Training makes a difference
|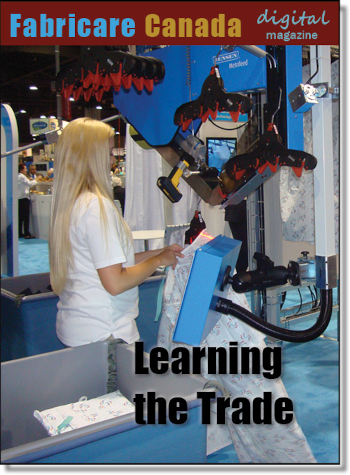
The dry cleaning/wet cleaning and laundry trade is more complex than your customers realize. To them, it’s a matter of getting out the spots and returning the garments on time. You know there’s a lot that goes on behind the scenes.
We asked, you answered
We posted a quick survey asking how YOU were trained, and what the results have been. Answers came in from Alberta, Ontario, Saskatchewan, and Quebec. Without exception, those who responded have been in the industry more than 15 years. Obviously, it’s a great place to get your foot in the door.
Most who responded are in dry or wet cleaning, but we had a few from industrial laundry facilities, or “other” branches of the industry. Many of them started out in relatively humble positions.
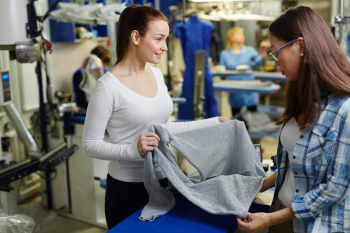
- Part time front counter clerk
- Assembler
- Presser
- Service technician
- Soiled sort wash floor operator
- Plant support
- Route driver
- Helper on deliveries
- Selling equipment
But they hung on. They got training, and they rose through the ranks. Where are they now?
- Owner/Operators
- Plant Managers
- President
- National Sales Manager
- Director at large healthcare laundry
- Association executive director
- Chief Operating Officer/General Manager
- CEO
Their training ran the gamut from being instructed by other employees or the boss, to going to school, to learning from outside equipment reps and consultants. Most listed more than one form of training they’d had along the way. In the process, they also learned pretty much every position in the plant, making them more valuable to the company — as evidenced by their rise to the top over time.
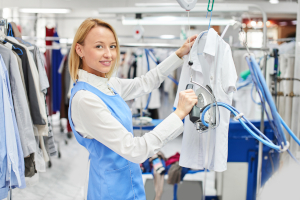
Who’s the best?
When asked if there were specific trainers who had been most helpful to them that they wanted to salute, our respondents had no trouble coming up with names. Many have become legends in our industry.
- Kevin Marois
- Too many to list.
- DLI, IFI, Stan Golomb, Sid Tuchman, Brian Kerr, Irving Berlin, Eric Cole, Stan Kaplan.
- Too many to mention; each were excellent.
- Kevin Marois on equipment maintenance. And he’s offered seminars that have been extremely valuable. There are dozens of others.
- My parents.
- My late father-in-law, Alexander Shindman.
- DLI.
- John Sealey.
Formal training
Mary Scalco is the CEO of the Drycleaning & Laundry Institute (DLI), which began in 1927. We asked her why formal training — or at least good training — is so important to the success of an individual, and therefore a company.
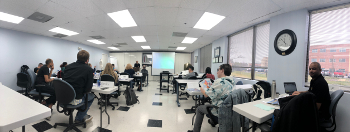
“Training is so important to maintain the professionalism of the industry,” she said. “This is not a business you learn by trial and error because during that process you may be ruining customers clothes. You want to learn how to process garments the correct way and by teaching the science behind why something is done the individual learns how to handle and is able to successfully handle something new, something they may have not seen before. Fashion is always changing, consumer needs are always changing so with the proper training you can handle anything that comes across your counter.”
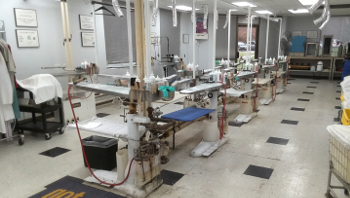
Sometimes it’s just not feasible to send people away for training, of course. Cost is a consideration, and time. And that’s why schools like DLI have evolved over time to meet the needs of today’s companies for highly-trained employees.
“DLI has incorporated virtual training courses into the school,” said Scalco. “These courses are great for those individuals that, for whatever reason, cannot get away from home for any length of time. There is nothing like face to face, hands on training, though. Our students tell us that that is the best part of the training they get at the school.”
Our series continues…
All this month we’ll have articles on training, and a first-hand report from our columnist, Linley McConnell, fresh back from her class at DLI.