Family still has to play by the rules
|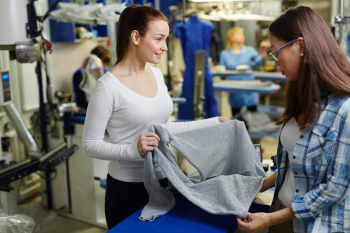
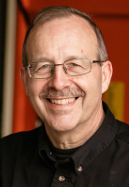
This month Fabricare Canada is focusing on couples who own businesses together. We have many customers like that. There is even a term for them: Mom and Pop stores. He does the cleaning and she does the pressing. Or maybe he does the pickup and delivery …
One of the problems with some of these small stores is that they are run as a family and not as a business. There are no written policies. Procedures change from day to day. Safety is ‘just common sense’. Unfortunately it is only ‘common sense’ after you have been burned or had a close call.
It’s fine if a husband and wife don’t care about their own safety, but there are often counter staff or part-time pressers. They need to be safe at work.
Safeties Bypassed
It is going to cost money to fix that machine. We all know whose pocket that money is coming from. And there is not much money in that pocket. Our firm has a policy about bypassing safeties – WE DON’T DO IT. We refuse to put our customers at risk.
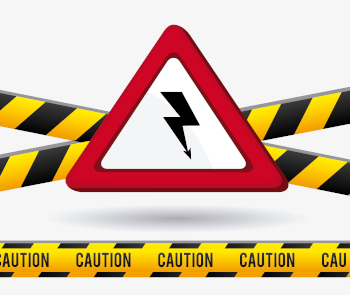
We do see it happen though. The safety bar on the shirt unit is disconnected. The second button on the Ajax sleever is bypassed. The door switch and lock on a washer don’t work anymore. The nitrogen cylinder not connected to a dry cleaning machine.
That is exactly how accidents happen. Yes, there have been fatalities: people reaching into washers that are still rotating. These machines are powerful and must be treated with respect.
When you bypass a safety feature on a machine, you create a risk of injury. Even more critical is the fact that you have created a liability. You have become personally liable for any injury that happens. Don’t tell me that Workers’ Compensation will cover any accident. If they find out you willingly bypassed a safety feature, they may also hold you personally liable and come after your personal assets. Maybe that will get your attention – even if an injured employee doesn’t seem to bother you.
Panels Left Off
Another pet peeve of mine is panels left off machines. “It’s just going to break down again so I will have to open it up and fix it again.” What if someone trips and falls into that machine? Rotating parts, bare wires, hot pipes. Think about the paperwork you will have to fill out if someone gets injured! (Tongue in cheek.)
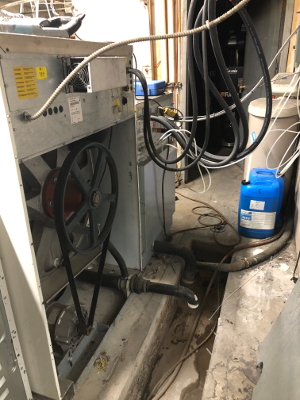
Your staff are too valuable and too hard to replace. They deserve a safe place to work. They give you their energy and time. The least you can do is provide them a safe place to work. Can you survive without that key employee?
So go have another look at your plant. Reinstall those missing panels. Repair those machines that don’t work properly. Insulate those pipes before someone gets burned. If I get burned your bill is going up!
Another related situation may be the couple’s small children in the store. We have seen many babies in laundry baskets over the years. That is fine. But they don’t stay in the basket. “Don’t leave your screwdriver on the floor. He likes to try to put it into the electrical receptacle.” We try to take the sharp tools away and give junior something safer to play with.
Familiarity sometimes leads to casualness. Not every plant is like this but they could be. All of these things add up to a safety concern.
Actual Examples
You may think I am exaggerating things. Let me give you a couple of examples. We recently looked at a collar-and-cuff press. When you turn on the power switch, the head automatically closes. “Hope you are ready because it is coming down full speed.” The owner said it has always been like that. That is the way they use it. That may be true but that is not the way it came from the factory. Our technician was not aware of the problem and narrowly missed having his hand crushed.
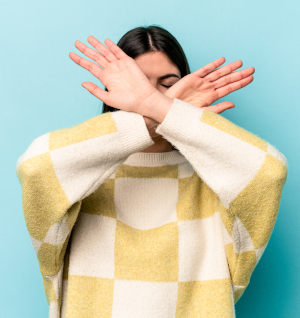
In another plant the safety bar for the shirt unit was not working properly. In our testing we confirmed that the problem was the safety switch. We bypassed the switch to confirm it was the one causing the problem. The owner wanted us to leave it bypassed so he could finish the shirts for the day.
One of our customers recently had a problem with a dry cleaning machine. They had broken the still door switch. Rather than replacing the switch, they just jammed it back together. No more alarm so they thought they were good to go. It ran fine until the next time they cleaned the still. They closed the door partway and started the machine. There was no alarm, but there was a lot of solvent that spilled out of the still because the door was not completely closed.
There may be other safety concerns in your plant: uninsulated steam pipes, unlabelled chemicals, steam and vacuum pedals that have been switched, hangers on the floor, etc. They are annoying but they probably won’t result in a critical injury.
The problem with a small store is familiarity. Everyone knows about everything, so safety concerns slip. Just because it is a family run store it doesn’t mean it has to be unsafe.
Kevin Marois founded Calgary-based Integrity Mechanical in 2003 to service plants in western Canada. He writes on issues related to equipment, its purchase, maintenance and use. You can reach Kevin at office@imicanada.ca or via his website www.imicanada.ca