Managing Machines
|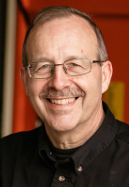
I was asked to do a seminar on Equipment Maintenance at the Alberta Textile Care Association convention in Calgary, May 13, 2023. When I questioned further, there wasn’t anyone who was really interested in learning how to repair their machines. Hmmm.
What they were interested in was learning ‘How to Manage their Machines’. Let me warn you right now that this will be work. You won’t finish this in a day or even a month. If you are not interested in working hard on this area of your business, don’t bother reading any further.
This is the first of a three-part series based on my presentation in Alberta.
You have machines, you need maintenance
You own (or manage) a dry cleaning, wet cleaning or laundry facility. One of the significant components in your operation is equipment. Without equipment, you have a bunch of people in a room holding dirty, smelly clothes. Equipment breakdowns are a significant stress in your life.
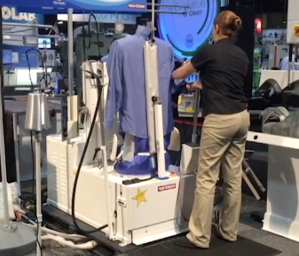
It doesn’t matter how good your marketing program is, how well your staff are trained, or how great your facility is – if you can’t produce what you promise, your business is doomed. There is not a day that goes by without some sort of an issue with some machine.
It’s a huge cost to have people standing around. But that is not the significant part. What about the promises to your customers? What does it cost you when you don’t deliver on time? Without operating machines, you have nothing.
You may not like machines, but you use them and you need to care for them. It’s time to take control of this area of your business.
What can you avoid?
There are different approaches to maintenance. I do understand that you don’t necessarily want to be the one doing the repairs. That’s fine, but you still need to control this critical area. Let’s talk about some different approaches to maintenance.
Approach #1: Ignore the problem
Some people’s idea of a maintenance program is to do nothing. They carry on blissfully ignoring the warning signs. Ignoring their staff requests.
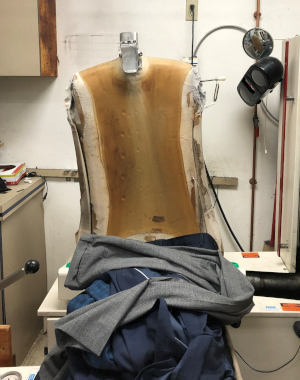
I have seen the shirt press with a bad shock absorber. The presser spends a minute trying to straighten the shirt out, but when she sends the buck in, it jerks the shirt sideways – and makes a big mess. But as long as that body kept moving back and forth, the owner would not do any repairs. It banged so hard that it was damaging other parts too.
At another plant the load still smelled when it came out of the machine. The plan was to hang it a bit longer or just hope the smell went away before the customer picked it up.
Bad idea. Ignoring the problem means you end up with a bigger bill than you should have had. But the stress level will go down, because soon you won’t have enough customers to worry about. Train your people to notify you when something is not working properly – and then take action.
Approach #2: Hire someone else to do it
The second approach to maintenance is to farm out everything and hope that your guy is taking care of things. You might say, “I don’t understand it so I’m not going to think about it.” Hopefully you have a good guy who is looking out for your best interests.
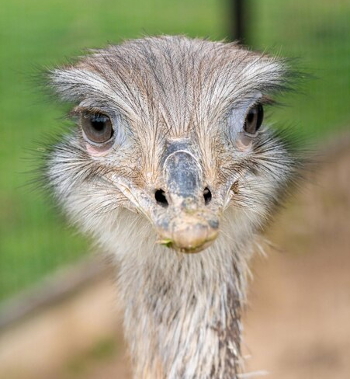
We spoke to a customer this week who did not even know what solvent was in his dry cleaning machine. He couldn’t tell us when we asked. So we asked to see the SDS sheet for his solvent. He didn’t know what that was either.
He wasn’t worrying about maintenance; he had hired someone, but things were not good. (His wife was very quick to tell us about the problems they were having.)
Approach #3: Relax, because it is taken care of
The best approach is a balance – some repairs done by your people, some done by technicians. Even with this approach, however, you need to be in control. You hire people, you organize technical support. You are aware of what needs to be done and you are monitoring it.
Your people know what daily and weekly maintenance tasks they need to do, and you are making sure that they are being done. I would suggest that you can do maintenance, without getting your hands dirty, by being in control of what is happening.
What things do you have to do?
Even though you aren’t holding the screwdriver, there are still some things that you must do.
Understand the process
You may not understand how your machine works mechanically, but you absolutely must understand the process that is happening when you press START. Is it a one-bath cycle or a two-bath cycle? Are you pumping to the tank or the still? Are you circulating solvent through the filter? Is it in the first wash or is it on cool-down?
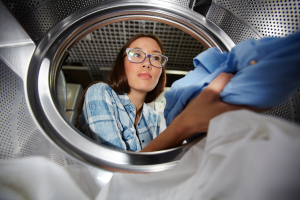
The same thing applies to your washing machine. When you look at it in operation, is it in the wash step or a rinse? Is it a high water level or a low water level? What are the rotation times?
