Begin a Maintenance Program
|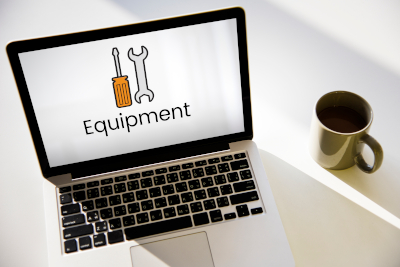
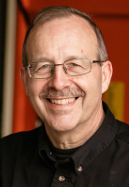
This is the second of a three-part series on maintenance that was originally presented at the Alberta Textile Care Association convention in Calgary, May 13, 2023.
Last month we talked about the minimum that you as an owner (or manager) have to do to keep things running. This month we will discuss how to start a maintenance program. Next month we will look at ways to save money on equipment maintenance.
How do I start a maintenance program?
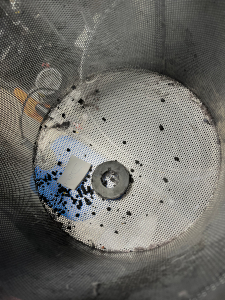
We all agree that you need to maintain your machines. And we both know that you don’t do a very good job of taking care of them (I’ve seen your plant). So how do we change that?
A good place to start might be to total up all of last year’s invoices for maintenance and padding. That might motivate you to look after those machines. It is work keeping track of your machines, but it will save you money, keep your staff happy, reduce your downtime and improve your quality.
It may seem rather overwhelming designing a maintenance program for your entire plant all at once. You can’t do everything at once. Pick a couple of key areas and get them organized. Then expand to other areas of the plant.
My suggestion would be to start with the dry cleaning machine and the shirt unit. Those are both critical machines and they need a lot of attention.
What needs to be done?
Commit yourself to doing the necessary groundwork. To find out what maintenance needs to be done, look in the manual from the equipment manufacturer. All machines have a service schedule. The manual will list maintenance items that must be done so the machine will continue operating properly.
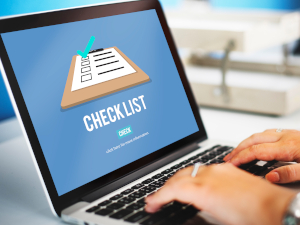
To build a schedule of required maintenance, use the manuals, consult your maintenance people, talk to the manufacturer. Then make a list for each machine. You need to include cleaning, maintenance, padding and observations (being aware of pressures, temperatures, sounds, etc.), so that you know the machine is operating properly.
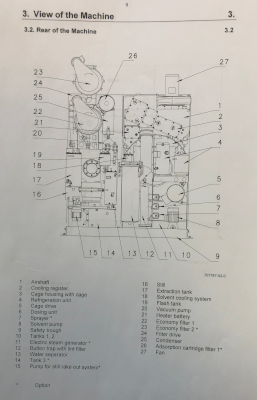
Let me give you a couple of examples:
Clean the spotting board
- Flush through with water every month.
- Check the flapper valve so the chemicals can drain into the waste bucket.
Check the float valve in the return tank
- Check if it is overflowing in the morning.
- Or it may be slow to fill back up during the day.
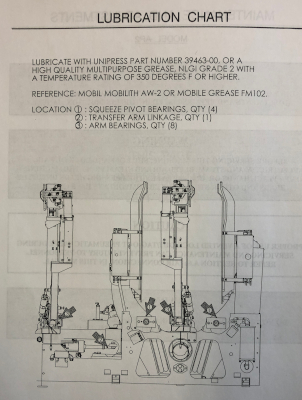
Check the drain valve and water valves in the washers
- Check for water going down the drain.
- Check for low water levels in the drum.
Check/change compressor oil
- Drain the compressor air tank every day.
- Check the air filter every 6 months.
- Change the oil every 6 months (Devair recommends every 3 months).
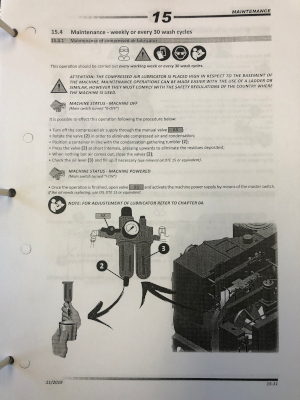
You can’t do this all at once. Take your time and build a good program. As you have time, include the rest of your machines.
