The Manual – An important part of the machine
|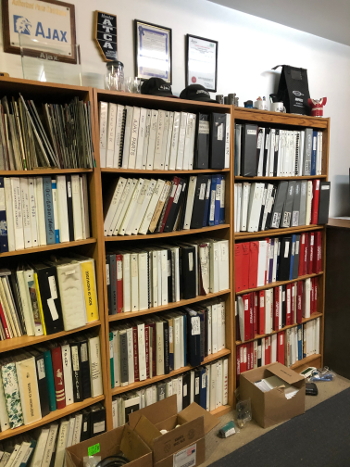
Your New Machine
That’s a beautiful machine you have there! It’s shiny and seems to work well. You must be proud to own it.
Are you proficient at operating it? Do you know what maintenance is required to keep it operating like new? Have you read the manual?
I already know your answers to those questions. I can tell by your phone calls that you don’t know anything about your machine. In fact, you can’t do much more than just start a cycle. When there is a problem you are hopelessly lost.
Have you read the manuals for your machines? (Can you even find them?) Machines are becoming more sophisticated all the time. We can do amazing things with the process controls, especially on washers and dry cleaning machines.
Last week I adjusted the towel cycle on a dryer for a customer. Her plant is in Moose Jaw (Saskatchewan), and I was in Calgary (Alberta). The Internet of Things is a great time saver – I never left my shop. Machines today are powerful, but only if you can control them.
Why do you need a Manual?
When you bought that new car did you throw the owner’s manual in the garbage? Did you just get in the car and start pressing buttons until it started to move? Why do we assume that we can just figure things out as we go?
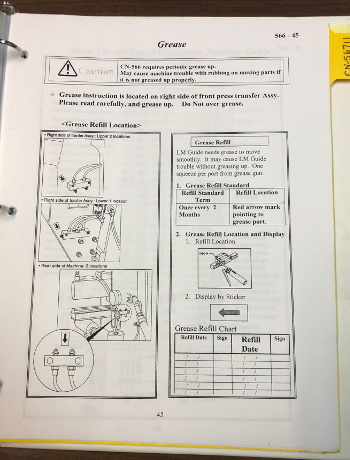
Today’s machines are more complicated. Things change between models. You may find that button doesn’t do the same thing any more.
We find people every week who don’t know how to operate their machine manually. Or they don’t know how to check filter pressure, or pump solvent from one tank to another.
We had a customer last week who did not know that he had to clean the pump strainer on his dry cleaning machine. We couldn’t figure out why his pump was not moving much solvent. We assumed (wrongly) that everyone knows you have to clean the pump strainer.
If you can spend $50,000–$75,000 buying a machine, surely you can spend a couple of hours reading the owner’s manual.
How to read it
Do not read it cover to cover. You won’t retain much. I know. I have done it many times.
The best way is to cover a section at a time. Understand how to operate the machine first. Next time, look at what maintenance is required. Highlight the parts that you need to refer back to. Bookmark the page so you can find it again. This book is just a tool to help you get the most from your machine. It doesn’t have to look pretty.
Error code pages should be copied and posted near the machine, so they can be referred to whenever there is a problem. There is a wealth of information in that book; share it with whoever needs it.
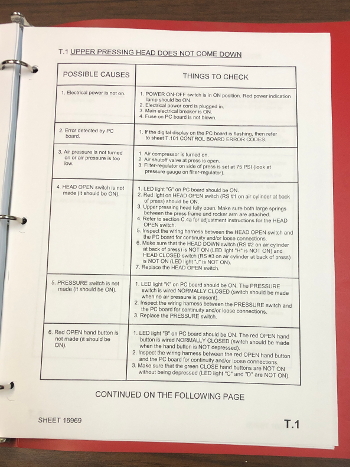
Where to get a Manual?
So you lost the manual. Or you bought a used machine and don’t have one. Now what?
