approach to customer satisfaction and retention in the linen, uniform and facility services industry.
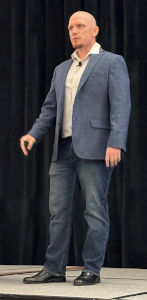
In his keynote address, Ben Kniffen, the CEO of Linked Selling, expanded on the success formula of hitting the right person with the right message with the right delivery through tools and practices that he calls, “The Ultimate Client Acquisition Playbook.” Kniffen returned for one of the breakout sessions that focused on marketing and how to combine the best mix of LinkedIn, SEO, paid ads and other channels to create unbeatable omnichannel marketing campaigns.
A two-part breakout session titled, “The Service Side of Sales and the Sales Side of Service,” with Steve Royals and Ray Shabandarian, both from Performance Matters, discussed creating a balance between sales and service and how to apply service skills to sales and apply sales skills to service. A hands-on group exercise had attendees break into small groups to create, review and present a new account installation check list.
Ed Kwasnick, director of business development, ARCO/Murray, defines a trusted adviser as someone whose judgment and perspective rate highly in multiple capacities. Kwasnick delivered a general session expanding on the three keys to creative value-based customer relationships: expertise, transparency and solutions.
During the breakout session for video marketing, Ashley Carroll, Prudential Overall Supply, and Emily Hauber, CITY Laundering, compared the processes of in-house vs. outsourced video production and walked through a 10-step checklist needed for success regardless of the platform you choose.
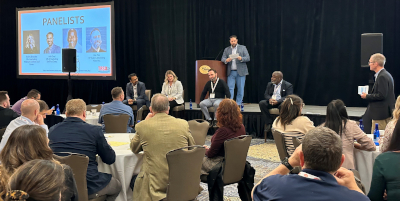
The final session ended with a lively panel discussion that featured some of the top marketing talent from several operators in the linen, uniform and facility services industry, sharing their stories of successes, as well as challenges and where they see the industry heading. Panelists included Kelsey Breeden, director of marketing, Wildman Uniform and Linen; Asit Goel, VP of marketing, UniFirst Corp.; Tracy Chamblee, VP of marketing, Nixon Medical; and Ben Fox, VP of sales & marketing, Alsco Inc.
One of the most requested sessions was Conversation Starters, where attendees can sit with other operators and suppliers in small groups and share views about specific topics in the industry.
The culminating event of the summit is the awarding of the “Best-of-the-Best” marketing idea, a fun contest between attendees who share one of their successful ideas throughout the day. Attendees all vote and Alsco Uniforms’ video highlighting their top sales performer in a spin-off of Indiana Jones was selected as the winner.
“This year’s Marketing, Sales & Service Summit was the best to date that I have attended,” said CITY Laundering’s Director of Communications Emily Hauber. “The speakers and the breakout sessions were diverse and left me with some good takeaways.”
Kasey Wahl, sales and marketing director, Amtex Innovations, added that, “It’s great to see how many people continue to value the information they receive at this conference and come back every year.”
Next year the event will be at the Westin Buckhead in Atlanta on Nov. 12, 2024. Learn more at trsa.org/marketingsummit.
IAHTM Names Angela Becker its 2023 “Don Pedder Lifetime Achievement Award” Recipient
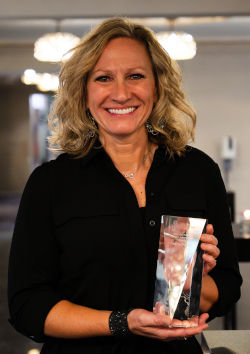
The International Association for Healthcare Textile Management (IAHTM) has named Angela Becker
its 2023 “Don Pedder Lifetime Achievement Award” recipient. The award was presented at IAHTM’s Annual Education Conference held at The Omni King Edward Hotel in Toronto.
Angela Becker, who has been working at Ecolab for 28 years, plays a pivotal role in driving innovation, sustainability, and efficiency within the commercial laundry market. Over the course of the last 12 years, she has held critical director roles in R&D and Marketing within the Textile Care Division. Steve Fox of Ecolab stated that Becker’s roles have truly advanced Ecolab’s vision of what is vital: clean water, safe food, and healthy environments.
Angela Becker serves on the TRSA Hygienically Clean Board and has presented at many industry events, including IAHTM, The Clean Show, ALM and Western Textile Services Association. Becker has been published in multiple laundry trade association publications and holds commercial laundry patents at Ecolab that will yield as much value in the future as they do today.
Beyond her many accomplishments at work, Angela is a parent to three boys. Steve Fox stated that one of the qualities he admires about Becker is how she has mastered the art of doing the meaningful things, not only at home and work, but in her community, as well. He stated that she is very passionate about volunteering in her community and was just awarded the Volunteer of the Year Award from the city of Saint Paul, MN foundation.
IAHTM congratulates Angela Becker, this year’s award recipient, and thanks her for the many contributions she has brought to the industry.
IAHTM is a nonprofit membership organization for healthcare laundry cooperatives that provides senior-level textile managers with resources and support to maximize their laundries’ efficiencies and control costs without compromising quality or patient focus. To learn more, visit IAHTM.com.
Methods for Management Celebrates 70th Anniversary at Success 2023
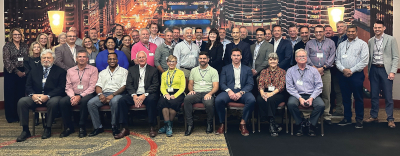
Methods for Management (MfM), a leading management consulting firm, recently celebrated its 70th anniversary in style. Their members, guests, and industry experts gathered at The Hilton Chicago Magnificent Mile Suites from October 26th – 28th for Success 2023.
Founded in 1953 by Max Rechnitz and later joined by his daughter, Deborah Rechnitz, in 1980, MfM has become a trusted partner for independent business owners pursuing their personal and business goals. Today, the firm is led by Managing Partner Kermit Engh, who joined MfM in 2014.
Success 2023 offered attendees an opportunity to connect with industry peers, interact with leading vendors, and gain invaluable insights from distinguished speakers. Keynote speakers included Steve Baker from The Great Game of Business who gave two presentations: “The Great Game of Business with Mini Games” and “Quality Time Remaining.” Jeff Butler, speaker, author, and workplace strategist, spoke about “Winning the Talent War.”
Featured speakers included Jennifer Whitmarsh, a Customer Service Pro, who shared “Keys to a Successful, Thriving Workplace Culture.” Bob Clements, Co-founder of Benchmark Business Group, discussed “Realizing Value: Whether It be by Luck or by Your Own Design.”
In addition, the conference featured an impressive list of industry speakers, including Toran Brown, Vice President of SPOT; Nathaniel Dubasik of Metalprogetti; Cohen Wills of Cleaner Marketing; Wesley Nelson of Sankosha; and Jeff Gude, MfMBI. Representatives from industry-leading POS systems SPOT and SMRT also hosted breakout rooms for users to learn about updates and ask questions.
Nadine Rana, owner of Style and Grace Cleaners in Toronto, praised the event: “I’ve never felt more cared for after leaving the 70th MFM Success meeting of 2023! This conference truly surprised and delighted our management team beyond our expectations! This year’s phenomenal line-up of world-renowned keynote speakers certainly empowered us with tangible tools to develop a limitless mindset.”
The event had a packed agenda, starting with a welcome cocktail reception on Thursday evening, followed by two full days of speakers and interactive sessions. Saturday evening saw members and guests attending the Awards cocktail hour and dinner, where accolades for Best Van Design, Best Store, and Best Social Media Campaigns were awarded. During the awards dinner, attendees heard heartfelt words from Diana Vollmer, the former managing partner of MfM. Additionally, Kermit Engh presented some new features and additions to member services that will roll out in early 2024.
Kathy Benzinger of Benzinger’s Clothing Care echoed similar sentiments about the event: “The location was beautiful, and so was the event. It was professionally run, with great speakers and topics and fantastic food. But the most impressive part of the event was the celebration of 70 years, which was awe-inspiring. I left the conference feeling grateful for my MFM membership and the opportunity to make new MFM friends and visit old ones.”
“The event was a resounding success,” said Kermit Engh, Managing Partner at MfM. “The caliber of speakers combined with the enthusiasm of attendees made for a truly memorable 70th-anniversary celebration. We’re excited to see how attendees will implement the powerful knowledge shared in their businesses and personal lives.
“Success 2023 was a fantastic industry event with excellent participation from the MfM community and alums and generous support from friends in the industry. Celebrating this critical milestone together was invigorating, and we look forward to 70 more years of success.”
TRSA’s Regional Production Summits
Three Dates, Three Cities, One Agenda
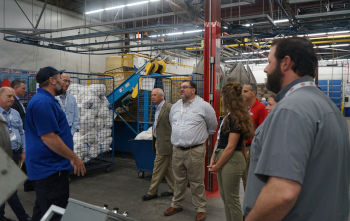
The Textile Rental Service Association is bringing its popular production summits and plant tours closer to its members, allowing members to choose from three regional locations on three different dates. Each TRSA Regional Production Summit will have the same insightful speakers covering important topics. Production Managers and GMs from local areas will combine for engaging panel discussions, and there will be informative plant tours for each Regional Production Summit.
The West Coast Summit will be the first in the series on Jan. 24-25, 2024, at The Palm Casino Hotel and Resort, Las Vegas, NV. TRSA is teaming up with Wisconsin Association of Textile Services (WATS) for the Midwest Summit, slated for May 1-2, 2024, at the Hyatt Regency, Milwaukee, WI. The final Regional Production Summit will be held Oct. 15 – 16, 2024, at the Newark Liberty International Airport Marriot, Newark, NJ, offering plants from the Northeast easy access to the summit.
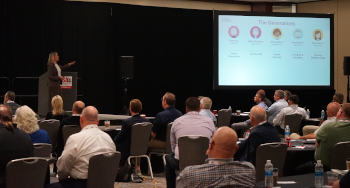
Nancy Roberts, CEO & Founder, The DISC Wizard, will offer a keynote address for all three summits focusing on emotional intelligence. “Numerous studies have confirmed that 90% of top performers in all fields have high emotional intelligence,” Roberts said. Her keynote will dig deeper into why emotional intelligence is such a crucial factor in personal and professional success, and how employees can be come more emotionally intelligent.
General sessions with consistent speakers across all three regions will cover these topics:
o Production managers roles in preventative maintenance
o Fire safety strategies for prevention
o Leadership and Decision Making: Are you captain or crew?
o Process improvement and root-cause analysis
o Facilitated roundtable discussions focusing on regional issues, fire safety, production scheduling and leadership development
An interactive panel discussion made up of general managers and industry executives from the local regions will round out each summit. Closing out each summit will be two local plant tours per region. Debriefing with plant-management personnel and other tour attendees following the tours allows for comparison of practices and further insight into these efficiently run plants and is always viewed as a highlight of the summit.
Registration is currently open, and more details can be found at trsa.org/productionsummit.
GreenEarth/DLI Host Online Workshop Nov. 11
Open to all who wish to participate
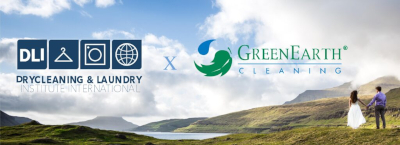
GreenEarth is teaming up with DLI (Drycleaning & Laundry Institute) on November 11 for a virtual workshop highlighting the “Sustainable Garment Care Revolution: GreenEarth x DLI Showcase”. Anyone who wishes to participate in the virtual event is welcome to do so.
Topics to be covered in the course of the event include:
- GreenEarth Affiliate Update (Tim Maxwell)
- Elimination Waste Disposal Costs with Optimized System (Andy Lien)
- Grow Your Business by Connecting with Today’s Customer (Karen Maxwell)
- Differentiate Yourself in the Market, Marketing Plans (August Garcia/Erin Horne)
- Branding Your Business (Ken Sandy)
- Machine Maintenance Sustain, Prime & ACF (Andy Lien)
- Q&A
To participate, go to the link and follow directions.
CINET Preparing for 2024 Global Best Practices Event
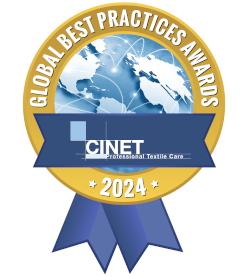
CINET, the European fabricare association, has hosted a Global Best Practices competition for the past five years. Some Canadians have ranked high in the contest. It takes a good bit of effort to compete, including completing a detailed explanation form about your company, producing a video or other presentation, etc. So now is the time to start working to show how great your company is doing! Here is the notice from CINET:
World PTC Congress & GBPA 2024
Meeting the World’s Finest, the World’s Best
New Business, Innovation & Social Responsibility
Following five successful International events with hundreds of participants and thousands of followers, CINET is now making preparations for the next edition scheduled for November 8 and 9 2024 at Texcare International in Frankfurt, Germany.
We had a wonderful Global Best Practices Event in 2022 in Milan. Please find a link to the After movie of 2022 here. Not only the winners, but also the other participants were extremely enthusiastic about this event. They have had exiting experiences with colleagues of other countries and were able to take tools to their own organization for implementing ideas and making investments in new opportunities. This event was streamed worldwide and the winners were profiled extensively in the trade press, journals, media & TV around the world (see also the NewsLink: Global Best Practices Awards 2022 (cinet-online.com)).
World Congress
Now CINET has started preparations for the 6th Edition in Frankfurt, this time accompanied by the First PTC (Professional Textile Care) World Congress of this kind, to profile modern Professional Textile Care to the industry, clients and stakeholders. The potential of the PTC industry to contribute to economic, social and circular development will be highlighted for a world audience and demonstrated by the best performing companies from all over the word.
CINET expects:
- Delegations from some 60 countries,
- 300 attendants,
- 200 participants
- An online reach of about 25,000 professionals worldwide.
The conference will be multilingual, including Special Country Editions, and will be streamed to all major markets worldwide.
Organization
For the next edition CINET invites national associations from all parts of the world to cooperate via a co-host arrangement and present the PTC industry at its best.
- Bringing the most advanced knowledge and services together in an exceptional program.
- Provide great inspiration for PTC companies to develop their business in difficult times.
- Present the capabilities of the PTC industry to be known and recognized for their contribution in society.
- Demonstrate how innovations can lead to sustainable profitable businesses.
Best Showcases in PTC
Market disruptions and accelerated innovation require true entrepreneurship of management teams in modern retail and industrial textile service companies. Visitors are offered an unforgettable “WOW” experience in many ways: personal contacts with like-minded professionals, inspiring business ideas and set ups, loads of information of initiatives and businesses set up in other countries and a positive impact on their current business, as well as PR to their customers.
The winners will be selected by an independent international jury of some 25 professionals, and evaluated according to the market situation of their own country.
Registration is possible via this link for Registration GBPAP 2024. It will include one free admittance ticket for the Texcare International Show, one of the biggest international trade shows for the PTC industry, as well as a free admission ticket to the Official Presentation Program of finalists on November 9th, 2024 in Frankfurt.
For more information please visit the CINET website: www.cinet-online.com or contact the CINET-secretariat: cinet@cinet-online.com or phone: +31 344650430.
OCTOBER 2023 NEWS
TRSA’s 110th Annual Conference
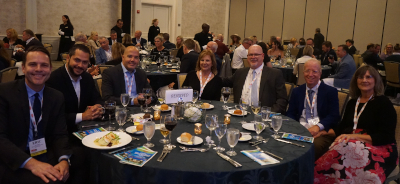
The Textile Rental Services Association (TRSA) held it’s 110th Annual Conference Oct. 10-12 at The Ritz-Carlton Tiburon Golf Resort Hotel in Naples, FL. Nestled between the beach and the golf course, the conference connected key linen, uniform and facility services industry leaders, allowing an opportunity to mix professional development and industry updates with several networking opportunities including an interactive charcuterie building challenge, the TRSA Open Nine-Hole Golf Tournament and an optional brewery tour.
UniFirst’s Executive Vice President Michael Croatti, who has attended four Annual Conferences, enjoys attending the TRSA Annual Conferences for the chance to network and learn from others. He was impressed by the 2023 Naples location and said, “It was a great destination, with good networking opportunities, fun team building events and valuable insights. I took three pages of notes.”
The 110th Annual Conference’s agenda offered a wide range of general and breakout sessions, including a pair of keynote speakers. Walter Bond, a former NBA player who is now a motivational speaker, best-selling author, business coach and co-founder of a leading professional training and development organization, talked about using motivation to overcome obstacles that stand in your way, allowing your business to generate momentum toward winning.
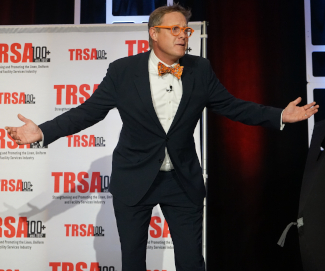
The second keynoter, Andrew Davis, CEO, Monumental, has been recognized as one of the industry’s “Jaw-Dropping Marketing Speakers,” and is a mainstay on global marketing influencer lists. Davis has crafted documentary films and award-winning content. During his keynote session, titled “The Cube of Creativity: Why adding constraints sparks innovation, action and delivers out-sized results,” Davis discussed how some threats help spark creativity and innovation.
Four breakout sessions at the conference included the following topics:
- Hiring and retention
- A panel of Environmental, Social and Governance (ESG) experts
- Economic and Industry Update from the Robert W. Baird Facility & Industrial Services Research Team and Andrew Wittmann CFA, director, senior research analyst
- Intelligent business growth
Attendee Jim Buik, president and owner of Roscoe Co., was impressed with the AI general session, Artificial Intelligence (AI): From Sci-Fi to Production and Profitability that Charles Irizarry led. Buik stated, “I picked up some great ideas from Andrew’s session.”
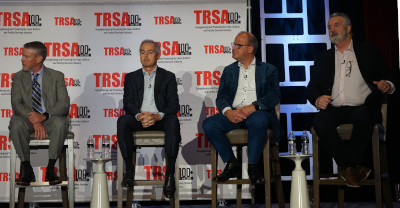
A global panel included Hartmut Engler, managing director, CWS Workwear International, Duisburg, Germany; Ray Hayes, executive director – innovation & capability, Specialized Linen Services, Victoria, Australia; Jim Kearns, executive vice president, Alsco Inc., Salt Lake City; and Xavier Martiré, CEO, Elis Group, Saint Cloud, France. The panel focused on industry growth from a global and local perspective. Buik added, “Ray (Hayes) provided the best insights that a local independent could use.”
During the State of the Association and Annual Membership Meeting, TRSA leaders provided an annual update on the association’s finances and member-driven initiatives. At the meeting, attendees saw the re-election of three board members – Brian Herington, PureStar Group, Las Vegas; Liz Remillong, Crothall Laundry Services, Huntersville, NC; and Steve Sintros, UniFirst Corp., Wilmington, MA – as well as the election of new board members Theresa Garcia, Division Laundry and Cleaners, San Antonio; and Josh Wildman, Wildman Uniform and Linen, Warsaw, IN.
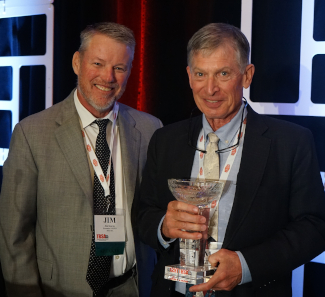
During the meeting, attendees also gained insight into the development of TRSA certification programs, in-person and virtual events, information-sharing opportunities and industry-specific training.
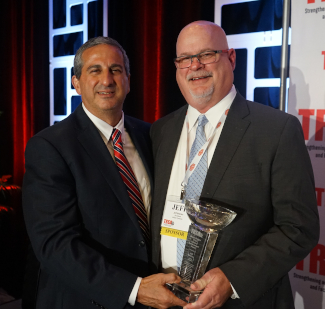
The 110th Annual Conference also offered Industry Awards recognition, including the Operator and Supplier Partner Lifetime Achievement Awards. Jim Vaudreuil, president, Huebsch Services, Eau Claire, WI, accepted the Operator Award, while Jeff Belcher, the former president and owner of Alliant Systems, Irving, TX, was selected as the Maglin-Biggie Lifetime Achievement Award honoree for supplier-partner executives. For more information, visit www.trsa.org/awards.
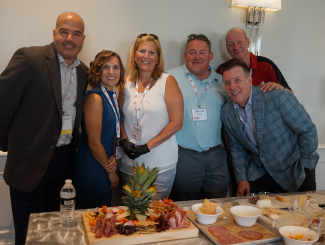
The event kicked off with a Supplier Partner Council meeting and welcome reception for all attendees. Activities for spouses and/or significant others included a welcome meet and greet, morning yoga class on the beach and a chef-led cooking class. Sponsors of the event included Royal Basket Trucks, JENSEN USA Inc., Kannegiesser ETECH, Ellis Corp., Pellerin Milnor Corp., Unitex International Inc., G.A. Braun Inc., Brim Laundry Machinery Co. Inc., Lavatec Laundry Technology Inc., Monarch Brands, Alliant Systems, ARCO/Murray and The Clean Show presented by Texcare.
Kasey Wahl, sales and marketing director, Amtex Innovations, summed up the conference by noting that, “The conference was great, the keynote speakers were awesome, breakout sessions fantastic and the networking is unbeatable. I highly recommend coming to the Annual Conference.” Next year, the 111th Annual Conference will take place Sept. 24-26 at the Broadmoor, Colorado Springs, CO.
How does your laundry stack up?
ALM Launches Benchmarking tool
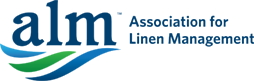
The Association for Linen Management (ALM) has launched its industry benchmarking platform for 2023 – LaundryMarksTM by ALM. The comprehensive, easy-to-use, secure and valuable platform collects data from laundry operations and generates data and insights so operators can make more informed decisions to improve their business performance for single- and multi-location laundries.
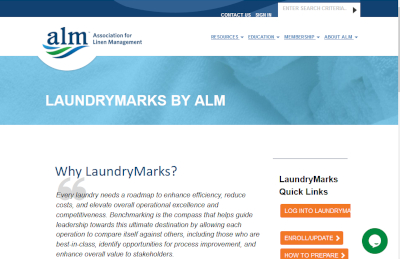
All laundries are invited, and encouraged, to enroll in LaundryMarks and submit their company’s data from Oct. 14 – Nov. 17 via the portal – laundrymarks.org. Participation is free, and each participating laundry will have access to real-time benchmarking data and custom reports.
“We modified the portal to improve useability and now provide real-time data to all participants,” said Sarah Brobeck, RLLD, executive director, ALM. “We are passionate about helping the laundry industry succeed and feel that benchmarking is a powerful tool for improving operational performance. It provides a clear picture of where your operation stands in relation to its goals and competition, as well as helping identify opportunities for improvement.”
The 2023 LaundryMarks by ALM collects financial and operational data from 2022. All data is validated by a third-party within 24 hours of submission, and participants will get real-time data access to industry-specific key performance indicators in production, workforce efficiency, utilities, safety, quality and profitability. Data entered is anonymous, encrypted and stored on a secure server. It will only be shared in aggregate via the portal.
“The real value of LaundryMarks comes from the information provided, so we need participation from members within the laundry industry,” added Brobeck.
All laundry operations regardless of industry, size or ALM membership status can participate in LaundryMarks by ALM by visiting the website.
TRSA adds two new Directors
Textile Rental Services Association (TRSA), the association for linen, uniform, and facility services, hosted the election and swearing in of five Directors Oct . 12 during the business meeting at its 110th Annual Conference in Naples, FL.
The TRSA Nominating Committee Chaired by Immediate Past Chair Noel Richardson and including Vice Chair Randy Bartsch, Ecotex Healthcare Laundry; Treasurer P.J. Dempsey, Dempsey Uniform & Linen Supply; and Director Jimmy Arnett, Workwear Outfitters; had recommended a slate of Directors for re-election to serve a second three (3) year term (October 2023 – 2026). TRSA members at the business meeting voted in favor of the slate, which included:
- Brian Herington (PureStar)
- Liz Remillong (Crothall)
- Steve Sintros (UniFirst)
Two first term directors were also elected:
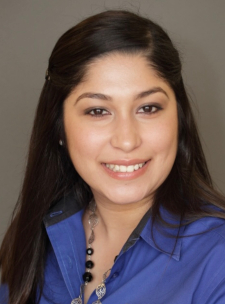
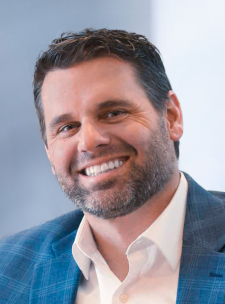
- Theresa Garcia (Division Laundry)
- Josh Wildman (Wildman Uniform & Linen)
Garcia and Wildman served on the TRSA Strategic Planning Committee and represent the next generation of leadership at their organizations.
