Start your engines
|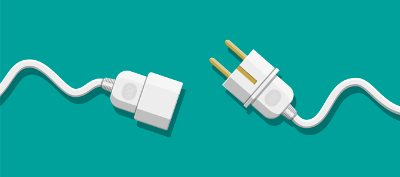
Things have been bad and are going to continue to be bad a little longer, but the end is in sight. The vaccine is out and the government is doing everything it can to reduce the restrictions. Yes, we still have to be careful, but 2021 is going to be a better year.
If your plant is like most, you have either been shut down for a while or you have been operating 1–2 days a week – and those are actually only half days. You haven’t changed your padding, you are low on solvent and there is a whole list of maintenance things that you are avoiding.
It’s time to get back to work. How do you get out of a hole so deep you can’t see out? Change your attitude – you have made it this far; you will survive.
If your machines have been shut down or used infrequently, you need to confirm that things are working properly.
There may be a smell in your dry cleaning machine or there a valve that is sticking. The timing may be off on your shirt unit. The padding may be hard on your press. Things break down over time, even if they are not in use. Let’s take a look at a few things.
General Inspection
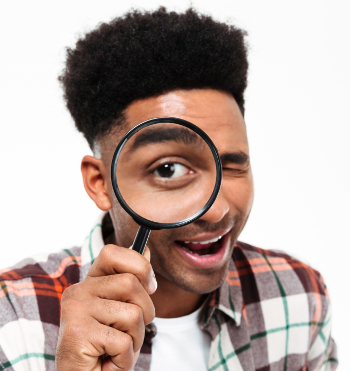
I am working on the assumption that you are slowly ramping up again. You have spare time – use it wisely. I’ll give you some general suggestions for all machines and then I’ll list some specific things for individual machines.
Get a clipboard and a pen, open your eyes and take a fresh look. Check that each machine is operating properly. Are the steam traps hot? How is the timing on the press? Does everything move at the right time? Are there any leaks? Strange sounds or smells? Do you have the right supplies in the right places? Is the padding clean and resilient? Take some time to vacuum off each machine. Look at valves, switches and control settings. Things get moved and forgotten.
Boiler
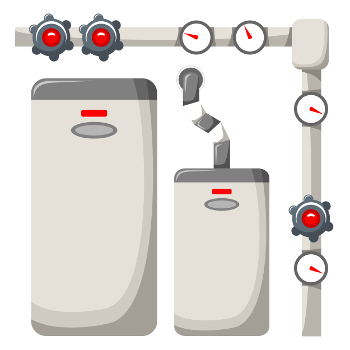
Check the safeties, pressure controls, water level controls, flame sensors and the safety valve. Are the gaskets or the sight glass leaking? You need to do the Annual Inspection even if you haven’t been using the boiler. Those gaskets will leak after a year whether you are using the boiler or not. How is the return tank? Often the float valve will stick if it hasn’t moved in a while.
Dry Cleaning Machine
What you need to do depends a bit on what solvent you are using and how you shut the machine down. Clean the water separator – it may give you a ‘dirty socks’ smell on the clothes. Give the still a good cleaning – down to bare metal. Do you need to clean or replace the solvent filters? Fill the lubricator.
Run a cycle and monitor the steps of the cycle. Is the solvent pumping properly? Are you reaching the correct temperatures during the drying cycle? Does the freon need to be topped up?
See the start-up guidelines Kreussler developed and shared with me in the linked PDF you can download. These give pointers for starting equipment from scratch, after a short shutdown, or a prolonged one. Excellent information.
Vacuum
Does the water drain out properly? Are the hoses still in good shape?
Padding
The padding on your shirt unit and presses is always the first thing that gets ignored. “We can put it off a little longer. I only have to do a little touch-up.”
Even though you haven’t been using that press, the padding is still deteriorating. The foam gets hard even when the press is not in use.
Your finish quality decreases slowly over time. Every day the padding is a little worse. Every day you spend a little more time doing touch-ups. Eventually the dollars you spend in touch-ups far outweigh the cost of the new padding. You are no longer saving money.
So either you or your technician will have to walk through the plant and touch the padding on every machine. Are the pads hard? Are they torn or dirty? Are there holes in the air bags?
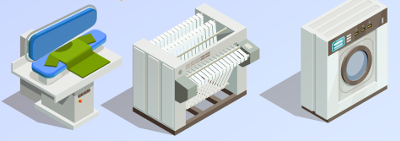
Shirt Press
Watch as the arms and the chests move. Is everything moving smoothly and at the right time? Have you cleaned the lint filters? Check the padding carefully – it is critical to getting a good quality shirt. Turn all the other machines off and listen for air leaks. Check the vacuum hoses for cracks.
Dry Cleaning Presses
Check that the steam traps are hot. That the steam valves are working properly and that the vacuum valve seals up tight. How is the grid plate and press pad? Is there water dripping from the iron?
Air Compressor
Check the oil. Does the tank drain still work? How is the refrigerated air dryer? Vacuum off the belt guard.
Spotting Board
When was it last cleaned? Run some hot water through it to flush out any chemicals.
Washers/Dryers
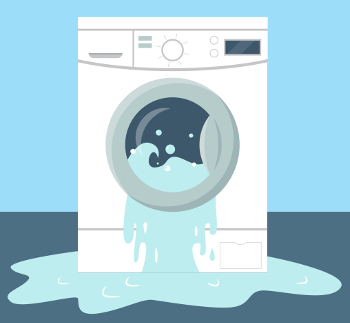
Check for leaking valves – either inlet or drain valves. Listen inside the drum to see if you can hear water dripping. Look at the drain pipe and see if water is leaking out when the washer is running. Check detergent pumps – squeeze tubes and the levels in the pails. Check that you are reaching the correct water level. The level control tube sometimes gets plugged and doesn’t read correctly.
Training
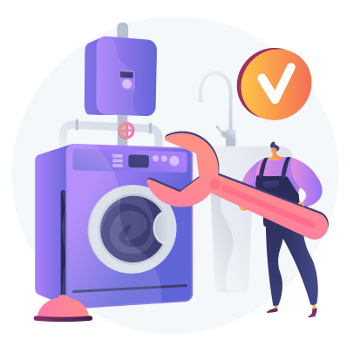
This would be a good time to do some training. Check that people are following your procedures. Systematize your procedures. Train and cross-train. We all forget things and your pressers and cleaners are no different.
Maybe you could even do some maintenance training. When someone has to clean their own machine they tend to take better care of it.
Your people will be happier. Your quality will improve and you are going to be busy. You could even sign them up for an online DLI course.
Take the time
This sounds like a lot of work. It is a lot of work. It’s what you should have been doing for the last 9 months. Even if it takes a week or two to get things back in shape, it is well worth it.
There is hope
2020 is over. The vaccine is out and the case counts will come down. Once the restrictions are ended we can get back to business. Where does your road to recovery lead? What is your business going to look like in 6 months? You have to make that decision. The only certainty is that things will not return to the old ‘normal’, and if you aren’t running a tight ship you will be going down with it.
The virus has eliminated weaker plants and changed all of the better managed ones.
Make a plan, get those machines working and move forward. You have to get strong before the next crisis arrives.
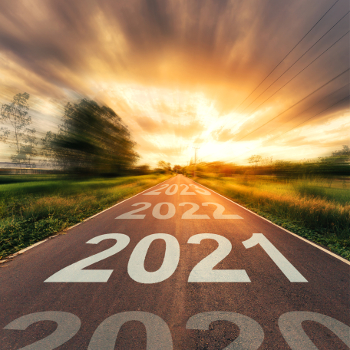
Kevin’s contact info: