Live and Let Dye
|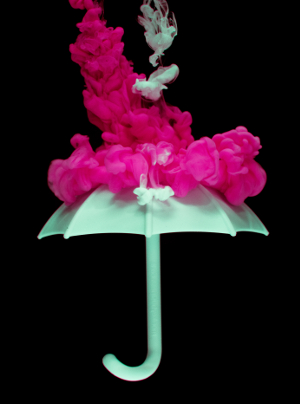
The swirl of a multi-coloured scarf, the bright pop of colour on a necktie, a swishing sky blue skirt, the interesting animal print pattern on a pair of athletic shoes. Umbrellas that look like giant sunflowers. Sheets and quilts that light up a room. Draperies that set a mood and tie together the entire theme of a home. What would fabrics be without colour?
There are many kinds of dyes – from natural to synthetic – that enhance our lives with brightness. But most are applied using very inefficient processes that result in an abundance of waste going into the environment.
Interesting statistics:
- Conventional dyeing uses an average of 100–150 litres of water to dye one kilogram of textile material.
- 28 billion kilograms of textile fashions are dyed using 5 trillion litres of water each year.
- Some of the things that make dyes valuable (durability, resistance to degradation, anti-microbial agents in them, ease of application) make them more environmentally toxic.
- The waste water from textile plants is said to be classified as the most polluting of all industrial sectors, considering its composition and volume.
- Dye in the environment can interrupt photosynthesis (the process of turning carbon dioxide into oxygen by plants), which impacts the entire ecosystem.
How is dyeing done?
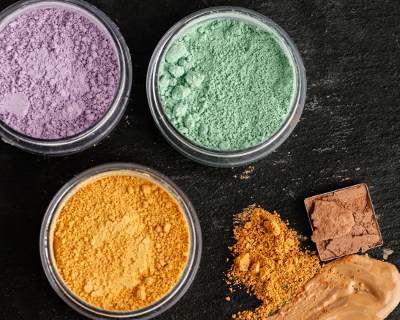
Fabrics are prepared (bleached, optical brighteners added, impurities removed) and then dye is applied. No dye works on every fibre, so there are many types of dyes. They may adhere to the surface of the fibres or be absorbed into them. The dye chosen is based on what the fabric is made of and what it will be used for. For instance, fabric like an awning that will be exposed to sun must not fade. Fabric that will be wet, like for swimsuits, must not have dyes that run in water.
Finally, the fabric is finished by rinsing away excess dye, which results in contaminated waste water. Anywhere from 10%–50% of the dye used is lost at this stage, resulting in about a million tons of dye compounds in the environment each year. Of course, water treatment processes are used to try to remove the dyes before the water is released, but it is an exceedingly difficult chore.
Synthetic fibres don’t take dye well
If you’ve ever tried to paint something that is synthetic, like a plastic lawn chair, you know that the paint you apply is really just sitting on the surface of the plastic. It doesn’t sink in, and is easily scraped off with use. When it comes to synthetic fabric fibres, there is the same difficulty on a much smaller scale. Yet the impact of having colour wear off can make a garment unwearable from an aesthetic viewpoint.
What can be done differently?
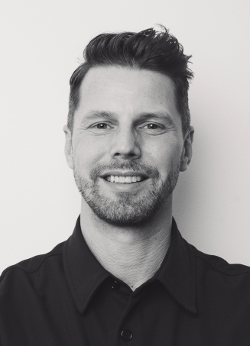
There are companies attacking the problem of dye waste by changing the process that introduces it. One such company is We aRe SpinDye, a Swedish company established to create a sustainable and transparent standard for dyeing synthetic textiles. (The name is a combination of ‘We’ for the collaborative effort, ‘Re’ for recycled and ‘SpinDye,’ the name of the technology.) They are not the only ones, but their approach is very interesting. (Another company to research is DyeCoo.)
“71% of the earth’s surface is covered by water, of which only 2.5% is fresh water – with some bound up in glaciers, and much below the surface as groundwater,” said Andreas Andren, CEO of We aRe SpinDye, in explaining the need to be frugal with water in industrial procedures. “Washing, dyeing and finishing of textiles requires large amounts of clean, fresh water – ranging from 100 to over 300 cubic metres of water per ton, depending on the material and efficiency of the manufacturing processes.”
He estimates that annual global textile production is between 60 and 70 million tons, requiring 9 million cubic metres of water – enough to fill 3.6 million Olympic-size swimming pools.
We aRe SpinDye is turning the process on its head. Rather than applying dye to the finished textile, they are inserting the dye directly into the synthetic fibres as they are being extruded and prepared for use in fabric manufacture. They say this results in a significantly lower use of resources.
“On average, we are using 75% less water, 90% fewer chemicals, 30% less carbon dioxide and 30% less accumulated energy,” Andren said.
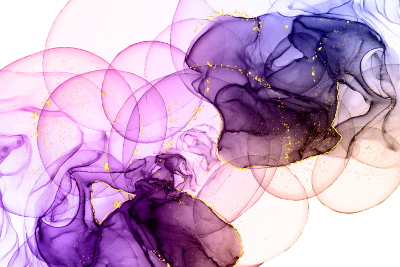
When asked why their process is better, Andren gave an example. “Think about a LEGO brick. There is no logical reason why a synthetic material would be processed, manufactured, injection moulded, and then coloured on the outside,” he said. “Not only is it immensely difficult to make colour and dyes stick onto a surface made of synthetic material, but it would also require an additional processing step. However, that is exactly what is being done in the textile industry.”
What does the industry think?
The company has formed agreements with an impressive array of fashion companies that want to have their products dyed in the more environmentally friendly manner. They include:
- Fjällräven
- H&M
- Bergans of Norway
- Peak Performance
- Adidas by Stella McCartney
- NOAH
- Superdry
- Gina Tricot
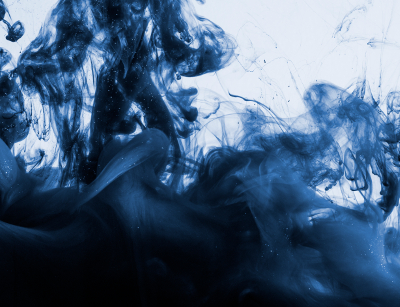
There are sure to be more companies that look for ways to improve their environmental footprint in the manufacturing of their goods. As demand for better practices goes up, research and development will follow.
How will garments and textiles dyed in this manner change your cleaning processes? What might you have to consider in handling them? Don’t wait until they show up at the front counter before you start learning about some of the new technological ramifications in the fashion industry.
[For exhaustive information on dyeing: Textile Dyes: Dyeing Process and Environmental Impact.]