“We are pleased to welcome Theresa Garcia and Josh Wildman as new members of our board, and congratulate Brian Herington, Liz Remillong and Steve Sintros on their reelection. We look forward to working with them in the coming year to continue advancing our mission and serving our members,” said Joe Ricci, TRSA CEO and Chairman. “Their unwavering commitment to the industry is truly remarkable.”
For more information on TRSA, visit the website.
CINET holds International Workshop in Toronto
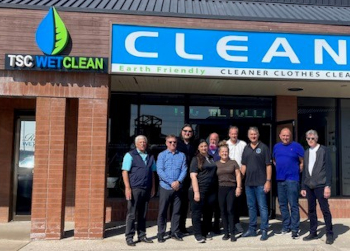
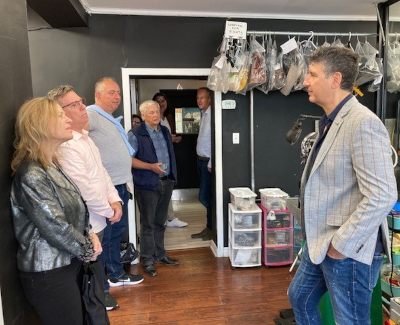
CINET (the European fabricare association) organized workshops on wet cleaning, leather cleaning and carpet cleaning in Toronto September 27-29. This initiative was intended to explore the possibilities for education and training, as well as profiling modern services to specialty markets.
Workshop hosts were TSC Wet Cleaning, owned by Dino Kantzavelos, and Love Your Rugs and Carpets, owned by his brother, Tony.
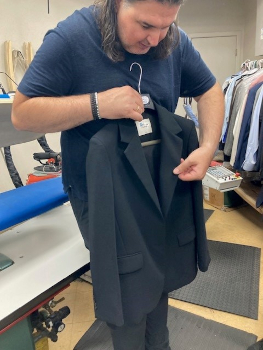
The excellent tour through the plants and open discussions on every aspect of the business and processing of the items was highly appreciated by all participants.
They provided insight into their companies’ philosophy and activities, and their commitment to service their customers with the highest retention rates possible.
Report courtesy of CINET.
Cintas acquires Rental Uniform Service
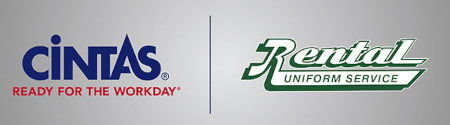
Cintas Corp., Mason, OH, recently acquired Rental Uniform Service, a North Carolina-based, family-owned and operated uniform and facility services rental business.
Rental Uniform Service was founded in 1949 by James Waggoner. Currently, Waggoner’s grandson, Danny Lawrence, serves as the company’s CEO. Waggoner’s four daughters also are involved in leading the company, which serves customers in North Carolina, South Carolina and Tennessee through two locations: its original Statesville, NC, facility and its Gastonia, NC, plant.
“The Waggoner and Lawrence family has been a regional leader in this industry, and we’ve always respected how they’ve run their business,” said Scott Garula, president and COO of Cintas’ Rental Division. “The family built a company that delivers outstanding quality and service to their customers, which has generated tremendous customer satisfaction and retention. We look forward to adding talented and dedicated employee-partners to our organization. We have very similar operating philosophies and cultures, which will also help the transition for their customers and staff.”
Danny Lawrence, CEO of Rental Uniform Service, added that, “This business has been incredibly important to our family for decades, so it’s bittersweet to leave the industry. Our family has tremendous respect for Cintas. They run a first-class business and put their focus on their customers and their employee-partners. Our companies have strong alignment on values, making Cintas the obvious decision to work with during this transition.”
Report courtesy TRSA.
Don’t Leave Money On the Table
DLI’s November webinar will help U.S. cleaners file for employee tax credits
Small businesses in the States are still able to collect Employee Tax Credit money from the U.S. government. The Drycleaning & Laundry Institute will host a program on November 8 at 1 p.m. Eastern time to help member dry cleaners file for this benefit before time runs out.
Bringing the dry cleaning and laundry community together, DLI hosts weekly coffee-and-shop-talk meetings every Tuesday on Zoom so members can discuss what’s happening.
November 2023 Live Virtual Education Program
DLI presents the following virtual training schedule for November 2023.
- November 1 –New DLI Member Virtual Welcome Reception and Orientation
- November 8 –Money on the Table: File for ERC Before the Deadline
- November 15 – Marketing Lab Virtual Roundtable Discussion
For more information: https://www.dlionline.org.
CFA Preliminary Conference Report
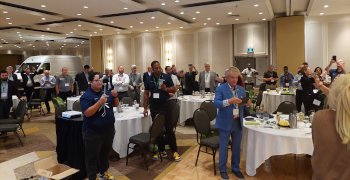
We asked Sid Chelsky, Executive Director of the Canadian Fabricare Association, for a brief report on the convention that was held September 29-October 1.
NOTE: This is a preliminary report. A full report is on the way, so please check back.
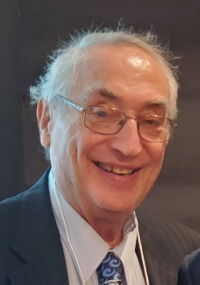
This conference was one of the most successful conferences that we have ever had. The attendance was higher than usual, and we had people join us from as far away as Japan, Europe, the United States and across Canada.

Attendees at the conference were greeted with a full room of tabletop displays and equipment they could look at. I want to personally thank everyone who took the time to attend, sponsor, speak at and participate in the equipment and tabletop presentations. Your presence helped make this event worthwhile.
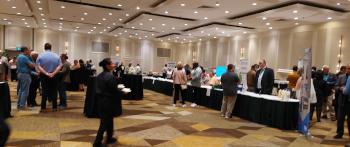
Prior to starting the conference, all the allied trades in attendance had the opportunity to address those present about the history of their company and what they can do to assist operators in improving their profitability and increasing productivity. The live equipment demonstrations led to the purchase of at least 10 Sankosha presses by our members, as well as our invited guests. To that end, I would like to congratulate Harry Lin of Dufferin Custom Cleaners in Thornhill, who won the CFA award of $1,000 towards the purchase of equipment at the show and the distributor discount of $1,000 with the purchase of equipment at the show.
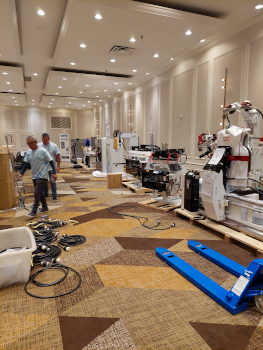
We had a raffle for a free membership for 2024, and the winner was Michelle Kruiliki of Newtex Cleaners in Kitchener.
In addition, Jacquelyn Stevens of Willms & Shier Environmental Lawyers LLP donated prizes for three additional draws.
We had a fact-filled program of information that cleaners could take back to their plants and implement. All our speakers received overwhelming applause for their presentations. In particular, Jason Loeb of Sudsies Cleaners in Florida, shared much information and hopefully will return to a future conference.
The Sunday morning workshops were great, and we had to bring in additional tables and chairs to accommodate all those who wanted to attend and learn more from our speakers.
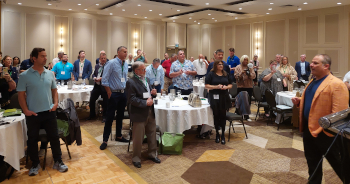
Many Americans came north to Toronto to attend the conference (quite a few came to listen to Jason Loeb, who is an icon and respected operator in Florida.) Speaking with many of them afterward, they said that they were looking forward to attending future CFA conferences in Canada. This conference has put the CFA on the international stage and enhanced the importance of the work we do for our members, our customers, and the community.
If you were there, please tell all your industry associates about what took place in Toronto and encourage them to consider making the time to travel to our future conferences. They will not be disappointed.
Industry veteran Doug Story opens new Laundry consultancy
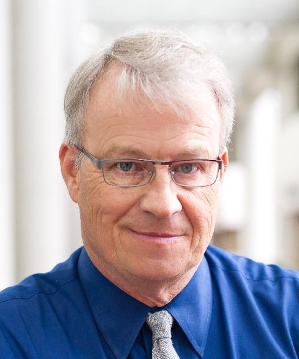
For over 35 years, Doug Story worked with customers worldwide in the industrial laundry and institutional cleaning business and showed them how to make the washroom side of their operations more efficient. After serving in various capacities – ranging from an R&D chemist to a division president – he has now opened MorgenBrooke, LLC., a North Carolina-based group consultancy.
He established MorgenBrooke to address what he terms as undervalued operational resources in commercial and industrial laundries. Looking at the considerable rise in operational costs in recent years for an industry already known for its paper-thin margins, Story believes his chemicals and operational expertise can help operators significantly reduce their laundry’s operational costs.
“Laundry organizations were already experiencing challenging times before the COVID-19 pandemic arrived three years ago,” notes Story. “Plants often struggle with their operational needs, especially in terms of managing their wash aisle chemical, and productivity costs. We have developed a process that can analyze these areas and drive them to become more efficient, with the added effect of lower costs and an improved bottom line.”
Story says MorgenBrooke’s unique Productivity and Resource Optimization (P.R.O.) evaluation and decision-making program is applicable to any size laundry or institutional operation.
“In the past I led teams where we implemented a similar program that enhanced operational efficiencies. We spend time with the engineers and teach them about proven methods to improve the washroom area by reducing water consumption, wastewater, labor time and energy,” commented Story.
“With our P.R.O. program, we can create a portfolio where our customers have a choice in how they can move forward. It includes everything from custom dispensing systems and unique, automated methods of processing, to running performance scenarios on the impact a new piece of equipment will have on your operation before you write the check.
“We combine this process with various auditing reports that can be used for internal performance measures and/or external bench marking against the market as a whole. Overall, it is designed to be part of the solution as a critical tool that can aid an owner or managing executive in their decision making process.”
To learn more about how MorgenBrooke can help your operation, contact Doug via email: storydoug@att.net.
SEPTEMBER 2023 NEWS
DLI 2023-24 Board of Directors
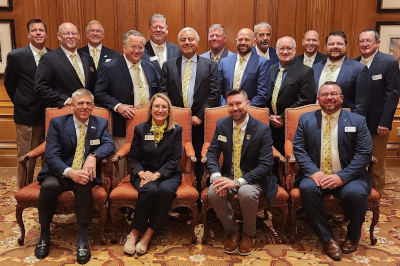
Each year the Drycleaning & Laundry Institute‘s (DLI) Board of Directors brings on new members as other members retire or move into Executive Committee positions. This August DLI bid farewell to Chairman Bobby Patel of BeCreative360 and Kona Cleaners in Orange, CA and Ed Longanecker of Iris City Cleaners in Mount Pleasant, IA, while welcoming Dan Sims of Jim’s Formal Wear in Trenton, IL and David Grippi of Clean Brands in Naples, FL at its Summer Board Meeting.
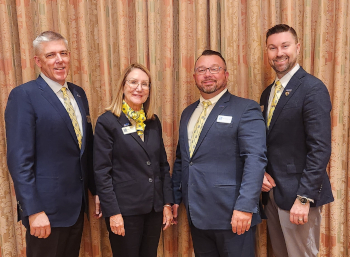
(Left) DLI’s 2023-2024 Executive Committee (left to right): DLI Treasurer Toran Brown, DLI President Kathy Benzinger, DLI Chair Jeff Schwegmann II CED®, CPD®, CPW®, and DLI President-Elect Kyle Nesbit. All Executive Committee positions are for the 2023–2024 term.
All Executive, Director, and District Committee Member leadership positions are volunteer. DLI greatly appreciates the time and resources all members of the Board of Directors share in guiding the Institute.
Board members in photo above:
Front Row (left to right): DLI Treasurer & District 8 Director Toran Brown, Rytina Fine Cleaners & Launderers, Sacramento, CA; DLI President Kathy Benzinger, Benzinger’s Clothing Care, Hamburg, NY; DLI President-Elect Kyle Nesbit, TIDE Cleaners, Spring, TX; and DLI Chair Jeff Schwegmann II, CGCP®, Sunshine Cleaners, Cold Spring, KY.
Second Row (l-r): District 2 Director Norman Way, Puritan Cleaners, Richmond, VA; District 5 Committee Member Tom Ustanik, Lansing Cleaners, Lansing, IL; District 8 Committee Member Ray Rangwala, Esteem Cleaners, Pasadena, CA; District 7 Committee Member Ryan Fish, Red Hanger Cleaners, Salt Lake City, UT; District 4 Director Raymond Kroner, Kroner Dry Cleaners, Cincinnati, OH; and Allied Trades Committee Member Jeff Jordan, Fabritec International, Florence, KY.
Back Row (l-r): District 3 Director Don Holececk, Crown Cleaners, Knoxville, TN; District 4 Committee Member John Mertes, Ziker Cleaners, Inc., Mishwaka, IN; District 2 Committee Member Chris Edwards, A Cleaner World, High Point, NC; Allied Trades Director, Mark Albrecht, The Route Pros, Woodbury, NJ; District 5 Director Dan Sims, Jim’s Formal Wear, Trenton, IL; District 1 Committee Member David Grippi, Clean Brands, Naples, FL; and District 6 Director Danny Bahlman, CGCP®, Bahlman Cleaners, San Angelo, TX.
Not Pictured: District 3 Committee MemberRhonda Eysel, Master Klein Dry Cleaners, Columbus, GA; District 7 Director Hilary Taylor, Continental Cleaners, Salt Lake City, UT; District 6 Committee Member Allan Cripe, Valet Cleaners, Temple, TX; and Mary Scalco, CEO and Secretary of the Board.
DLI 2023 summer graduates
DLI’s School of Drycleaning Technology trained 16 students in its 383rd General Drycleaning Course, composed of the five-day Introduction to Drycleaning Course, July 17 – 21 and ten-day Advanced Drycleaning Course, July 24 – August 4.
Founded in 1927, DLI’s School of Drycleaning Technology has helped shape the careers of thousands of drycleaners worldwide. In these courses, students learned about:
- Sorting loads for drycleaning
- The science of drycleaning
- Fibers and their characteristics
- Fabric construction
- Cleaning silk, stain, and other fabrics
- Soil and cleaning theory
- Operating a drycleaning machine
- Stain removal chemistry and procedures
- Removing coffee, ink, grease, and other stains from clothing
- Pressing pants, coats, blouses, ties, pleated garments, and skirts
- Using tensioning equipment to improve finishing quality
- Using bleaches without damaging fabric color
- Distillation procedures
- Understanding the differences between solvent types
Upcoming 2023 DLI Courses
- On-Site Introduction to Drycleaning: October 16 – 20
- On-Site Advanced Drycleaning: October 23 – November 3
Prospective students are invited to learn more and register at www.DLIonline.org/Education or to call Melissa Wagner at 800-638-2627.
DLI’s 383rd Introduction to Drycleaning — July 17 – 21, 2023
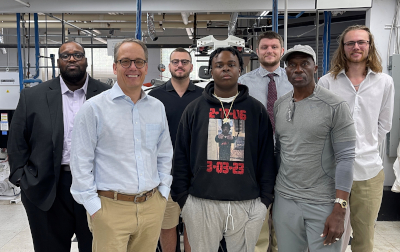
Front row (left to right): Chad Mayr, University Cleaners, Lexington, VA; Te’Kwan Harris, Nu Royal Dry Cleaners, Newport News, VA; and Thurman Leonard, Nu Royal Dry Cleaners, Newport News, VA.
Back row (l-r): Jonathan Ballard, Augusta National Golf Club, Augusta, GA; Evan Suber, Perfect Cleaners, Inc., Los Angeles, CA; Davis Sexton, Crown Cleaners, Knoxville, TN; Alexander Hollenkamp, Regency Cleaners, Tyler, TX.
Not pictured: Deangelo Butler, BLE Cleaners, Nassau, Bahamas.
DLI’s 383rd Advanced Drycleaning Course — July 24 – August 4, 2023
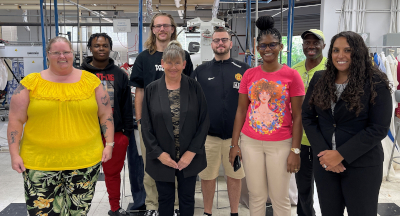
Front row (left to right): Melissa Monroe, Budget Cleaners, Gulfport, MS; Ashley Aguilar, Summit Cleaners, Colorado Springs, CO; Natalia Pedro, Pristine Laundry Hub, Georgetown, Guyana; Janay D’Souza, Dependable Cleaners, Denver, CO.
Back row (l-r): Te’Kwan Harris, Nu Royal Dry Cleaners, Newport News, VA; Alex Hollenkamp, Regency Cleaners, Tyler, TX; Evan Suber, Perfect Cleaners, Inc., Los Angeles, CA; and Thurman Leonard, Nu Royal Dry Cleaners, Newport News, VA.
Whirlpool Corporation Unveils New Leading Edge Technology Center
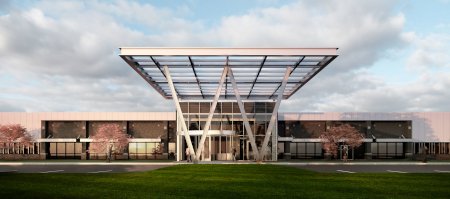
Technology center to be laundry, dishwasher and small appliance innovation hub
Facility to employ more than 500 Michigan-based high-tech talent
Whirlpool Corporation unveiled a new 153,000-square-foot technology center in St. Joseph, Michigan on August 18, 2023. The $60+ million project expands and replaces much of the current St. Joseph Technology Center. This is the first of a three phase plan to redesign an iconic research and development facility that has been home to decades of appliance innovations.
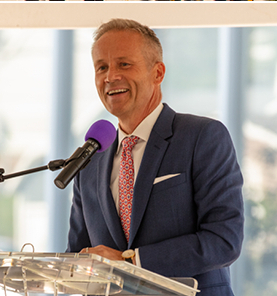
“In 1911, the first electric washing machines were built here in St. Joseph, Michigan, and we continue to grow that legacy with the investment in this new, state-of-the-art technology center,” said Marc Bitzer, Whirlpool chairman and CEO. “We are committed to this community, and to improving life at home for families around the world. This new technology hub helps enable both of these promises by creating a new space where future innovation will come to life.”
The expanded St. Joseph Technology Center is LEED Silver certified, a globally recognized ranking of sustainability achievement and leadership. The work that is done in this new facility will be focused on delivering consumer solutions through the washers, dryers, dishwashers, and small appliance products designed and tested here including the iconic KitchenAid Stand Mixer. The facility employs more than 500 technicians, engineers, designers and adjacent roles, and contains 21 testing labs.

“This $60 million investment by Whirlpool builds on the company’s longstanding commitment to Southwest Michigan,” said Gov. Whitmer. “This transformative project will help Whirlpool attract top talent, put more people on paths to good-paying, high-skill jobs, and continue our mission to help anyone ‘make it’ in Michigan. Our unemployment rate is the lowest it has been in 23 years, we are moving forward on housing and community revitalization projects across the state, and we just delivered a bipartisan budget to lower costs, expand workforce programs, and power economic development. We look forward to continuing our work together to build a bright future.”
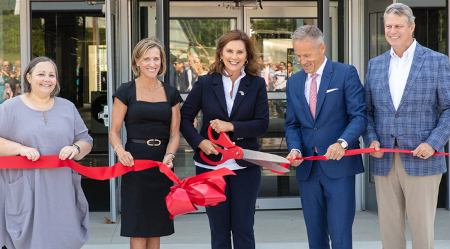
Whirlpool Corp. has invested more than $230 million in new or expanded facilities in the St. Joseph and Benton Harbor communities in the last ten years. The company also invested an additional $23 million in the 80-unit Emma Jean Hull Flats housing development in Benton Harbor which opened in June.
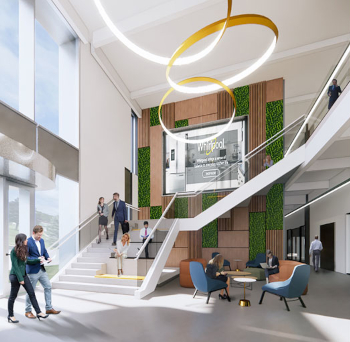
“This new building offers state-of-the-art technology for product design, development and testing to help address consumer needs now and for the future,” said Pam Klyn, Whirlpool executive vice president of corporate relations and sustainability. “The appliances designed within the four walls of this new technology center will represent new levels of innovation and sustainability so consumers can feel confident they are making the right choice for their lifestyle and the environment. “
As employees begin to transition to the new building, work will continue into 2024 to complete the next phases of the St. Joseph Technology Center project including renovation of the facade of the remaining portion and increased parking to improve access for employees.
AUGUST 2023 NEWS
Upgrading their Knowledge, Building the Industry
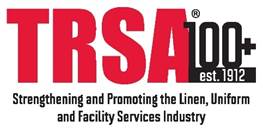
TRSA has two programs aimed at increasing the knowledge base and skills of the next generation of laundry leaders. They recently graduated a class from each program.
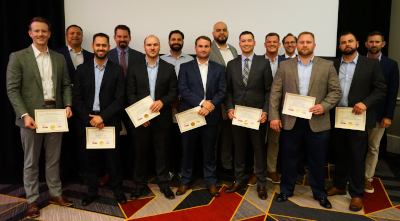
TRSA’s Executive Management Institute (EMI) held its 58th yearly commencement on Aug. 10, with 14 rising industry leaders graduating after completing the final segment of a four-year educational program for members of the linen, uniform and facility services industry. The dinner program also included remarks from students, faculty and TRSA leaders, plus a witty and well-executed skit performed by Year III students.
EMI was launched in 1965, mainly as a way for the scions of family-owned industrial laundries – many of whom began working full-time after high school – to gain university-level skills in areas such as marketing and finance. Today’s EMI, held annually at the University of Maryland, has evolved into a wide-ranging program. EMI emphasizes both technical and leadership skills, coupled with the development of networking contacts that will endure long after this year’s nearly 150 students complete the program.
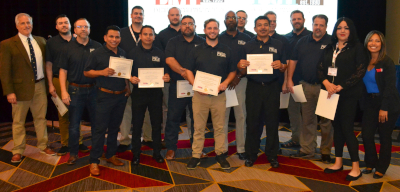
TRSA concluded its 33rd Annual Professional Management Institute (PMI) on Aug. 10 at the University of Maryland. The PMI curriculum provided attendees with a mixture of industry-specific education in a classroom setting, as well as hands-on experience through a pair of plant tours, culminating with Session II PMI students taking the Certified Professional Laundry Manager (CPLM) exam.
Both sessions kicked off the week with lectures and group exercises covering topics specific to the linen, uniform and facility services industry such as soil sort, wash-aisle equipment, scheduling and managing workflow, managing quality control and production efficiency, safety awareness, inventory control, customer service, training and development, coaching and mentoring, employee retention, budgeting and return-on-investment (ROI), and more. To see how these best practices work in the field, both sessions of PMI students embarked on plant tours on Aug. 9. PMI Session I students visited the Alsco Uniforms facility in Lanham, MD, while Session II attendees visited Mayflower Laundry & Linen in Belcamp, MD.
CFA Conference Speakers Announced
The Canadian Fabricare Association has announced the following speakers and topics for its September 29-October 1 “Embracing Change” conference in Toronto.
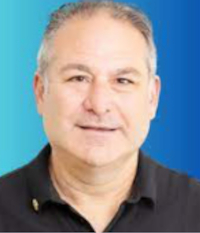
Jason Loeb, Sudsies Cleaners
How to build and grow your business
The work of Jason Loeb is always associated with passion and a smile. As founder and president of Sudsies.com he stresses a combination of the highest quality product with exceptional customer service to provide impacting experiences for his clientele. His genuine attention and on-the-spot advice makes him frequently sought out to work with clients from all over the world as an industry consultant and forum speaker presenting topics on marketing, employee motivation and sales growth. Despite Loeb’s vast accomplishments and unlimited energy, his formula for success is simple: differentiate yourself, be true to your brand and exceed your customer promise.
