K-Bro is K-BIG!
|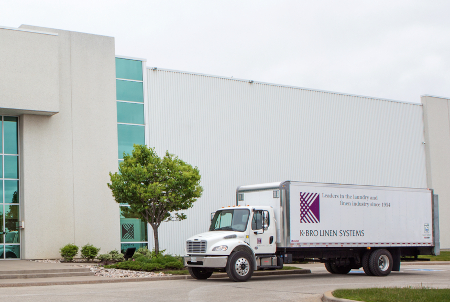
The K-Bro Linen plant in Vancouver called “Riverbend” was nominated for our Best Plants competition. To wind up Laundry Month, we’re starting the Best Plants tour early by giving you a look inside one of these monster plants. Our guide for the tour is General Manager Kevin Stephenson.
The plant is state-of-the-art from the front door to the back, and stuffed with Jensen equipment, as are other plants in the K-Bro family across Canada. Take a look!
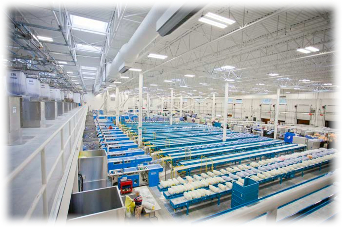
Just the Facts
- Plant is roughly 120,000 sq. ft.
- There are over 100 employees per production shift.
- Runs 1 shift per day, 10 hours per day.
- Processes about 200,000 pieces per day.
- Transportation conducted through a third party partner operating approximately 20 vehicles, either straight truck or tractor trailer.
What is the philosophy of K-Bro, as demonstrated by the company’s growth and operational standards?
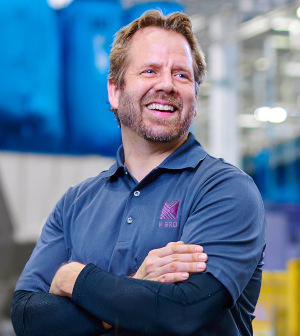
We are proud of our seven-decade history of responsible, innovative growth. While delivering industry-leading service, we have embraced our responsibility to the communities in which we operate and service. Putting people first, being dependable partners and embracing environmental stewardship remains our guiding philosophy.
At the core, K-Bro is a customer centric company with a strong focus on dependability (surety of service), quality (linen and service quality) and cost-efficient linen programs (inset with value adds). Within the Riverbend branch, we achieve this through experienced laundry operators and long tenured employees, and a company culture which puts customers first. The management team is committed to each other which translates into a mindset that drives continuous improvement and dedication to providing the best service possible for our clients.
How did you go about choosing the equipment in the plant, and why did you opt for what you have?
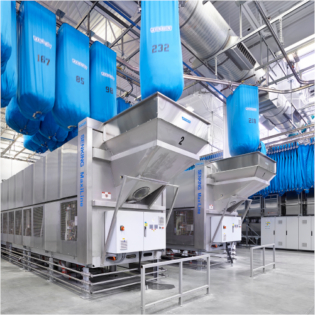
The K-Bro plant in Riverbend is the fourth build of its nature, experience from the previous three builds provided knowledge that contributed to the final design. Equipment reliability, pre- and after-sales service, and standardization (ability to share spare parts, knowledge) were major considerations when selecting an equipment partner (Jensen).
The plant is a steamless operation and was constructed with a sustainability focus by incorporating state of the art equipment technology to minimize consumption of gas, water and electricity that innately creates a positive impact on our carbon footprint. We continue to drive improvements in this area and are always on the look out for new technology that can further improve the operations.
Minimizing any transference of bacteria or viruses is key in your approach to processing textiles. How do you motivate the people on the floor to uphold this vital goal?
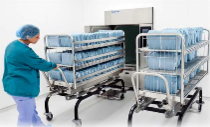
Hygiene best practices are supported through the adoption of employee training, infection prevention procedures, accessibility of personal protective equipment for staff, and contingency planning. Several attributes of the plant design incorporated details to assist infection prevention and therefore inherently helps minimize transference of bacteria or viruses (2 touch points on the clean side).
We carry both the TRSA Hygienically Clean and HLAC Hygienically Clean accreditations which help to drive best practices and keep us current on evolving industry trends. As a predominantly healthcare processing facility, our dedicated customer service team frequently engages with our customer base to make sure we adhere to and give thought to both plant operations and on-site delivery services.
