Change is Hard!
|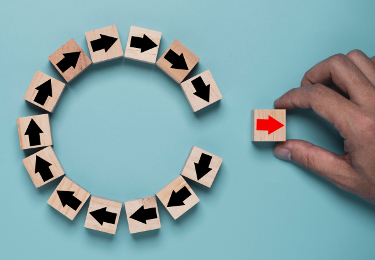
So you ordered a new machine. It will be there in two weeks. That is so exciting. Everyone is excited – except the person who will be using it.
We do a lot of work ahead of time to make sure everything is prepared for a machine installation. We get the right parts, tools and supplies. We line up electricians, picker trucks, plumbers, and maybe even a glass guy to remove the window.
We try to make sure it all goes like clockwork. We make the transition as smooth as possible. But sometimes in spite of all that, the installation is not a good thing. Oh, the machine was installed OK and everything was on schedule. The problem though is your staff and their resistance to the change.
Change will be stressful. How can you prepare your team for this transition? There are four main areas that you need to consider when you implement a new machine.
Select the right machine
It is critical that you select the right machine in the correct size for your plant. Most owners think this area is totally their responsibility. They pay the bill so they get to choose the machine.
That is correct. But there is a better way to approach it. If you involve your staff, it means that you respect them and value their opinions. If they are using the machine every day they probably have a good idea about what is needed.
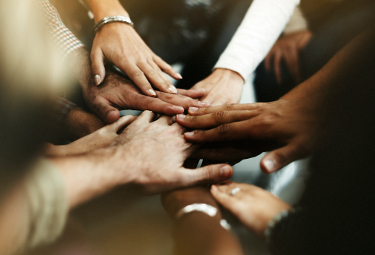
The biggest key to this is getting them on board with the change. If they help to ‘choose’ the machine, they are committed to make ‘their’ machine work in your plant.
It will take time and money, but take them to visit a plant that is using that exact same machine. Let them see it in operation. Let them talk to someone who likes the machine and is comfortable using it. That can save a huge amount of stress on everyone when you install your machine. This can be a key area to a successful implementation.
I know you are going to make the ultimate decision yourself, but if you both choose the same machine, they will think it was all about them making the choice.
Explain the Schedule
A machine installation can be very disruptive to your regular work processes. Prepare your people ahead of time for the change.
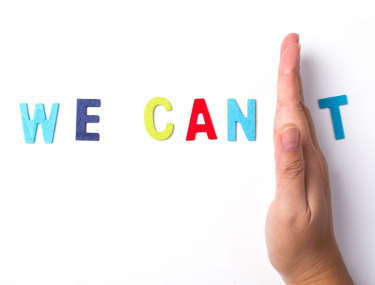
Explain the installation schedule. “It may be very cold for a day while we move the machine in through the front window. Bring your coat. We are going to have difficulty tagging while they are moving the machine. We may have to use this computer or that phone for part of the day. You can’t hang your shirts here when the men are working.”
Explain that things will be different for a day or so and you appreciate their help through this process. It can be frustrating for the installers and your staff if they are both trying to work in the same area.
Training and Expectations
Once the machine is installed, your people need training. You can’t operate this machine like you did the old one. New machines may require new procedures. The load size may be different. The schedule may change because of cycle times. What SOPs are you going to change and have you explained those changes?
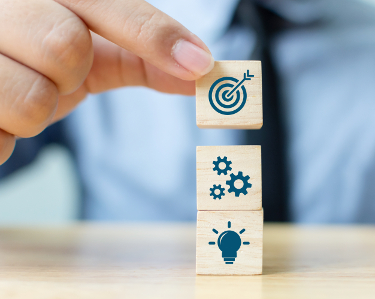
Your people need clear training on how to operate the machine. If your operator is not trained and comfortable using the machine, he/she will never like it.
Training could be done by your equipment guy. We are glad to train your staff how to operate the machine properly, but we are not prepared to train them on how to do their jobs. Maybe the factory rep will come for the start-up and training. Most would be glad to do that. Or maybe you could bring in a consultant to train your people and help with the implementation.
Make sure the machine is working properly before you turn it over to your staff. If it doesn’t do what it is supposed to do, they will never like it or use it. Better to go without the machine for an extra day than have them frustrated and hating the machine.
Part of training is explaining your expectations. How will they use the machine? What piece counts do you expect? What daily maintenance do they need to do? Those expectations need to be reinforced a week later. It is difficult to learn everything the first time.
Management Preparations
Not everyone will be happy that you are changing a machine. There may be hard feelings from others who wanted their machine replaced first. Other staff may like the existing machine. “You change this press and I will quit!” Even though they had problems they understood those problems and were used to them.
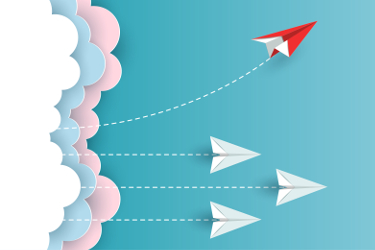
Consider ahead of time who might resist this change and be mentally prepared for whatever you have to do. Try to help them through this transition. If that doesn’t work, are you prepared to fire someone if they don’t use the machine properly and work with you? If things go really bad you may have to decide whether you will keep the new machine or the old staff.
Hopefully you have prepared everyone so that it’s not a problem.
Management part of the Install
Writing out a big cheque isn’t the only thing you need to do. You need to do some work ahead of time. Your staff are uncertain and concerned about what might happen. Maybe they are concerned that the new machine will increase production so much that they lose their job.
Change is difficult. The only cure is information. Maybe that means sending your cleaner to a neighbour’s plant for a day to get comfortable with the new cleaning process. You need to be aware and work to help your people. Change is only stressful when it is accompanied by the unknown.
We can change your machine. Can you ‘change’ your staff?
Kevin Marois founded Calgary-based Integrity Mechanical in 2003 to service plants in western Canada. He writes on issues related to equipment, its purchase, maintenance and use. You can reach Kevin at office@imicanada.ca or via his website www.imicanada.ca