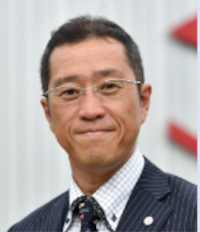
Ken Uchikoshi, Sankosha
Global Perspective of the Fabricare Industry and how to help propel business in the future
As President of Sankosha, one the biggest brands recognized throughout the fabricare industry worldwide, Ken Uchikoshi travels the world extensively and has valuable insight as to why our industry has faced a drastic slowdown. According to Uchikoshi, we are facing a generational change from the 70’s typical business model to the next generation. But what are the next steps? Ken will speak about the trends of the world situation, and provide anecdotal advice to help propel your business into the future.
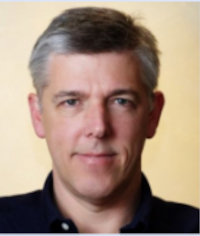
Tom Beidle, SPOT
Focusing on Industry Macro Trends
Tom Beidle is the CEO of the Personal Services Division at Xplor Technologies and leads the Xplor Spot business. He has spent 20+ years in SaaS and eCommerce companies. His experience extends across both public traded and private equity-backed software firms. He is also a mentor and advisor to start-ups and high growth technologies.
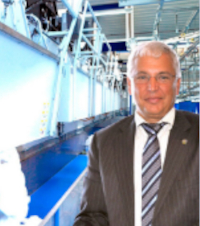
Peter Wennekes, CINET
State of the Industry
At the head of the CINET (International Textile Care Committee) since 2006, Peter Wennekes intends to promote the textile care professions at an international level. A tireless ambassador for the profession, he is also the organizer of the CINET Awards, which reward laundries and dry cleaners
around the world for their best practices.
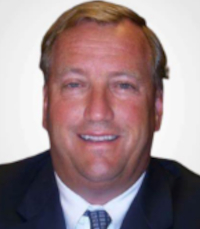
Jon Meijer, DLI
New DLI Website
Jon Meijer is the Director of Membership for the Drycleaning & Laundry Institute in Laurel, Maryland.
After starting with DLI (formally IFI) in 1982, Meijer has gone on to become a popular industry speaker and has written numerous articles and bulletins for DLI’s Fabricare magazine. He continues to represent the industry all over the United States and Canada, working with government agencies such as the Occupational Safety and Health Administration, the Environmental Protection Agency and Environment Canada.
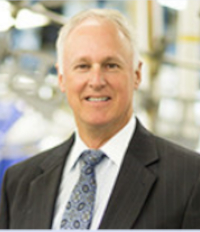
Kermit Engh, Methods for Management
The Eight Drivers of Company Value
Kermit Engh has been an owner/operator in the dry cleaning industry for over 30 years, a member of MfM for more than 27 years, the president of the Association of Wedding Gown Specialists for over 20 years, a member of DLI and LCI, and winner of numerous industry awards including the 2016 CINET Internationale Sustainability Award. It’s his honor to facilitate Methods for Management to continue to foster industry communication and innovation.
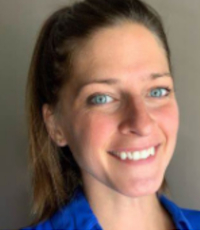
Jennifer Whitmarsh, Route Pro
The 5 Common Denominators in Successful Members Delivery Routes
Join Jen as she shares the top 5 common denominators, she sees within the route success of member companies. Learning best practices and procedures will help your delivery route grow and grow right.
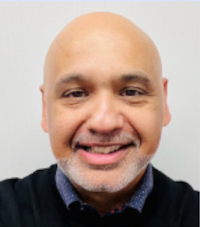
Ravi Gill, Groupe Daoust/Forget
Survival and Growth through Evolution
Ravi Gill as the VP of Corporate Development at Groupe Daoust/Forget Inc. has been tasked with overseeing the evolution of one of the largest dry-cleaning brands in Canada and one of the largest wet-cleaning operations to be found anywhere on the planet. Our goal is simple. To create a sustainable, profitable and adaptable business model that can help to reinvigorate our industry in the challenging decades to come.
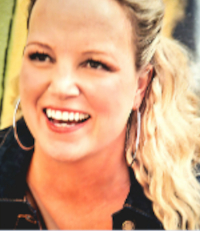
Kim Sekleski, Wright Cleaners
Customer claims and working with a manufacturer
Kim discovered her own niche within the Dry Cleaning industry when she grew tired of poorly manufactured clothing wreaking havoc on her machinery, her counter staff, and her bottom line.
This experience quickly transformed into an opportunity to educate her customers about warranties and recalls, fostering a mutually beneficial relationship between the industry and manufacturers. As she states, “The customer isn’t always right, but they can be enlightened about the garments they invest in,” empowering them while maintaining the industry’s commitment to preserving their impeccable wardrobes.
For more information on the conference, visit the website.
Canadian Summit Keynote: Navigating Generational Diversity
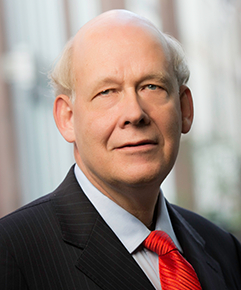
Karl Moore, a scholar who researches the impact of workplace-generational issues, will give a keynote address at TRSA’s Fourth Annual Canadian Production Summit this Oct 4-5 in Toronto.
Moore, an associate professor at the Desautels Faculty of Management, McGill University, Montreal, will discuss his new book “Generation Why: How Boomers Can Lead and Learn from Millennials and Gen Z.” Moore will offer insights on the management strategies that senior leaders can use to effectively recruit, motivate, manage and retain a younger workforce.
Currently, four distinct generational cohorts are simultaneously contributing to workforces across North America. People over the age of 45 were taught and shaped with a different worldview than those under 35. The group known as “Gen Z” (born 1997-’12) and younger millennials (born ’81-’96) in most cases hold different attitudes and expectations than baby boomers (born ’46-’64). Therefore, managing these groups effectively requires varying approaches. “In today’s world, young people are looking for purpose beyond just making money,” Moore said in a recent interview with Textile Services Weekly. “They want to have a social impact.”
By extension, Moore added that Gen Y and millennial staff want to contribute their ideas to help plan a company’s future. “Young people want to be part of (developing) the company’s strategy,” he said. “They want to have a voice in the discussion of where the company’s going.” Involving employees of varying ages and levels of experience can improve corporate strategies. For example, front line staff could have closer contact with clients and fellow employees, and they can offer ideas for developing new approaches. “Emergent strategies come from people on the front lines,” Moore said. Ultimately, senior management is responsible for decision making, but incorporating different ideas and approaches can help their organization adapt to and succeed in a rapidly changing business environment.
A key approach for managers who are leading staff from multiple generations is a process that Moore refers to as “Reverse Mentorship.” Managers must emphasize not only leading and mentoring, but also listening to and learning from their employees. Simply put, managers should “Listen more, talk less,” said Moore, “(Managers) still need to talk, inspire and uplift, but listening is a bigger part of the job than it was 10 years ago.”
Generational differences can impact a company’s bottom line, either positively or negatively. Moore will argue in his upcoming talk that if leaders can successfully bridge this gap, “(Employees) will be more engaged; you’ll get more done and you’ll have better strategies.”
Click here for more information and to register for the Oct. 4-5 Canadian Production Summit in Toronto. In addition to Moore’s keynote speech, the Summit also will feature two Toronto-area plant tours including Topper Linen Supply and HLS Linen Services, as well as sessions covering global trade, regulatory and legislative updates, facilitated roundtable discussions and an operator sustainability panel.
What can we do?
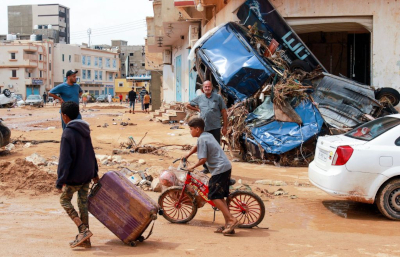
Everywhere you look, people are devastated. A summer of wildfires across Canada, Hawaii’s Maui fire, a massive earthquake in Morocco leaving thousands dead or unaccounted for, a sweeping flood in Libya. Here are a few tips for you, your company and your customers who want to help.
Give through a recognized organization after checking them out.
The last thing you want is for your effort and money to be wasted. To learn more about any charitable organization, use sites like Canada Helps or Charity Navigator, which rate the effectiveness of charities on a number of criteria. With respect to the four disasters listed above, they’ve done the work for you and have a number of suggestions for each crisis. Click the links below to see reputable charities in each case.
Round up others to help you raise more funds.
None of us has bottomless pockets. Get your staff, friends, and customers involved.
For example, the staff at Tingue recently gave $4,500 to The United Way’s Maui Fire Relief Fund. They raised the money through a challenge for their operations team to walk a combined 500,000 steps on August 17.
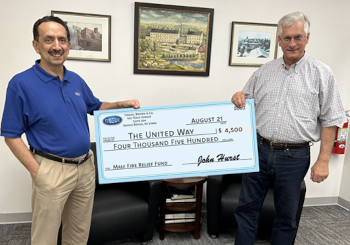
“The passion and dedication displayed by our teams has been nothing short of remarkable,” the company news release said, adding that the challenge “has motivated an inspiring journey of camaraderie and purpose.” The company also held an e-commerce campaign, with $50 donation given to the fund for every $100 order placed online by their customers.
Disasters like these can strike anywhere, anytime. Thank you for giving!
Jeff Belcher to receive Maglin-Biggie Lifetime Achievement Award
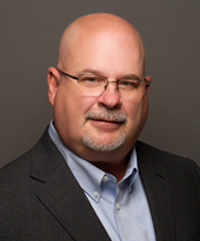
TRSA announced that Jeff Belcher, the former president and owner of Alliant Systems, Irving, TX, was selected as this year’s recipient of the Maglin-Biggie Lifetime Achievement Award for supplier-partner executives. Belcher will receive the award on Oct. 12 at TRSA’s Annual Awards Dinner, held in conjunction with the 110th Annual Conference at the Ritz-Carlton, Tiburon, in Naples, FL.
“It has always been a privilege to represent Alliant Systems and its predecessor organizations,” Belcher said. “I think back to all of the mentors, friends, co-workers and relationships, and realize the incredible impact that each of these individuals had on my career. These relationships spanned my fellow employees, each of our customers, those acquaintances developed through TRSA meetings and, in particular, TRSA’s EMI program and friends and colleagues in the industry. This collective guidance and advice helped shape the values and character of what Alliant Systems became, and I will always be thankful for each and every one of those that contributed with ideas, thoughts, advice and guidance.”
Belcher joined the linen, uniform and facility services industry in 1985, installing and providing support for soil-counting systems. Ultimately, he became the president and owner of Alliant Systems. Under Belcher’s leadership, the company grew to become the largest supplier of route accounting and mobile computing software solutions to independent textile rental companies. He retired from Alliant Systems in April 2022.
“Jeff’s leadership style was to lead by example at all times,” said Eric Smith, the director of sales and marketing at Alliant Systems. “He was a listener. He always wanted to know what operators were doing and what they needed to compete in the marketplace. He was great at developing teams, building consensus and finding solutions that would work for everyone.”
One of Belcher’s most significant contributions to the industry was assisting TRSA in its fight to protect the industry against patent-infringement claims that were threatening textile rental operators in 2019. Belcher provided countless hours of his time assisting behind the scenes to help work toward a solution for the industry. In addition to time, he also contributed significant financial resources. Belcher’s ability to work with industry associations and groups, other operators, and suppliers to help build consensus on a solution was critical to the final resolution, which was achieved at the end of 2021.
Under Belcher’s leadership, Alliant Systems always recognized the value that TRSA provides to the industry. Supplier-partner membership in TRSA was always important to him. Even more important was the value of TRSA-sponsored training programs, such as TRSA’s Executive Management Institute (EMI). Belcher was the first EMI graduate from Alliant Systems, and he went on to send another dozen or more Alliant managers and employees through the program to gain the same benefits and education that he received during his time in the program.
In 2012, he was one of eight industry veterans named to TRSA’s EMI Executive Task Force with a goal of improving the EMI curriculum. The task force made several changes to the program which have proven to be successful to this day. Changes to the curriculum included adding subjects such as technology, disaster management, succession and project management.
CFA issues Industry Invitation
The following letter arrived from Canadian Fabricare Association Executive Director Sid Chelsky, regarding the association’s upcoming conference.
Dear Cleaner or Allied Trade:
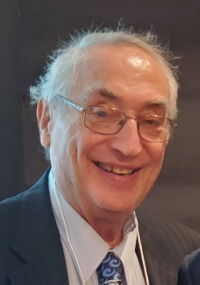
I am reaching out to you and inviting you to attend our upcoming conference on Friday, September 29th, 30th, and October 1st. This year it is especially important that we provide our members every possible way to maintain and grow your business.
The cleaning industry has gone through some difficult times because of the Covid 19 pandemic. Over one third of the cleaners across Canada and the United States closed their doors. You are to be commended that you have weathered the storm so far. However, we believe that you cannot continue to do it alone without help from others in the industry.
To this aim, we have put together a very special weekend of education and training to assist you in maintain and growing your business and increase your profits. Including our knowledgeable speakers, is our keynote speaker, Jason Loeb, who operates a very successful cleaning and laundry plant in Florida. He is well known for his dedication to those in our industry and has offered to share his knowledge with you.
In addition, we have speakers that will help you diversify the services you provide, add profitable route delivery service, add POS (point of sale) systems to better control the processing of customers garments and household items. There will be equipment including presses and washer / dryers on display as well.
Several of our speakers have added a workshop on Sunday morning, which is included in your registration. You will have the opportunity to discuss in depth how to add high end clothing to your volume and get higher prices for processing them, as well as things to do to manage your business and ensure it is profitable.
You can attain registration by going online at www.fabricare.org and fill out the forms for the conference. I hope to see you there.
Sidney Chelsky,
Executive Director, Canadian Fabricare Association,
E: canadianfabricare@fabricare.org
T: 416-573-1929
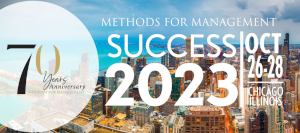
70 Years of Success
Methods for Management Celebrates with Success 2023 Event in Chicago
Methods for Management (MFM), the most experienced consulting firm in dry cleaning Management Bureaus, announces Success 2023, a celebratory event in honor of its 70th anniversary, October 26-28, 2023, at the Hilton Chicago Miracle Mile in Chicago, IL. (SEE OUR EVENTS CALENDAR FOR MORE DETAILS.)
Methods for Management (MfM) was founded in 1953 by Max Rechnitz, who was later joined by his daughter, Deborah Rechnitz, in 1980. Together, they built a strong reputation as a top-notch management consulting firm, assisting independent business owners in achieving their personal and business goals.
In 1997, the team was further bolstered by Diana Vollmer, who became a senior consultant with the firm. Her expertise significantly enriched MfM’s services until her retirement in 2014. A member since 1997, Kermit Engh became the Managing Partner of MfM in 2014, bringing decades of business experience, specifically through Fashion Cleaners.
Success 2023 will include an impressive line-up of presenters, including two keynote speakers.
Steve Baker, Vice President of the Great Game of Business, and co-author of The Great Game of Business 20th Anniversary Edition, specializes in Open-Book Management, Strategy & Execution, and Leadership and Employee Engagement, and Jeff Butler, a speaker, author, and workplace strategist who explores human behavior within the working world.
Additional speakers scheduled include Bob Clements, Co-founder, Strategic Marketing Director, and General Counsel for Benchmark Business Group; Jennifer Whitmarsh, Customer Service Route Pro of Route Pros; Bill Albers, President of SMRT; Toran Brown, Vice President of SPOT, and Jeff Gude, MfMBI. Along with this fabulous speaker line-up, industry leading POS systems SPOT and SMRT representatives will be hosting breakout rooms to enable users to talk one-on-one.
“The entire Methods for Management team is looking forward to the celebratory event and the opportunity to gather current and past Methods for Management members,” says Kermit Engh, managing partner of MfM. “We are thrilled to bring our members together to celebrate this momentous occasion.”
A welcome reception for attendees kicks off the event. On the final evening, an award ceremony will honor members selected as winners in categories such as Best Idea, Best Plant, Best Van, etc.
Attendees will also have time to enjoy all Chicago has to offer. From world-class shopping, The Art Institute of Chicago, Field Museum, Millennium Park, River Architecture Cruises, Navy Pier, and much more.
The event is for current Methods for Management (MfM) dry cleaning Bureau members, alumni, and industry sponsors. MfM is encouraging all MfM alums and any dry cleaners wanting to learn firsthand the benefits of Bureau Membership to contact vreed@mfmi for all the details.
Annual CLATA Tom White Memorial Golf Event
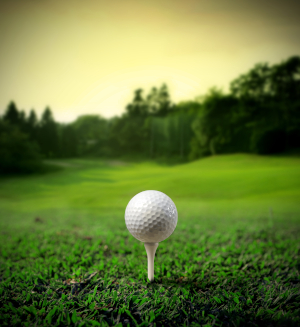
The event is Thursday, September 7, 2023. This year’s event promises to be one of the best yet! The Management at Bay of Quinte Golf Club are excited to be welcoming CLATA back to their facility. There is a new course layout, now with three new holes in play, and a unique “warm-up” hole, making this a 19-hole course. Those who attended last year’s event probably remember seeing the new holes being worked on during their time on the course. Additionally, they have invested in new state-of-the-art electric power carts and even more importantly, a re-vamp of the restaurant with a new management team and Head Chef.
There will be a PRIME RIB DINNER — guaranteed — the new chef (Colin) has been given strict instructions that only the finest quality will be acceptable!
SEE FLYER FOR DETAILS HERE. Please let Trevor Holmes know your teams/attendees asap, but no later than Friday, August 25, 2023.
From Karate Kicks to Top Golf
TRSA’s 2023 Leadership Summit
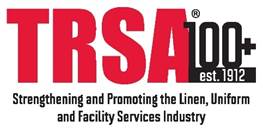
On June 13-15, the Textile Rental Service Association hosted its 2023 Leadership Summit in Oak Brook, IL. After a full day of education and networking on June 14, the Summit closed with a panel featuring CEOs from several leading North American linen, uniform and facility services companies.
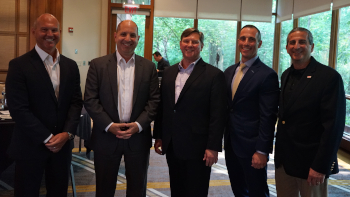
The panel presentation featured Brian Herington, CEO, PureStar Group, Las Vegas; John Ross, CEO, Mission Linen, Santa Barbara, CA; Jim Rozakis, executive vice president & COO, Cintas Corp., Mason, OH; and Steve Sintros, CEO, UniFirst Corp., Wilmington, MA. The panel was moderated by TRSA President & CEO Joseph Ricci and Senior Editors Jack Morgan and Jason Risley.
Topics covered during the panel included:
- Opportunities for growth, including healthcare outpatient clinics and surgery centers as well as the potential for direct sale.
- Ongoing labor challenges – while staffing has improved over the past year, it is still difficult to find qualified labor, as well as retain staff in certain areas such as engineering and maintenance.
- Emerging technologies and how they’re impacting operations, and how data is being collected and used to fuel business insights.
- The impact of private-equity firms on the linen, uniform and facility services industry.
- Each executive’s approach to leadership and ongoing professional development.
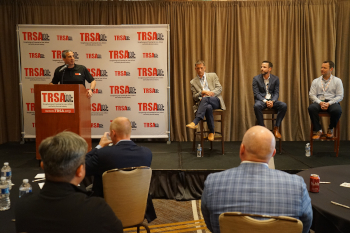
The Leadership Summit kicked off with a Supplier Partner Workshop on June 13 featuring an advocacy update from Kevin Schwalb, vice president of government relations at TRSA. This was followed by a special presentation on recruiting young talent presented by Cody Brazil, TRSA’s digital marketing manager. After a short networking break, a panel on Strengthening Partnerships between Supplier Partners and Operators was led by Theresa Garcia, COO, Division Laundry & Cleaners; Josh Wildman, CEO, Wildman Uniform & Linen; and Sara Gunderson, manager, Gunderson Uniform & Linen Rental. The opening day closed with a Supplier Partner Networking Reception and a Leadership Summit Welcome Reception. The next day, the Leadership Summit offered a full day of programming beginning with keynote speaker David Kovar, who touched on how his martial-arts training fueled his passion for helping organizations and businesses achieve profitability and growth.
Breakout sessions specifically aimed at CEOs/Executives, Next-Generation Executives and Emerging Leaders included Applying the Leadership Mindset; Remaining Union Free; Positive Employee Relations; How to Create Your Support Network in a Family Business; and the Future of Fleets. The day wrapped up with the CEO panel.
The event closed on June 15 with a Next-Generation Executives Workshop, followed by a networking outing at Top Golf.
TRSA Production Summit Returns to Toronto
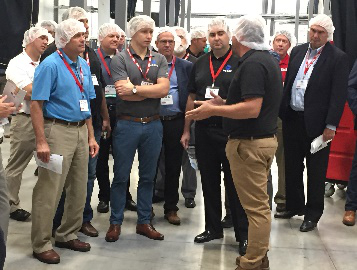
TRSA is returning to Toronto this year to host the 4th Annual Canadian Production Summit following the COVID-19 pandemic hiatus. The Production Summit is a great opportunity for TRSA members and nonmember operators to participate in interactive sessions, tours and, network opportunities. Scheduled for Oct. 4-5, the summit will provide an opportunity for participants to stay abreast of developments in the evolving linen, uniform and facility services markets in Canada.
Dr. Karl Moore will deliver the keynote address at the summit. As an associate professor at McGill University’s Faculty of Management where he teaches graduate courses in strategy and leadership and has authored or edited 10 books. Dr. Moore will focus discussion on his most recent book Generation Why – How Boomers Can Lead and Learn from Millennials and Gen Z.
The summit will feature several general sessions on a wide variety of topics including:
- Global Trade: Discussing the impact of taxes, duties and regulatory issues, multicultural and multilanguage issues and how to handle them in a linen, uniform and facility services plant.
- Regulatory and Legislative Update
- Operator Sustainability Panel that will cover best practices, the impact of certifications and the environmental focus looking forward.
- Hot Topic Roundtable Discussions determined by attendees
The Summit will also consist of two Toronto-area plant tours including:
- Topper Linen Supply with two building totaling 56,000 square feet
- HLS Linen Services a 64,000 square foot plant specializing in healthcare
McConnell Classic raises over $100,000 for Campfire Circle!
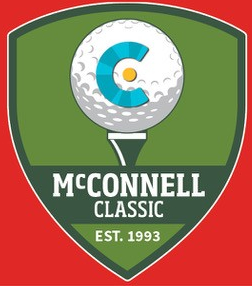
On Tuesday June 6 the McConnell Classic had a full field of 144 golfers and more than 160 for dinner at Royal Ontario Golf Club to raise an incredible $100,575. The funds go to Campfire Circle, which operates camp-based programming for children and families affected by childhood cancer. This brings the event’s total contribution to over $1,400,000 since the Classic began in 1993.
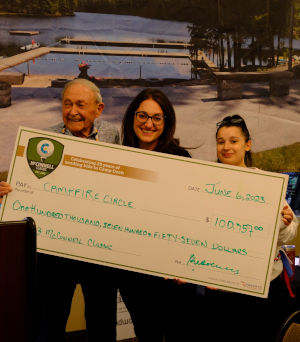
The day wouldn’t be possible without the support of generous contributors, participants, and volunteers. Rob McConnell, President of Gibson’s Cleaners, is a member of the planning committee and provides monetary support for the day’s activities.
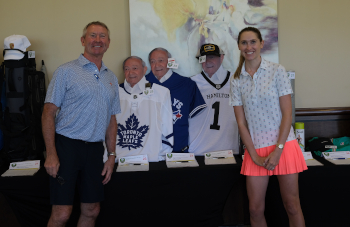
“Gibson’s has always believed in giving back to our community, and it feels wonderful we can support this amazing organization every year with our time, money, and expertise.”
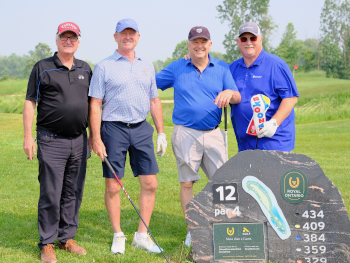
Michelle Patrick, Gibson’s IT Coordinator has been heavily involved in the tournament’s organization for over a decade. “It was great to see another full field of golfers out on the green this year! We’ve gotten the planning of this event down to an art.”
