Interview with a Magician
|INSTALLMENT 2 IN THE MECHANICAL MAGIC SERIES
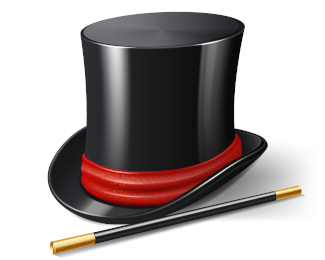
You’re probably afraid to ask your mechanic some of the questions we asked ours, because the longer they are in your plant, the more money they cost you. So we’ve saved you the expense and pinned down Kevin Marois of Integrity Mechanical on some behind-the-curtain thoughts.
The Magician
Kevin Marois
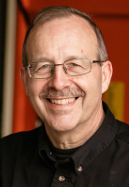
Founded Calgary-based Integrity Mechanical in 2003 to serve plants in Western Canada. He writes for this magazine on issues related to equipment, its purchase, maintenance and use. You can reach Kevin at imi@telus.net, or via his website, www.imicanada.ca.
Roughly how many pieces of equipment do you think the average dry cleaner has? The average laundry?
One more than can comfortably fit into the plant. It seems that every dry cleaner tries to fit one more piece into a plant that is already overcrowded. Most plants have 15-20 machines.
In your experience, which break down the most frequently? Why?
The oldest machines. New machines don’t break down very often. We have customers who can’t believe how much less stress they have after they replace one or two machines.
Dry cleaning machines and shirt presses are the most complicated. They have multiple processes happening at the same time and one problem often causes other problems.
Timing on a shirt unit is critical. The press may be going through all the right motions but if the timing is off you will be doing a lot of touch ups.
What is your favourite piece of equipment in a plant? Why do you like it?
My favourite machine is a sewing machine—because we don’t fix them! I like all the machines we service. I guess I like boilers and dry cleaning machines. They are impressive pieces of equipment.
The old Ajax shirt units were a challenge. Lots of air operated valves and copper lines going back and forth.
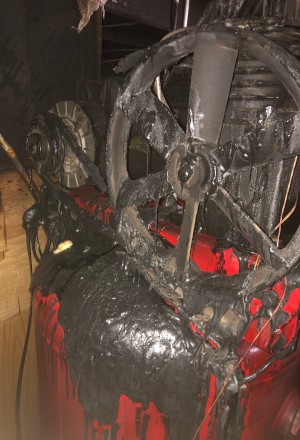
What is the most overlooked piece in the plant? How critical is it to overall operations?
Probably the air compressor. It is stuck in a hot boiler room and coated with dust and lint. Most people do not change (or even check) the oil. There is not too much you can do without an air compressor.
We know of an air compressor that was left on all night and caught on fire. (See photo at left.)
Tell us your war story! What happened “that time” when you were able to save the day by fixing something? (You know, the story you remind yourself of when you’re having a bad day.)
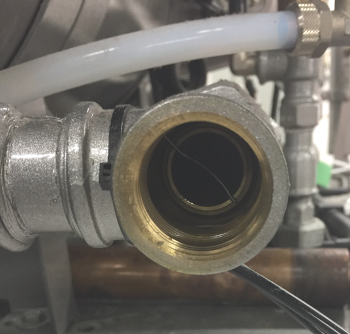
I flew half way across the country one time to take a pin out of a solvent valve. It was leaking enough vacuum that the still would not cook. The worst part was that I had told the fellow to look for that exact issue.
Usually the rigging is the more challenging part of the job. We have moved equipment out of basements, taken machines apart to get them through doorways, and lifted lots of machines in through windows.
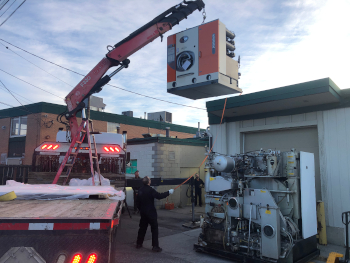
The most satisfying though, is helping customers and watching their business grow.
If you could get all the dry cleaners or launderers in one room for ten minutes, what is the piece of advice you’d most like them to hear from you as their mechanic?
Tell me the truth. I already know you did something stupid. Give me all the facts and will try to help you save money even if I can’t help you save face. Don’t waste your time trying to fix it yourself. Let us do what we do well and you can get on with running your business.
Is there a mechanic you can think of you would like to salute for his/her ability and commitment to excellence?
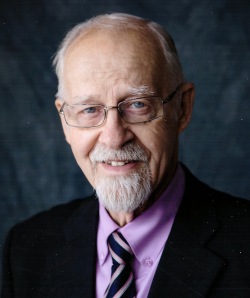
I appreciate my father, Hector Marois, for his patience while I was learning things. Like the time I blew up his lawnmower. He would buy good tools and allow us to make mistakes so we could learn the proper way to do things. He taught me to solder and thread pipe and how to take something apart even if you don’t know anything about it.
I appreciate our team as well. Our guys work hard, they enjoy their work and they really care about helping our customers succeed.
I also appreciate our customers. Some of them have been with us for 20 years. They bring us their dreams and allow us to bring their ideas to life.