Custom-Built Drying System Reduces Gas Usage by 52%
|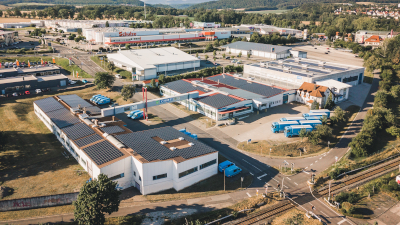
Long before ‘German engineering’ became a popular catchphrase in North American advertising lore, Coburger Handtuch & Matten Service ( CHMS GmbH & Co. KG) was planning a future with it in mind. The family-owned and -operated business in central Germany will mark its 70th anniversary in October. As a key regional service provider of towel dispensers, mops and dirt trapping mats, they have established themselves as an innovative and forward-thinking company with a social conscience.
Throughout the years, Coburger has embraced its engineering ingenuity. Various design improvements and developments over the years which reduced energy consumption led to them becoming part of a network of German companies dedicated to saving resources and the environment.
Today, after a longtime business relationship with Lavatec, the company is enjoying the benefits of being the first in the world to install a custom built LAVACascade drying system. By significantly reducing their drying cycle, the three-tiered system with nine dryers overall has dramatically improved efficiency with a 52% gas savings and lowered associated costs.
Generational expertise paves the way to greater success
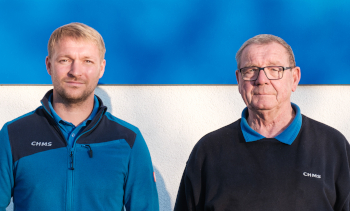
CHMS is a prominent employer in the town of Rodental, about three miles from its original location in Coburg. Home to about 13,000 residents in Bavaria, the largest state by area in the Federal Republic of Germany, the company moved there in 1990, 36 years after CHMS was founded by Gustav and Gertrud Krause in an old horse stable. Owner Joachim Krause began his career working for his parents in 1970, and he now runs the operation with his son, Fabian, who serves as the managing partner.
“I began working here right after completing my economics studies in September, 2013,” recalled Fabian. “Working at the laundry wasn’t new to me because my sisters and I used to spend a part of our holidays handling cloth-roll towels and floor mats.”
The company managed its laundry operation all under one roof back in 1990, but has since expanded. Their complex now contains three separate buildings totaling about 84,000 square feet of space. Construction is underway on a new picking hall that will provide an additional 8,600 square feet when it opens later this year.
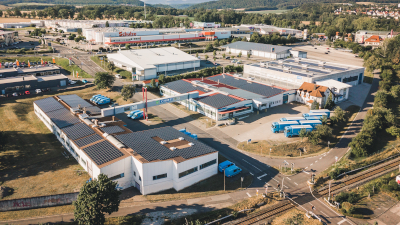
Fabian Krause explained each of the buildings is dedicated to a specific purpose. One is to wash the floor mats, another is to wash the cloth-towel rolls, and the other is used for storage. He says a crew of 50 employees manages the workload during a nine hour shift, five days a week.
“We have about 2,200 customers, some who have been with us for over 30 years. About 2,050 of them are direct customers – a complete mixture of restaurants, every type of business, and public residents – within a 100 mile radius. The other 150 are laundries throughout Germany, Belgium, Switzerland, and The Netherlands, where we do their roll towels and mats,” said Krause, noting that CHMS operates a fleet of six trucks and 15 vans to service their customers.
“The trucks drive over 220,000 miles a year to the laundries, and the vans that are used for the bulk of our customers log over 185,000 miles each year.”
Those vehicles are kept busy as CHMS achieves record levels of throughput. A year before the COVID-19 pandemic began, Krause said they initiated a growth masterplan that included new Lavatec equipment.
The 2019 purchase of a 10 compartment LT100 tunnel washing system with 220-pound capacity per chamber, coupled with a pair of LX 425 washer extractors with 285-pound capacity and a TT-745 gas dryer with 290-pound capacity, were installed in the mats building. One year later the LAVACascade drying system came online.
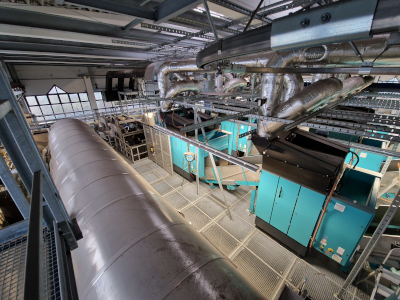
The new equipment added firepower to the Lavatec wash aisle machinery CHMS already had running in the rolls building next door. A 27-year-old, LT50 tunnel with 11 compartments and 110-pound capacity per chamber runs in tandem with a slightly larger 18-year-old, LT50 machine with 12 compartments and 130-pound capacity. Another LX 425 washer extractor is a bit smaller than the other two with 250-pound capacity, but it has produced consistently reliable results since 2013.