The day was filled with fun and laughter with the highlight being comments from Campfire’s Circle Ashley Dykan and Camper Stefani D’Amico.
Congratulations to everyone involved for this wonderful accomplishment.
Amendment 15 to bring stricter boiler regulations to Canada
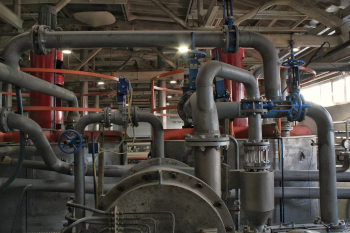
Amendment 15 is a directive passed by the Government of Canada. Starting in 2025, all commercial fuel-burning technologies for primary space heating manufactured in Canada must have a thermal/combustion efficiency of at least 90 percent. For commercial gas boilers manufactured on or after Jan. 1, 2025, the Amendment sets condensing boilers as the standard for all installations.
This includes commercial gas boilers for hot water systems.
High-efficiency boilers are 85 – 89 percent efficient and have a lower upfront cost. Condensing boilers can reach efficiencies of 98 percent, as they are able to capture flue gas heat that would have otherwise been wasted and reuse it in the heating process to save energy and reduce emissions.
Once Amendment 15 takes effect, the only boiler retrofit option for most commercial buildings will be to upgrade to a condensing boiler. For some buildings, this will require more than swapping out an old boiler for a condensing one. For example, condensing boilers need to operate at lower temperatures to achieve condensing levels, so venting systems may need to be upgraded to accommodate the condensate produced and avoid corrosion. Replacing a single boiler in a multi-boiler system can also be a challenge if the system is not designed to accommodate the venting and plumbing requirements of a condensing unit.
Contact your boiler distributor/installer for further information and to be sure you are in compliance when the time comes.
Lavanett named Distributor of the Year by Girbau North America

Girbau North America (GNA) recently recognized several distributors with 2022 Distributor of the Year awards for superior sales and service within specific markets. Award winners include AAdvantage, in Garland, Texas; Eagle Star Equip. (Eagle Star), in Troy, Mich.; Fowler Laundry Solutions (Fowler), in Union, N.J.; AAdvantage, in Garland, Texas; and Lavanett, in St. Laurent, Quebec.
- Lavanett earned the Canadian Distributor of the Year award for excellence in multiple markets, including on-premise, vended, industrial and textile care. Owned by Earl Eichen, Lavanett employs 20 team members and provides laundry and textile care solutions, parts and service to customers throughout Canada. “Lavanett once again captured GNA’s attention in Canada,” said Jorgensen. “Earl and his team work hard to provide targeted laundry solutions to a wide array of markets, as well as unrivaled service after the sale, which is a huge part of their success equation. GNA congratulates them on another great year representing the Continental Girbau, LG Commercial, Econo and Poseidon brands.” Find out more about Lavanett, visit www.lavanett.ca or call 877-398-1194.
- AAdvantage received awards for excellence in the athletic, industrial and on-premise laundry
markets through the sale and support of Sports Laundry Systems®, Girbau Industrial® and Continental Girbau® (Continental) laundry solutions. AAdvantage, a division of EVI Industries Inc., is led by President Ryan Smith and is among the largest volume distributors in the world, according to Girbau North America (GNA) Vice President of Sales Joel Jorgensen. “AAdvantage has an outstanding sales team, backed by one of the industry’s best parts and service departments,” he said. “Customers always get the support they need before, during and after the sale. They are a top-notch distributor and we are proud to work beside them.” For more information about AAdvantage visit www.AAdvantagelaundry.com or call 800-880-2138. - Eagle Star earned the award for excellence within the textile care market through sales and
support of Poseidon Textile Care Systems® (Poseidon). Led by Michael “Stucky” Szczotka, Eagle Star is a full-service distributor of quality solutions for the textile care, vended laundry and on-premise laundry markets. The company, with more than 47 years in the industry, offers dry cleaning and laundry planning, equipment, installation, parts and service. “Eagle Star and Stucky helped us create, field-test and launch the Poseidon brand through their market expertise,” said Jorgensen. “Since then, Stucky and his team have introduced Poseidon to the textile care market, where the brand has taken hold and continues to grow year-over-year. Eagle Star’s continuous sales efforts, backed by their first-class service and technical support make them a valued industry partner.” For more information about Eagle Star Equipment, visit www.eaglestarequipment.com or call 800-482-3400. - Fowler received the award for excellence within the multi-housing laundry market through the sale and support of LG Commercial, Econo and Continental Girbau laundry solutions. Led by Doug Fowler and founded in 1952, the multi-generational company employs 70 team members focused on unsurpassed customer service. The full-service company is among the largest laundry equipment distributors in the Mid-Atlantic region and serves the vended, multi-housing, on-premise and industrial laundry markets. “The Fowler team makes it easy for customers to do business with them because they provide full service and support at every stage, from the laundry amenity proposal and facility upgrades to the value-added elements critical to an extended relationship with their customers,” said Jorgensen. “At GNA, we are proud to work beside them.” To find out more about Fowler, visit www.fowlercompanies.com or call 800-334-1824.
A man who made a difference
Joseph Petrozzi, founder of Coats for Kids, dies at 95
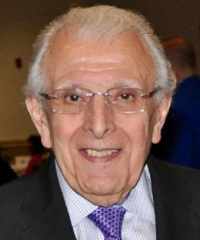
It started because he looked out his dry cleaning shop window and saw children going to school in skimpy jackets. He rounded up some coats, cleaned them, and watched warm smiles blossom. Eventually, Joseph Petrozzi’s soft-hearted gesture grew to be a regional, national and then international charity phenomenon.
Joseph passed away on June 6 at the age of 95. Read more about his remarkable story here.
2023 TRSA Annual Production Summit & Plant Tours
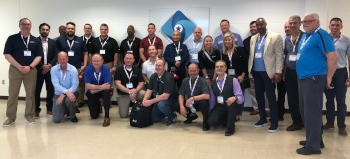
TRSA hosted its Annual Production Summit & Plant Tours in Kansas City, MO in May. During this two-day event, 91 attendees traveled from across the country for a full day of professional development focused on plant production, followed by a day of touring two Kansas City-area facilities.
The opening day of the Production Summit kicked off with a keynote speech from Dr. Melissa Furman, MS, DBA, founder and consultant at Career Potential LLC. Furman’s speech was titled Managing and Leading the Future Workforce. During her keynote address, she gave guidance on challenges that affect the future workforce such as burnout, generational gaps and acknowledging personal biases. Attendees were then given the chance to attend two of four breakout sessions.
The first breakout session was on preventative maintenance and was delivered by Joel Bell, engineering director at UniFirst. Bell coached attendees on the importance of technology investment and forethought in keeping operations in satisfactory conditions. The second breakout on automation and emerging technology was delivered by Gerard O’Neil, owner and CEO of American Laundry Systems and Scott Voss, vice president of technical engineering & installations at Ellis Corp. Their session was centered on the emergence and implementation of new technologies to decrease cost, starting with incremental gains that will likely remain manual labor-intensive. The final two breakouts were on Energy Efficiency and Water Treatment &
Usage and were delivered by Michael Lewis, senior client advisor at APPI Energy; John Schultz, director of water solutions at Ellis Corp. and Keith Ware, an industry veteran that is currently a consultant.
After a brief lunch and Legislative Update by Kevin Schwalb, vice president of government relations at TRSA, attendees reconvened into one group for a session on how industry colleagues are faring with pounds/pieces per operator hour under post-COVID labor scenarios that can result in laundries paying more for less production. This session was titled Identifying People/Equipment and Productivity Measures, and was delivered by Todd Leeth, strategic growth leader at Spindle. The attendees then broke into small groups of their choosing to have facilitated round-table discussions on issues affecting the industry such as automation, training, and recruitment and retention. The attendees were able to air their pain points and offer advice at a peer-to-peer level.

The first day of the Production Summit ended with a General Manager’s Panel Discussion where three panelists were able to discuss operational factors at their plants and their perspectives on their roles within the industry. The panelists were Peter Brown, general manager at Mickey’s Linen, McKenzie Lee, general manager at Alsco, Naples; and Matt Shapiro, general manager at Walker Medical Linen Service.
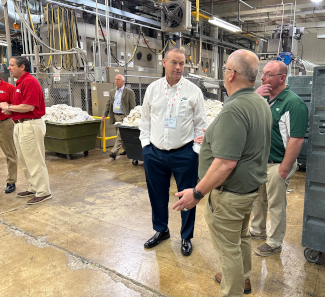
On May 11, the attendees broke into two groups to participate in plants tours of the Kansas City plants of both Crothall Healthcare and Cintas.
Crothall Laundry began processing laundry in their 50,000 square-foot facility in 1973. Crothall specializes in healthcare laundry and averages 260,000 lbs. of laundry per week at this branch. The facility utilizes one, six-module (220 lb.) tunnel washer with seven dryers, one 14-module (105 lb.) tunnel washer with six dryers, two 165-pound extractors with two dryers and two 65-pound extractors with two dryers.
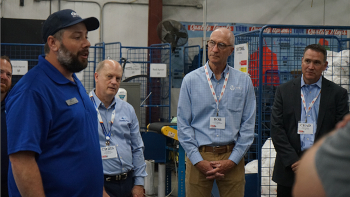
Cintas welcomed TRSA and the summit attendees to its 44,000-square-foot facility, where they kicked off the tour by discussing the company’s employee-partner engagement concepts that help promote workplace safety, a key component in a multi-faceted optimization program that emphasizes its employee-partners’ voice. Visitors were then guided through the facility to show the organizations safety procedures across different aspects of the plant including fleet safety, industrial wash alley safety and much more.
Lewis summed up the Summit experience as both a presenter and attendee when he said, “I enjoy meeting the people of the industry as they tell their stories. You get a wealth of knowledge when you get to speak to people who have decades of experience running plants.”
TRSA Canadian Roundtable discusses current issues
(Report from TRSA)
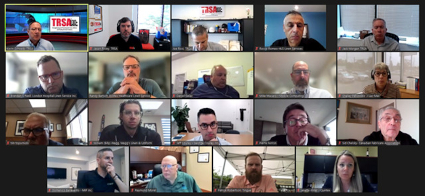
A group of 30-plus Canadian laundry operators and supplier partner executives discussed a range of regulatory concerns affecting the industry during TRSA’s Canadian CEO/Executive Roundtable on May 16.
TRSA President and CEO Joseph Ricci kicked off the 90-minute online session by welcoming Canadian colleagues and inviting them to participate in an open dialogue on issues of concern such as wastewater-compliance rules and the need to promote the use of reusable healthcare personal protective equipment (PPE) in the aftermath of the COVID-19 pandemic.
Next, TRSA’s Vice President of Government Relations Kevin Schwalb offered a quick overview of regulatory issues now pending before the U.S. federal government and among various states. Example include:
Pending restrictions on fleets using conventional fuels: California recently finalized rules calling on companies to implement 100% zero-emission commercial vehicles by 2035, a dozen years from now. Some 14 other states, including New York, Maryland and Colorado are following suit, modeling their restrictions on California’s rules. Canada’s moving in a similar direction – if not quite as aggressively – to mandate zero-emission vehicles. Click here for details. Schwalb noted that the federal or state governments could postpone the compliance deadlines but that’s not guaranteed.
PFAS in wastewater: The U.S. Environment Protection Agency (EPA) and various states, such as Michigan, are implementing restrictions on wastewater containing per and polyfluoroalkyl substances (PFAS) that officials believe are linked to health problems in people. Officials have singled out a minute number of the roughly 5,000 PFAS compounds, such as perfluorooctanoic acid (PFOA) for strict limits.
The EPA wants to dramatically reduce the use of these “forever chemicals” that don’t break down in nature and are present in manufactured goods such as isolation gowns and fire-resistant clothing. Planned limits would allow only 4 parts per trillion of PFAS in wastewater, an amount so miniscule that it’s almost undetectable, Schwalb said.
Microplastic pollution: State officials in California are considering requiring all commercial and consumer washing machinery to include costly filtering equipment to eliminate plastic waste.
For their part, the Canadian operators and suppliers in attendance said they’re facing regulatory issues at least as challenging and in some cases, more so than those in the U.S. Tim Topornicki, president of Topper Linen Supply, Toronto, noted that he recently installed a dissolved air floatation system to remove excess oil and greases in wastewater prior to discharging it. The company also must pay carbon taxes on fossil fuels, a fee not yet widely imposed in the U.S.
Another operator, Janette Millar, COO of Quintex Services Ltd., Winnipeg, noted that her company installed an expensive reverse-osmosis system several years ago to keep pace with the area’s rigorous wastewater-compliance requirements.
On the healthcare front, Schwalb noted that TRSA is working both at the federal level and in various states to encourage the use of more sustainable reusable iso gowns and to discourage the home washing of scrubs and other healthcare workwear garments due to hygiene concerns. Schwalb noted that widespread shortages of disposables arose during the COVID-19 pandemic, as demand spiked and manufacturers – based mainly in East Asia – couldn’t keep pace with hospitals’ requirements.
TRSA laundry operators stepped up to the challenge with reusable iso gowns that could be laundered and reused. Now, with the pandemic largely over, many hospitals are reverting to disposable PPE, thus leaving themselves vulnerable to future shortages should another pandemic arise. In response, Schwalb is leading an effort with members of Congress to send a letter to Secretary of Health and Human Services Xavier Becerra asking him to direct hospitals to maintain a 50-50 balance of reusable vs. disposable PPE to protect patients and healthcare staff. The draft letter also asks Becerra to have the agency conduct a study of the benefits of reusable healthcare PPE.
As for outreach at the state level, a bill recently introduced in New York with TRSA’s active support, would mandate that hospitals maintain a 50-50 mix of reusable vs. disposable PPE.
Canada faced a similar crisis of shortages of disposable gowns when demand spiked during the pandemic. As in the U.S., Canadian commercial and central laundries helped fill the gap with reusable gowns. Randy Bartsch, chair and chief executive of Ecotex Healthcare Linen Service, a Vancouver-based group of laundries, said that both the Canadian federal government, along with various provinces, through a special Pandemic Emergency PPE provisions order, procured millions of disposable gowns during the pandemic.
The problem is many arrived too late to aid in the pandemic response. In Ontario, as an example, they now have more than 46 million surplus gowns in storage, many that do not meet healthcare specs. These emergency PPE items represent a “sunk” cost to the government, and their shelf life is limited, said Bartsch, who is also vice chair of TRSA. Healthcare in Canada operates on a “universal access” model and is funded by government through a “single payer” system.
The federal government apportions tax dollars to each province to fund the full spectrum of healthcare provided by hospitals and community health facilities. While reusable gowns are used in Canada more extensively than in the U.S., laundry operators see pressure on hospitals to use up the disposable stock before its expiration date, thus discouraging replenishment of reusable stock.
Schwalb said TRSA would be happy to assist Canadian operators in their advocacy efforts regarding healthcare, environmental and other issues. Ricci closed the online program by noting that TRSA and Canadian operators and suppliers will have an opportunity to extend their discussions of policy and other business issues this fall at TRSA’s Canadian Production Summit & Tours. Scheduled for Oct. 4-5 in Toronto, the program will feature expert speakers and networking opportunities, as well as tours of technically advanced plants. Ricci encouraged anyone with suggestions for the TRSA event in Toronto to contact him at jricci@trsa.org.
DLI Advanced Course #382 graduates multinational class
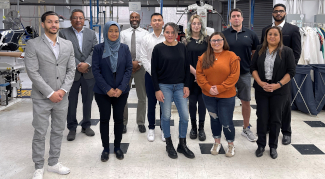
Isaiah M. Roldan, Wedding Gown Preservation Co., Endicott, NY; Aryani Mohamad Hasseri, Noble Medtech Sdn Bhd, Kuching, Sarawak, Malaysia; Ofelia Yessenia Medina, Dry Clean Super Center, Collierville, TN; Courtnie Beverly, Holiday Cleaners, LLC., Demopolis, AL; Judith Ordonez, Martinizing of Benbrook, Fort Worth, TX.
Back row (l-r):
Abang Ismawi Abang Ali, Noble Medtech Sdn Bhd, Kuching, Sarawak, Malaysia; Michael Pulliam, Mi Cleaners, Lanham, MD; Jimmy Lam, Strathfield Dry Cleaners, Strathfield South, New South Wales, Australia; Brittany Fuhrman, Wedding Gown Preservation Co., Endicott, NY; Tony Bettinazzi, CaaStle, Groveport, OH; Gogul Nalainathan, North York, Canada.
Mark Villareal, former Navy diver, educator, and real estate business owner, entered the cleaning business when he bought a drop store in Houston, Texas, two years ago. He found success with the drop store and expanded by adding a full plant to his Midtown Cleaners & Tailors operation in August 2022. “I was able to turn [the drop store] around but when it came to the plant, I realized I was walking into a whole new solar system of information for me and I felt really intimidated.” He encountered a problem with a stain and contacted the Stain Wizard [A.L. Wilson’s Jeff Schwartz], who referred him to the Southwestern Drycleaning Association, who referred him to DLI and its School of Drycleaning Technology.
He enrolled in DLI’s Spring 2023 Introduction to Drycleaning Course calling it “very eye-opening.” He said, “There are two facets that I really enjoy. The first part is collaborating with fellows from the industry. We have all sorts in the class,” he said. “I happen to be an owner, we have general managers, pressers, so it allows me to get a different perspective from different businesses from around the country and how they’re doing their jobs individually and how they’re managing their plants in these different areas,” he said.
“The second, probably the most valuable part of being here, is the hands-on experience,” Villareal said. “Everybody learns differently. For me, I’ve always been a book learner. Give me a book, I’ll memorize it, take a test, no problem. But this is dry cleaning. This is hands-on. So, when we go back to ‘The Lab’, probably the best-looking dry cleaning plant you could find, and you stand in front of that spotting board, that’s when things become real,” he said.
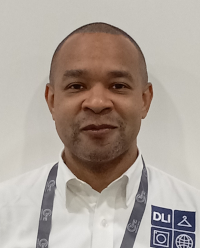
“We have an amazing instructor, Brian Johnson who is great in the classroom, very informative, but when he gets behind the spotting board, you can tell he’s at home,” he said. “That level of confidence allows me confidence to go about it. If you’re going to mess up, this is the place to do it. That type of practical application is the most valuable aspect of the course.”
Ryan Brown with Dublin Cleaners, a third-generation cleaning business in Columbus, Ohio, said he attended DLI’s course because he’s been working in the industry for 12 years. “Everything I did was front of the house: customer service, sales, big into the technology side but I really knew nothing about how our product is created,” he said. “I knew nothing about pressing, the dry cleaning, the chemicals, fabrics. It’s crazy – 12 or 13 years go by and how much education there is still to be learned,” he said. “Attending this DLI class helps me train my customer service reps, my drivers, the customers on things I probably wouldn’t have known. Now, with this class I’m educated even more.”
“Our CEO and President, Brian Butler, empowers our company to become educated. He really wants to have us be trained so we can train our employees and our employees can train our customers,” Brown said. “Between doing this and other educational seminars, we can be the best we can be.”
“Day One was probably a bit overwhelming, learning about things I just didn’t understand on the chemical side,” Brown said, noting the course’s volume of information. “For me, I loved the hands-on training. Being on a utility press or a hot head, being on a spotting board and understanding how to actually get a stain out of a garment is amazing. The hands-on approach in a class like this is honestly priceless.”
CHECK OUR EVENTS CALENDAR FOR UPCOMING CLASSES.
Kreussler, Inc. and the Ohio Fabricare Association extended scholarships to several students in DLI’s 382nd General Drycleaning Course.
Fabricare Canada offers the Tom Kimmel Scholarship to DLI once a year, for either the beginning or advanced course. Open to Canadians who speak English and work in a dry cleaning plant. To apply, send an email of why you’d like to take the course to becca@fabrciarecanada.com.
Nalini Ramki celebrates her 2nd Anniversary at the helm of Suede Master Leather Cleaners in Toronto
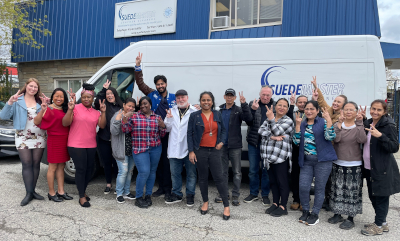
Taking a leap of faith can be daunting, especially when it comes to purchasing a business during a pandemic. For Nalini Ramki, it was a risk worth taking when she purchased Suede Master Leather Cleaners in April 2021. “You only have one life to live” was the motto that fueled Nalini’s drive and passion. Along with a clear vision for business development, she brought a new energy and leadership style as the cornerstone for growth.
Nalini shared, “It has taken sweat, tears, and sleepless nights to get to the second anniversary! We got here in one piece and smiling – we are patting ourselves on the back for it!”
Over the past two years, Nalini has steadily increased services and forged lasting relationships with dry cleaners across Canada and New York State. As their name suggests, they are leather, suede, and fur garment care experts. Suede Master also describes itself as the largest bridal-wear cleaner in Canada, taking care of each wedding gown no matter the intricacy. They also clean luxury garments and specialty rugs.
In 2002, Suede Master was one of the first in Canada to utilize the proprietary silicone-based system. In 2021 when Nalini purchased Suedemaster she was committed to converting the dry cleaning operation to 100% GreenEarth. Today, she is happy to report the conversion is complete.
Maytag designates May as Maytag Month
Special financing available to qualified buyers
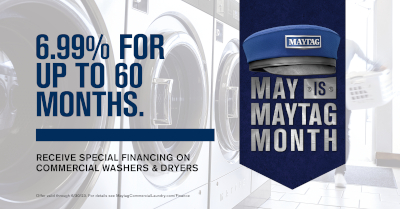
Maytag is using its “May is Maytag Month” to encourage commercial customers to replace outdated or inefficient equipment with new Maytag Commercial Laundry washers and dryers.
The special financing offer only lasts through June 30, 2023. Coin laundry store owners, on-premise laundries, route operators and apartment building owners are eligible for 6.99% financing for up to 60 months when they finance through Maytag Commercial Laundry and Eastern Funding. More offer details can be found at MaytagCommercialLaundry.com/financing.
“In the current economy, many business owners are looking for ways to improve productivity or profitability, and new equipment can help them do that. We don’t want the cost of financing to get in the way,” said Amy Gardner, Maytag Commercial Laundry Director of Sales, Service and Parts.
“Traditional lenders are often not very familiar with commercial laundry operations or mostly-cash businesses like laundromats. So we work with lenders with industry experience to offer rates that can be much more favorable than those of other lenders.”
Gurtler Acquires OMNI Solutions UV Technology for Tunnel Systems
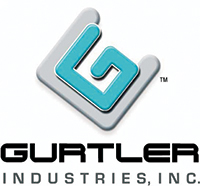
Gurtler Industries announced on March 30 an agreement with Omni Solutions to acquire full rights to Omni’s Sulaos, Smart Ultraviolet Light Advanced Oxidation System. Under the agreement, Gurtler will own the Sulaos technology exclusively for the tunnel system markets across the world. Gurtler will also partner with Omni’s current users of their technology in existing tunnel systems.
Greg Gurtler, president of Gurtler says, “We are very pleased to be able to acquire this technology. The Omni UV System enhances the oxidation process in tunnels, increases stain removal and whiteness, and most importantly, significantly reduces microbial contamination in the tunnel.”
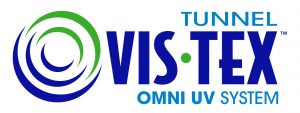
Gurtler will be rebranding the system under the Gurtler Vis•Tex™ family of equipment and dispensing systems. The system is designed for today’s modern tunnel washers and will be renamed as the Vis•Tex Omni UV Tunnel System. The system treats press water with a combination of potent oxidizers and ultraviolet light and returns the treated water to the rinse zone, virtually eliminating organic contaminants, which provides reduced microbial contamination in the rinse zone.
Two years ago, Gurtler and Omni Solutions entered into an exclusive marketing/distribution agreement for the Sulaos equipment. Matt Wenzel, executive vice president of Gurtler observes, “The decision to fully acquire this UV Tunnel System technology was natural outgrowth of our exclusive distribution agreement. Over the last two years Gurtler has learned about the major benefits of this exclusive technology and how to best adapt it to today’s tunnels operations and the market’s needs.”
