A child could do laundry – but do it right?
|You may think that because you do lots of laundry, you are a laundry expert. Maybe. But any grade school kid can do laundry – does that make them experts?
The difference is that you do it professionally. You need to know about detergents, load classifications, fabric content, garment construction and machine maintenance. And, you need to make money doing laundry, without ever damaging anything.
Machine problems
Washing machines are quite reliable but there are still some things that can go wrong. Your machine has inlet valves that allow cold or hot water into the machine. Sometimes they don’t open; sometimes they don’t close off tight. If the valve doesn’t open you may not get enough water or you may get the wrong temperature of water. If the valve doesn’t close tight, there may be water leaking into the basket whether the machine is running or not. That may overfill the machine and dilute your detergent or it may just waste water.
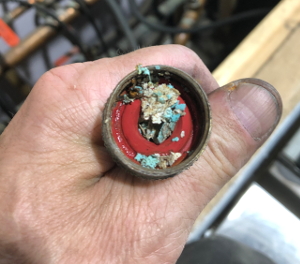
How do you check your inlet valves. Look at the drain pipe when the machine is not running. Is there water running down the drain? If yes, then one of the valves is leaking.
Another critical component is the drain valve. It may stick open or it may not close tight.
You should not see a steady flow of water down the drain when the machine is operating. Sometimes the valve sticks because it is jammed with collar stays or mop strings. This one is a little more difficult to fix. Take the drain hose off the valve and look inside. Clean the valve and see that the ball moves freely.
Most washers use a pressure switch and hose to control the water level. If that hose becomes plugged or restricted, you may get an alarm or you may not get sufficient water to wash properly. Disconnect the hose and flush it clean.
The washer has some other parts (temperature sensors, belts and an out-of-balance switch). They are not difficult to fix. Just check in your manual for your particular machine. Or check with the manufacturer’s tech support line.
Operator problems
So now let’s talk about the problems that you cause. The most common problems are overloading/underloading or selecting the wrong cycle.
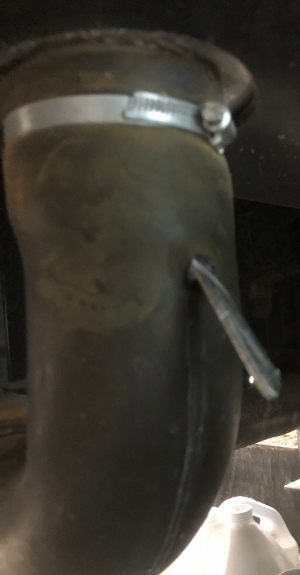
We have had a washer overloaded so much that they broke the door trying to force it closed. Or how about the operator that puts the load in, adds a little water so the load will compact and then fills the machine to the top. Mechanical action is part of the cleaning process. As the goods lift and then drop, water is forced through the fabric – flushing the soil out.
Overloading the machine eliminates that mechanical action. The ISO 9398 standard says you need 10 litres of drum volume for every kilogram of weight. The load has to tumble – not just rotate.
Underloading is a problem as well. Too small a load will not have the mechanical action it needs and it may not balance well when you try to extract it. Plus it wastes water and detergent.
Another operator problem is selecting the wrong cycle. The wrong cycle may result in excessive temperature, too much mechanical action or the wrong detergent.

Some operators use powdered detergent, which is fine as long as the operator actually uses the correct amount. Often the detergent is just carelessly dumped in. They use the same cup for all the machines. One load may get too much and the next load may not get enough.
Loads need to be classified correctly. We have all seen what happens when a red article is washed with the whites. Finally, pockets need to be checked. Or, if you are doing restaurant work, you need to remove the forks and pizza crusts before you put the load in to wash.
New machine features
Technology will help you eliminate some of these problems. Most machines now are softmount. With the inverter control they are able to retry the extract multiple times if the load goes out of balance. That same inverter can be used to weigh the load before the cycle starts. Water levels and detergent injections can be adjusted based on each load’s weight.
Wash computers now control the amount of mechanical action, temperature, water level, time and even the extract. Newer machines provide detergent signals to control what product is injected in each load. Individual cycles can be customized to match the goods being processed.
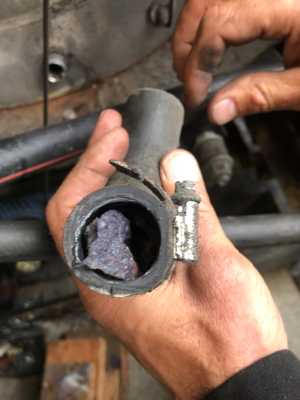
Water level controls are more sophisticated. They will read if a water level increases or decreases during the wash. Is the inlet valve leaking into the drum, or the drain valve leaking out?
The newer machines will have error logs and operator history so you can monitor things. We can even adjust your cycles remotely and receive an email notification when there is a problem.
In other words, it pays to invest in new equipment when technology justifies the cost through improved operation, efficiency and productivity.
Final thoughts
A commercial washer can make you money. One that is not working properly or is not operated correctly can cost you a lot of money. Washers are more reliable now, so we tend to forget about them. Once a month you need to take 10 minutes to ensure everything is working correctly and that your operators are following your procedures.
Kevin Marois founded Calgary-based Integrity Mechanical in 2003 to service plants in western Canada. He writes on issues related to equipment, its purchase, maintenance and use. You can reach Kevin at office@imicanada.ca or via his website www.imicanada.ca.