Innovation in the rear-view mirror
|As we focus on new innovations this month, I decided to think back over some of the changes I have seen over my career. Some are things you may not be aware of or even appreciate.
Washing machines
Washing machines today should really be called washer/extractors. They wash and then they extract. When I started in this business we washed in one machine and then transferred the dripping load to an extractor. The dryness of the load was dependent on how long you let it spin. There was no timer – pay attention!
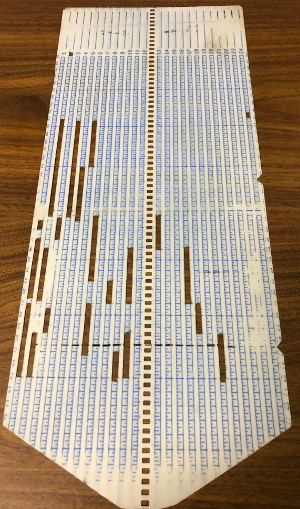
The washer was controlled by a card. Depending on the brand of washer there might be little bumps or even slots in the card to turn things on and off. Most of those washers had only one or two cycles. Everything was processed on the same cycle.
After that we got hard-mount washers. They would wash and extract in the same wheel. The G-force was only 100 so they didn’t go too fast, but at least you didn’t have to transfer the heavy bags of wet laundry. You had to have a good floor under a hard-mount washer – otherwise the whole building would shake.
Finally we moved up to soft-mount washers. These washers have springs and shock absorbers, so they don’t need a heavy concrete base. They also have computer controls that allow for multiple cycles and full control of the wash process.
Pressing equipment
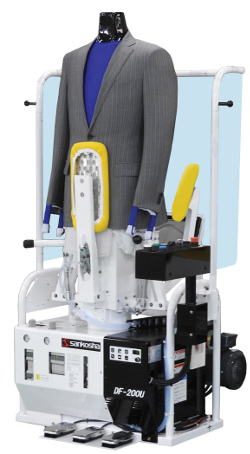
The Cissell suzie was the standard for decades. It would blow some steam and hot air into the jacket and then stretch it out of shape while it dried. Today’s finishing equipment uses multiple clamps and expanders to stretch a garment while it is being steamed and dried. Pant toppers clamp the cuffs and stretch the fabric while it is being steamed and dried.
One good thing that has changed is that most plants today do not have foot stompers. These presses were operated manually. Step on that big pedal and pull down on this handle and the head will close. We are certainly thankful for automatic pressing equipment.
Dry cleaning machines
I can remember powder filtration. You put in a scoop of diatomaceous earth and then a scoop of Darco powder. Darco is ground up carbon – as black as can be. You better hope the pump doesn’t hiccup or that black powder goes all over your load.
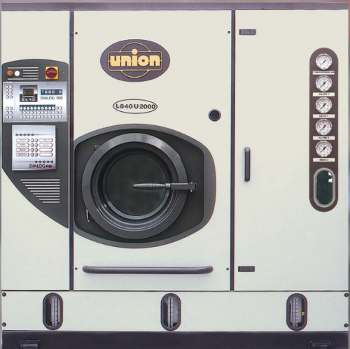
We now have foam sensors in the still to prevent boil overs. Some of our customers don’t even know what a boil over is. If the steam pressure is too high or there is moisture in the solvent, the still can cook too fast and overwhelm the solvent condenser. Sludge from the still mixes with water in the separator and the whole mess gets flushed into the clean solvent tank.
The worst part is that mixture of sludge/detergent/water/solvent boils at a lower temperature than solvent, so it is even more prone to boil over again. If you try to rush things it will boil over again and contaminate the tank you just finished cleaning up.
Dry cleaning machines used to have a switch or lever for every function. You controlled everything. The computers on dry cleaning machines now control the entire process – time, temperature, mechanical action, detergent injection. You can create different programs for different loads.
Detergent
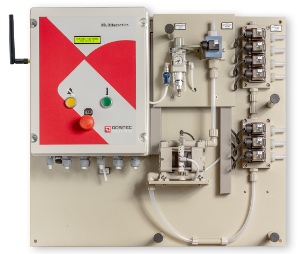
One of the first things I learned in this business was how to titrate Staticol. You took a sample of detergent from the dry cleaning machine, added several agents and watched for a colour change drop by drop. Then you could calculate how much detergent to add to the tanks. The tanks were charged with detergent. Once or twice a week the solvent was distilled and detergent had to be added to maintain the correct charge.
We also had a device called a conductivity control. It measured the moisture content in the solvent and would meter in a small amount of water to help remove the water-soluble stains. It worked well, but occasionally something would go wrong and it could dump a bunch of water into the machine, causing dye bleeding or maybe even a boil over.
Today detergent is injected automatically, the amount being adjusted according to the size of the load. It removes odours, controls bacteria and gives the fabric a nice hand.
Inverter controls
This is a box that controls the motors on your washer or dry cleaning machines. It allows for full speed control. It will protect the motor from an overload and it allows us to control wash and extract speeds. We can have gentle wash, regular wash, slow extract, high extract – and we do it all with fewer controls than previous machines.
An inverter allows you to do gentle wet cleaning and shirt laundry in the same machine. It also controls the basket or fan speed on your dry cleaning machine. We can even reduce the air flow as the load dries.
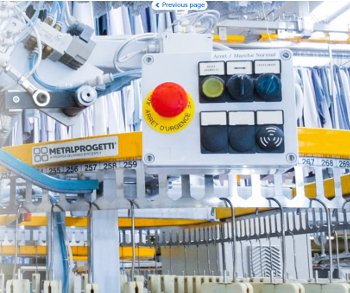
Assembly conveyors
This is something from science fiction. You scan a bar code, the conveyor takes that garment, bundles it with the other items from the same order and then puts a bag and a label on it. If there are too many items to put in one bundle, it splits the order and labels each bundle appropriately. And it never phones in sick. It doesn’t have trouble reading numbers upside down and it doesn’t reverse numbers while looking for the correct invoice.
Shirt units
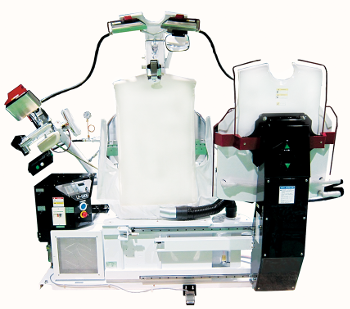
Shirt units were always three machines. Sleever, collar-and-cuff and body press. That means you paid for an extra machine, you did an extra pressing step and you had to maintain a third machine. If your presses weren’t working properly or your presser was having a bad day, you could have ‘leave off’ marks at the top of the sleeves. And really big or small shirts always required touch-up.
Most shirt units today have blown sleeves. They may also pull down on the tail of the shirt to keep the box pleats straight. An operator can be trained in hours instead of weeks, and most operators can produce a nice shirt without much effort.
The other choice for shirts is a combination form finisher/shirt press. Smaller plants can use the same machine to press shirts and jackets. The production speed is slower but the cost is significantly less and the savings in floor space is huge.
More to come!
These are just a few of the innovations I have seen over the years. I guess you know how old I am now. Hopefully you appreciate how good your equipment really is.
We are certainly looking forward to Texcare International in Germany this fall. There will be lots of new things to see. Hope to see you there.
Kevin Marois founded Calgary-based Integrity Mechanical in 2003 to service plants in western Canada. He writes on issues related to equipment, its purchase, maintenance and use. You can reach Kevin at imi@telus.net or via his website, www.imicanada.ca.