Under the terms of the agreement, Gurtler will take responsibility for the existing Omni UV Tunnel Systems in the market. Wenzel says, “Gurtler will be contacting all of the current users of the UV system in their tunnels and reviewing their operations to make sure they are taking full advantage of this unique technology’s capabilities.”
“We are excited about the adoption of this technology by Gurtler,” Omni Solutions founding member Andrew Rupnow said. “We look forward to working with their talented team throughout this process to ensure a smooth transition for our existing Sulaos customers. Gurtler’s advanced support infrastructure and deep knowledge in the commercial laundry industry will help advance this technology to the next level. Omni will continue focusing on its primary business, the LUX™ UV Laundry Program, and would like to sincerely thank the Gurtler team for their continued partnership and support over the years.”
CLATA Annual General Meeting Makes History
The Cleaners & Launderers Allied Trades Association’s AGM was held on March 30, 2023 at Scaddabush Restaurant in Etobicoke, ON.
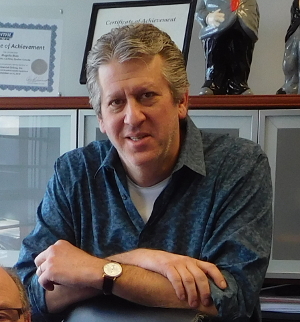
Earl Eichen completed his long time presidency of 7 years and was commended for guiding the Association through a difficult few years, and for re-vitalising the CLATA Brand at the CLATA Canadian Receptions during the Clean Shows in New Orleans and Atlanta.
Ashlynn McConvey was voted in as the new president making her the first female to lead the association. Apart from being the first female CLATA President, she is also the 3rd generation of McConveys to hold the position. Her grandfather, Darcy, was one of the founding members of CLATA in 1958.
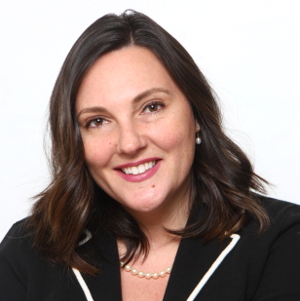
“I would like to thank Earl Eichen for stewarding the association for many years, including the very precarious COVID times. The Canadian CLATA reception in Atlanta at Clean 2022 was outstanding and a welcome return for all of our members. I am honored to step into the role of President of our organization in the third generation as a McConvey and the first ever as a female!”
2023-24 Board of Directors
- Ashlynn McConvey (Dalex Canada Inc.), President
- Steve Freeman, Secretary & Past President
- Trevor Holmes (Seitz Inc.), Treasurer & Past President
- Malcolm Caldwell (Harco), Director
- Patrick Robertson (Tingue Canada), Director
- Denis Lamarre (Lavanett), Director
- Marc-Antoine Gelac (Kannegeisser Canada), Director
- Nicolas Legault (Gurtler Industries Canada), Director
- William Kahan (Unipress), Director
- Artur Keyes (Extox Industries), Director
- Earl Eichen (Lavanett), Immediate Past President
The annual golf tournament will be held on Thursday September 7th at the Bay of Quinte Golf Club. Further details will be shared at a later date.
The next AGM is scheduled for March/April 2023.
UNX-Christeyns honored with 2023 SafeTRSA Safety Excellence Award
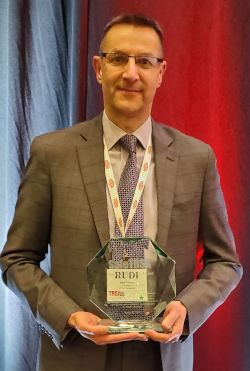
UNX-Christeyns was recognized by the industry for the third consecutive year on March 22 when company President Rudi Moors accepted the 2023 SafeTRSA Safety Excellence Award. It was presented at the TRSA’s 13th annual Legislative Conference industry awards dinner held at the Westin City Center in Washington, D.C.
UNX-Christeyns won the award for completely revamping its liquid laundry chemical product labels. A new color-coded system provides care and safety information for each product grouping. Team members are also involved by training and assisting distributors and customers on the new labeling system.
“The UNX-Christeyns label improvement effort reflects the company’s embrace of safety as a true corporate value, a key characteristic of companies that win the SafeTRSA award,” said Ken Koepper, TRSA Director of Member and Industry Relations. “Better labeling touches the bases that score laundry safety success; getting employees involved in recommending improvements, prompting top management to fund these, and devising new training and communication that utlimately culminates in better protection.”
“As one of our core values, we place safety among the highest priorities for customers, distributors and employees,” said Moors. “To achieve the best results, it requires us to place an emphasis on making chemicals as safe as possible. On behalf of the entire team at UNX-Christeyns, we are deeply grateful to receive this award.”
The company won the TRSA Above & Beyond Service award in 2022 for providing exemplary service to customers. It followed the 2021 TRSA Company Community Service award where the company was recognized for its involvement in local events. Employees continue to volunteer their time and participate in various community fundraisers and projects. This includes cleaning all uniforms of players competing in the Little League Softball World Series, which returns to Greenville, N.C., in August for its third consecutive season.
Jensen-Group reports high revenues and return to pre-Covid levels
Revenue of 341.6 Million EUR for 2022, an increase of 31.5% compared with 2021.
The Jensen-Group is back at pre-Covid-19 activity levels, despite strong headwinds from supply chain disruptions and their impact on our business activities. The setbacks in the hospitality sector of the past years are now limited to certain areas of the globe. They are eagerly awaiting recoveries in these countries, and the business opportunities this will generate in the future.
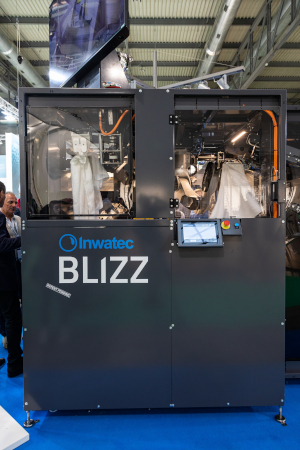
Investments for the future
The Jensen-Group assessed that automated solutions using robotics and AI would be increasingly in demand. In its fifth year of co-operation with Inwatec Aps, the company commissioned many new laundries on all continents, in which robotics enjoyed the same self-evidence as tunnel washers and integrated finishing lines. The collaboration reached a new peak in 2022 with the development of the new BLIZZ, a new approach to automate the feeding of terry towels into a folding machine. Automated solutions are said to improve the total sustainability of laundries, as they prolong the life of textiles and machines and guarantee highest health and safety levels.
Sustainability has been part of the Jensen DNA ever since its launch of the CleanTech concept in 2008, which was well demonstrated with all exhibits displayed at Clean Show/Atlanta and Expo Detergo/Milano. The launch of the new XR dryer was a major breakthrough: It will set new benchmarks in productivity thanks to its extra airflow for a greater air exchange and up to 15% higher evaporation capacity.
In 2022, the company officially opened its re-built American manufacturing plant which had been destroyed by a hurricane. The Jensen factory in Panama City, FL engineers and produces material handling solutions as well as washroom equipment for the US market.
The Jensen factory in Xuzhou/China was the first within the Jensen-Group to install solar panels as well as new e-bike charging stations as part of a “bike-to-work” initiative. The team at Jensen China is said to be overjoyed that the three-years-long lockdown has finally come to an end, and that production is running at 100%.
Outlook
The view of 2023 is clouded by geopolitical and military threats as well as a possible slowdown in demand due to an economic recession in key markets.
“We are restrained positive about the future, as we count on achieving normalization in the supply chain by the end of 2023”, confirms Jesper Munch Jensen, CEO of the JENSEN-GROUP.
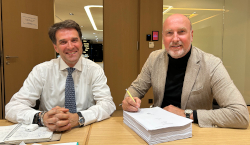
On March 9, 2023, the Jensen-Group and Miura have agreed to a joint-venture that will make the Jensen-Group a key partner for Miura’s wholly owned subsidiary Inax, one of the main manufacturing and distribution companies for heavy-duty laundry equipment in Japan.
Preceded by the USA and Germany, Japan is the third-largest economy in the market. Its laundry industry is characterized by high-tech solutions, highly automated processes, and the need for hygienic solutions. With this Joint Venture, Jensen is boosting its market presence in Japan.
“We started our Go East strategy a long time ago. This joint venture is the culmination of many years of hard work and dedication. I have always wanted to be a market leader in Japan, which is one of the largest and most automated heavy-duty laundries markets in the world”, confirms Jesper Jensen.
For further information, contact: Jesper Munch Jensen, Chief Executive Officer, Tel.: +41 34 426 1646 – marketing@jensen-group.com
Association of Linen Management News
ALM Announces UNX-Christeyns Support for ALM Quick Start
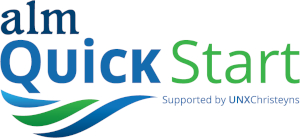
Recognizing the value and need to help educate newcomers to the industry, the Association for Linen Management (ALM) created ALM Quick Start. This online eLearning opportunity allows incoming textile care industry professionals to quickly and effectively gain a consistent industry framework. UNX-Christeyns recently joined ALM in supporting the program as part of their ongoing efforts to provide the best possible resources for the betterment of the industry.
ALM Quick Start was initially introduced with a soft launch at The Clean Show 2022 in Atlanta. The non-profit trade organization’s mission is to advance industry excellence, and it has developed multiple education, training and certification programs. ALM Quick Start represents the next phase of an ambitious campaign where supervisors and managers can receive training to better understand the industry and their business.
“One of the main concerns we are hearing from our members is the shortage of skilled labor. There simply are not enough workers and it is impacting their operations,” acknowledged ALM’s Executive Director, Sarah Brobeck, MBA, RLLD.
“We believe education is part of the solution, and that’s exactly what ALM can provide. ALM Quick Start is designed to shorten the learning curve and help new hires in supervisory and management roles get up-to-speed with accurate and consistent information. Having well-informed and trained employees will improve efficiency and aid in employee retention. UNX-Christeyns understands this value and we are truly pleased to be joining forces with them.”
ALM Quick Start focuses on three disciplines: wash chemistry, equipment management, and production & operations. Laundry supervisors, vendor salespeople and service workers can complete the program in as little as three hours, and the courses are available for up to 90 days after they enroll.
“We applaud ALM for the work they do. They have been a trusted and longtime go-to source for the industry,” said Josh Lilley, CEO of UNX-Christeyns. “ALM Quick Start is another shining example of their leadership efforts. We view this initiative as a critical component to ensure a stronger future for our industry. That is why we support ALM Quick Start and plan to help grow it together with ALM.”
For more information visit the website.
ALM’s 2023 IMPACT Conference Exceeds Pre-Pandemic Attendance
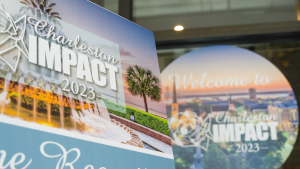
The Association for Linen Management (ALM) sold out their 2023 IMPACT Conference, held last week in Charleston, South Carolina, exceeding pre-pandemic attendance levels! This rapid event recovery reflects IMPACT’s reputation for high-level education in an intimate environment, which is ripe with opportunity for business development, problem solving, and strategic thinking.
“The energy and enthusiasm of attendees was off the charts,” shared James Mangini, RLLD, ALM Board President and Senior Director of Supply Chain Logistics for MaineHealth. “The amount of networking that took place, business being conducted, and minds being challenged and enlightened with actionable takeaways from the educational programming was phenomenal.”
Featured presenters at the conference included Jerry Holl, author of the three-time international Award-winning book, Downhills Don’t Come Free; Dan Lundergan, MHA, CEO of University of Utah Health, Hospitals and Clinics; and Jay Juffre, Executive Vice President of ImageFIRST.
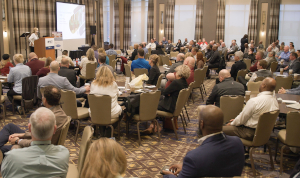
This year’s conference premiered a new business-to-business forum, IMPACTful Connections, featuring one-on-one meetings between allied trades professionals and laundry and linen operators. Participants raved about the opportunity to learn about products and services.
“We’re always looking for new innovations and open to looking at new equipment in the laundry,” said Paul Jewison, RLLD, CLLM, and President of Textile Care Services in Rochester, MN. “Our company was able to meet with eleven companies representing equipment, textiles, and laundry bags. This was an efficient way to learn about a lot of new products and technology in a short period of time. We’ll definitely participate next year.”
Working to make the new IMPACTful Connections beneficial for both the operators and the vendors was a key focus for ALM staff in planning the new event. The success of that effort was seen by the comments from those who exhibited as well.
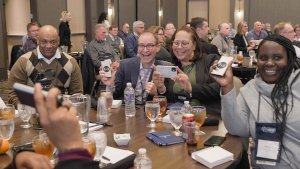
“ALM’s foresight to create meaningful ways to connect with our customers, such as IMPACTful Connections, is why our organization chooses to participate as a top-tier sponsor,” expressed Nicole Grubich, RLLD, CLLM, Vice President US-Business Unit, MIP, Inc.
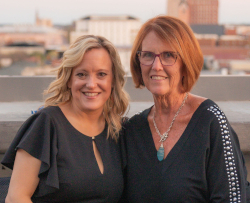
MIP returned for the sixth time as an exclusive sponsor of IMPACT’s most popular evening event, which was held at Charleston’s highest rooftop venue, The Pour Taproom. During the event, attendees and ALM’s Board and staff bid their final farewells to retiring executive director, Linda Fairbanks, who was honored with a champagne toast and poignant speeches from long-time colleagues.
“We’re already strategizing for an even bigger conference in 2024! This is just the beginning of many great things to come for ALM and its members,” said Sarah Brobeck, MBA, RLLD, ALM’s Executive Director. “We’re also working on new avenues to continue providing valuable resources and innovative ways for members to connect throughout the year.”
Avery Dennison Acquires Thermopatch
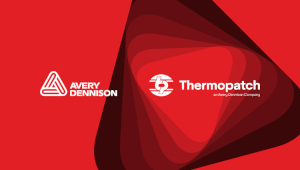
Avery Dennison announced that it has completed its acquisition of Thermopatch, a leader specializing in labeling, embellishments, and transfers for the sports, industrial laundry, workwear, and hospitality industries. Thermopatch will become part of the company’s Solution Group, Apparel Division. The acquisition will allow the combined business to build on collective industry knowledge, leveraging the company’s know-how, quality, and service to drive growth in external embellishments. Thermopatch, headquartered in Syracuse, New York, had revenues of approximately $40 million in 2022, with around 200 employees, with operations in North America and Europe.
Fabricare Canada checked with Thermopatch to see if there would be changes in Canada, and we were told, “Everything will remain the same.” Same phone numbers, same representatives, etc.
“We are thrilled to welcome Thermopatch into the Avery Dennison family. It’s an excellent strategic fit for expanding our position in embellishments, labels, and transfers,” said Michael Barton, senior vice president, and general manager RBIS Apparel Solutions. “We continue to accelerate our progress within our external embellishments business, going from strength to strength and entering new markets. In doing so, we are building on last year’s launch of Embelex, Avery Dennison’s full-service, end-to-end platform for on-product branding, graphics, and trims, and accelerating our strategy to drive growth and innovation in this market. Combining Thermopatch and our strong product portfolio and long-standing customer relationships will enable us to continue to grow and deliver value for all our stakeholders.”
“This next chapter is a great opportunity for us,” said Tom DePuit, CEO of Thermopatch. “I am proud of what we as a business have accomplished over the last 85 years and I am confident that Thermopatch will continue to thrive. With the combined capabilities of both businesses, we can further advance innovation and provide increased value for our customers and the industries we serve while continuing to deliver the same quality of service.”
K-Bro Acquires Paranet
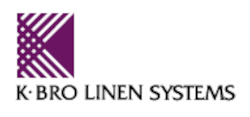
K-Bro Linen Inc., Edmonton, Alberta, Canada, recently announced that it completed its acquisition of Buanderie Para-Net (Paranet), according to a news release.
K-Bro completed the transaction for an enterprise value of $11.5 million and a potential earnout of $1.9 million. Paranet is a private laundry and linen services company for the Quebec City healthcare and hospitality markets. The purchase price will be satisfied by drawing down on K-Bro’s revolving credit facility.
“With continued momentum in our business, we have been refocusing on strategic acquisitions and have an active M&A pipeline,” said Linda McCurdy, President and CEO at K-Bro. “The Paranet acquisition is another example of our strategy of acquiring high-quality operators with leading market positions, enabling K-Bro to grow market share in key regions. The acquisition also provides us with additional operating efficiencies, capital expenditure synergies and significant growth capabilities. We remain well positioned from a balance sheet and liquidity perspective, and will continue to be disciplined as we evaluate acquisitions.”
PayRange Launches #IHEARTPAYRANGE Contest for Users
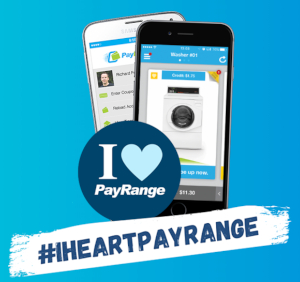
PayRange Inc., a manufacturer of a mobile payment app and payment hardware for automated retail, announced the launch of the #IHEARTPAYRANGE contest for users of the PayRange App. The contest is intended to celebrate and thank the more than 6 million loyal PayRange users.
To enter, a user simply uploads a photo to Instagram with a comment sharing why they love PayRange, tag @payrange and use the hashtag #IHEARTPAYRANGE. Winners will be selected from the entries based on how much the user’s story inspires PayRange. One grand prize winner will receive free purchases for a year, paid out as 250 free purchase credits valued at up to $4 each. Nine additional winners will receive free purchase for a month, paid out as 25 free purchase credits valued at up to $4 each. PayRange will announce the ten winners on May 1, 2023, on the company’s Instagram page.
“Our users are passionate about PayRange and their love for the service.” stated Stephanie Cordisco, Executive Vice President of PayRange. “We want to share this enthusiasm and offer users a chance to win free purchases for a year they can use on any PayRange enabled machine, from vending to laundry, carwash to amusement, and more.”, finished Stephanie.
PayRange is covering the cost of the prizes, and operators who’s machines the free credits are used on will be paid in full like any normal transaction. PayRange operators will be provided with a promotional poster to support the contest which will run from March 7, 2023, through April 18, 2023. In addition to operator marketing support, PayRange will promote the consumer contest with in-app alerts, user email notifications, a contest website and more. Additional details and complete contest rules are available on the website.
Hohenstein develops new test method for micro fibre impact
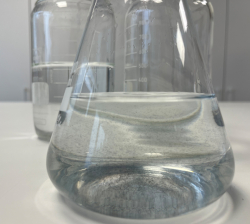
Testing service provider Hohenstein has worked with partners to create a new standardized test method for detecting and classifying the environmental effects of textiles during washing. DIN SPEC 4872 combines analysis of fiber release, biodegradability and ecotoxicity.
The test method according to DIN SPEC 4872 shows how many fibres are released during textile laundering, how well these fibres degrade in wastewater and how harmful the fibre residues are to the environment.
Studies have shown that washing textiles releases microfibres into the wash water, which cannot be sufficiently retained by wastewater treatment plants. Synthetic fibres pose the greatest risk to the environment because of their longevity and inability to biodegrade.
However, Hohenstein project manager Juliane Alberts does not give the all-clear for biodegradable fibres and natural fibres : “Biodegradability alone does not mean that pure natural fibres , for example, are completely harmless to the environment. They, too, remain in ecosystems until they completely degrade and can also have a negative impact. In addition, additives, auxiliaries or finishes used in textile production can further slow the degradation process and leach into the environment.”
The new standard is said to enable textile producers and suppliers to test, evaluate and compare products for fibre release during washing and environmental impact. Juliane Alberts sees this systematic evaluation as an opportunity for the textile industry to take the initiative on environmental impact: “Our reliable data can be used as a basis for more targeted product development. This is a way to actively and consciously control further environmental pollution.”
With more than 40 offices and laboratories, Hohenstein is an international partner for independent testing, certification and applied research around the human-textile-environment interaction. They develop science-based methods and standards that consider the user in real life, not just in the lab. Through standard or customized testing, and interpretation of the results, Hohenstein experts solve problems, verify claims and help partners bring better, safer products to market – more sustainably. Hohenstein is a founding member and leading provider of the OEKO-TEX® portfolio of services, and is certified by the U.S. Consumer Products Safety Commission (CPSC ID #1058) as a third-party, independent laboratory for CPSIA compliance verification. Hohenstein.US
Gurtler Holds Global Sales Conference
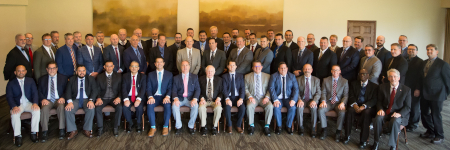
Gurtler Industries held its Global Sales Conference in December. The three-day conference was held at the Briar Ridge Country Club in Schererville, IN, just outside of Chicago, and was attended by over 75 members of the Gurtler sales and service team, headquarters support team, and management.
Representatives were present from the USA, Canada, Mexico, and Australia. Due to the pandemic, this was the first time since 2018 that Gurtler brought together the sales and service team for the conference which focused on technical and safety training, recognition of top sales performers, and a celebration of Gurtler’s 40th Year Anniversary.
As part of Gurtler’s continuing effort to improve customer service, Gurtler invited four customers from the industrial/F&B and healthcare laundry markets to participate in a panel to review how they perceive their expectations and standards for service from their chemical representatives. In addition, during the conference representatives from six major manufacturers of standard and tunnel washing systems shared their latest innovations and technology with the sales and service team and the manufacturers heard feedback from the service team on how the systems perform in Gurtler’s markets.
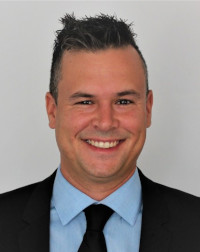
At the conference, Gurtler recognized the top sales and service performers from the last few years. The salespersons of the year for the last two years were also announced. Nicolas Legault from Ontario, Canada, earned the honor for 2021 and Joe Valdez of the Pacific Northwest was named salesperson of the year for 2022.
Lastly Greg Gurtler, President and Bill Gurtler, Chairman of Gurtler Industries shared their thoughts on the 40th Anniversary of Gurtler’s founding in March of 1982. Plus, they presented an employee appreciation video that focuses on the role that our entire team plays in providing superior customer service across the entire laundry market. The video is posted on the Gurtler YouTube page.
Gurtler Industries is a leading manufacturer of advanced detergents, specialty chemicals and injection systems for the commercial laundry industry. From its headquarters and research center in suburban Chicago, Gurtler supports the entire spectrum of the laundry industry, including healthcare, hospitality, industrial uniforms, shirt laundries and textile rentals. Gurtler is a family company now in its third generation, maintaining its tradition of excellence, innovation, and service.
For more information, contact Gurtler Industries at 1-800-638-7300 or visit www.gurtler.com
HLAC Releases 2023 Standards
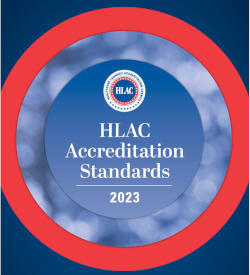
The Healthcare Laundry Accreditation Council released its 2023 updated standards to guide the industry in maintaining the highest possible quality work. Some highlights include: More emphasis on standards impacting hygienically clean linen More emphasis on functional separation and clean/soil issues Less emphasis on items that do not directly impact hygienically clean linen (i.e. eyewash stations) More flexibility for operators who employ different methods to obtain hygienically clean linen Easier to read standards, less duplication, better referenced standards You can watch the webinar or access the standards on the website.
Harco Canada Open House in Quebec
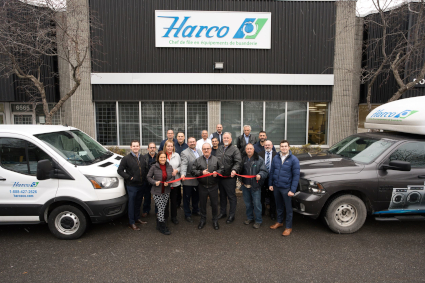
Harco Canada Inc. welcomed dozens of customers and suppliers to an open house in December. The open house celebrates an expansion for Harco that took place in February 2020 (just before the shut downs) in the province of Quebec.