This isn’t magic. There are understandable mechanical processes occurring. You don’t need to understand what makes the machine work, but you need to understand the steps in the cycle. What process is occurring right now?
Different garments or goods need different processes. You may not know what number the valve is that opens, but you need to know which tank you are pulling solvent from. What are the implications when one of those processes doesn’t work properly?
I understand that this is hard work! You are not going to learn it all in one day, but you do need to learn it.
Learn the names
You need to be able to communicate with your staff and your mechanic. To do that you must know the name of the part you are looking at.
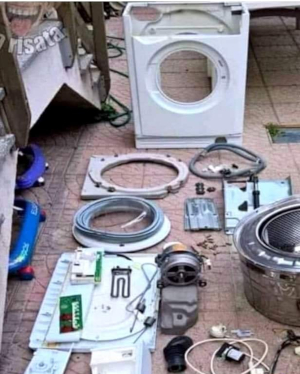
I had a phone call from a lady, “The thing fell off the side of the boiler,” she said. My thought?Either that thing doesn’t matter or you need to hang up the phone and run as fast as you can.
Sorry, I don’t know what the thing is. And if I don’t know what you are talking about, I can’t help you. We have to be able to communicate. Most people don’t put the effort into this.
Usually, they learn the name for a part when they have to pay for one. That is a $4,000 refrigeration compressor. I think you will remember the name for that one.
Manuals and error codes
Every machine comes with a manual. Sometimes the manuals are worth almost as much as the machine itself. They are a vital resource for your staff and also for your technician. Manuals contain installation procedures, maintenance schedules, wiring diagrams and error codes. Everything you need to know is in the manual. Don’t buy a machine unless you get a manual with it.
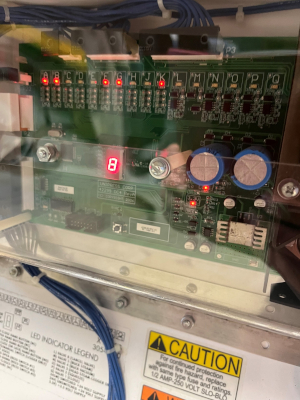
The manual will have detailed instructions on how the machine needs to be installed. If it is not installed correctly, it will not work properly. The manual will contain settings for anything that is adjustable on the machine. It may be possible to adjust temperatures, pressures and time on different things. Not every machine is the same. Sometimes the settings change over the years. The manufacturer has made specific recommendations so you can get the best possible results.
If I have to trace a wire or air hose, the diagram in the manual will save a significant amount of time. (You can read that as saving you money!) The manual has maintenance recommendations – things that need to be done to maintain peak operation. They may be daily procedures that your staff follow, or annual maintenance that your technician does for you.
Those manuals should be available to whoever operates the machine and whoever does maintenance on it. The manufacturer knows best. The pages that are most often referred to in the manual are the Error Code pages. They indicate what is wrong with the machine and usually give a recommendation on how to resolve the issue.
Relationship with the Trades
This is absolutely your area, your responsibility. You pick which technicians work in your plant. You hire or fire them and you pay them. Most importantly – you are at their mercy when you have a breakdown. Most tradespeople have too many customers. They are continually deciding who they are going to bump off today’s list. How do you rate?
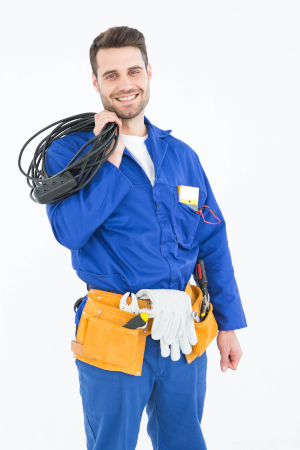
Do you pay their bills on time, do you listen to their advice? Is your plant clean? Are you a nice person that the technician likes to deal with? Or are you the guy that the technicians say, “I hate going to that plant.” I’m not just talking about myself and my technicians. I’m talking about your electrician, painter, boiler guy, welder, etc. Whoever it may be.
View their service as a relationship. It is not a one-time purchase and you can go down the road to the next guy if you want. This is a relationship that you need to develop and nurture. You will need that person badly one day.
Have an ongoing relationship with your technical people. Use them whenever you can. Try to use them sometimes when it isn’t an emergency. You can’t use him once a year and expect to be on the top of his priority list.
Build yourself a technical team: plumber, welder, boiler tech, electrician, etc. Use them so they are familiar with your plant and your way of doing things.
One other thing: don’t lie to your mechanic. He will know and he will think you are an idiot. Give him bad information and you will get bad results. If you didn’t do what you were supposed to do, tell him. If you did something stupid and wrecked the machine, tell him that too.
He already knows. You didn’t call him because you were lonely!
Pay your service team quickly. We pay our sub-trades within days of using them. They know there will be no issues when they work for me. If I need something in an emergency, they all respond quickly.
Next month we will talk about how to start a maintenance program for your plant and who should be doing the actual work.
Kevin Marois founded Calgary-based Integrity Mechanical in 2003 to service plants in western Canada. He writes on issues related to equipment, its purchase, maintenance and use. You can reach Kevin at office@imicanada.ca or via his website www.imicanada.ca