What makes a K-Bro plant stand out head and shoulders above other plants? What do you feel makes it the best at what it does?
We invest in state-of-the-art facilities to serve customers for the long-term. K-Bro has always valued environmental stewardship, and we invest in highly efficient, energy and cost reducing equipment from world-class manufacturers. Planned, energy efficient equipment redundancies ensure year-round reliability through the most demanding times. Space is optimized and computerized control systems oversee the many factors that impact quality, energy-use and cost. We are committed to continuous improvement in operating and energy efficiencies.
3 things make it stand out:
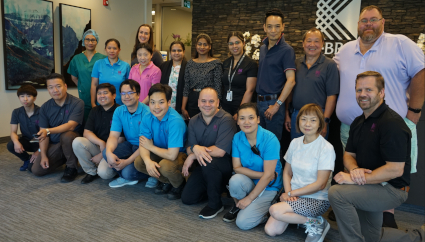
- Our People – you can have the best race car in the world, but without the right driver, pit crew, etc, it won’t perform. We have a team comprised of amazing talent in both this location and across the company. Having the ability to either reach out for support or provide support when needed creates a network that is second to none. We have numerous members of the management team in Vancouver and across our organization that have surpassed the 20 years of service mark which provides an unparalleled depth of laundry knowledge under the same company umbrella.
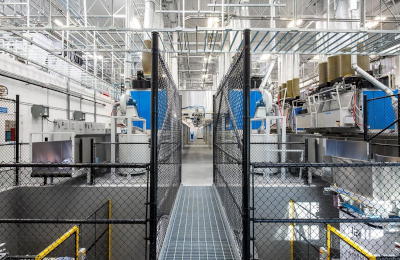
- Innovation – our latest 4 builds – many similarities – standardization (layout, flow, focus on safety, employee work environment), with each version adding enhancements over the previous.
- Adaptability – with the key people and ability for innovation, the organization has the strength of being able to adapt to changing market needs and challenges. The experience of the COVID Pandemic created a very uncertain environment and both the organization and each local team had to continually evolve to meet the ever-changing dynamics.
What does a “bad day” at K-Bro look like? How do you get things back on track?
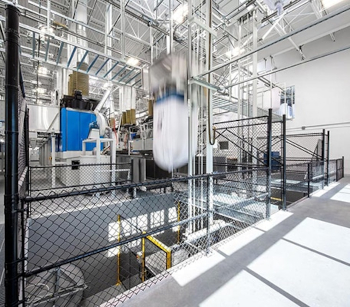
We never look at any day as a “bad day”… some days just happen to be better than others. But things like power outages and inclement weather (ie. winter storms impacting staff’s ability to get to work, making deliveries) can certainly create obstacles to overcome. At Riverbend, we’re fortunate that the plant has built in equipment redundancies, and available operational capacity that can be increased to very quickly get back on track.
Where feasible, our in-house maintenance team does a tremendous job making sure we have critical back up parts on hand to ensure efficient operations and works closely with numerous key vendors to ensure urgent parts are available, if the circumstance arises.
8. Are there specific individuals in the plant you’d like to salute for their above-and-beyond work?
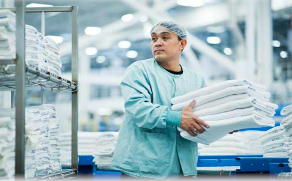
Several members of the Riverbend team have been showcased on the current version of the company website. Its not so much the work of any one individual but rather the combined efforts of all the multitude of pieces that keep us moving forward.
What’s in the future for K-Bro? You’re the biggest in the country. Where do you go from there?
Whether we grow organically or through acquisition, one thing for certain is that our customer focus will remain a top priority. We believe that if we can offer the best solutions for our customers and generate value towards achieving their mission, we will continue to be a partner of choice, and this reputation will only help us in growing K-Bro’s footprint, within and beyond Canada.
Your plant may not be anywhere near the size of a K-Bro operation, but there are things you can learn from industry leaders like this one. The emphasis on excellence is key. Keeping employees in sharp focus motivates them to help build the company. Finding what they do best and homing in on it has meant K-Bro’s name is synonymous with laundry — and with the future.