“We more than doubled the square footage and the warehouse is 3 times larger than our previous warehouse space,” said Malcolm Caldwell, vice president of sales. “We are excited to offer more inventory of equipment and parts to our Quebec customers.”
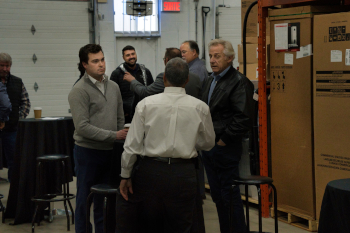
The comments from attendees were positive, and those who had visited the former building liked the fact that the new warehouse is much larger and has two types of forklifts to move and store the products, making it much more efficient.
Attendees also commented on the supply of parts in the inventory and how well organized the parts area is. Customers liked the fact that there is a parts counter that they can access without having to go through the main office.
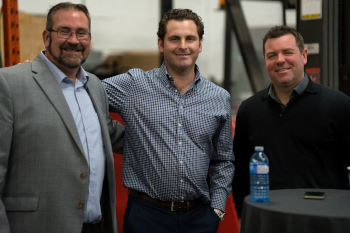
To facilitate easy equipment pick up, the facility includes a ramp and loading docks. so any type of truck or trailer can be accommodated.
The Harco office team are pleased with the way the new facility allows them to be more organized and able to focus on customer requests.
Harco senior management attended the event, and service sessions and demonstrations were conducted throughout the day. The Harco team look forward to the opportunity to support the laundry equipment, parts and service needs of Quebec and eastern Ontario customers.
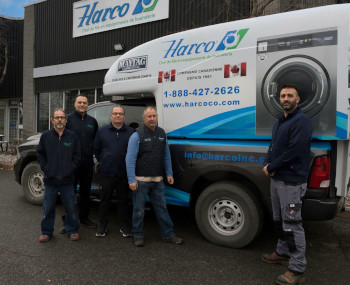
DLI and CCA Defeat Plastic Bag Ban
Comments from Mobilized Members Saved the Day
The Drycleaning & Laundry Institute (DLI) and California Cleaners Association (CCA) mobilized members to defeat a proposed ban on drycleaning bags in the city of Los Angeles.
DLI and CCA learned about the city’s proposed ban about one week before the city’s December 1 vote. DLI and CCA immediately worked to mobilize members and share comments in defense of the industry’s use of poly bags.
“DLI and CCA headed off what might have been a very costly outcome for the industry,” said DLI CEO Mary Scalco. “Once enacted, measures like this are often replicated by other municipalities and states across the country.”
American Drycleaner interviewed Scalco and CCA President Toran Brown who is also DLI’s District 8 Director and owner of Rytina Fine Cleaners and Launderers in Sacramento, California, about the issue for its special report, “L.A. Cleaners, Associations Fight Proposed Poly Bag Ban,” released in audio format on December 8, 2022. The following is a transcript of that report. Readers may also listen to the report on the American Drycleaner website: https://tinyurl.com/4zsm4pdf
Transcript of American Drycleaner’s Special Report Episode 45:
L.A. Cleaners, Associations Fight Proposed Poly Bag Ban
Dave Davis
Hello. This is a special report from American Drycleaner. I’m Dave Davis, Editor of American Drycleaner magazine. Legislators in Los Angeles met on December 1 to consider banning single use plastic bags used in groceries, hardware stores, and other businesses in that area. Many drycleaners feared that the poly bags they use to package and protect their customers’ clean clothes would also be affected by the proposed ban. Their concerns were addressed by both local and national trade organizations who studied the issue and added the voice of the drycleaning industry to the discussion.
The proposal, prepared by the L.A. Department of Sanitation, was heard by the city’s Energy, Climate Change, Environmental Justice, and River Committee. Both the California Cleaners Association on the local level and the Drycleaning and Laundry Institute on the national level, mobilized to get clarification on the issues. Both organizations also submitted letters stating why single use poly bags are necessary in the drycleaning process and why they’d be difficult, if not impossible to replace.
Toran Brown, President of the California Cleaners Association, explains that a former board member of the CCA let the organization know that single use plastics used by drycleaners had recently been added to the review of possibly banned items. The organizations had to work fast to make sure the voice of the drycleaner was heard in the discussion.
Toran Brown
Unfortunately, because of the timing we didn’t have a lot of leeway in order to mobilize a lot of people. We literally had about a week and a half – and worse yet in the middle of all this was the Thanksgiving holiday – so that took a couple of days out.
Dave Davis
The CCA was able to gather members of the southern California area together and reached out to the Drycleaning & Laundry Institute to discuss strategy.
Toran Brown
CCA former board member Jim Douglas really took the lead on this. He contacted L.A. city sanitation, and really began to explore with them what their objectives were, educated them on the implications from an operational standpoint within the industry, and began that dialogue of “Okay, we need to work together to find a viable joint solution.”
Dave Davis
Brown believes that these efforts and dialogues are key in getting drycleaning poly bags excluded from this type of legislation.
Toran Brown
For a drycleaning operation, there’s a much bigger implication for us than there is for a pharmacy or a hardware store that simply is just finding an alternative packaging source for their products.
Dave Davis
This process highlighted the value the trade organizations can provide to drycleaners not only in Los Angeles, but for the industry in general.
Mary Scalco, CEO of DLI, believes this type of presence is needed both at the local and the national level.
Mary Scalco
To me, advocacy is sort of well-placed conversations. You need to talk to somebody and you need to know who to talk to and what to say. So, when it’s on the local level, they know who knows who. You know, who knows somebody on the city council? Who can talk to somebody in the legislative arena out there? On the federal level, it just becomes a more global conversation.
Dave Davis
Scalco believes that being able to bring her bright cleaners together on a regional or a national stage is one of the main benefits of having trade associations.
Mary Scalco
We have the ability to mobilize all the drycleaners in the country if we had to for certain issues and we’ve done that in the past. We were prepared to try and do that if California escalated to the next level. Because it’s important for people to hear, I think, when you’re making these decisions, whether it’s on the local level or regional or federal or even globally, you need to hear from the industry you’re regulating to find out what those consequences are.
Dave Davis
While the ban on poly bags would have only affected L.A. cleaners for now, Scalco believes it’s important to enter into the conversation early rather than when matters have already been decided on a larger scale.
Mary Scalco
What happens whenever something like that proposal goes through, no matter where it is, it could have ramifications for the entire industry. We want to make sure we’re on top of it whether it’s at a federal level that’s easier for DLI to take the lead on, but in something like the Los Angeles city proposed ban, the California Cleaners Association being the local organization, can probably be a little bit more effective because they can actually go to the meetings and show up in person if they need to. We’ll also fly out if it ever gets to that point, but the idea is anything that happens on the local level has the potential to affect the entire country.
Dave Davis
Scalco feels that government issues, environmental concerns, and business needs don’t have to be a cross purposes but it does take communication to find the correct solutions foreveryone.
Mary Scalco
I would think any association, having those conversations, as long as both parties are willing to listen and to make adjustments, you’re going to come out with a better regulation. You’re going to come out with a better rule that not only protects what they’re trying to protect but also protects the industry as well. You know, we’re sometimes at an advantage because we’re a small business. In most cases drycleaners are small business owners, and nobody likes to put small business out of business. So, if you’re having a conversation where both sides are listening, you can come out with an agenda that works for both people.
Dave Davis
Ultimately, the Los Angeles committee clarified the proposed legislation, addressing the concerns aired by drycleaners and the trade organizations, stating implicitly that the proposed ban would not extend to drycleaners. For American Drycleaner, this is Dave Davis.
11th Annual TRSA Healthcare Conference Pulls in More Than 150 Attendees
Trends, opportunities and challenges are key focus
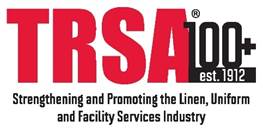
More than 150 operator and supplier partner executives serving the healthcare market sector attended Textile Rental Services Association’s 11th Annual Healthcare Conference in Scottsdale, AZ. The two-day conference featured a full day of industry-specific education followed by a tour of Emerald Textiles’ 65,000-square-foot plant in nearby Phoenix.
“This was a great conference,” said TRSA Vice Chair Randy Bartsch, CEO, Ecotex Healthcare Linen Service. “It was good to see such a good turnout, representing so many people both on the processing side as well as our vendors. This is a great event every year to get together with the people that we work with in the industry. You don’t want to miss it!”
The opening day of the conference kicked off on Nov. 16 with a morning keynote delivered by Ryan Donohue, strategic advisor, NRC Health and The Governance Institute. Titled “Patient No Longer: The Brave New World of Post-COVID Consumerism,” Donohue’s address detailed patients growing expectations and needs, with a focus on how healthcare providers and companies serving the healthcare sector can strategically meet these ever-changing expectations. He also examined the impact of COVID-19 on the healthcare sector and how it led to innovations such as greater use of virtual doctor’s visits.
Donohue is an expert on this topic through his work with many top health systems and hospitals to understand the changes resulting from a more consumer-centric healthcare environment. His clients include the Mayo Clinic, Trinity Health, Baylor Scott & White Health, New York–Presbyterian Hospital, Providence and Partners HealthCare. Donohue continues to research how consumers make decisions and how providers can move to the leading edge in consumer and patient engagement and retention.
After Donohue spoke, attendees heard the tale of how Inova Health System in Northern Virginia designed and produced a custom, reusable isolation gown to counter the personal protective equipment (PPE) shortages brought on by the COVID-19 pandemic. The custom gowns ensured adequate supply of the healthcare system’s second-most-used type of PPE, while also eliminating 213 tons of waste per year due to the system’s former use of disposable gowns. The new gowns are currently in use at two of Inova’s five hospitals. Lucy He, director of infection prevention and control, and Mandy Campanaro, senior service line partner, at Inova Health System, joined Carlos Iniguez, quality assurance and compliance officer, HandCraft Services Inc., Richmond, VA, to discuss the details of this reusable PPE. HandCraft provides laundry services for Inova Health System.
The morning ended with a pair of data-driven sessions recapping the results of TRSA’s recent healthcare survey and long-term care initiative. Kevin Schwalb, TRSA’s vice president of government relations, then provided attendees with a lunchtime update on the latest regulatory and legislative initiatives that TRSA is working on in Washington, DC, and at the state level on behalf of its members and the industry.
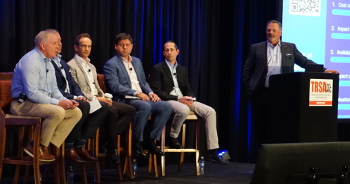
The afternoon concluded with several panel sessions on topics such as the value of reusable healthcare textiles and garments, and the use of marketing and sales to convince long-term care facilities to outsource their laundry. Bartsch moderated the final panel. The session featured five senior executives, including:
- Jason Berstein, president, Nixon Medical Inc.
- Jim Cashman, CEO, ImageFIRST
- Karl Fillip II, CEO, NOVO Health Services LLC
- Andrew Kratky, CEO, Emerald Textiles
- Joe LaPorta, president & CEO, Healthcare Linen Services Group
The panel discussion featured several interactive polls that gave attendees the opportunity to share their thoughts to help steer the dialogue. The wide-ranging panel discussion touched on topics such as the prospect of a recession and its likely impact on the healthcare market, investing in automation, challenges serving the healthcare sector, and instilling culture and values throughout an organization.
“I really enjoyed it,” Kratky said. “This is actually my first TRSA conference that I’ve been to, and I thought it was great. I thought the interaction with the people that were here was really good, the panels were really good and it was great to hear what was going on in different parts of the industry and different regions outside of where we call home in California, Nevada, Utah and Arizona. So it was well-rounded. I really appreciated the opportunity to be here.”
The Healthcare Conference concluded the following day with a tour of Emerald Textiles’ Hygienically Clean certified facility in Phoenix. The 65,000-square-foot plant opened in October 2003. It is equipped with three Pellerin Milnor tunnels, each of which has 10, 150 lb. modules. The facility’s 240 employees process 80,000 lbs. of laundry per day. Emerald Textiles is in the process of expanding the plant to prepare for additional capacity and efficiency. The Phoenix plant is in the process of installing a new Milnor tunnel washer with 10, 150 lb. modules, a 40 BAR single-stage press, along with a rail system for sling bag loaders, a conveyor and a two-cake elevating shuttle. Six Milnor dryers also are being installed to complement the system, each with up to 325 lbs. drying with a two-cake load.
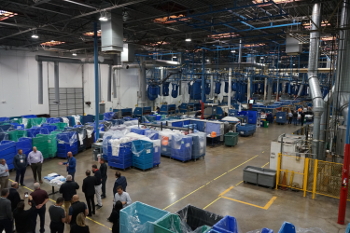
“It’s amazing to see all the new technology, how it comes together, and learn some best practices and new systems,” said Jeff Peterson, sales manager, Spin Linen Management, Omaha, NE. “The plant tour gives us the opportunity to see what innovations are out there that we hadn’t thought about yet. Thanks to TRSA and Emerald Textiles for setting up the tour. It’s been a great experience.”
Several meetings took place the day before the Healthcare Conference’s formal kickoff, including the Hygienically Clean Healthcare Advisory Board and Users’ Group meetings. The Hygienically Clean meetings were followed by a CEO/Executive Roundtable. TRSA President & CEO Joseph Ricci moderated this discussion, which drew more than 40 senior-level executives.
TRSA’s Healthcare Conference was sponsored by five-star partner Kannegiesser ETECH, four-star partners G.A. Braun and JENSEN, premium sponsors Brim, Lavatec, Pellerin Milnor and Unitex International, and supporting sponsors APPI Energy, G.A. Braun, Lac Mac and Pellerin Milnor.
For more information on TRSA, visit the website.
CFA Conference Wrap-up
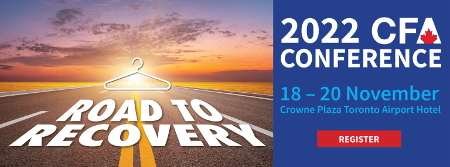
By Sid Chelsky, CFA Executive Director
The Canadian Fabricare Association held another successful conference. I am not going to spell out everything everyone said but will highlight the items they talked about. If you were unable to attend, you missed a great conference.
The first speaker was Karen Maxwell of GreenEarth* Cleaning and as always, she was superb. She spoke on:
- Growing your business
- Building relationships
- Improve customer retention
- Engage with your customers
- Build on reputation
- Increase referrals
- Add more sales – offer more services
- How to reduce claims
- Who are our customers and what do they want
- Environment top of mind and sustainability
- Do it right, and do it on time
- Customers care 20% on product and 80% on service (How you make them feel)
- CSRs must want to make people happy
- Treat your staff well, so they want to stay
- How to keep your customers
- Knowledge is power
- Loyalty programs
- Cross promotions (i.e., coffee cards)
- Solicit feedback
- Stand out in the crowd
Frank Flair – Flair Consulting
- Discussed his life story and experiences
- Give CSRs autonomy to go beyond normal service
- Charge premium price for great customer service
- Sales up, service down = recession
- Training for new hires – experience
- Meet and exceed customer expectations
- Treat your customers the way they want to be treated
- You are in a customer perception business
- Think creatively – reinvent ourselves (road to recovery)
- Your competition is who the new customer came from
- We must keep innovating
- You need to confirm your information (not verify)
- Why is your correspondence so angry
- Listen to understand – not to reply
Jordan Cohen – MacDonald, Sager LLP
- Roadmap to sale and purchase of a business
- Share sale vs asset sale (tax considerations)
- Employment law considerations
- Termination clauses
- Minute books
- Key lease considerations
View Jordan’s presentation
Jon Meijer – Dry Cleaners & Launderers Institute (DLI)
- Results of the pandemic
- Industry changed overnight
- 33% of cleaners closed
- More closures to come as government assistance ends
- Make changes to our businesses
- What can we do for you now
- Good news – industry is much stronger (less competition)
- Most members doing better than pre pandemic
- Future EPA concerns – possible phase out of perc
- PFAS – polysubstance (used in Teflon, waterproofing, clothing, fast food wrappers)
- Forever chemical – cancer concerns
- Carbon absorption
Richard Ponsonby – Richard Ponsonby Creative
Richard presented the new CFA website and asked for input from the members on what they may want on it. He urged members to send in their suggestions of what content they would like to see for the public and member sections of the website.
Rick Mugno – SMRT Systems
- Explained how Point of Sales systems (POS) worked and the many uses derived from them
- Manage your business better
- Make your business more efficient
Tonny Colyn – Salvation Army Thrift Stores
Explained what sustainability means (social, environmental, economics). Executive Director suggested that members should acquire a drop box to put in their locations to receive garments not wanted by customers to be reused and recycled. Salvation Army Thrift Stores work with other charities to help reduce the volume of textiles that are going into landfills. Consumers are looking for ways to behave environmentally in their purchases.
View Tonny’s presentation
Tim Maxwell – GreenEarth* Cleaning
- Explained the history and growth of GreenEarth*
- Rental properties for the most part are only allowing GreenEarth* plants in their shopping centres (i.e., Rio Can)
- False Green claims are hurting the ability to rent properties
- Utilization of new technologies
- Prices are dropping on purchases of silicone
- New technology by GreenEarth* Sea Clear* stopping over 90% of microfibers going down the drain
- More usage of reusable garment bag – reduce use of poly bags
Jacquelyn Stevens – Willms & Shier Environmental Lawyers LLP
- Greenwashing; Truthiness; Risk
- Disinformation of stating you are environmentally green
- Organic cleaner – misinformation
- VOC – Volatile organic compound
- Canadian Code of Advertising Standards
- Competition Bureau
- Discourage use of vague statements
- Penalties and fines are very high
- Any consumer can file a complaint or file a class action
Rick Mugno – SMRT Systems Workshop
- Business growth
- History of SMRT (formerly Liberty)
- Make a living without doing everything
- Cloud based – safe security
- Text customers and ask for comments by customers 15 minutes after they pick up or deliver order
- Red comment comes right back to you
- Green comment goes to Google to make a review
- Trigger based marketing (monitors when you came in last)
- SMRT reviews
- Able to take a picture of every garment received and a picture of garment on completion
Scot Kight – Check Point
- Scot spoke about security for your systems
- Risks faced by small and medium size business
- Spoke about malware
- Spoke about ransomware
- Offered solutions
There was a lot of content offered to attendees in a short period of time. Next year’s conference will be even better, so watch for details as the conference comes together.
For more info on CFA, check the website.
50+ Marketing Executives Share Ideas at TRSA Summit
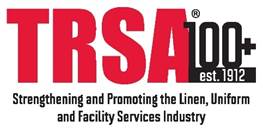
Alexandria, VA – Nov 1, 2022 – “Social media is not an extension of your brand, it is your brand,” said social media guru Corey Perlman in a keynote address at TRSA’s Fifth Annual Marketing & Sales Summit on Oct. 25-26 in Tampa, FL. Perlman’s presentation, dubbed Social Selling: How Digital Marketing Can Strengthen Your Business, focused on why marketers must make social media a priority, drew more than 50 marketing and sales staff from the linen, uniform and facility services leaders from across North America.
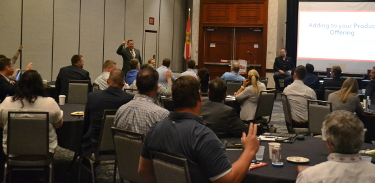
As the owner of Impact Social Inc., Perlman has been at the forefront of digital marketing for more than a decade. An author, speaker, consultant and nationally recognized social media expert, Perlman shared his eight social-selling principles, including why you must prioritize your platform, and why doing good things also is good for business.
Perlman returned to the summit that afternoon to lead a digital-marketing master class. This hands-on interactive workshop had attendees evaluating their own social-media sites, based on the eight social-selling principles addressed during the morning session. “If you are looking for more engagement in your social media, talk about someone else, your teammates, your customers, your company partners,” Perlman advised in a key takeaway point that had attendees reviewing their company posts and rethinking their content-planning calendars.
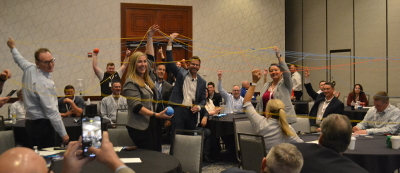
Another popular conference session was dubbed Let’s Talk: Conversation Starters. In this workshop, attendees gathered in peer-led groups based on common interests. They engaged in open discussions on any of four topics: social media, the value of search engines in marketing, best practices for lead generation and how to grow market share for rental vs. direct-sale goods.
In addition, the summit included two panel discussions. Jeff Wile, the owner of Infinite Laundry, Coral Springs, FL, led the first session, titled, Developing a Marketing Strategy with Proven ROI. Jeff Peterson, sales manager, Spin Linen Management, Omaha, NE, also showcased a direct-mail gift box that Peterson and his team had sent to selected prospects. The campaign’s ROI far surpassed their goal of a 5:1 ratio of year-over-year revenue.
Mark Lewis, director of business development at Dempsey Uniform & Linen, Jessup, PA, also led a presentation on ideas for improving ROI by rolling out new products for a company’s portfolio. Lewis outlined the steps required to effectively research and present new products.
A second panel, facilitated by Ben Fox, director of sales and marketing, Alsco Uniforms, Salt Lake City, focused on aligning sales and marketing with service and operations. A mix of operators and suppliers, from marketing, sales and operations, shared ideas on how their companies can do more to align priorities among these groups. They discussed suggestions for improving communications, focus and teamwork. Ryan Matthews, Alsco Uniforms, the new chair of the TRSA’s Marketing & Sales Committee and a senior national sales manager at Alsco, reminded attendees that, “When working on the alignment of your company players, don’t leave out the customers’ point of view.”
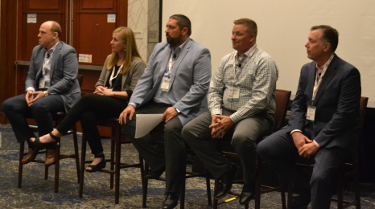
Rounding out the conference was a “best of the best” competition, in which 19 attendees submitted one of their successful marketing promotions, campaigns, videos or sales hits. During networking breaks between sessions, attendees were shown each of the submissions with a short quote explaining the idea and visual of the success. At the end of the summit, attendees voted for their top choice. Zach Ostendorf, a videographer from CITY Laundering, Oelwein, IA, was the big winner with his “day in the life of route sales rep” video. Ostendorf went home with bragging rights, plus a $250 Amazon gift card.
Reflecting on the substance and value of the summit, Mark Crewes, Workwear Outfitters, Nashville, TN, commented that “The entire day’s events were very well done. I would recommend attending future events and will encourage someone from our marketing department to also attend future sales and marketing summit meetings.” Next year’s TRSA Marketing & Sales Summit will be held in Memphis, TN, in October 2023.
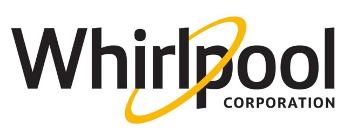
Whirlpool Corporation to reach 100 percent renewable electricity
Whirlpool Corp. states that it has entered into a second wind Virtual Power Purchase Agreement (VPPA) to step up progress toward its commitment to reach Net Zero (scopes 1 and 2) emissions in its plants and operations by 2030.
This agreement with ENGIE North America will represent 53 megawatts of clean, renewable wind energy over 12 years.
In order to meet its 2030 goals, the company is maximizing previous investments in onsite renewable energy and making energy-efficient upgrades across its manufacturing plants. At the same time, investments are planned in off-site renewable energy opportunities through Virtual Power Purchase Agreements. By doing so, the company intends to see its customers are to be provided with clean, renewable energy to the grid.
In February, the company joined the U.S. Department of Energy’s (DOE) Better Climate Challenge. This initiative is targeting a reduction of greenhouse gas emissions by 50% within 10 years. By collaborating with the DOE and other organizations the company aims at substantially cutting carbon and saving energy.
(NEWS COURTESY OF CINET)
Braun Service Schools return
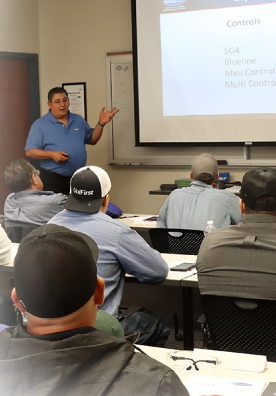
Braun announced the preliminary schedule for its comprehensive service schools in 2023, with two courses so far.
