You CAN save on maintenance
|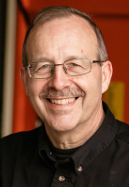
This is the third of a three-part series on maintenance that was originally presented at the Alberta Textile Care Association convention in Calgary, May 13, 2023.
We first talked about the minimum that you as an owner (or manager) have to do to keep things running. Last month we talked about how to start a maintenance program. This month we will look at ways to save money on equipment maintenance.
How to grow money
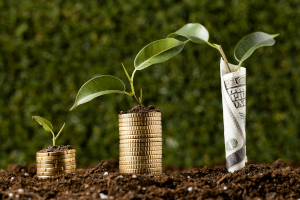
So now we get to the part that you really want to hear – how to save money. It is expensive to repair equipment. Technician’s wages are high; machine parts are unbelievably high. Freight costs on parts have skyrocketed.
My company has four technicians. We provide solutions to problems but we bill for those solutions by the hour. I come to your plant and spend an hour, so I send you a bill for an hour. It works out to about $2 per minute. Not as bad as a lawyer or accountant, but still costly.
Our guys are trained to say hello and get right to work. They are not there to spend time chatting with your staff unless they are discussing the problem. Because we bill for time, we try hard to reduce the time to do the repair.
Keep it clean

A clean machine is easier to maintain and repair. You (or your operator) can vacuum up lint just as well as I can. Plus, you do it for (almost) free. Throw out those old parts. If we took it off the machine because it didn’t work, then throw it out.
We have plants where we have to be extra careful not to drop a screw or small part. There is so much lint and garbage inside the machine that we can’t find anything. If you know that we are coming to fix a machine, save us some time by taking the old hangers out of the press. Or moving the boxes of supplies out of our way.
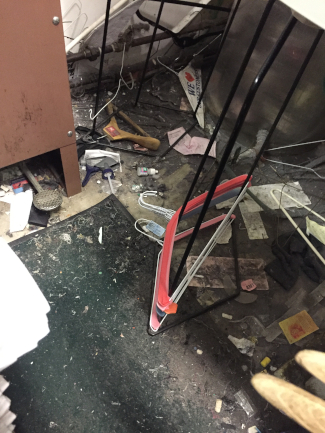
Most plants are not as bad as the ones in these photos, but there are things you could do to speed up our work. Sometimes we have to walk around a machine to get to the back. The path we have to follow is right where the presser normally hangs the finished garments. Yes we will be careful and stay clear of those garments, but that takes extra time. Couldn’t you hang them on the other side for an hour so I can move around more easily?
Good Info – error codes and symptoms
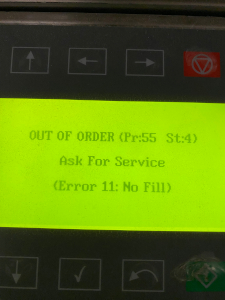
Virtually every machine being sold now has some sort of self-diagnostics. It will give you an error code or indication of what the problem is. That is a great help – but only if you give me accurate information.
It is not helpful when you say it’s doing the same thing again. Or, I didn’t look at the error code – I just turned it off and back on. Or, how about the fellow who told me the error code on his shirt unit was 99. Except that the error codes on that machine only go to 40. The best option would be to take a photo of the error code. The same goes for a description of the symptoms. Give me better information and you will get better results.
Another way that customers waste time and money is by telling us what they want us to do. “Change the check valves.” Or, “I need a new pump.” Our techs are trained to say, “I can do what you tell me to do or I can fix the problem. Those may not be the same thing. Would you like to tell me what it is doing and we will see about getting it fixed.”
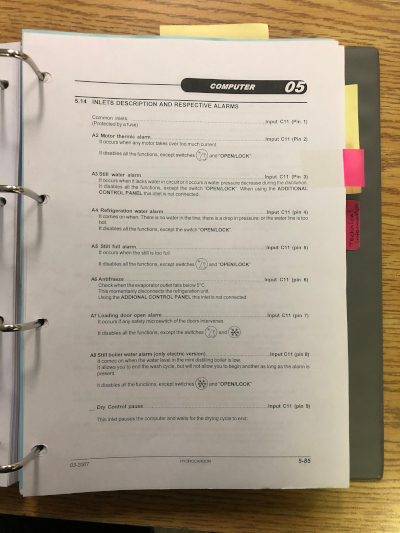
Often when we arrive the machine functions perfectly well. I could replace several parts but I would just be guessing. Is that really what you want? Give me a good description (including the error code) and we will do our best.
Make sure you have copies of the manuals for your machines. Especially the wiring diagrams. Some of the new machines even include the error codes in their computers. Plus they usually have a section on how to recover from each of the error codes.