First choice would be to contact the manufacturer. If it is a current model, most of them will supply a PDF file at no charge. You don’t even have to print it. There is a good chance that you can download the manual yourself from their website.
If it is an older machine, go back to whoever you bought it from. There was a manual when the machine was new. They might just have to look harder.
You may be able to Google the machine and find one that way. Most parts manuals are available online from parts distributors.
If that doesn’t work you might be able to get one from your repair technician. It might be a paper manual that he has to copy, but at least you will have it when you need it.
You could also ask other dry cleaners if they have the same model of machine and if they have a manual.
If you are going to buy a used machine, tell the seller you won’t buy it unless he provides a manual with it. Most people are too lazy to look for the manual. They never used it so they think you probably won’t either.
Who needs the Manual?
So who needs the manual for your machine?
The operator. The person doing scheduled maintenance. The technician doing repairs. The owner, to make sure he/she understands how the machine is being operated or repaired.
Most operators use about half of the machine’s features. They either don’t understand or don’t care to learn anything more than they need. They don’t care about anything else as long as the cycle starts when they press that button.
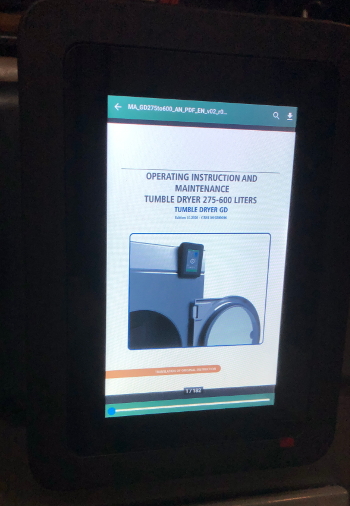
Every machine needs scheduled maintenance. Not all of it has to be done by a technician. Every manual explains in detail how to keep that particular machine operating properly.
Technicians use manuals to confirm part numbers when ordering replacement parts. We also use lists of error codes to diagnose problems. One of the most valuable parts of a manual is the electrical and air schematics. Those save time (and expense) when we are diagnosing a problem.
Finally, the owner needs a manual to make sure the machine is being operated properly. How many pieces is the machine capable of producing per hour? What maintenance does the machine require and what is the cost and time required to do those repairs? The owner doesn’t need to understand everything about the machine, but he/she needs to understand enough to make informed decisions.
The older your machine gets, the more valuable the manual is. If we can’t find a wiring diagram, we may have to trace a wire from one end of the machine to the other. We may have difficulty ordering a part because we don’t have a number. Our techs have tablets with hundreds of manuals on them, but that is still not enough.
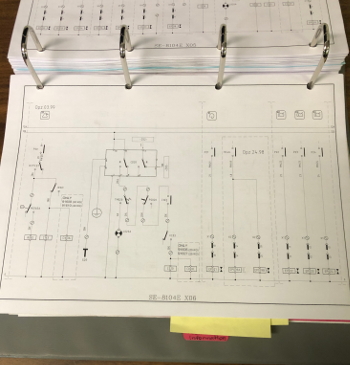
One great feature on newer machines is a manual that you can read on the machine’s display screen. Unipress even has a maintenance log that you can make notes in when you do maintenance or repairs.
The Manual is part of the machine
Equipment manufacturers spend lots of money developing manuals for their machines. Every fact and drawing has to be checked for accuracy. Maintenance recommendations have to be confirmed in the field. Repair procedures have to be followed and verified. It’s a huge investment that they make to ensure that their machine performs as promised in your plant.
Don’t leave it in the bottom of your filing cabinet. Let everyone use it. It is a tool to make your machine even more valuable.
It will save you time and money, but only if you use it.
Kevin Marois founded Calgary-based Integrity Mechanical in 2003 to service plants in western Canada. He writes on issues related to equipment, its purchase, maintenance and use. You can reach Kevin at office@imicanada.ca or via his website www.imicanada.ca.