Who will do it?
So you have a list of what needs to be done. The question now is who will do it? I see three choices: the machine operator, your staff maintenance person or an outside technician. It’s not a one-answer question. You need to involve all those people at one time or another.
I firmly believe that every machine operator should have to do some daily or weekly maintenance on their machine. Clean the lint filters, wipe the press down, and clean the chests on the shirt unit. If they do that they will take ownership of their area.
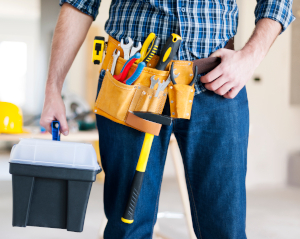
Slightly more complicated tasks could be done by an in-house ‘handy person’. They could change press pads, swap detergent pails, clean the stills, and maybe even grease the equipment. You have to do some of this in-house – there isn’t enough money to bring in a technician for all those tasks.
There are times, though, that you will have to call in an outside technician with specialized tools and experience to work on your machines. Someone who can quickly diagnose and fix your problems.
Who will monitor?
The most important point of all of this is that you need to take control of this area of your business. Regardless of whoever is doing the maintenance, someone has to be responsible to make sure those tasks are done. In most plants that will be you.
You need a scheduled maintenance plan and you need a budget for maintenance.
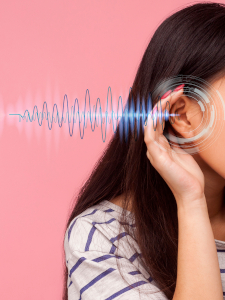
You MUST be involved in this critical area of your business. It has to be done on your schedule and to your standards. That equipment is an investment, not just an expense.
How do you monitor things? Checklists are essential, but the best way is MBWA – Management By Wandering Around! Once a week, tune everything out and just walk through your plant focusing on your machines. Look, listen and smell.
You don’t have to know what is wrong, just that something has changed. Look for stains or leaks. Listen for steam or air leaks. Smell the machines and the processes. Look at the pressure gauges – put a line where normal is. Train your people to talk to you. Get them to report when something is different.
There are almost always signs that a machine is going to break down. Things change gradually, and if you’re not intimately aware of how things SHOULD be, you might not notice until it is really bad – at that point, it may be too late.
When is it time to stop?
Now that we’ve got you doing maintenance, do you know when to stop? You can keep almost anything running, if cost is not a consideration. But every machine has its lifespan. Every plant should have an equipment replacement plan, rather than a knee-jerk scramble to get something in when a key piece dies.
Make a list of your problem machines. List them from critical to ‘it would be nice’. Then put in suggested replacement dates for each machine. That date doesn’t mean you can’t push things back, but at least you are thinking about it and are preparing to do something, and getting resources in hand to do it.
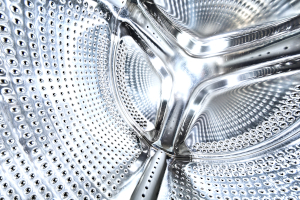
You need to do some research. What machine is best for your plant? What options do you have? Do your homework so you’re not stuck buying whatever is available.
When you have a breakdown, you will pay anything to get the machine back up and running. You’ll pay overtime wages to whatever mechanic shows up. You’ll pay overnight freight charges to get the part. And you probably won’t get as good a result as you would have if you’d planned ahead.
We have customers that replace one machine every year. They usually don’t have breakdowns or emergencies. The other benefit to new machines are the new features – better controls, savings in labour and more efficient operation. Plus, your staff are happy and not standing around.
Equipment maintenance is one of those difficult things that most people try to ignore. You can’t get away from the machines so you may as well take control – before they do.
Kevin Marois founded Calgary-based Integrity Mechanical in 2003 to service plants in western Canada. He writes on issues related to equipment, its purchase, maintenance and use. You can reach Kevin at office@imicanada.ca or via his website www.imicanada.ca