“Servicing the rolls division is the largest part of our sales,” said Krause, pointing to a chart showing the company’s growth since 2019. He explained how the rolls volume continues to rise with a 30% increase during this period, and he anticipates the five-year cycle for the mats business to nearly double with similar volume levels by the end of 2024.
“The COVID-19 pandemic did not have a big impact itself on our business. We did have some contracts postponed until 2022,” he admitted, adding the company’s mats division experienced a 49% increase that year.
“Through our investment in the larger Lavatec tunnel washer, LAVACascade, and with the building expansion in 2020, we had forecast doubling the amount of washed mats from 2019-2023. In the near future, we expect the floor mats business will have a higher growth potential and will overtake the towel rolls side of our operation.”
Equipment that supports Sustainability and reduces environmental impact
The engineering prowess CHMS has displayed through the years was tantamount in the development of their custom built and unique LAVACascade drying system.
They have embraced green methods for a long time, making use of about 4,000 gallons of recaptured rainwater daily for use in the mat washing process. Those efforts are supported by a patented water-recycling filtration system they developed.
In 2004, CHMS unveiled a vapor heat exchanger for their ironer’s exhaust air. The new and patented air circulation system improved performance, resulting in major energy savings.
That development figured strongly into their future plans, but Krause said a University of Nuremburg Technology research study is what triggered his father’s interest. The 2010 report prepared by the German Federal Statistical Office analyzed the total energy consumption of 3,800 laundry and dry-cleaning businesses. It determined 90% of the total energy consumed was used for the heating of water.
What Joachim Krause found interesting was each business had systems to recover or re-use water, but only one had installed a facility to re-use waste heat from laundry dryers. Of the 28 dryers they had, it applied to only four.
Looking at ways to reduce costs and meet new government regulatory mandates to reduce energy and emissions, Joachim Krause reached out and met with Wolf-Peter Graeser. Lavatec’s Germany-based president co-owns the company with Mark Thrasher, who manages North American operations from U.S. headquarters in Beacon Falls, Conn.
“My father had the idea that led to LAVACascade. He presented it to them since they had a longtime business relationship and Mr. Graeser saw the potential for it,” said Fabian Krause.
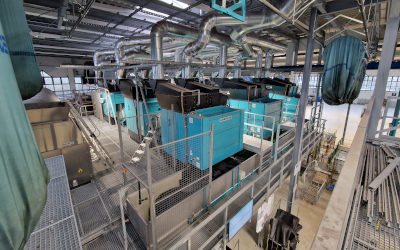
The result is an engineering marvel that reduces the overall ecological impact and produces massive energy savings compared to a standard dryer. By lessening the processing time and increasing linen throughput with less wear and tear, it leads to a domino effect of benefits including a reduction in downtime. With less gas needed, the cycle time is 30% faster and substantially lowers CO2 emissions.
The first phase of the three-tiered continuous drying system introduces recirculated high heat to the laundry load by using the exhaust air of the second dryer. Recirculation is easily programable, and when the first phase is completed the dryer tilts for unloading.
The middle stage involves the load traveling on a conveyor belt to the second dryer. When loaded into the machine, heat loss is reduced during the transfer and the dryer remains hot, so no energy is wasted to heat it again. The third dryer is the cooling stage.
“Our LAVACascade is a closed system, which means it doesn’t convert energy for any other uses,” said Krause. “We do have a combined heat and powerplant which produces electricity using natural gas. The resulting heat is used for the tunnel washers of the mats, the washer extractors, the office building, and to melt the snow on the driveway of the mats building in the wintertime.”
Several North American laundry executives and Industry publication editors recently toured the CHMS facility with Lavatec’s leadership and saw the comprehensive energy control system in action. Krause said continued refinements are paying off, citing 2023 statistics detailing how the amount of kilowatt hours to operate it have dropped consistently month-over-month.
“Our energy management software shows the specific gas consumption of each phase, compared to the gas consumption of the one Lavatec TT-745 gas dryer we have. LAVACascade saves us 52% compared to the gas consumption of a single dryer where the normal drying time is 25 minutes. LAVACascade’s drying time is just 19 minutes.”
Krause further explained what his statistics revealed and what his goals are for this year.
“The specific gas consumption last year averaged 218 kilowatt hours per ton, compared to 460 kilowatt hours for the TT-745 gas dryer. LAVACascade is meeting our expectations and the goal is to achieve a specific gas consumption averaging 180 kilowatt hours per ton,” he acknowledged.
“Since this machine was the first of its kind, Lavatec has spent valuable time together with us and our employees during the installation period and since. They are in close contact with us, and we appreciate their cooperation to optimize and enhance the system.”
For more information, visit www.LLTusa.com.