Initial 2023 Schedule:
- Washers and Dryers — April 18 – 20
- Finishing Equipment — May 23 – 25
Each class will cover:
- Proactive maintenance (scheduling and delivery)
- Basic operations
- Print/schematic interpretation
- Basic programming
- Effective troubleshooting techniques for electrical, pneumatic, mechanical and hydraulic aspects
- Basic repairs
Qualified attendees need a basic understanding of plant equipment operation, electrical and mechanical logic.
The classes will be held at Braun’s manufacturing facility in Syracuse, NY. Custom Service Schools are also available. For these custom schools, Braun personnel will travel to a client’s laundry facility and train their staff on equipment function and required maintenance. These sessions are tailored to the client’s specific needs and include both hands-on demonstrations and classroom discussions.
For more information, visit the website, or call (800) 432-7286, ext. 219.
TRSA Professional Management Institute graduates new crop of managers
The Textile Rental Services Association offers a training to managers to help them improve their facilities and operations. The multi-year course graduated 11 industry professionals from the 4-year program, and gave certificates to those completing years 1 to 3 at its recent commencement event on August 11 at the University of Maryland.
The association offers the Roger F. Cocivera Professional Management Institute (PMI), a Maintenance Management Institute (MMI) and the 4-year Ehrlich-Stempler Executive Management Institute (EMI).
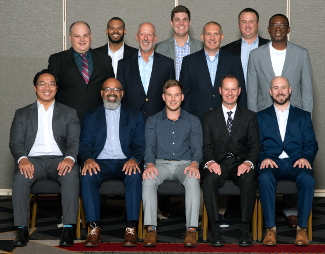
“It’s just been absolutely fantastic,” said Cory Rosenberger, HCSC-Laundry, Allentown, PA said of the EMI. “I would absolutely recommend it to everybody. It’s invaluable for your growth.”
The EMI just completed its 57th yearly edition. With nearly 40 students, EMI’s Year I class was among its largest ever, according to EMI Dean Kent Baker, who’s served on the EMI faculty since 1976. He summoned the Year I students to the stage, noting that, “If I’m not mistaken and somebody correct me if I’m wrong, but I believe that this is the largest class that we’ve ever had.” He added that size hadn’t inhibited the lively discussions that had taken place during the week.
TRSA President and CEO Joseph Ricci thanked students, faculty, staff and the program sponsors for helping to make this year’s EMI program possible. The sponsors included Kannegiesser ETECH, Brim Laundry Machinery Co. Inc., G.A. Braun Inc., JENSEN, Lavatec Laundry Machinery, Pellerin Milnor Corp. and Unitex International Inc.
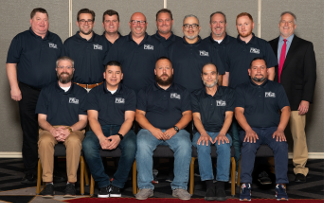
The PMI program saluted 14 laundry and supplier professionals as they received their 2-year certificates. The program ran from August 7-12, with new and returning students participating in classes focused on teaching them best practices for improving their company’s efficiency, as well as their development as industry leaders.
“I really liked the program,” said Adriana Reyes of ImageFirst, a first-year PMI student. “It was a lot of learning, and I received a lot of great feedback from the instructors and other students. Now I can go back and help my plant and be more successful.”
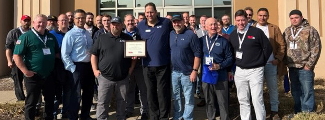
October 12-14 saw 40 professionals convene in Rosemont, IL for the MMI training. Speakers included Steve Rowell, president of Accelerated Ventures, a seasoned keynote speaker and training consultant. He oversaw an interactive session showing engineering leaders exactly how they must adapt to succeed. Joel Bell, Senior Manager of Reliability and Maintenance at UniFirst Corporation led a general plant safety session on Lock Out/Tag Out. A discussion session on protecting equipment and sourcing parts rounded out the day.
Paula Brown, production manager at Shasta Linen Supply said, “I really gained a lot of information to help me learn and work with the engineers and protecting equipment for the company.”
Workshops and presentations in Day 2 included one entitled Results Oriented Reliability and Maintenance Management providing tools to help extend the life of equipment. Deanna Griffin of The Griffin Group offered human resources experience on how to accelerate the hiring process. Paul Jewison, VP and general manager of Textile Care Services spoke on roof safety and fall protection. Chuck Rossmiller, Director of Laundry Programs at Medline Industries discussed general guidance on disinfecting a plant. Peer-to-peer roundtables ended the day.
The final day included a plant tour of Superior Health Linens, which processes 40,000 lbs. Of laundry per day. Afterward, presentations by Matt Lewis, Laundry Market Manager of Kemco Systems on key energy management a performance strategy ideas and Ian Bigelow, Executive Officer of Simple Management Solutions on developing a defensible capital budget.
TRSA programs are held regularly, and can help industry members improve their performance and grow their careers. For more information, visit the website, TRSA.org.
Maytag tests 7 machines through 60,000 cycles in lab test
Last month, Maytag engineers ended a 7-year lab test on the Commercial Laundry MHN33 front-load washers; a test of the DuraCore Drive System that started in 2015 with 10 machines running daily, with proper use and care and adherence to the recommended maintenance schedule.
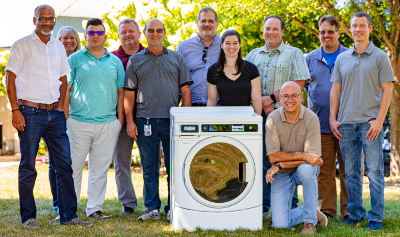
Throughout the course of the ongoing lab test, three of the 10 machines were removed from testing and used at trade shows to demonstrate the results achieved while the remainder of the 7 machines reached over 60,000 cycles individually.
To put that in context:
- In a multi-family property 1 washer/dryer pair can serve 8-12 families; if a family on average washes 5.2 loads of laundry per week then that washer would have to run continuously between 20 to 30 years until it’d reach 60,000 cycles
- It is common for a Commercial Laundry machine in a laundromat or hotel to run at least 5 loads a day, 365 days per year; it would take over 32 years for that machine to reach 60,000 cycles.
Parameters and disclaimer
The press release on the testing included the following:
The test was “based on lab testing of the DuraCore Drive System up to 60,000 consecutive 34-minute timed cycles using an 11-lb laundry load on the “Heavy Load” setting. The DuraCore Drive System as tested included Hub, Drive Bearings, Bearing Spacer / Shaft Sleeve, triple-lip with garter spring Tub Seal, Cross Piece Assembly with Drum Shaft, and Drum. Individual washer dependability may vary in actual use. This testing is not meant to supersede the machine’s actual warranty. (See maytagcommerciallaundry.com for specifics related to your machine.)”
The testing team
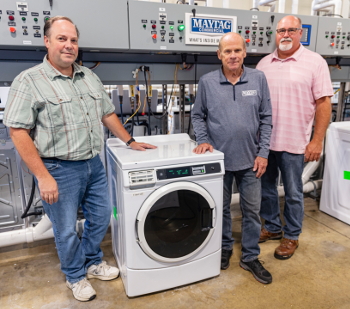
Dan Roscoe, Engineer Lead, has been working for Maytag Commercial Laundry since 1989 and led the design concepts seen in the tested machines.
Jason Hudock, Engineer Lead , has been with Maytag Commercial Laundry for over 12 years and led the efforts to translate design into production launch, testing and validation.
Engineer Kurt Werner has worked for Whirlpool Corporation for over 40 years. He has more than 25 patents in his name and is an expert on laundry drives and motors. Kurt started working on commercial laundry in the 1990s and focuses on producing long-lasting equipment.
In 2019, the Commercial Laundry marketing team decided to take one of the MHN33 test models from the lab offline after more than 25,000 cycles to bring it as a display at The Clean Show in New Orleans. A live feed video was playing showing what was going on in the lab including the techs coming in and out and changing out loads. This year in Atlanta, as the machines reached over 60,000 cycles, another one of them was on display along with a look of internal components to demonstrate how the DuraCore Drive System held up after all those cycles.
Engineers are satisfied with the results obtained for the past 7 years and will shift efforts to start testing new machines launching to market soon.
HLAC updates standards for 2023
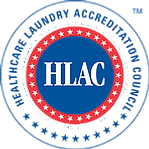
The Healthcare Laundry Accreditation Council (HLAC) offers accreditation to laundries that provide quality healthcare textiles and have proven the process they use is accurate and credible. The HLAC board of directors and committee members determine the standards used in the accreditation process, after listening to industry professionals’ feedback. Now the 2023 updated standards have been released.
A few things to expect from the updated standards:
- More emphasis on standards impacting hygienically clean linen
- Prominence on functional separation and clean/soil issues
- Less focus on items that do not directly impact hygienically clean linen i.e., eyewash stations
- Flexibility for operators who employ different methods to obtain hygienically clean linen
- Easier to read standards, less duplication, better-referenced standards
HLAC is planning a live informative webinar to spell out what’s new, and answer any questions.
To view the 2023 Accreditation Standards, visit the website.
To register for the Zoom webinar, go to the information page.
UNX-Christeyns Begins the Building Process after The Clean Show
Progress continues at a steep rate at the new UNX-Christeyns. Now marking 90 days since finalizing the merger, and with a dedicated goal to become one of the top chemical providers in the textile care marketplace, the company is sharpening its growth strategy by tackling one key building block after another.
“The Clean Show was a pivotal event for us,” said CEO Josh Lilley. “There was extraordinary excitement in being able to bring members of our management, sales, and R&D team together as part of the integration process.”
“Having our team at The Clean Show in Atlanta helped everyone understand the immediate and future goals to satisfy our commercial laundry, dry cleaning and textile service customers,” added president Rudi Moors. “Going forward, we plan to build off that success and emphasize the capabilities and technologies we now bring to the marketplace as one company.”
A key building block in the company’s strategy includes a comprehensive plan for a new corporate campus in Greenville, N.C. that is expected to be completed in 2023. The new state-of-the-art campus will become the central headquarters for UNX-Christeyns product and equipment manufacturing, engineering, research and development, marketing, sales and operations.
“We currently operate in two different locations, with our manufacturing division separated from our home office team,” said Lilley. “We are taking the necessary steps to secure property that will unite our teams and enable us to manufacture the most innovative products as efficiently as possible. We are working to share our plans with a more detailed announcement in the coming months.”
Methods for Management holds Q3 Bureau Meetings, introduces new benefits
International consulting group Methods for Management (MfM) held its third quarter Bureau Meetings, in which members of the group travel to one plant or another in the group for an in-depth look at how it operates. All the members are in a cost group of non-competing companies that share their financials, marketing and advertising efforts, challenges and successes together. At the end of a plant tour, the members give the hosts constructive critiques and suggestions for improvement and innovation.
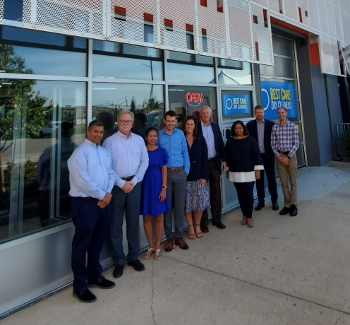
The Canadian Management Bureau met September 13-14 at Best Care Dry Cleaners in Winnipeg, MB. Kevin Hiebert and Lisa Loscerbo hosted the group. All members shared fresh ideas, toured Best Care’s state-of-the-art facility and enjoyed an evening of dinner and socializing.
New Benefits
Two new benefits for MfM members were announced at the various Bureau meetings.
The first is the Value Builders platform for increasing a company’s value, both for members moving toward transitioning their businesses and those who want to start building value for the future.
Each member will have access to one Value Builder module monthly on a self-study basis, along with a monthly discussion with Kermit Engh, a certified Value Builder Coach. Through these modules, members will work through value-building exercises.
Members who complete all the modules are said to be in a better-positioned business for a transition (whether to the next generation or for sale) or have a more valuable and profitable business to operate.
Canadian Bureau member Don Mungal of Drape Master Platinum in Toronto, Ontario, CA, said after going through the Value Builder system, “Value Builders have broken down what seem to be monumental goals into simple and proven strategies that have started to change the direction of our company. Kermit Engh and the Value Builder platform have provided tremendous support and guidance that has helped us work on our business and not in our business.”
The second benefit introduced is the next iteration of the Methods for Management financial platform, MfMBI, MfM’s financial platform. These include enhancements to the trend analysis platform, including creating multiple custom KPI reports for the various departments within each member’s company.
For more information on Methods for Management, visit the website.
23 Board of Directors
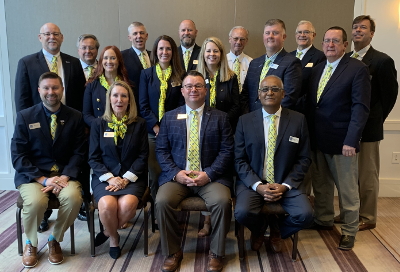
Drycleaning & Laundry Institute officials swore in DLI’s 2022-2023 Board of Directors at its Summer 2022 Board Meeting in Atlanta. DLI’s Board is comprised of fabricare business owners and operators from eight regions around the U.S., an Executive Committee, and Allied Trades representatives. All Board members volunteer their time and energy to guide the Institute toward providing the best benefit to DLI member cleaning professionals.
The 2022-2023 DLI Board of Directors includes:
Chair: Bobby Patel, Kona Cleaners, Costa Mesa, California
President: Jeff Schwegmann II, CGCP®, Sunshine Cleaners, Cold Spring, Kentucky
President-Elect & District 1 Director: Kathy Benzinger, Benzinger’s Dry Cleaning, Hamburg, New York
Treasurer: Kyle Nesbit, Tide Cleaners, Spring, Texas
District 2 Director: Norman Way, Puritan Cleaners, Richmond, Virginia
District 3 Director: Don Holecek, Crown Cleaners, Knoxville, Tennessee
District 4 Director: Ray Kroner, Kroner Dry Cleaners, Cincinatti, Ohio
District 5 Director: Ed Longanecker, Iris City Cleaners, Mount Pleasant, Iowa
District 6 Director: Danny Bahlman, Bahlman Cleaners, San Angelo, Texas
District 7 Director: Hilary Taylor, Continental Cleaners, Salt Lake City, Utah
District 8 Director: Toran Brown, Rytina Fine Cleaners & Launderers, Sacramento, California
Allied Trades Director: Mark Albrecht, The Route Pros, Woodbury, New Jersey
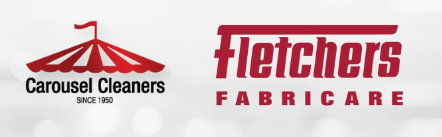
Carousel Cleaners & Fletchers Fabricare certified as Affiliates of America’s Best Cleaners
Carousel Cleaners and Fletchers Fabricare have both received notification of their official national certification as Affiliates of America’s Best Cleaners, a dry cleaning industry certification agency.
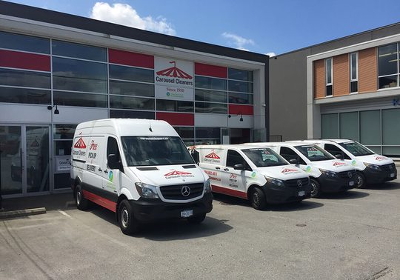
Servicing Vancouver since 1950, Carousel Cleaners has been a staple in their community for over 70 years. Through the years, they have shown a willingness to embrace emerging technologies and maintain uncompromising standards for customer service and carbon footprint reduction. They are actively engaged with their community and are frequent contributors to charitable organizations in their area.
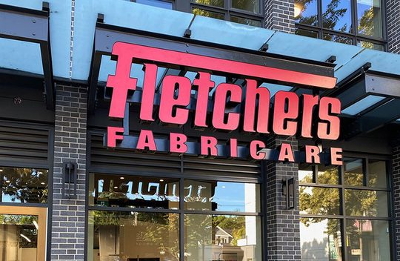
Founded in 1968, Fletchers Fabricare has been providing premium dry cleaning and laundry services to the greater Vancouver area for over 50 years. Fletcher’s Fabricare’s commitment to modernization has helped them evolve alongside the ever-changing needs of their customers. Led by their expert, knowledgeable and talented team, they’ve cultivated a genuine approach to their service that allows them to pour their heart and soul into the care of their customers’ fabrics.
President Cam Bastien said, “Our company has been transitioning from a small family business to a larger company while maintaining our high level of craftsmanship and family-style culture. With this expansion and new corporate structure comes a greater emphasis on foundation, skills and systems development.”
Executive Director Chris White shared, “We are excited to add our second Canadian affiliate to America’s Best Cleaners. The Carousel Cleaners and Fletchers brands are synonymous with excellence and first-class service in the Vancouver, B.C. market. We are thrilled to have Cam and his entire team of leaders and highly skilled technicians able to represent our brand in Canada.”
Bastien added, “The power of a forward-thinking group of similar-minded, organization size and caring individuals providing advice is priceless. We are looking forward to both giving and receiving from this group and growing together for many years to come.”
As two of under 50 businesses certified by America’s Best Cleaners, Carousel Cleaners and Fletchers Fabricare both join an exclusive group of elite dry cleaners within the United States and Canada.
America’s Best Cleaners is a certification agency and team of consultants who assist owners, managers, and team members to realize their full potential while striving for continued personal and professional success. For more information on America’s Best Cleaners and its affiliates, visit: https://americasbestcleaners.com/contact/
Starchup Joins Cents to expand pickup and delivery
Cents, a venture-backed technology company serving laundromats and dry cleaners, has acquired Starchup, a pickup and delivery, dry cleaning and POS software. Through this acquisition, Cents will be able to bolster their existing pickup and delivery platform by adding functionality and further investing in new tools and features to help laundry and dry cleaning owners grow their business.
Nick Chapleau has joined Cents as Head of Dispatch, and will be leading the development and commercialization of the pickup and delivery product.
The combined companies will spend the next few months building a roadmap for adding and improving features of both systems into one integrated platform.
For more information, visit the website.
DLI Announces 2022
Ontario Hazardous Waste Program Registry changes
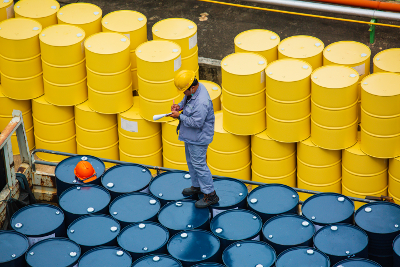
Ontario’s hazardous waste generators (including dry cleaners) have some new rules to take note of to avoid running foul of regulators.
The main change is in the method of reporting. Instead of paper reports being sent in, now waste generators will be required to submit their reports through an online reporting portal, beginning January 1, 2023.
Companies can designate their waste recycler to submit the reports and pay any fees involved, but this must be done according to the regulation. Rather than try to restate the rules and changes, we’re making a PDF file available to you for downloading. It is the official presentation from the Ontario government, and is easy to read and understand.
Please download it here, and review it so you are ready for the new regulations when they kick in.
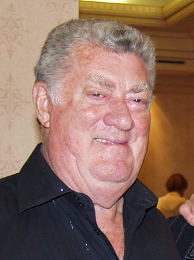
Tom White passes away
Tom White, active in the fabricare industry for over 60 years, passed away on August 30 at age 96. Read more about Tom and see memorial details by visiting our People page.
GreenEarth acquired by Greybull Stewardship
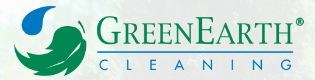
Greybull Stewardship, L.P. (“Greybull”) formally announced its acquisition of GreenEarth Cleaning. The Kansas City, Missouri-based company is the world’s largest brand of environmentally friendly dry-cleaning solvent.
The GreenEarth acquisition marks the latest significant expansion into the garment care space for Greybull. In recent years, the Jackson, Wyoming-based equity firm has invested in several cleaning franchises under their Clean Brands company, including both Lapels Cleaners and Martinizing Cleaners.
The GreenEarth management team, headed by Tim Maxwell, will continue to serve in their current roles.
“This entire acquisition process has confirmed to me that ownership of the GreenEarth Brand is moving from multiple pairs of guiding hands that founded the company more than two decades ago to a group that understands the potential opportunities available through so many avenues in the professional fabric care space,” says Maxwell. “The entire team here at GreenEarth is excited for the opportunity to continue to bring environmentally non-toxic cleaning to our affiliates around the globe.”
Maxwell added, “The most important thing to note about this acquisition for our customers and affiliates is that GreenEarth will continue to be GreenEarth. The ownership may be different, but the direction and vision of the company and commitment to our business partners remains the same.”
Continental Creative Services changes name to Girbau Creative Services
Continental Creative Services (CCS), a division of Girbau North America (GNA), recently changed its name to Girbau Creative Services (GCS). “We wanted to change the name to better align with our parent company, Girbau Global Laundry Solutions (Girbau),” said Creative Services Manager Kim Foxcroft.
Developed in 2005 to support GNA distributors and end-users, GCS offers cost-effective marketing, advertising and public relations services. With a team of laundry industry marketing experts, GCS provides distributors and their customers with everything from logo, brochure and website development to signage, direct mail campaigns, vehicle wraps and press releases, according to Foxcroft.
“We’ve worked closely with distributors and store owners for years to provide the kind of marketing support that sets them apart in the eyes of their customers,” she said. “Today, we move forward together under the Girbau umbrella – focused on customer proximity, one team and innovation and sustainability.”
For more about GNA or GCS visit www.gnalaundry.com or call 920-428-4682.
ALM releases Monkeypox Best Practices for hotels
The growing concern over the increased spread of Monkeypox in the United States provides an opportunity to address best practices for hotel textile processing and handling. With a focus on protecting workers and providing a safe and comfortable environment for the travel public, the Association for Linen Management (ALM) and the American Hotel & Lodging Association (AHLA) have partnered to release their latest best practice document Monkeypox: Textile Handling Guidelines for Hotels.
This collaborative effort included multi-dimensional textile service providers, end users, regulatory authorities, and related industry subject matter experts. The final document involves research of regulatory compliance and incorporates the concerns of the public, customers, and key stakeholders.
“As business and personal travel returns to typical numbers, we felt it important to revisit the best practices for hotel laundries, including additional measures to keep textile service professionals and guests safe during travel with the increase in Monkeypox cases” said Linda Fairbanks, ALM’s Executive Director. “And after our work with AHLA during COVID-19, we welcomed the opportunity to collaborate with them again on this project.”
For access to the complete Monkeypox: Textile Handling Guidelines for Hotels document, please email Leesy McCorgary at lmccorgary@almnet.org.
Tingue Invests in Management Team’s Future
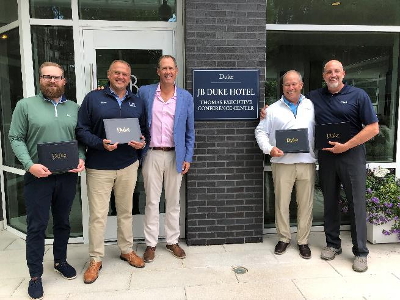
Tingue’s management team attended a week-long executive education program at Duke University’s Fuqua School of Business, with each participant earning a certificate in Finance.
The Duke program is designed to introduce participants to the essential elements of financial reporting, including managerial and financial accounting. Additional topics include, interpreting financial statements and developing capabilities to communicate operating, marketing, sales, and growth strategies in financial terms.
CEO David Tingue explained, “Our management team has historically been strong in operations management and in sales management. As I look ahead, I believe our managers will best serve both Tingue, Brown & Co., and their customers if they combine this expertise with strong financial competence as well. To that end, we turned to Duke University to help raise the financial understanding and aptitude of four of our company leaders: David Rovetto, Regional Sales Manager; Jamie Bridge, Regional Sales Manager; Chris Melchionni, Regional Sales Manager; and Patrick Robertson, VP of Operations.”
Patrick Robertson had high praise for the program. “An exceptional course. Building from basics on day one, to real-world applications on the final day. The Duke program has allowed me to analyze financial statements and make impactful decisions backed by the data. A deeper understanding of company financials is critical for any leader, and this program has made me a much more competent decision-maker within our organization.”
CFA works to raise profile of industry in Canada
Some things you can do on your own as a business owner to improve your standing in the community. But others are best done by Associations of members. The Canadian Fabricare Association is launching an initiative to remind municipalities, cities and provincial governments of the key role fabricare professionals play in the community.
In speaking to the City of Mississauga Council, CFA President Dino Kantzavalos proposed a program called “Get Close with Your Cleaner Again!“, urging customers to remember those who are standing by to care for their garments once again.