Keep good records
Maintenance decisions are based on information. How good is your information? Do you have poundage charts, shirt counts, and solvent mileage? How else will you know if something is wrong.
We had a customer who had a problem with his water separator. It was dumping solvent with the water. The operator was oblivious to the problem. It they had tracked solvent mileage they would have discovered the problem much sooner.
Your operator can track some of these records. How many loads have you done since you spun the filters, cleaned the still, regenerated your carbon adsorber? How many shirts have you pressed since you changed the padding and when will it be due again? When did you last change the detergent pail – is the detergent pumping in properly? These are all signals that you need to pay attention to.
Free shirt padding
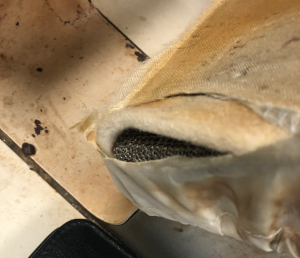
Let’s talk about shirt padding. As an example, Unipress recommends that you change the pad and cover after 10,000 shirts. Can you go 10,005 shirts? Or even 10,100? Sure! No problem at all. You might have to touch up one or two extra shirts a day.
Let’s see how those numbers work out:
Average presser’s wage $18, and with benefits $20.
You pay $1 for three minutes.
For the sake of argument let’s say it takes three minutes to touch up a shirt.
Two extra shirts a day is $2 per day.
That is only $10 per week.
But if you leave the padding another two weeks, she is probably touching up four shirts a day.
So that is $20 per week.
After a month it is 8 shirts a day and $40 per week.
But in the past month you paid out an extra $110 for extra touch-ups.
You did that to save the cost of a new pad/cover. That pad and cover cost $87.
The problem is that the change is gradual. “Must have been a bad shirt. Maybe she is having a bad day.” You make an excuse but you don’t notice the change until it is costing you lots of money. And a touched up shirt is never as good as a pressed shirt. And hard padding on a collar and cuff press will result in broken buttons. So you can change your padding on time for no additional cost.
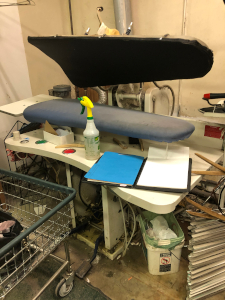
Whether it’s a press pad or pads/covers on a shirt unit – don’t try to stretch the time. You appear to be saving money, but have you calculated the additional labour cost when things don’t work perfectly? What is the cost of a lost customer because his shirts or pants weren’t done right? Figure out the cost of padding on a per garment basis – you will be surprised at how little it costs. Plus, it improves morale. When your people have machines that work well and do a good job, they try harder for you. Give them the tools to do the job properly.
Buy an air dryer
An air dryer removes water vapour from your compressed air. It will save you repairs and it will keep your machine working better. When you compress air, there is condensed moisture that circulates with the air.
The water washes the oil out of valves and cylinders. It is almost impossible to restore that lubrication in the air system on a machine. An air dryer will cost around $2,000 but it will pay for itself within two years. It will save you on repairs and it will keep your equipment working smoothly.
Work with your technician
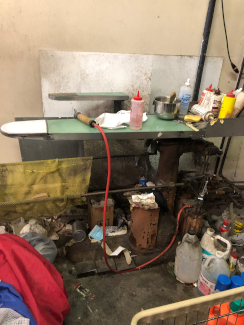
We would like to respond to every emergency immediately but often that is impossible. We are almost never standing at the office hoping for someone to call. What we are able to do sometimes is make suggestions. Sometimes it is just a matter of opening a valve or flipping a switch or making an adjustment.
If you are willing, we can often work with you to get you going. But you need to be able to follow instructions and you need to know the names of some of the parts. But you have to work with us – even if it is difficult. Or you can just wait till tomorrow or the next day and we will come and fix it.
You will do maintenance
The bottom line in all of this is that you are going to do maintenance – just try to do it on your terms. Willingly or otherwise, inexpensively or otherwise. No one else is going to do it for you and it has big financial implications
I know this sounds a lot like I am whining about working in your plant. I am not. We regularly move lint, boxes of hangers, clothes and even people out of the way. We do whatever it takes to fix your machine. But understand every additional minute costs you money.
I know this is work. If you are willing to put some time and effort into maintaining your equipment, you will save some money. Think about your machines once in a while. They deserve a little attention too!
Kevin Marois founded Calgary-based Integrity Mechanical in 2003 to service plants in western Canada. He writes on issues related to equipment, its purchase, maintenance and use. You can reach Kevin at office@imicanada.ca or via his website www.imicanada.ca