‘All I need is the air that I breathe’
|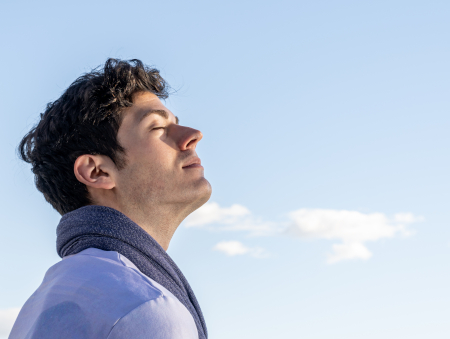
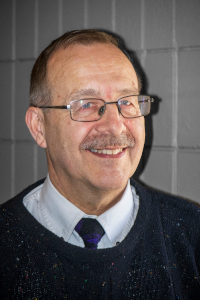
Let’s talk about air. I’m sure we have discussed this before, but we seem to have lots of plants having air issues right now. The review is probably a good idea. Machines are like people. They need a steady flow of clean, dry air. It can’t be too hot or too cold. And it has to be clean air.
Air pressure is what creates movement in all of your machines. Whether it is the head closing on a press, the arm waving on a shirt unit or a valve opening on your dry cleaning machine – all of those things happen because of compressed air.
You have an air compressor somewhere in your plant. It takes room air and squishes it into a tank. That pressurized air travels down the pipes to each machine to cause things to move. Almost every machine in your plant uses air in some way for its operation.
Compressor Maintenance
The air compressor is probably the most neglected piece of equipment in any plant. The only attention it gets is to flip the switch on in the morning and off again in the evening. Hopefully, you also drain the tank once a day.
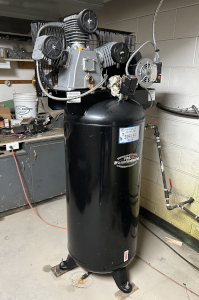
Compressors are amazing pieces of equipment. They operate in an environment that is too hot. The oil is rarely checked. And most of them are covered in dust and lint. It’s amazing they work at all. Compressors should be installed somewhere cool with a good supply of clean air. They generate a lot of heat and the temperature is hard on the motor and the pump.
Old compressors spit out a lot of oil with their air. That oil has often been baked in the compressor. It breaks down and forms a sticky goo that plugs pipes and causes valves to stick.
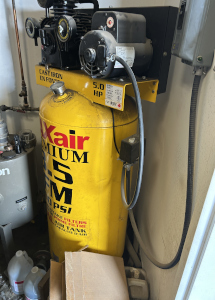
The head on your press doesn’t close. The arms don’t drop on your shirt unit. The tank inlet valve on your dry cleaning machine is stuck open.
All caused by bad air.
Compressors have a duty cycle. Run for X number of minutes, then turn off for X number of minutes. Check your manual to make sure you are not overworking your compressor. Different styles of compressors have longer or shorter duty cycles.
You may wonder where the water in your compressed air system comes from. There is humidity in the air in your plant. That humidity is condensed back to water in the air system. That water needs to be removed to protect the lubrication on the valves and cylinders on your machines. The first line of protection is to drain the air compressor tank every day. Crack the valve open for a few seconds and blow the water out of the tank.
Refrigerated Air Dryer
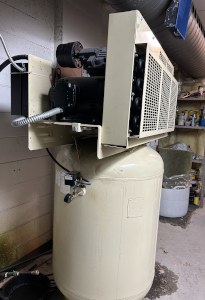
This is a critical piece of equipment that many plants don’t have. Moist air goes into a box and dry air comes out. The result is that your machines run better. That’s all you need to know. Cooling the air causes the water vapour to condense back to liquid so it can be removed from the air stream.
The air dryer is usually installed with a particulate filter in front of it and a coalescing filter after it. The particulate filter will keep out any debris and it will remove some of the water. The coalescing filter will remove any oil from the air stream. A lot of oil coming from the coalescing filter is an indication that your compressor is having problems.
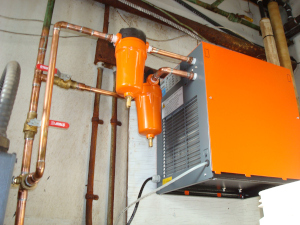
The air dryer uses room air to cool its refrigeration system, so it should not be installed in a boiler room. The heat in there makes it work harder.
Air Filters and Fittings
Most pieces of equipment have a combination air filter and air regulator where the air line connects to the machine. That device will separate out some of the moisture in the air. It has an automatic drain that dribbles the water out as it accumulates. That is good. You want that water dripping on the floor rather than going into the machine.
Most machines today use push-to-connect air line fittings. They are great to build the machine and to maintain it. Eventually, though, some of them will start to leak. A slight hiss is not unusual. When it becomes a significant leak it should be repaired. Some machines have dozens of push-to-connect fittings, so it would be difficult and expensive to try to replace them all.
Monitor your machines for air leaks. If they get bad, your compressor will be overworked. We have seen plants where the compressor runs non-stop. That situation won’t continue for long.
Your Maintenance Program
You may have an organized and scheduled air management program. Or you may simply wait until everything quits working. Either way, one of us will benefit from your program. I am OK with either. We have plenty of work so if you want to save some money, take care of your compressor.
If you don’t want to see me, buy an air dryer and take care of your air compressor. I guarantee that it will save you a lot of money, your machines will run better, and your staff will breathe easier.