In part, his statement said:
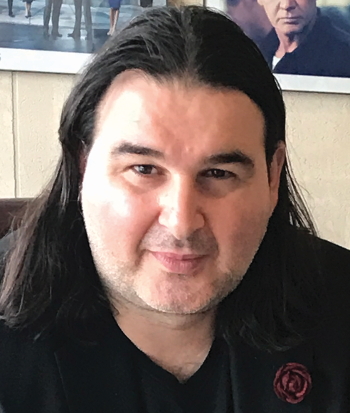
CFA President
The last two years have been extremely challenging across all levels. We lived through some unprecedented events not seen in our country. This pandemic has caused many businesses to suffer economic stress because of lack of revenues, partly due to government-implemented lockdowns and the encouragement to “stay at home”.
However, no industry has suffered more than ours. We saw on average, up to a 90% drop in sales across the country for almost two years. A more dramatic statistic is that our industry has closed over 30% of its locations nationwide. One of the key contributors to these declining numbers is that our industry was deemed an ‘essential service’, thus causing us to miss out on much-needed financial assistance which other businesses were able to benefit from. Another key detriment was the removal of travel. Not travel in the traditional sense but the type of travel that would take you to a social function. Even funerals were limited. Between zoom meetings and all restrictions there was no need to have your suits and dresses and shirts taken to your cleaner.
We are not asking for a handout. We are asking for your assistance in helping us tell our story.
The City of Mississauga issued a supportive proclamation on July 6, signed by John Kovac, Councillor, Ward 4. It read:
WHEREAS the City of Mississauga is home to over two-hundred dry cleaners, of which combined employ thousands of Mississauga residents;
WHEREAS the City of Mississauga is a significant provider of businesses associated with the fabricare industry;
WHEREAS many businesses have endured economic hardship due to the societally negative effects of the pandemic;
WHEREAS dry cleaning businesses, on average, have experienced a considerable decline in their sales locally and nationally, with many locations having been closed down as a result;
WHEREAS the dry cleaning industry once thrived and is now in desperate need of community support and revitalization;
THEREFORE BE IT RESOLVED
That the Council of the City of Mississauga extends its support to members of the dry cleaning community by acknowledging the hardship suffered but rallying behind their “Get Close with Your Cleaner Again” industry campaign; and further,
That the Council of the City of Mississauga connects with their counterparts at the Federal and Provincial levels, local-area MPs and MPPs included, and calls upon them for their support of this campaign and for their further assistance where possible.
For more information, contact Dino at 416-804-2261 or kdk@tscwetclean.com.
TRSA names Brian O’Neil Lifetime Achievement Award Winner
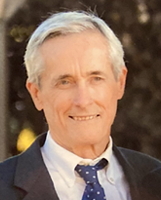
The Executive Committee of TRSA’s Board of Directors recently voted to honor Brian O’Neil, president of California Linen Services, Pasadena, CA, with the association’s highest honor, the TRSA Operator Lifetime Achievement Award. O’Neil will receive the award on Sept. 15 at TRSA’s Annual Awards Dinner, held in conjunction with its Annual Conference in Nashville, TN.
O’Neil, 80, has dedicated his career to working in the linen, uniform and facility services industry and continues to lead the staff at California Linen, where 25% of its employees have been with the company for 25 years and another 25% have been for another 10-25 years.
TRSA Chair Noël Richardson, president, Shasta Linen Supply, Sacramento, CA, noted that the Executive Committee’s decision, “allows us the pleasure of extending a heartfelt thanks for Brian’s service to the industry with the TRSA Operator Lifetime Achievement Award. This is bestowed in recognition of exceptional personal service to our industry and to the associations that serve our industry.”
O’Neil has longstanding ties to TRSA. He served on TRSA’s Board of Directors from 2003-’09 and chaired TRSA’s Textile Management Committee from 2001-’03. O’Neil also served as the vice chairman of the Textile Management Committee from 1999-’01. California Linen Services is certified Clean Green® and Hygienically Clean Food Service®. Additionally, the company has sent employees to EMI, PMI and MMI to further their industry-specific professional development.
Brian’s son Andrew, the general manager at California Linen commended his father’s achievement: “Humble and soft spoken, Brian inspires others to become leaders within the organization and beyond…He is a staple in the community and respected by many industry leaders.”
For more information on the TRSA Operator Lifetime Achievement Award and to review past recipients, visit www.trsa.org/awards.
Malboeuf chosen President-Elect of ALM
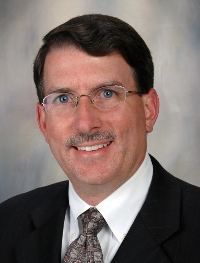
Chip Malboeuf will join the Association for Linen Management (ALM) Board of Directors at the end of June. Malboeuf has been a long-time member of ALM, and succeeds Jim Mangini, RLLD, as president-elect as Mangini moves into the role of president. Malboeuf has over 28 years of experience in the industry, and currently he serves as vice president of Engineering for ImageFIRST Healthcare Laundry Specialists.
“I am honored and humbled at being selected for this position,” said Malboeuf. “I look forward to working with the ALM leadership and members and am excited for the opportunity to share my knowledge of the industry and to give back to ALM members.”
Malboeuf has taught myriad ALM educational programs throughout the years, and his history with ALM has built a foundation for collaboration with both the incoming and outgoing Board presidents.
“I am excited that Chip Malboeuf been chosen by our membership to serve as the president-elect of ALM,” said Mangini. “Chip’s extensive background within our industry is an asset to not only our membership but also our Board. I welcome the opportunity to work side-by-side with him over the next few years.”
“I am thrilled to have Chip join the ALM Board as president-elect,” said Rich Bott, RLLD, CLLM, who is shifting into the role of immediate past president. “I have known Chip for several years and his reputation, integrity, and industry knowledge are exceptional. Chip will add tremendous insight and leadership to ALM as we look to the future to provide excellence in both education and support to our industry. I appreciate Chip’s willingness to serve and look forward to working with him.”
ALM Executive Director Linda Fairbanks is pleased with the members’ decision for ALM leadership.
“I am so proud of how many wonderful individuals we have throughout our membership,” said Fairbanks. “So many step up to help others learn from their expertise, and Chip is the quintessential example of working together to make things better for everyone. I’m confident that with his leadership, ALM and its members will continue to grow and thrive!”
Cindy Molko, former ALM President, retires
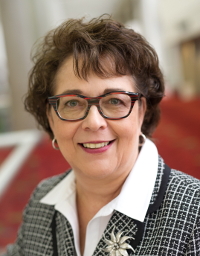
Cindy Molko, RLLD, CLLM, and former president of the Association for Linen Management (ALM) Board, recently retired from her position at Mayo Clinic after nearly 43 years of dedicated service.
“Some of my fondest ALM memories have been with Cindy,” said Linda Fairbanks, ALM executive director. “Cindy has always been someone we could reach out to for knowledgeable guidance, whether it be for industry education, understanding member needs, or business insight, she has always been generous and enthusiastic in helping textile care professionals.”
That knowledge has been gained through years of working at every level within The Mayo Clinic. Cindy began as a Central Service Tech, and was quickly promoted to a supervisory position, where through the years, she was instrumental in building the Mayo Linen and Central Services into what it is today.
“It has been an incredible experience to work with Cindy, whose knowledge and experience is invaluable to the organization and industry,” said Kathy Mulhern, Director Linen and Central Service, Mayo Clinic, Rochester, MN. “I cannot thank Cindy enough for her mentorship. Cindy’s consistent support and leadership is responsible for all our accomplishments. Congratulations on your retirement!”
Despite Cindy’s many responsibilities at Mayo, she always found time to lead by example in other industry associations and organizations. At ALM, Cindy has spoken at conferences, taught at the Laundry & Linen College, as well as leading by example by completing and maintaining certifications in both the Registered Laundry & Linen Director (RLLD) and the Certified Laundry & Linen Manager (CLLM). She has also participated in the Boards of the Minnesota Health Care Central Service Materials Managers (MHCSMA) and the International Association of Healthcare Central Service Materiel Management (IAHCSMM).
Christeyns USA and UNX Industries sign merger agreement to for UNX-Christeyns.
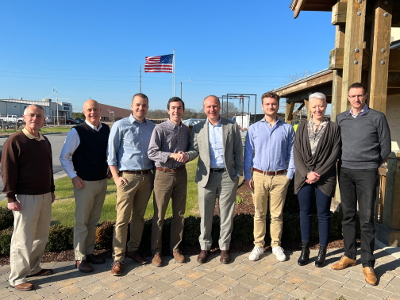
Principals involved with the new UNX-Christeyns include, from left to right: Board Chairman Griff Garner; Board member Edwin Clark; CEO Josh Lilley; owners Josh Clark and Alain Bostoen, and Mr. Bostoen’s son, Hector; Vice President of Operational Integration Ann Cayet; and President Rudi Moors.
June 13, 2022 – UNX Industries and Christeyns USA announced they are entering into a definitive merger agreement to create UNX-Christeyns. The new U.S. based company will be able to deliver a portfolio of chemicals, detergents, engineered equipment and cleaning solutions to the commercial and industrial textile care market.
This alliance creates opportunities for customers by combining Christeyns’ global innovation and supply chain capabilities, with UNX’s domestic manufacturing and distribution platform. The agreement also means the companies will be combining their booth space (#4128) and discussing future plans with customers at the upcoming Clean Show, July 30-August 2 at the Georgia World Congress Center in Atlanta.
With the arrangement beginning July 1, company headquarters will be located in Greenville, N.C. Josh Lilley of UNX will serve as Chief Executive Officer and Christeyns’ Rudi Moors becomes the President. Sales and service staffs, as well as their established distributor networks throughout the country, will remain in place.
“We have embraced family values for over 60 years in our business, and now another like-minded family-oriented business with a global reach has joined us,” commented Lilley. ‘This agreement makes us a stronger, more flexible organization that is laser focused on expanding our presence in the U.S.”
“This is a true 50-50 partnership, and both companies have compatible values and a shared passion for serving our customers,” remarked Moors. “Current and future customers will benefit from a wider selection of products and wash concepts, enhanced service, and the chemical innovation and R&D capabilities we have to offer.”
UNX was founded in 1958 and earned a reputation for providing companies with superior, commercial grade cleaning products for their laundry, houskeeping and warewash needs. A supplier to a variety of industries including industrial laundries, education, healthcare, food service, hospitality and athletics, their equipment also is said to help customers increase their efficiencies and extend linen life.
“We strive to bring added value to our customers, and this merger gives us the ability to provide better buying power and new product concepts to make them more efficient operators,” said Lilley. “Christeyns has 46 offices, 17 manufacturing facilities and nine R&D centers around the world. When you add in the manufacturing, distribution and supply chain strengths UNX has built domestically, these are strong attributes that will benefit our customers.”
Christeyns USA was a division of Christeyns, the $300M family-owned and operated Belgian manufacturer of cleaning, hygiene and disinfection products for laundries, the food industry, cleaning companies and the medical sector serving customers in over 50 countries.
“We intend to be one of the top three chemical providers in the textile care sector,” said Moors. “As a family owned company, UNX developed very close relationships with their customers that was integral in building their business. When you add in the full complement of resources from an internationally respected company, UNX-Christeyns represents the best of both worlds. We have our customers’ best interests in mind, and our combined resources and experience will benefit them across the board.”
Any customers who have questions are encouraged to contact their respective UNX Industries and Christeyns representatives.
About UNX-Christeyns
Based in North Carolina, the partnership of UNX and Christeyns brings together more than 100 years of experience in the textile care industry. Specializing in commercial quality cleaning chemicals for the laundry, housekeeping, warewashing, and dry and wet cleaning markets, these products are supported with custom designed dispensing equipment. Learn more by calling 800-869-6171 for more information or visit the website.
The final countdown to banning some single-use plastics in Canada begins today
Read the official government press release here.
What does it mean for you? Will it include the poly you send your customers’ garments home in? Read the definition of a “single use bag” and you may be enlightened… or confused.
SPECIAL UPDATE FROM KEN OLSEN of Environment and Climate Change Canada, via Sid Chelsky:
“I have followed up with our colleagues managing the Plastics Regulations and they have informed me the Single-use Plastics Prohibition Regulations do not cover dry cleaning bags.
Further details are available in the Technical Guidelines, where it is noted that bags to protect clothes after professional laundering or dry-cleaning are not intended to be prohibited by the Regulations: Single-use Plastics Prohibitions Regulations Technical Guidelines – Canada.ca
Gurtler Celebrates 40 Years with Video
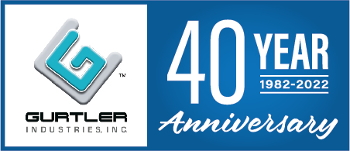
Gurtler Industries recently released a short video that commemorates the 40th Anniversary of the company. The video features the three generations of the Gurtler family, Bill, Greg and Jake, and their thoughts on the company that had its start in 1982. Bill, now the Chairman and his son Greg, President, were there at the beginning when Gurtler Chemicals started as a regional laundry specialty chemical producer and service provider. Now Gurtler has stretched its coverage across the US, Canada, and Mexico, opened a business unit in Australia and has customers in the Caribbean and Central America.
Jake Gurtler, V.P. Corporate Accounts, joined the company in 2008 and is the third generation to take a role in managing Gurtler’s growth. In the video, Bill, Greg, and Jake review how Gurtler has built on its successes over the decades with primary focus on the Gurtler Advantage: Service, Innovation and People. They especially take the opportunity to thank all our loyal customers, some who have been with us for the entire 40 years!
The video can be accessed on the company’s website home page or on Gurtler’s YouTube Channel.
Gurtler Industries is a leading manufacturer of advanced detergents, specialty chemicals and injection systems for the commercial laundry industry. From its headquarters and research center in suburban Chicago, Gurtler supports the entire spectrum of the laundry industry, including healthcare, hospitality, industrial uniforms, shirt laundries and textile rentals. Gurtler is a family company now in its third generation, maintaining its tradition of excellence, innovation, and service.
For more information, contact Gurtler Industries at 800-638-7300 or visit www.gurtler.com
AWGS Annual Meeting in Florida
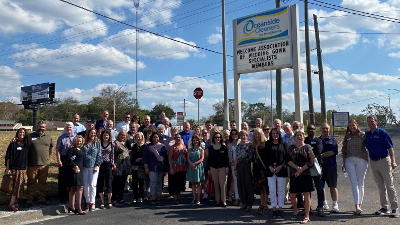
Members of the Association of Wedding Gown Specialists (AWGS) met recently in Jacksonville, Florida, to discuss marketing strategies with wedding industry experts and elect officers. This year there were two stops on the traditional plant tour: one at Oceanside Cleaners award-winning plant (2020 CNET Global Best Practices) owned by AWGS members Mike and Amy Harris, and the other at the company’s remarkable, completely computer-programmed drop shop.
A highlight of the meeting was the presentation of the eleventh annual Jack Barth Memorial Award of Excellence. Initiated by Linda Stokes-Barth in remembrance of her late husband and his achievements in the dry cleaning industry, the award recognizes a member of the Association of Wedding Gown Specialists for advancement, promotion, and development of industry standards for wedding gown care and for outstanding contributions and service to the Association and its members.
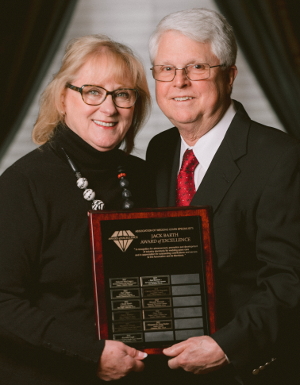
For the first time ever, there were dual honorees, Greg and Margaret Butler of Dublin Cleaners in Columbus, Ohio. As AWGS president Kermit Engh noted when he presented the Barth Award, “The Butlers represent the heart of our association—family-owned businesses with a long history of both exceptional care for wedding gowns and community activity. When the Butlers joined the association in 2007, they credited AWGS for tripling their gown business over the following year, but AWGS in turn has greatly benefited from their membership—not least because we truly look forward to the true pleasure of their company at our meetings.”
Speakers at the conference presented a range of important trends and ideas for branding and networking. Kirsten Ott Palladino, founder and editor of EquallyWed.com spoke about learning to use inclusive language and affirming values. Something as simple as adding the phrase “We support wedding equality” to a website is an effective way to better serve and market to the rapidly growing LGBTQ+ community.
Trevor Allred of Kenect.com demonstrated the benefits of marketing via text through a business phone number rather than a personal cell phone. As opposed to dealing with texts to a personal number at inconvenient times, a company’s business phone can be programmed to be available 24/7 and accommodate a repeatable process with an automatic response.
Francis Flair’s exceptional presentation completely convinced the group that effective management of the customer’s experience can make price irrelevant. As he describes on his website, www.FlairConsultingGroup.com, creating standards for each part of the cycle of the customer’s experience removes variations and provides a consistent world-class customer experience at every touchpoint by every employee. Flair’s personal story is also inspiring. Growing up in an orphanage in Ghana alongside his younger brother, he personifies the American dream of personal achievement.
Other presentations included “Is Your Number 1 Employee (Your Website) Ready” by Tracy Arnett of Wedding and Party Websites, “Surviving the Pandemic and What Lies Ahead” by Kermit Engh of Methods for Management, “Documenting the Bride’s Gown” by Vikki Reed of Fashion Cleaners in Omaha, Nebraska, and “Why and What to Blog” by Michael Astorino of Fabricare Cleaners in Norwalk, Connecticut.
In addition to speakers, there were a series of round-table conversations offering everyone in the group the chance to discuss topics ranging from the best techniques for dirty hemline to magnets for attracting wedding couples.
Re-elected to office were president Kermit Engh, vice president Gary Fine of Parkers Custom Clothing Care in Toronto, Ontario, and secretary-treasurer Sharlene Thum of Five Star Wedding Gown Specialists in San Antonio, Texas. Malcolm MacGregor of Browns Cleaners in Ottawa, Ontario, serves as immediate past president and chair of the finance committee.
Incoming members of the Board of Directors are Mila Martin of ArGown Preservation in Bentonville, Arkansas, Michael Rowe of Shores Fine Drycleaning in High Point, North Carolina, Angel Suarez of Rey’s Cleaners in Miami, Florida, and Heather Ziccarelli of Owl Cleaners in Pittsburgh, Pennsylvania.
Sponsors of the event were Foster-Stephens, Inc., Sankosha-USA, Inc, Select Risk Insurance, and Kleerwite Chemicals.
AWGS is a not-for-profit trade association with members in seven countries.
DLI Virtual Presentations in June
The Drycleaning & Laundry Institute (DLI) is hosting two intriguing webinar presentations in June that you won’t want to miss. Both presented by long-time cleaners who’ve “been there, done that, and survived it”, the online sessions will cover the areas of laundry lockers and evaluating your marketing efforts.
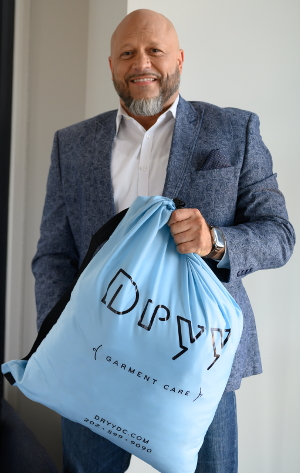
My experience implementing dry cleaning lockers
June 8, 1 p.m. Eastern time
Ken Sandy of Dryy in Washington, D.C. can save you the frustration of figuring it all out for yourself where laundry lockers are concerned. His presentation will walk you through what he did right… and what he did wrong along the way.
If you’re thinking about diving into the interesting service of providing laundry lockers, you’ll want to tune in.
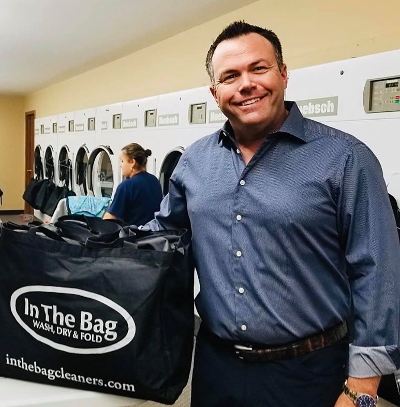
Measure your marketing — Only do what works
June 15, 1 p.m. Eastern time
Industry marketing coach Dave Coyle of Maverick Drycleaners of Wichita, Kansas will help you figure out how to measure your marketing efforts. After all, how can you tell what works if you don’t measure it? His presentation will help DLI members evaluate their marketing so they can focus on what drives result.
In addition, DLI will also offer it’s usual Peer-to-Peer Members-Only Zoom Calls and the On Demand Video Library is always available. For details on any of DLI’s programs visit the website: DLIonline.org
TRSA Annual Award Winners
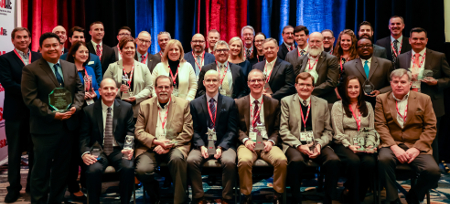
On March 30, 2022, individuals and operations were honored by their peers for outstanding efforts made in specialized categories in their digital, safety, educational, inclusionary and operational pursuits.
Best Plant Award
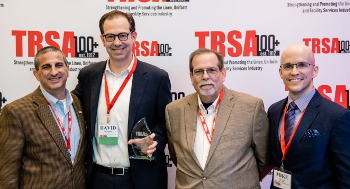
This an award honoring a company that is setting the standard for how an operation should be run, as voted by their peers. This year the highest honor that TRSA can bestow was awarded to the Unitex plant in Linden, NJ.
Unitex was honored for their diligent commitment to customer satisfaction, ensuring high reviews through weekly surveys, quality fulfillment rate reviews and data analytics. Operating seven days a week, the plant houses 200 full-time employees and produces nearly 140,000 pounds of laundry to serve nearly 30 routes weekly.
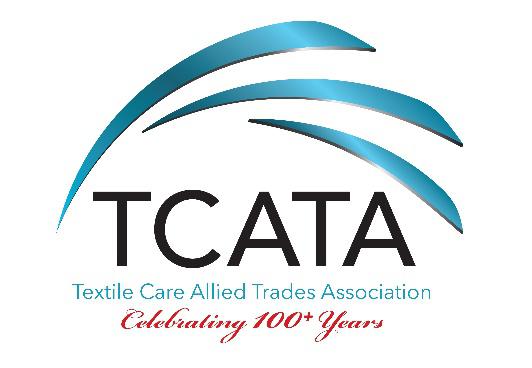
TCATA Honors Schwarzmann
The Textile Care Allied Trades Association honored Fred Schwarzmann, Jr. of A. L. Wilson Chemical Company with the prestigious J. Morry Friedlander Award at its 2022 Annual Educational & Management Conference, April 3–6 at Wild Dunes Resort in Isle of Palms, SC.
Fred served on the TCATA Board of Directors in various positions from 2005-2011 and most recently as President of the Board beginning in January 2020.
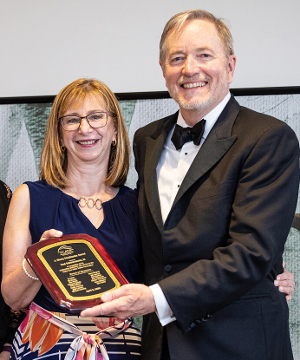
After receiving the award, Fred said, “I was certainly touched by the recognition I received, but I know that my contribution would not have been nearly enough in a vacuum. Only by pulling together were we able to protect TCATA through the dark days and re-launch it into a bright future. Thank you once again!”
TCATA established the J. Morry Friedlander Award to honor outstanding dedication and service to the association, naming it to acknowledge the unrivaled enthusiasm, dedication and goodwill Friedlander generated in his more than 40 years of service. Only six people have received the award since it was introduced in 1994.
New President
Also at the event, John Silverman, President of Tschopp Supply Company of Buffalo, NY, was installed as the incoming president of the Textile Care Allied Trades Association. He will serve a two-year term as president.John previously served on TCATA’s Board of Directors representing Distributors and in the role of Treasurer.
John began his career at Tschopp in 1989. By 1999, John became Corporate Vice President and General Manager. In 2005, James Tschopp retired, and John Silverman assumed the role of Corporate President. When asked what being a member of TCATA has brought to Tschopp Supply, John said, “The relationships and connections I’ve made through TCATA have helped Tschopp Supply grow as a company.”