THE FIXER
|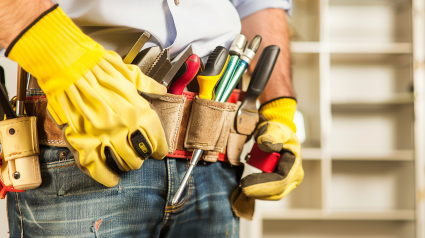
SERIES: Your Allied Trades Team
If you have laundry or dry cleaning equipment, you are going to have mechanical issues. Period.
While that can seem daunting, if you have a good allied trades person backing you up, it’s more of an annoyance than a crisis. When it comes to LaundryLux equipment (ElectroLux Professional, Wascomat, and Encore Pro brands) one of the go-to people is Ernesto Rodriguez, also known as The Fixer.
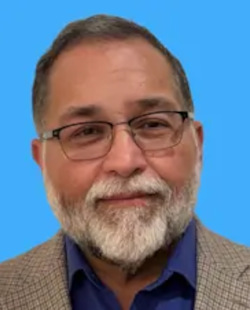
Ernesto Rodriguez
Sr. Director, Product and Technical Learning
erodrugiez@laundrylux.com
Website: Laundrylux.com
We reached Ernesto working on a project in Los Angeles, CA. Don’t let the fancy title fool you — Ernesto is a dirty-hands guy who is not afraid to tackle what needs to be done.
When asked what services LaundryLux offers to it’s customers beyond the obvious sales of equipment and other goods, Ernesto was enthusiastic in his reply. For this interview, he focused on the On-Premise Laundry side of the business.
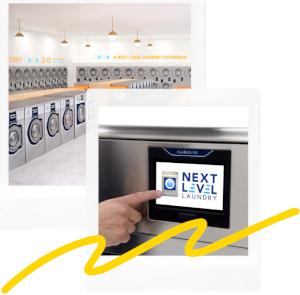
“We use 5 distributors in Canada, and many more in the U.S.,” he said. [Ontario Laundry Systems is one of these distributors, and initiated this salute to Ernesto and his team.] “Our distributors have access to technical training for their own technicians and also to train operators of the equipment. We do regional training in Canada and the US once a year, in cities like Toronto, Vancouver, Los Angeles, Dallas, and Jacksonville, FL.
“We also offer chemical training for vendors like Ecolab, Gurtler and Diversey, who handle distribution to nursing homes, hotels, and other institutions.”
For those who can’t get to a training session, or who need help right away, LaundryLux has solutions.
- A support line is available from 8 a.m. – 6 p.m. (EST). The number is 516-371-0700. Press 4 for technical care.
- Because of COVID, the manuals for equipment were digitized, and owner/operators and mechanical technicians can get access to them online directly. All machines since 2019 have a QR code on them, and the manuals can be accessed by scanning it.
- There are YouTube videos available on topics such as unpacking new equipment, installation of dryers, using card systems in laundromats, and more.
- ElectroLux may send out trainers from the factory to do training, especially in the case of a total installation to be sure the people operating the equipment are ready to go.
“Our sales team is very knowledgeable, too,” he said. “There is a combined experience pool of almost 180 years that the operators can call on.”
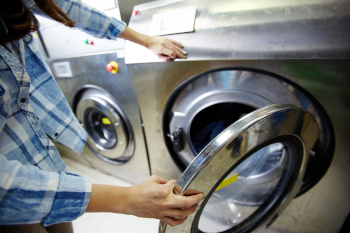
In addition to technical help, LaundryLux also offers marketing help through it’s Creative Services group. They can help with fliers and information, as well as instructions for machines in different languages (French, Spanish, etc.)
The Financial Services department can assist with helping buyers afford their equipment.
Stories
Ernesto is a character, and he’s full of stories about some of the jobs he’s been part of.
“One of my jobs is to be part of the “Escalation Team,” he said. “We have full support on the technical line, but if a job requires the personal touch, we’re here.”
He gets into interesting situations.
“There was a situation in Whistler, BC. An ironer had some problems. Technicians went out to get it up and running, and then they held a training class, because the company had a lot of new people.” Going that extra mile not only meant the equipment would be operating at its optimum, but that the team using it had full confidence in their abilities.
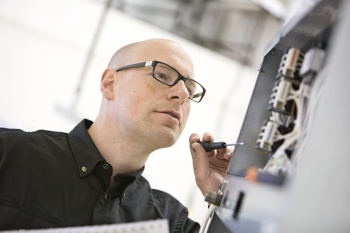
An unusual customer experience involved an oil platform in the Gulf of Mexico. The equipment was spilling water all over, and the crew thought it was defective. We asked if there were special considerations when putting equipment on a rig that is in constant motion.
“We sell a specific marine variant of our equipment for applications like oil platforms and cruise ships,” he said. The motion is only one part of the problem. “They’re using seawater to run it, and that salt can be very bad for equipment unless it’s ready to handle it.”
In the case of the oil rig, he flew out on a helicopter to see the machine in place and assess the problem. “They thought it was the equipment,” he said. “But when I got there, I discovered they’d hooked it up incorrectly. I corrected the hook-up, and everything worked perfectly.”
Just another day not-in-the-office for him.
Just call them
Some equipment owners seem reluctant to call for help when things go wrong with their equipment.
“They’re afraid it will take too long to get a technician out there, and want a quicker resolution,” he said. “So they call the local home improvement store to try to get someone to fix it.” This isn’t always the best solution.

“Some also think it’s still 1985, and they’ll be charged to talk to someone on the phone. That’s not the case with us,” Ernesto said. “They do run into issues if their equipment is over 25 years old, because parts may not be available. But we don’t charge to help you find the solution.
“We do all we can to help owners of our equipment. I tell them all the same thing. I show them the QR code. There’s information and help available if you pick up the phone or use the code,” he said. “Most distributors have stickers on the equipment, often with their phone number on it. Use it. Just call.
“Time is money, so use the resources at your fingertips. Email us. We reply.”
Inevitable change
The LaundryLux website describes Ernesto this way:
Ernesto Rodriguez, Senior Director, Product & Technical Learning at LaundryLux, is a pivotal leader in advancing knowledge and innovation across North America. With over 15 years of field engineering expertise in commercial laundry and a decade of experience in technical training for industries like nuclear power and semiconductor fabrication, Ernesto blends hands-on technical insight with a passion for education.
At LaundryLux, he develops and delivers both foundational and advanced training for the distribution network, crafting innovative learning materials and integrating modern technologies to enhance the learning environment. His deep commitment to operational excellence and industry innovation has made him a recognized subject matter expert and a vital resource for introducing the next generation of technology and expertise into the field.
He’s an incredible resource to all those he helps. Unfortunately, with a background like that, he’s going to retire eventually. But there’s good news: he’s mentoring his replacement already.
“I want him to have developed his own reputation by the time he takes over.”