Gimme Some Love!
|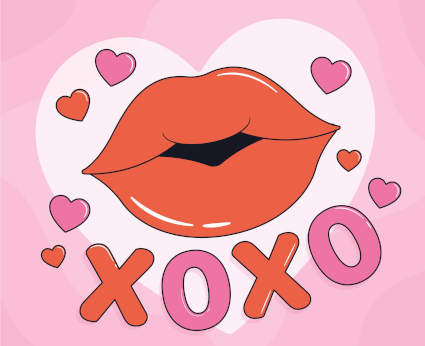
Air compressors need love, too
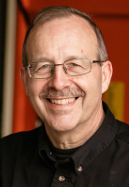
It has been hot lately. Unbearably hot. Are you taking care of your team? Making sure they are not overheating? No – not your human team, your mechanical team.
That heat caused a major problem for one of our customers recently. It destroyed his air compressor and left him shut down for a few hours. We got him going the same day, but there are other long-term issues that may give him further problems. Before we get to that, lets cover the basics on air compressors.
Meet your compressor
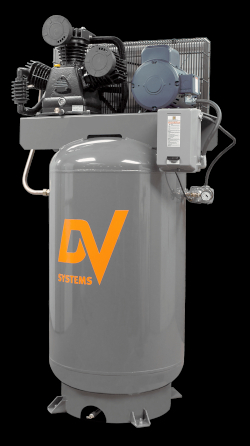
The air compressor takes air from the room and squishes it into a holding tank. Compressing it gives it power to make things move. We use it to open and close presses, turn valves on, move arms up and down, and even for removing stains.
When we compress the air, there are two problems we face. One is heat from squishing the air. The other is that we concentrate the moisture that is present in room air. Compressors have fans and various tubes that radiate heat to help cool the air. The cooler your compressor room, the better.
Proper compressor habitat
The best place to install your air compressor is anywhere except the boiler room. The boiler room is hot and humid. I know most compressors are installed in the boiler room. Wherever it is, the room should have a supply of outside air for cooling and for suction into the compressor.
Keep the fan and after-cooler clean. They build up a lot of lint. The oil in your compressor also helps with cooling. Check it monthly and change it regularly (see manufacturer’s guidelines). When it is really hot, you might consider setting up an additional fan to blow on the unit. Keeping your compressor cool will greatly extend its life.
Care and feeding
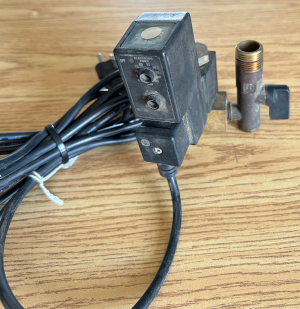
Compressor tank auto-
drain.
The other problem is moisture. When you compress air, you concentrate the naturally occurring humidity in the air – as it cools in the tank, it changes back to water. That water will rust your tank and wreak havoc with your equipment. When the water droplets go through solenoid valves and cylinders, they flush out the lubricant. Now you have valves and cylinders that stick or may be slow moving. That can give you major problems on a shirt unit, where the timing is critical.
Your first step to removing that water is to drain the tank daily. It is best to do this in the morning when everything is cool. Open the tank valve and blow out the accumulated water.
We were recently at a plant that had a new manager. She wasn’t aware she needed to drain the tank. We drained about 60 L of water out of the tank.
One other option is an automatic tank drain. You can set the timer on it to automatically drain any accumulated water out of the tank.
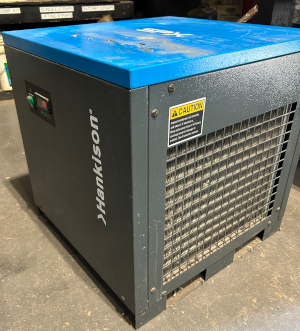
The best way to remove water from compressed air is to use a refrigerated air dryer. This device cools the air enough that the water vapour condenses and can be drained out before it reaches the machines. These air dryers are expensive – but not nearly as expensive as when I come to visit.
One other thing you can do to help your compressor is to fix the air leaks in your plant. Turn the compressor on when nothing else is running and you will be able to hear the leaks on each of your machines. You need to understand that when a machine is 10 years old there will be numerous small leaks all over the machine. It is not practical to try to fix all of those, but you can fix the bigger leaks.
The rest of the story
Let me finish telling you about our customer with the dead compressor. His boiler room was so hot that you couldn’t hold your hand on the wall. The compressor would start fine, but as it got up to pressure it would gradually slow down until is just stalled out and tripped the breaker. The pump (compressor) was damaged internally so we decided to just replace the entire compressor and tank.
But that wasn’t all the damage. When the compressor was running that hot, it was literally cooking the oil in the compressor and blowing it down the line with the air. When compressor oil breaks down it becomes sticky. We had to replace valves on several presses. We also found that there was so much goo/varnish stuck to the inside of the air pipe that the dry cleaning machine wasn’t getting enough air. This turned out to be a much bigger (and more expensive) issue that just a dead compressor.
You need compressed air to run your plant (unless you are going to iron everything by hand). Figure out your system and take care of it. When the compressor goes down, you will pay anything to get it up and running again. Avoid that situation and save yourself a lot of grief and money.
Kevin and Paula Marois founded Calgary-based Integrity Mechanical in 2003 to service plants in western Canada. He writes on issues related to equipment, its purchase, maintenance and use. You can reach Kevin at office@imicanada.ca or via his website www.imicanada.ca.